电动滚筒组分传动滚筒组和改向滚筒组,电动滚筒作为皮带运输机和提升等设备的动力。这是小编为大家整理的电动滚筒科技论文,仅供参考!
电动滚筒科技论文篇一
滚筒采煤机的工作原理分析
摘要:采煤机是机械化采煤作业的主要机械设备,其功能是落煤和装煤。�煤机械分为�煤机和刨煤机两大类,目前应用最广泛的采煤机械是滚筒采煤机。文章主要就滚筒采煤机的工作原理进行简单的分析。
关键词:采煤机械煤矿机械采煤
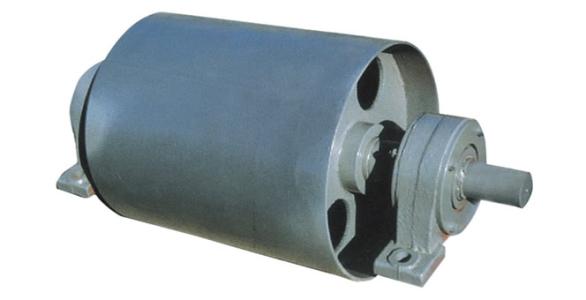
中图分类号:TD421文献标识码:A文章编号:1672-3791(2012)03(a)-0000-00
1滚筒采煤机的组成
主要组成现以双滚筒采煤机为例,说明其组成。如图1所示,它主要由电动机、牵引部、截割部和附属装置等部分组成。
1是滚筒采煤机的动力部分,它通过两端输出轴分别驱动两个截割部和牵引部。采煤机的电动机都是防爆的,而且通常都采用定子水冷,以缩小电动机的尺寸。牵引部2通过其主动链轮与固定在工作面输送机两端的牵引链3相啮合,使采煤机沿工作面移动,因此,牵引部是采煤机的行走机构。左、右截割部减速箱4将电动机的动力经齿轮减速后传给摇臂5的齿轮,驱动滚筒6旋转。滚筒是采煤机落煤和装煤的工作机构,滚筒上焊有端盘及螺旋叶片,其上装有截齿。螺旋叶片将截齿割下的煤装到刮板输送机中。为提高螺旋滚筒的装煤效果,滚筒一侧装有弧形挡煤板7,底托架8是固定和承托整台采煤机的底架,其中采空区侧两个滑靴套在输送机的导向管上,以保证采煤机的可靠导向。底托架内的调高油缸10可使摇臂连同滚筒升降,以调节采煤机的采高。调斜油缸1l用于调整采煤机的纵向倾斜度,以适应煤层沿走向起伏不平时的截割要求。
2 滚筒式采煤机各部分的工作原理
2.1 截割部
采煤机的截割部是由采煤机的工作机构和驱动工作机构的减速器所组成的部件。截割部还包括工作机构的调高机构和挡煤板及其翻转机构。调高机构和翻转机构都是采用液压驱动及控制的。截割部的作用是破煤和装煤,由图1中的挡煤板、螺旋滚筒、摇臂减速器和截割部减速器等部件组成。螺旋滚筒是采煤机的工作机构,它应能适应煤层的地质条件和先进的采煤方法及回采工艺的要求。还应具有落煤、装煤、自开工作面切口的功能。螺旋滚筒的优点是简单可靠,缺点是煤被过于破碎,产生的煤尘较大,截割比能耗较高。
滚筒属于浅截式工作机构,切人煤壁的深度小于1m,可以充分利用煤层的压酥区,降低采煤比能耗。为了保证螺旋叶片向运输机装煤,而不是向煤壁推煤,滚筒叶片的螺旋方向应与滚筒转向相适应。站在采空区一侧看滚筒,右螺旋滚筒应是顺时针方向转动,左螺旋滚筒应是逆时针方向转动。不论采煤机的牵引方向如何,都必须保持这个关系。在螺旋叶片长度一定的条件下,螺旋头数少,螺旋升角大,装煤效果好。但叶片螺旋升角过大,增加循环煤量和粉尘的飞扬,因此,螺旋头数也不能太少。
对采中厚煤层的采煤机多用两头螺旋。当工作条件较稳定、�煤机装机功率富余时,可采用三头螺旋滚筒。滚筒转速是一个比较重要的参数,它对于滚筒的截割和装载过程影响较大。滚筒转速过高则切屑太薄,将产生较多的粉煤,粉尘飞扬,比能耗较高。同时,也会引起循环煤增多,带来不利的影响。但转速高可以提高滚筒的装载能力。
