每个比较大的矿业公司进行选矿的时候,一般采用的都是“两段一闭路”流程。在进行选矿的时候一般初步矿石都是先进入到圆锥式破碎机进行一道破碎,接下来会再次进入到圆锥破碎机进行两段破碎;采用圆振动筛作为检查筛分与短头圆锥破碎机组成闭路碎矿。
在进行安置选矿厂的时候,一定要考虑到矿石中矿泥、矿粉对选矿带来的影响,在选矿过程当中经常出现碎矿筛分及粉矿仓堵塞现象,避免这种事情发生,可以添加了”块粉分流”干式脱泥工艺,采用中碎前预先筛分,干式脱除原矿中的矿泥和矿粉,单独用皮带直接运人设置,在磨矿前的粉料堆场(即泥矿仓),贮存预先筛下20~0mm粉矿,以保证碎矿、筛分及粉矿排料的流程畅通。碎矿工艺流程见图1。
工艺缺陷:
虽然碎矿流程中添加了“块粉分流”工艺,但在实际生产过程中,效果并不理想,反而引发了诸多矛盾,具体表现在如下几个方面。
(1)“块粉分流”后,分别设置泥矿仓和粉矿仓,人为造成了人选矿石性质的差异。20~ 0mm矿泥与矿粉含铜、含硫 品位较低,且有害杂质较多,与粉矿仓的块矿相比,浮选操作较困难,生产指标较低,必须经常改变药剂制度以确保生产技术指标的稳定。因此,在生产过程中,因磨浮操作人员偏向使用粉矿仓的块矿,导致经常出现粉矿仓空仓,而泥矿仓却是仓满的现象,致使供矿环节极不正常。
(2)增设干式脱泥后,碎矿工艺显得异常复杂。矿石从主井箕斗仓提升直至达到最终合格粒度产品,必须经历繁锁的倒运;常规“两段一闭路”碎矿工艺最多只需要9条运输胶带, 现有各种运输皮带13条。设立的生产岗位及操作人员数量剧增,日常设备维修工作量增大 , 单位矿石破碎成本居高不下,为选厂的管理带来了不利影响。
(3)厂房内操作空间狭小( 如中碎前干式脱泥筛分操作平台狭窄,更换筛网不便,在设计时,为了使设备之间能够有机联系,只能靠增加厂房面积和高度,使得部分皮带卸料点高差较大,造成设备损坏频繁,材料消耗加快,从而增大了生产成本。此外车间内部除尘效果差, 恶化了操作环境。
碎矿工艺改造:
改造依据:原设计碎矿工艺生产运转不畅,主要原因在于“块粉分流”干式脱泥工艺的添加,该工艺的主要目的是防止矿粉、矿泥对碎矿、筛分及矿仓的堵塞和干扰,然而,这一 目的在生产实践中未能实现,通过几年来观察和分析,得出如下结论。年来观察和分析 , 得出如下结论。1添加干式脱泥工艺后,并不能消除矿仓的堵塞现象。2矿泥、矿粉并非是导致矿仓堵塞的主要原因。几年以来,贮存20~0mm矿泥、矿粉的矿仓很少发生堵塞现象。主要是因为泥矿仓容量较小,只能贮存2~3小时生产用的矿量,且卸料口较大。3矿仓堵塞的主要原因是矿石存放时间过长,且高硫矿石氧化速度较快,从而使矿石出现结块所致。
因此,只要采取适当措施,缩短矿石在矿仓中的贮存时间,避免矿石在矿仓里氧化和结块,就完全可以从根本上消除矿仓堵塞的现象。取消泥矿仓,使干式脱泥筛下的矿泥、矿粉与块矿一道进入粉矿仓,不会引起任何负面影响。
方案与措施 :为达到简化碎矿工艺,提高工作效率的目的,确定改造方案是:取消“块粉分流”工艺,废除泥矿仓。原设计泥矿、块矿的流向分别是:
泥矿:干式脱泥筛分(预选筛分)筛下产品→9#皮带→10#皮带→11#皮带→泥矿仓→磨矿;
碎矿车间原设计方案是根据泥矿、块矿的流向而确定的,而厂房结构和工艺配置又联系密切, 因此,既要保留其“两段一闭路”主体碎矿工艺,又要不破坏原有厂房结构,实施工艺改造的难度较大。
确立总体改造方案后,经细致分析,拟定的改造措施是:原有9#皮带、10#皮带、11#皮带全部拆除,保留中碎前预选脱泥筛分,将其筛下漏斗延长,在原设计±0.00m m平台上安装一台长65.65m的运输胶带,连接在干式脱泥筛分筛下漏斗口与3#转运站之间,与7#皮带共用一个卸料站,使矿泥、矿粉进入8#皮带,与块矿一道进入细矿仓。
改造后泥矿、块矿的流向是:
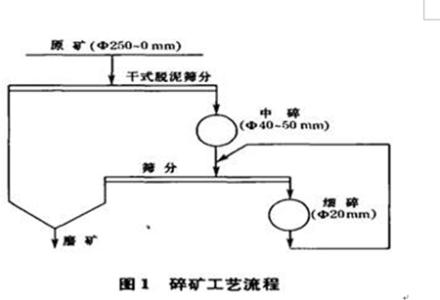
泥矿:预选筛分→新皮带→8#皮带→12#皮带→细矿仓→磨矿;
块矿:检查筛分→7#皮带→8#皮带→12#皮带→细矿仓→磨矿。
改造后,保留了原设计的主体碎矿工艺,但流程内部结构大大简化,取消了泥矿仓及相配套的两台圆盘给矿机,减少了3条运输胶带。
将传统的生产工艺进行改造之后,由于措施得当,改造后的新工艺自运行起来,碎矿工艺保持畅通,各个环节的碎矿工艺保持畅通,避免了生过矿泥干扰或矿仓堵塞等现象,减少了矿石的周转环节,操作简单,大大减少 了工人的劳动强度。消除了入选矿石性质的差异,使浮选操作较易控制,减少了浮选药剂添加的盲目性,产生了较好的间接效益。
环球破碎机网www.ycrusher.com总结,转载请说明出处,传统选矿厂破碎工艺存在的缺点改造方案http://www.ycrusher.com/technology/104526.html。