标签: 焊接缺陷
检测方法
杂谈
分类: 焊接知识讲座
八 焊接缺陷及检测方法
1.试述金属熔焊焊缝缺陷的分类及表示方法。
根据GB6417-86《金属熔化焊焊缝缺陷分类及说明》的规定,将金属熔焊焊缝缺陷分为以下几类:
第1类裂纹;第2类孔穴;第3类固体夹杂;第4类未熔合和未焊透;第5类形状缺陷和第6类上述以外的其它缺陷。
本标准按缺陷性质分大类,按其存在的位置及状态分小类,以表格的方式列出。缺陷用数字序号标记。每一缺陷大类用一个三位阿拉伯数字标记,第一缺陷小类用一个四位阿拉伯数字标记。因此,每一数字序号仅适合于某一特定类型的缺陷。例如,1021表示“焊缝横向裂纹”,1023表示“热影响区横向裂纹”等。
2.试述熔焊接头中裂纹的种类及表示方法。
熔焊接头中裂纹的种类及表示方法,见表1。
3.试述熔焊接头中孔穴的种类及表示方法。
熔焊接头中孔穴的种类及表示方法,见表2。
4.试述熔焊接头中固体夹杂的种类及表示方法。
熔焊接头中固体夹杂的种类及表示方法,见表3。
5.试述熔焊接头中未熔合和未焊透的种类及表示方法。
熔焊接头中未熔合和未焊透的种类及表示方法,见表4。
6.试述熔焊接头中形状缺陷的种类及表示方法。
熔焊接头中形状缺陷的种类及表示方法,见表5。
7.试述熔焊接头中其它缺陷的种类及表示方法。
熔焊接头中其它缺陷的种类及表示方法,见表6。
表6 其它缺陷的种类及表示方法
数字序号
名 称
说 明
600
其它缺陷
不能包括在1~5类缺陷的其它缺陷
601
电弧擦伤
在焊缝坡口外部引弧或打弧时产生于母材金属表面上的局部损伤
602
飞溅
熔焊过程中,熔化的金属颗粒和熔渣向周围飞散的现象。这种飞散出的金属颗粒和熔渣习惯上也称为飞溅
6021
钨飞溅
从钨电极过渡到母材金属表面或凝固焊缝金属表面上的钨颗粒
603
表面撕裂
不按操作规程拆除临时焊接的附件时产生于母材金属表面的损伤
604
磨痕
不按操作规程打磨引起的局部表面损伤
605
凿痕
不按操作规程使用扁铲或其它工具铲凿金属而产生的局部损伤
606
打磨过量
由于打磨引起的焊件或焊缝的不允许的减薄
607
608
定位焊缺陷层间错位
不按规定程序熔敷的焊道
8.什么是热裂纹?促使形成热裂纹的因素有哪些?
焊接过程中,焊缝和热影响区金属冷却到固相线附近的高温区间产生的焊接裂纹即热裂纹。又称结晶裂纹。其特征是断口呈蓝黑色,即金属在高温被氧化的颜色,裂纹总是产生在焊缝正中心或垂直于焊缝鱼鳞波纹,焊缝表面可见的热裂纹呈不明显的锯齿状,或与焊缝波纹相垂直呈放射状分布。个别情况下,热裂纹也可能出现在热影响区。热裂纹主要发生在杂质含量较多的钢、单相奥氏体钢、镍基合金、铝合金、钼合金等的焊缝金属中。
促使形成热裂纹的因素有:
(1)焊缝金属的化学成分 焊缝金属中C、S、P元素较多时,促使形成热裂纹。锰在熔池中能与硫形成MnS进入熔渣,可减少硫的有害作用,适量时可减少焊缝的热裂纹倾向。
钢中含铜量过多时,会增大焊缝热裂纹倾向。
(2)焊缝横截面形状 焊缝熔宽与厚度的比值越小,即熔宽较小、厚度较大时,容易产生热裂纹。
(3)焊接应力 焊件刚性大,装配和焊接时产生较大的焊接应力,会促使形成热裂纹。
9.如何防止产生热裂纹?