截割部减速器的作用是向工作机构传递动力并使工作机构保持在适当的位置。不同型号的采煤机,其截割部减速器的结构也不尽相同,但基本上都是采用齿轮传动。滚筒转速已呈现低速化的趋势,要使截割比能耗低和生产率高,必须是牵引速度要高,滚筒转速要低,齿数要少,即使煤的块度较大。采用棋盘式配置和大截齿就能达到比能耗低和生产率高的要求。所以,提高截齿的质量和工作性能,正确选用和安装截齿,对于提高�煤机的生产效率和降低生产成本有着重要的意义。
2.2 牵引部
为了提高牵引力,在液压牵引方式中常采用双牵引方式,即液压泵向两个液压马达同时供油的方式。能实现无级调速,随着采煤机外载荷的不断变化,要求牵引速度能随着载荷的变化而变化。在液压牵引采煤机中通过控制变量泵的流量来实现;在电牵引采煤机中则通过控制牵引电动机的转速来实现。能实现正反向牵引和停止牵引,在液压牵引采煤机中常采用单电动机,即截割和牵引使用1台电动机,因此牵引方向的改变或停止牵引往往通过液压泵供油方向的改变或停止供油来实现。
电牵引采煤机采用多电动机,截割电动机和牵引电动机是分开的,很容易实现牵引部正反向牵引和停止牵引。有完善可靠的安全保护由于采煤机的负载变化很剧烈,牵引部必须设有安全保护装置。在液压牵引采煤机中主要根据电动机的负荷变化和牵引阻力的大小来实现自动调速或过载回零,先进的采煤机还设有故障监测和诊断装置。在电牵引采煤机中主要是对牵引电动机的监测和控制来保证牵引部的安全可靠运行。
牵引部的组成及牵引方式牵引部由传动装置和牵引机构两大部分组成。传动装置的重要功能是进行能量转换,即将电动机的电能转换成传动主链轮或驱动轮的机械能。牵引机构是协助采煤机沿工作面行走的装置。传动装置装在采煤机上是内牵引,装在采煤工作面两端为外牵引。绝大部分采煤机为内牵引,仅在薄煤层和急倾斜煤层的采煤机上才使用外牵引。采煤机的牵引机构有有链牵引和无链牵引两种。目前大多数滚筒采煤机是采用锚链牵引。
在采高较大的中厚以上煤层的采煤机上,广泛采用立链轮布置方式。但随着采煤机功率的不断增大,对牵引链的强度要求也越来越高。由于使用了大直径的锚链后,节距越来越大,传动中牵引速度的周期性变化,产生脉动冲击负荷,对采煤机的运行不利。无链牵引提高了采煤机的可靠性和生产的安全性。采用无链牵引后,工作面取消了牵引链,比较安全,采煤机牵引时无冲击负荷,受力情况得到了改善,同时也取消了工作面两端的张紧补偿装置,为工作面使用多台采煤机创造了条件。随着高产高效工作面的出现以及采煤机功率和牵引力的增大,同时也为了工作面更加安全可靠,无链牵引机构方式将逐渐取代有链牵引方式。
3 结论
采煤机械是机械化采煤工作面的主要机械设备,担负落煤和装煤任务。现在普遍使用的采煤机械有滚筒式采煤机和刨煤机两种。因为滚筒式采煤机对各种煤层适应性很强,能适应较复杂的顶板条件,因而得到了广泛应用。而刨煤机要求的煤层地质条件较严,故刨煤机的使用数量近年来逐渐减少。
参考文献
[1] 刘送永,杜长龙,崔新霞. 滚筒式采煤机滚筒载荷谱的模拟分析与研究[J]. 山东科技大学学报(自然科学版), 2008,(01) .
