目前用来薄化晶圆的钻石刀具多为聚晶钻石(PCD),因其刀刃高度不一致,造成各刀刃的切削深度不同、工件受力分布不均等缺陷。终极钻石盘(Ulti-mate Diamond Disk, UDD)采用了全新的刀片式设计,克服了PCD刀具的不足,能减少工件表面刮痕损伤并延长UDD的使用寿命。
本文通过实验观察了经UDD切削后的晶圆表面形状、切屑形状以及磨耗后的UDD形状,分析了刀具转速及切深分别对晶圆表面裂痕生成的影响,并在综合切削力和比切削能的基础上得到了UDD的加工特性。
1、终极钻石盘
PCD钻石盘是将颗粒状的钻石固定在盘上,钻石颗粒多少因颗粒的尺寸大小以及形状而有高度不一致的情形,钻石颗粒高度有50-100μm的差距,造成高度较高的钻石颗粒在工作中易过度磨耗。
终极钻石盘(UDD) 将多况,钻石切割成顶端尖锐的刀片,取代了钻石颗粒,将刀片固定在基座上,刀片的平均高度仅差数个微米。刀刃高度儿乎一致,可达到设定实际切深以及固定的切削力,可减少表面刮痕及损伤层,切削力分布均匀,并可降低UDD的磨耗速度。
2实验设计
本实验采用三轴CNC综合加工机床,利用真空吸盘固定硅晶圆工件,加工后再利用检测设备观察硅品圆及UDD刀具的变化。
2.1加工参数影响实验
固定工件进给速率50 nun/min,改变主轴转速2 000 r/min ,3 000 r/min以及切深1μm,2μm、3μm实验参数如表I。本实验的目的是为了解不同转速及切深对晶圆所带来的表面材料的移除方式以及破坏方式,拟使用 SEM来观察表面形状以及由塑性切削至脆性破坏转换过程,并测m表面粗糙度以及观察生成的切屑。
2.2切削力与比切削能实验
改变主轴转速2 000 r/min,3 000 r/min,工件进给速率50 mm/min ,100 mm/min以及切深0.5-3μm考虑到脆性和塑性切削加工时,比切削能呈现出来的结果会有所不同,拟使用动力计采集不同加工参数下的切削力数据来计算比切削能,由此分析各种加工模式的特点,并通过各自加工后的表面形状来比对验证。
2.3刀具磨耗实验
晶圆未加工前的厚度大约是525 μm,预计晶圆薄化移除址约100μm,本实验是要测试UDD刀具的耐磨耗性,利用前两个实验累积的切削次数,使用三坐标测童仪观察UDD刀具表面形状及刀刃的磨耗形态,以衡量其耐磨耗性。
结语
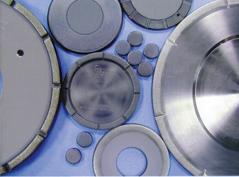
UDD刀片式的设计与传统聚品钻石砂轮的切削方式不同,前者由26个刀片与硬脆材料(晶圆)进行切削,后者是以砂轮与钻石盘之磨粒进行切削。
(1)晶圆表面的形状受到UDD的切削深度与主轴转速的影响,切深增加,UDD切削刀尖半径增加,塑性变形区超过负荷能址开始产生裂痕并扩大造成表面脆性剥落。而主轴转速增加,切削力会减小并增加摩擦的机会使材料软化利于切削,所以有效控制UDD的切削深度以及转速便能减少晶圆表面损伤以及次表面裂痕并提升表面粗糙度。
(2)由UDD切削出的切屑可判断其加工模式,切深0.5μm时,切屑形状为连续细长条状,而切深2μm时则为片状及块状切屑,由切屑的特性可判断切深0.5μm为塑性加工,切深2μm则为脆性破坏移除晶圆材料。
(3)切深量小、高转速、工件进给速率慢、无因次磨粒切深h,小,产生的尺寸效应带来了大的比切削能。 由佳密特钻攻中心http://www.giamite.com.cn 上传发表