(1)控制焊缝金属中有害杂质的含量 碳素结构钢用焊芯(丝)的含碳量均≤0.10%,硫、磷的含量应≤0.03%,焊接高合金钢时控制更严。
(2)预热 能减小焊接熔池的冷却速度,降低焊接应力。随着母材含碳量或碳当量的增加,应适当增高预热温度。
奥氏体不锈钢焊缝不能采用预热的方法来防止产生热裂纹。
(3)采用碱性焊条和焊剂 由于碱性焊条和焊剂具有较强的脱硫、磷能力,因此具有较高的抗热裂能力。
(4)适当调整焊接工艺参数 焊接工艺参数直接影响焊缝的横断面形状,因此适当减小焊接电流以减少焊缝厚度,有利于提高焊缝的抗裂性能。
(5)采用收弧板 焊接终了断弧时,由于弧坑冷却速度较快,常因偏析而在弧坑处形成热裂纹,即所谓的弧坑裂纹。所以终焊时应逐渐断弧,并填满弧坑。必要时可采用收弧板,将弧坑移至焊件外,此时即使产生弧坑裂纹,也因焊后需将收弧板割掉,并不影响结构本身。
10.什么是冷裂纹、延迟裂纹?促使形成冷裂纹、延迟裂纹的因素有哪些?
焊接接头冷却到较低温度下(对于钢来说在Ms温度以下)时产生的焊接裂纹称为冷裂纹。
钢的焊接接头冷却到室温后并在一定时间(几小时、几天、甚至十几天)才出现的焊接冷裂纹称为延迟裂纹。
冷裂纹(包括延迟裂纹)主要发生在中碳钢、高碳钢、低合金或中合金高强钢、钛及钛合金的焊接接头中。
冷裂纹多发生在接头热影响区或熔合线上,个别情况下出现在焊缝上。根据冷裂纹产生的部位,可将冷裂纹分为如下三种见图1。
(1)焊道下裂纹在靠近堆焊焊道的热影响区内所形成的焊接冷裂纹。其走向常与熔合线平行,但也有时垂直于熔合线。
(2)焊趾裂纹沿应力集中的焊趾处所形成的焊接冷裂纹。其走向常与焊缝纵向平等,由焊趾的表面开始,向母材的深处延伸。
(3)焊根裂纹 沿应力集中的焊缝根部所形成的焊接冷裂纹。其走向从焊缝根部开始,伸向热影响区或焊缝中。
形成冷裂纹的三大因素是:钢种的淬硬倾向大、焊接接头的含氢量高和结构的焊接应力大。特别是由氢促使形成的冷裂纹往往具有延迟的性质,常称为“氢致裂纹”。
11.如何防止产生冷裂纹?
(1)控制焊缝金属的含氢量 采用碱性低氢型焊条和焊剂;严格按规定烘干焊条和焊剂;仔细清除焊接区的污物、锈、油、水。
(2)预热 减慢接头的冷却速度以降低淬硬倾向。
(3)后热(消氢处理) 后热是指焊接结束或焊完一条焊缝后,将焊件或焊接区立即加热到150~250℃,并保温一段时间。消氢处理是在300~400℃加热温度内进行。两者均能促使氢逸出,但消氢处理效果更好。
(4)采用较大的焊接线能量 减慢接头的冷却速度。但线能量太大时,会促使热影响区形成过热组织,所以应适当控制,不能无限制地增大。
(5)采用奥氏体不锈钢焊条 因奥氏体组织塑性好,可减少焊接应力,并能溶解较多的氢,所以可用来焊接淬硬倾向较强的低合金高强钢,避免产生冷裂纹。
12.什么是再热裂纹?防止产生再热裂纹的方法有哪些?
焊后焊件在一定温度范围内再次加热(消除应力热处理或其它加热过程)而产生的裂纹称为再热裂纹。再热裂纹通常发生在熔合线附近的粗晶区中,从焊趾部位开始,延向细晶区停止。
钢中Cr、Mo、V、Nb、Ti等元素会促使形成再热裂纹,其影响可用下式表示
△G′=Cr+3.3Mo+8.1V+10C-2
△G′>2时,对再热裂纹敏感;1.5<△G′<2时,一般;△G′<1.5时,对再热裂纹不敏感。
防止产生再热裂纹的方法:
(1)预热 预热温度为200~450℃。若焊后能及时后热,可适当降低预热温度。例如,18MnMoNb钢焊后在180℃热处理2h,预热温度可降低至180℃。
(2)应用低强度焊缝 使焊缝强度低于母材以增高其塑性变形能力。
(3)减少焊接应力 合理地安排焊接顺序、减少余高、避免咬边及根部未焊透等缺陷以减少焊接应力。
13.什么是层状撕裂?防止层状撕裂的方法有哪些?