电动滚筒科技论文篇二
改向滚筒结构优化设计
摘 要:随着经济的迅速发展,我国科学技术水平在近年来也有显著提高,尤其在机械化水平上最为显著,这给滚筒结构、加工工艺及装配工艺带来了巨大的变化。当今社会焊接技术在不断发展,焊接强度变得稳定可靠,在滚筒设计过程中,越来越多的设计师们注意到焊接结构的作用,替换原有的铸造结构。采用胀套连接方式替换掉链槽连接细部结构部分。在加工技术方面,原有的加强肋板也被辐板代替。就当前发展形势来看,由刚性向柔性的设计理念已逐渐渗透到滚筒设计当中,并逐步成型且不断发展。
关键词:滚筒;结构;设计
1 滚筒结构设计中传统结构设计方法与存在的缺点
用传统的结构方法进行设计时,首先要根据以往的设计经验及判断来确定滚筒的结构形式,一般指结构布置、材料的选择、制定尺寸及制定相应工艺;其次是全面分析其结构;最后在滚筒成品生产完成之后才可以进行校对工作,一般都是通过力学模型来检测其强度是否符合规定条件,并对一些参数进行适当修订。由此可以得出结论:在传统设计理念中,缺乏合理的更新,只将结构分析视为校对及检验的工具。
由此可以分析传统设计中存在的缺陷是:(1)在有限的校对过程中,单次校对时间长,难度高,工作量大等问题,直接给设计人员带来困难;(2)材料分布情况不能得到有效合理的数据分析结果,对于提出理想的经济适用的方案有很大难度;(3)大量的精力都投入到初始设计方案当中,因此如果原则性问题出现在初始方案中,就会给整个设计带来不良影响,从而无法保证正确性,在年轻的设计师中,缺乏经验,压力又大。
2 滚筒结构设计优化现状
利用数学思想中的函数编程求解是滚筒结构设计得到优化的一个重要方式。利用数学思想,将数学模型运用到相应的结构转化当中,然后同样设置参数及目标函数,并且将约束条件抽离出来,进而可以将位置数值确定下来。通过此法得到的参数值可以达到使用条件标准,对细部尺寸进行参数化,进一步通过三维软件进行讨论,理论上可以实现最终目的,即优化滚筒结构设计。
虽然当前已经经历过很多的实验,然而,滚筒设计仍然不能在参数上给出最优化的一系列参数,在设计的过程中,设计人员仅仅改进了单一的零部件结构,以及研究其在整体结构中起到的作用及造成的影响。截至目前为止,仍然没有一套完整的参考设计方法可以应用到带式输送机整体参数的系统设计,优化所有零部件,特别是优化设计细部参数部分,装配方式组成的滚筒结构模式,有利于展开理论分析及参数验证整体结构,进而可以对所有参数组合进行最优的设计。考虑到整体结构的效果,设计员们都将思路集中到优化思想上,在滚筒设计研究课题中,这种思想极具突破性,值得人们关注并实践。
3 改向滚筒的优化设计
在滚筒设计优化的过程中,是彻底的将滚筒功能加以应用,仍然利用托辊为原型,利用托辊运动原理将滚筒设计为轴承内置形式[1,2],在进行设计的过程中,主要思考方向是对结构的设计,对受力的分析,同时进行理论验证;在结构设计方面,主体内容是在产品的结构中应用到轴承内置理论,目的是实现突破改向滚筒的设计结构;然后利用对受力程度的分析来检验优化设计滚筒结构的功能是否可以在实际中应用,是否具有稳定的结构,同时能够实现同等运力的产品结构参数,因此此项工作急需解决;接下来理论验证就要通过全面比较轴承外置式和轴承内置式两种滚筒得出结论:改向滚筒的设计理念具有一定的优越性,同时还要找出这种理念下存在的问题及不完美的地方。综合所有信息对改向滚筒设计进行整体的评价[3]。
带式输送机在进行常规作业时,改向滚筒在整个运行过程中担负着端部变更运输方向的角色和增加输送带在传动滚筒上的包角, 同时利用改向滚筒拉紧装置从而达到张紧效果,实现其作用。在这三种功能作用不同的情况下,人们之所以称其为改向滚筒,是由于改向的功能体现在不同位置上,同时满足改向滚筒的受力分析,其承担的压力及摩擦力仅来自其上部的张紧力,并且不会受到来自主动力方向力的作用。出于对以上两点的考虑,在轮毂和轴中间放置轴承,避免轴随整个滚筒一起转动,此方法既可以实现改向滚筒的作用,还起到固定轴的作用,有利于实现整体滚筒的定位及受力强度的平衡[4]。