焊接时,在焊接构件中沿钢板轧层形成的呈阶梯状的一种裂纹称为层状撕裂。层状撕裂经常发生在T形接头和角接接头中,其走向与钢板表面相平行见图2,图中箭头表示接头的受力方向。
产生层状撕裂的原因是在轧制钢板中存在硫化物、氧化物和硅酸盐等低熔点非金属夹杂物,其中尤以硫化物的作用为主,在轧制过程中被延展成片状,分布在与表面平行的各层中,在垂直于厚度方向的焊接应力作用下,夹杂物首先开裂并扩展,以后这种开裂在各层之间相断发生,连成一体,造成层状撕裂的阶梯性。
防止层状撕裂的方法:
1)严格控制钢材的含硫量。
2)采用强度级别较低的焊接材料。
3)在与焊缝相连接的钢板表面堆焊几层低强度焊缝金属作为过渡层,以避免夹杂物处于高温区。
4)预热和使用低氢焊条。
14.常用的抗裂性试验方法有哪些?
常用的抗裂性试验方法,见表7。
表7 抗裂性试验方法
序号
试 验 方 法
产生的主要裂纹类型
也可反映的裂纹
1
2
3
4
5
6
7
8
9
10
11
不需特殊的试验装置
斜Y形坡口焊接裂纹试验(GB4675.1-84)
压板对接(FiSCO)焊接裂纹试验(GB4675.3-84)
搭接接头(CTS)焊接裂纹试验(GB4675.2-84)
刚性固定对接试验
可变刚性试验
十字接头试验
十字搭接裂纹试验
窗形拘束对接裂纹试验
Z向窗口试验
Z向拉伸试验
H形拘束试验
热影响区冷裂纹
焊缝热裂纹
热影响区冷裂纹
焊缝热、冷裂纹
焊缝根部冷、热裂纹
热影响区冷裂纹
-
焊缝横向热裂纹
层状撕裂
层状撕裂
再热裂纹
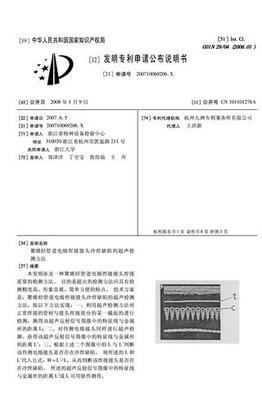
焊缝冷裂纹、热裂纹或再热裂纹
-
-
热影响区冷裂纹
热影响区冷裂纹
-
-
-
-
-
-
12
13
14
15
需特殊试验装置
插销试验
拉伸拘束裂纹试验(TRC试验)
刚性拘束裂纹试验(RRC试验)
可调拘束高温裂纹试验
冷裂纹
冷裂纹
冷裂纹
焊缝热裂纹
层状撕裂
-
-
-
16
17
间接评定方法
碳当量法
热影响区最高硬度不地(GB4675.5-84)
冷裂纹
热影响区冷裂纹
-
-
15.试述防止焊缝中产生气孔的常用方法。
1)仔细清除焊件表面上的污物,手弧焊时在坡口面两侧各10mm、埋弧焊时各20mm范围内去除锈、油,应打磨至露出金属表面光泽,特别是在使用碱性焊条和埋弧焊时,更应做好清洁工作。
2)焊条和焊剂一定要严格按照规定的温度进行烘焙:酸性焊条75~150℃;碱性焊条350~450℃;焊剂250℃,并保温1~2h。烘焙后的焊条应放在焊条保温筒内,随用随取。碱性焊条在露天存放4h以上时应重新烘焙,重复烘焙的次数不得超过3次。
3)不应使用过大的焊接电流。
4)采用直流电源施焊时,电源极性应为反接。
5)碱性焊条施焊时,应采用短弧焊。
6)引弧时应将焊条略作停顿,对引弧处进行预热,否则引弧处容易形成气孔。
7)采用手弧焊打底、埋弧焊盖面的工艺时,打底焊条应为碱性焊条,用酸性焊条打底极易产生气孔。
8)气体保护焊时应调节气体流量至适当值、流量太小,保护不良,易使空气侵入形成气孔。
16.试述常用无损检验方法的种类及其选择。
不损坏被检查材料或成品的性能和完整性而检测其缺陷的方法称为无损(探伤)检验。常用的无损检验方法有超声、射线(X、γ)照相、磁粉、渗透(荧光、着色)和涡流探伤等。其中超声探伤和射线探伤适于焊缝内部缺陷的检测;磁粉探伤和渗透探伤则用于焊缝表面质量检验。每一种无损探伤方法均有其优点和局限性,各种方法对缺陷的检出机率既不会有100%,也不会完全相同。因而应根据焊缝材质、结构及探伤方法的特点、验收标准等来进行选择。
不同焊缝材质探伤方法的选择见表8。
17.试述射线探伤的原理及焊接缺陷的影像特征。
射线探伤可分别采用X、γ两种射线,其探伤原理见图3。当射线通过金属材料时,部分能量被吸收,使射线发生衰减。如果透过金属材料的厚度不同(裂纹、气孔、未焊透等缺陷,该处发生空穴,使材料变薄)或体积质量不同(夹渣),产生的衰减也不同。透过较厚或体积质量较大的物体时衰减大,因此射到底片上的强度就较弱,底片的感光度就较小,经过显影后得到的黑度就浅;反之,黑度就深。根据底片上黑度深浅不同的影像,就能将缺陷清楚地显示出来。
γ射线的穿透能力比X射线强,适合于透视厚度大于50mm的焊件。
射线探伤常见焊接缺陷的影像特征见表9。
表9 射线探伤焊接缺陷影像特征
缺陷种类
缺 陷 影 像 特 征
产 生 原 因
气孔
多数为圆形、椭圆形黑点,其中心处黑度较大,也有针状、柱状气孔。其分布情况不一,有密集的,单个和链状的
1)焊条受潮
2)焊接处有锈、油污等
3)焊接速度太快或电弧过长
4)母材坡口处存在夹层
5)自动焊产生明弧现象
夹渣
形状不规则,有点、条块等,黑度不均匀。一般条状夹渣都与焊缝平行,或与未焊透未熔合混合出现
1)运条不当,焊接电流过小,坡口角度过小
2)焊件上留有锈及焊条药皮的性能不当等
3)多层焊时,层间清渣不彻底
未焊透
在底片上呈现规则的,甚至直线状的黑色线条,常伴有气孔或夹渣。在V、比V形坡口的焊缝中,根部未焊透都出现在焊缝中间,K形坡口则偏离焊缝中心
1)间隙太小
2)焊接电流和电压不当
3)焊接速度过快
4)坡口不正常等
未熔合
坡口未熔合影像一般一侧平直另一侧有弯曲,黑度淡而均匀,时常伴有夹渣。层间未熔合影像不规则,且不易分辨
1)坡口不够清洁
2)坡口几何尺寸不当
3)焊接电流电压小
4)焊条直径或种类不对
裂纹
一般呈直线或略带锯齿状的细纹,轮廓分明,两端尖细,中部稍宽,有时呈现树枝状影像
1)母材与焊接材料成分不当
2)焊接热处理不当
3)应力太大或应力集中
4)焊接工艺不正确
夹钨
在底片上呈现圆形或不规则的亮斑点,且轮廓清晰
采用钨极气体保护焊时,钨极爆裂或熔化的钨粒进入焊缝金属
18.试述射线探伤的质量标准。
根据GB3323-87《钢熔化焊对接接头射线照相和质量分级》的规定,射线探伤的质量标准分为照相质量等级和焊缝质量等级两部分。
根据采用的射源种类及其能量的高低、胶片的种类、增感方式、底片的黑度、射源与胶片间的距离等参数,照相质量等级分为A、AB和B三级,质量级别顺次增高。即后者比前者分辨相同尺寸的缺陷时,透照的厚度大。锅炉压力容器的缝照相质量为AB级。
焊缝质量等级共分四级,Ⅰ级焊缝内缺陷最少,质量最高;Ⅱ、Ⅲ级焊缝内的缺陷依次增多,质量逐次下降,缺陷数量超过Ⅲ级者为Ⅳ级,Ⅳ级最差。缺陷数量的规定:Ⅰ级焊缝内不准有裂纹、未熔合、未焊透和条状夹渣(允许有少量气孔和点状夹渣);Ⅱ、Ⅲ级焊缝内不准有裂纹、未熔合以及双面焊和加垫板的单面焊中的未焊透(允许有一定数量的气孔、条状夹渣和不加垫板单面焊中的未焊透)。