结合以往常用轴承外置式滚筒结构,以及基于创新的想法,现在所设计的轴承内置式改向滚筒新结构由轴座、轴、筒皮、接盘、轴承、透盖、密封圈Ⅰ和密封圈Ⅱ构成,结构示意图如图1:
图1 新型改向滚筒结构示意图
设计轴承座时,借鉴联轴器的连接方式,在两端轴座与轴之间采用键连接,接盘由辐板和轮毂两部分结构通过焊接技术使之成为一体结构,接盘与筒皮的连接方式则采用现如今比较可靠的埋弧焊接方式焊接而成,新设计结构中接盘与透盖通过螺栓连接,接盘与轴承采用过盈配合,轴承与轴也是采用过盈配合,配合尺寸满足接盘的内径比轴的外径大,透盖的内径比轴的外径大,而轴承则设计于接盘的内部,透盖的主要任务是用来保证内部轴承的干净不被污染,为了防止杂质等进入轴承,保障轴承的寿命,密封的作用则尤为重要,所以结构设计时设置了两个密封圈,(如图2)密封圈Ⅰ设在接盘与轴之间,密封圈Ⅱ设在透盖与轴之间。
图2 新型改向滚筒局部示意图
由上述本实用新型的技术方案可以看出,文章所述的新型改向滚筒,在结构上突破了传统轴承外置式改向滚筒的结构,使得结构设计简易合理,同时在生产以及现场应用上更为简便,对提高产量以及现场安装应用测试等操作提供了极大地空间和便利。新型改向滚筒的受力分析[5]:改向滚筒受力为:输送带所受的张紧力引起的对改向滚筒的压力P和两者之间的摩擦力Ff。两种滚筒受力相比,新型改向滚筒比传统滚筒少受到一个主动力矩的作用。
在传统滚筒进行受力分析的过程中可以得知,筒皮中点被视为筒皮的危险处,同时在轮毂辐板附近位置有较大的应力,无论从现场使用情况还是从经验方面,能够满足辐板附近位置的筒皮强度即可,根据现场真实状态来选择型号,并且仔细确认参数,接下来即可利用有限元分析软件展开模拟滚筒的现场操作。
在进行滚筒设计的过程中,设计员们就全面注意滚筒性能方面的稳定可靠,滚筒运行过程中保证筒体运转,同时保证轴不转,在任何情况下,都要保证筒体、轴、轴承及轴承座可以在同一圆心下运行。载负力始终由两个轴承均匀受载。相较于传统通用的改向滚筒两边的轴承和轴承座,都设置在滚筒体两侧外面的轴端处,筒体通过轴和轴承以及轴承座与输送机的钢架相连接有更大的优越性。传统的轴承外置式改向滚筒,在运转时筒体和轴一起转动,对轴承座的安装定位,正确性要求很高,稍不注意,就容易出现偏心,使得轴和轴承,轴承座三者不在同一个圆心上,轴承上受力就容易偏离轴承的中心线,增加了轴承的旋转阻力,容易造成轴承的局部磨损加速导致轴承的损坏。另一个细节就是为了纠正皮带跑偏现象不得不改变改向滚筒原有的定位点,容易使得轴承受力点偏移,造成轴承损坏。经过改进后的滚筒结构,不论在何种工况下,轴,轴承,轴承座都在同一个圆心上运转,减少了旋转阻力,降低了材料消耗和制造成本,降低运转时的能量消耗,延长了轴承的运转寿命,保持了良好的运转性能,安全可靠性高。
参考文献
[1]张亮有,董萌.带式输送机驱动滚筒非标准化设计[J].山西科技,2007(3):123-124.
[2]李克信,平建明,刘曙辉,等.带式输送机换向滚筒结构分析与改进[J].中州煤炭,1999(5):31-32.
[3]Callaghan.Advances in the design of mechanical conveyors[J].Bulk Solids Handling,1994(2):255-281.
[4]陈志杰.可调式内轴承改向滚筒[P].中国专利:92215888.6,1993.
[5]杨好志,马魁文.带式输送机全焊改向滚筒强度分析[J].起重运输机械,2007(7):65-67.