19.试述超声波探伤的原理及质量标准。
利用超声波探测材料内部缺陷的无损检验法称超声波探伤。超声探伤的原理,是利用焊缝中的缺陷与正常组织具有不同的声阻抗(材料体积质量与声速的乘积)和声波在不同声阻抗的异质界面上,通过超声波时会产生反射现象来发现缺陷的。探伤时由探头中的压电换能器发射脉冲超声波。通过声耦合介质(水、油、甘油或浆糊等)传播到焊件中,遇到缺陷后产生反射波,然后再用另一个类似的探头或同一个探头接收反射的声波,经换能器转换成电信号,放大后显示在荧光屏上或打印在纸带上。根据探头位置和声波的传播时间(荧光屏上回波位置)可求得缺陷位置;反射波的幅度可以近似地评估缺陷的大小,见图4。
质量标准:超声波探测焊缝的方向愈多,波束垂直于缺陷平面的机率愈大,缺陷的检出率也愈高,其评定结果也愈准确。GB11345-89《钢焊缝手工超声波探伤方法和探伤结果分级》中规定,根据对焊缝探测方向的多少,把超声波伤划分为A、B、C三个检验等级,检验的完善程度逐级升高,其中B级适合于受压容器。
焊缝质量等级分类见表10。表中数字为允许最大波幅长度。
20.试比较射线探伤和超声探伤各自的技术特性。
射线探伤和超声探伤的技术特性比较见表11。
表11 射线探伤和超声探伤的技术特性比较
检 测 方 法
射线照相法探伤
超声探伤
原
理
方法的原理
穿透法
脉冲反射法
物理能量
电磁波
弹性波
缺陷部位的表现形式
完好部件与缺陷部位的穿透剂量有差异。其差异程度与这两部分的材质、射线透过的方向以及缺陷的尺寸有关。
在完好部位没有反射波,而在缺陷部位发生反射波。其反射程度与完好部位和缺陷部位的材质有关。
信息显示
射线底片
荧光屏
显示的内容
完好部位与缺陷部位的底片黑度差
缺陷反射波的位置和幅度
易于检测的缺陷方向
与射线方向平行的方向
与超声波束垂直的方向
易于检测的缺陷形状
在射线方向上有深度的缺陷
与超声波束成垂直方向扩展的缺陷
被
检
物
铸件
◎
○
锻件
×
◎
压延件
×
◎
焊缝
◎
○
缺
陷
分层
×
◎
气孔
◎
○
未焊透
○
○
未熔合
○
○
裂纹
△
△
夹渣
◎
○
注:◎-很合适;○-合适;△-有附加条件时合适;×-不合适。
21.试述磁粉探伤的原理及质量标准。
利用在强磁场中,铁磁性材料表层缺陷产生的漏磁场吸引磁粉的现象,而进行的无损检验法称为磁粉探伤。
磁粉探伤原理:首先将被检焊缝局部充磁,焊缝中便有磁力线通过。对于断面尺寸相同、内部材料均匀的焊缝、磁力线的分布均匀的。当焊缝表面或内部有裂纹、气孔、夹渣等缺陷时,磁力线将绕过磁阻较大的缺陷,产生弯曲见图5a。此时在焊缝表面撒上磁粉,磁力线将穿过表面缺陷上的磁粉,形成“漏磁”,磁粉就被吸附在缺陷上见图5b,根据被吸附磁粉的形状、多少、厚薄程度,便可判断缺陷的大小和位置。内部缺陷由于离焊缝表面较远,磁力线在其上不会形成漏磁,磁粉不能被吸住,无堆积现象,所以缺陷无法显露。
常用磁粉是四氧化三铁(Fe3O4)和三氧化二铁(Fe2O3)。
缺陷磁痕按形状可分为三种:
(1)线状缺陷磁痕 其显示长度为宽度的3倍以上。
(2)圆型缺陷磁痕 除线状缺陷磁痕以外的缺陷磁痕。
(3)分散缺陷磁痕 在一定区域内同时存在几个缺陷的磁痕。
质量标准:根据ZBJ04006-87标准的规定,缺陷磁痕的等级分7级分别见表12、表13。
表12 线状缺陷磁痕和圆状缺陷磁痕的等级分类 (㎜)
等级分类
缺陷磁痕的长度L
等级分类
缺陷磁痕的长度L
1
2
3
4
1<L≤2
2<L≤4
4<L≤8
8<L≤16
5
6
7
16<L≤32
32<L≤64
L>64
表13 分散缺陷磁痕的等级分类
等级分类
缺陷磁痕长度总和L
等级分类
缺陷磁痕长度总和L
1
2
3
4
2<L≤4
4<L≤8
8<L≤16
16<L≤32
5
6
7
32<L≤64
64<L≤128
L>128
22.试述渗透探伤的原理及质量标准。
采用带有萤光染料(萤光法)或红色染料(着色法)的渗透剂的渗透作用,显示缺陷痕迹的无损检验法称为渗透探伤。
渗透探伤原理:将含有染料的渗透液涂敷在被检焊件表面,利用液体的毛细作用,使其渗入表面开口缺陷中,然后去除表面多余渗透液,干燥后施加显像剂,将缺陷中的渗透液吸附到焊件表面上来,通过观察缺陷显示迹痕来进行焊接结构表面开口缺陷的质量评定。其基本步骤见图6。
各种焊接缺陷痕迹的显示特征见表14。
表14 各种焊接缺陷的显示特征
缺 陷 种 类
显 示 迹 痕 特 征
焊 接 气 孔
显示呈圆形、椭圆形或长圆条形,显示比较均匀边缘减淡
焊接裂纹
热裂纹
显示一般略带曲折的波浪状或锯齿状的细条纹
冷裂纹
显示一般呈直线细条纹
火口裂纹
显示呈星状或锯齿状条纹
未焊透
呈一条连续或断续直线条纹
未熔合
呈直线状或椭圆形条纹
夹渣
缺陷显示不规则,形状多样且深浅不一
质量评定:焊缝质量根据缺陷痕迹的类型、迹痕的尺寸、显示迹痕的分布及间距、缺陷性质等进行评定。按照JBJ59、T《焊缝渗透检验方法和缺陷迹痕的分级》的规定,分为四个质量等级,Ⅰ级的质量最高,Ⅳ级最低,见表15。
23.焊接接头的力学性能试验包括哪些内容?
(1)焊接接头的拉伸试验(包括全焊缝拉伸试验) 试验的目的是测定焊接接头(焊缝)的强度(抗拉强度σb,屈服点σs)和塑性(伸长度δ,断面收缩率φ),并且可以发现断口上的某些缺陷(如白点)。
试验可按GB2651-89《焊接接头拉伸试验方法》进行。
(2)焊接接头的弯曲试验 试验的目的是检验焊接接头的塑性,并同时可反映出各区域的塑性差别、暴露焊接缺陷和考核熔合线的质量。
弯曲试验分面弯、背弯和侧弯三种,试验可按GB2653-89《焊接接头弯曲及压扁试验方法》进行。
(3)焊接接头的冲击试验 试验的目的是测定焊接接头的冲击韧度和缺口敏感性,作为评定材料断裂韧性和冷作时效敏感性的一个指标。
试验可按GB2650-89《焊接接头冲击试验方法》进行。
(4)焊接接头的硬度试验 试验的目的是测量焊缝热影响区金属材料的硬度,并可间接判断材料的焊接性。
试验可按GB2654-89《焊接接头及堆焊金属硬度试验方法》进行。
(5)焊接接头(管子对接)的压扁试验 试验的目的是测定管子焊接对接接头的塑性。
试验可按GB2653-89《焊接接头弯曲及压扁试验方法》进行。
(6)焊接接头(焊缝金属)的疲劳试验 试验的目的是测量焊接接头(焊缝金属)的疲劳极限(σ-1) 。
试验可按GB2656-81《焊缝金属和焊接接头的疲劳试验法》进行。
24.试述焊接接头金相试验的方法及内容。
焊接接头的金相试验包括宏观金相试验和微观金相试验两部分。
(1)宏观金相试验 直接用肉眼或低倍放大镜进行检查。
1)宏观(粗晶)分析 试验时在试件上截取横断面,然后经过打磨、腐蚀再进行观察。宏观(粗晶)分析可以了解焊缝一次结晶组织的粗细程度和方向性;熔池形状、尺寸;焊缝接头各区域的界限和尺寸;各种焊接缺陷的存在情况。
2)断口检查 在焊缝表面沿焊波方向车一条沟槽,槽深约为焊缝厚度的1/3,用拉力机将试样拉断,用肉眼或5~10倍放大镜观察断口处可能存在的缺陷种类和大小。断口检查对“未熔合”或“熔合不良”这种缺陷十分敏感,常用于管子对接接头中。
3)钻孔检验 用磨成90°角、直径较焊缝宽度大2~3mm的钻头在焊缝上钻孔、钻孔深度为焊件厚度的2/3,然后用10%硝酸水溶液浸蚀孔壁,可检查焊缝内部的气孔、裂纹、夹渣等缺陷,检查完毕钻孔处应予以补焊。钻孔检验目前用得较少。
(2)微观金相试验 用1000~1500倍金相显微镜观察焊缝金属的显微组织和显微缺陷(如微裂纹),可作为质量分析及试验研究的手段。
25.试述焊接容器耐压检验的目的及常用方法。
将水、油、气等充入容器内徐徐加压,以检查其泄漏、耐压、破坏等的试验称为耐压检验。耐压检验的目的是检查受压容器焊接接头的穿透性缺陷和结构的强度,并附有降低焊接应力的作用。
常用的耐压检验方法是水压试验和气压试验,其中以水压试验用得最多。
(1)水压试验 试验时将容器内充满水,然后缓慢加压,待压力升至容器工作压力时,暂停升压(管子无需),进行初步检查。若无漏水或无异常现象,再升压到试验压力,并在该压力下保持5min(管子试验时允许保持10~20s)。然后降至工作压力,并用10~15kg的圆头小锤,在距焊缝15~20mm处沿焊缝方向进行轻轻敲打,仔细检查。检查时,压力应保持不变。检查结果,如容器壁和焊缝上没有水珠和水雾,则认为水压试验合格。
(2)气压试验 用干燥洁净的空气、氮气或其它惰性气体作为介质充入容器内进行试验。试验时,应先缓慢升压至规定试验压力的10%,保持5~10min,进行初步检查。然后升压到规定试验压力的50%,如无异常现象,其后按每级为规定试验压力的10%,逐级升压到试验压力,保持10~30min,经肥皂液或其它检漏检查无漏气、无可见的异常变形即为合格。气压试验上仍一定危险性,仅用于不能向压力容器内安全充灌液体以及运行条件不允许残留试验液体的压力容器。
耐压检验的试验压力按《压力容器安全技术监察规程》的规定选用。
26.试述焊接容器常用致密性检验的方法。
焊接容器常用致密性检验的方法是气密性检验和密封性检验。
(1)气密性检验 将压缩空气(或氨、氟里昂、氦、卤素气体等)压入焊接容器,利用容器内、外气体的压力差检查有无泄漏的试验法称为气密性检验。
介质毒性程度为极度(氟、氢氰酸、氟化氢、氯等)的压力容器,必须进行气密性检验。
1)充气检查 在受压容器内部充以一定压力的气体,外部根据部位涂上肥皂水,如有气泡出现,说明该处致密性不好,有泄漏。
2)沉水检查 将受压元件沉入水中,内部充以压缩空气,如水中有气泡出现,说明受压元件的致密性不好,有泄漏。
3)氨气检查 在受压元件内充入混有1%氨气的压缩空气,将在5%硝酸汞水溶液中浸过的纸条或硼带贴在焊缝外部(也可贴浸过酚酞试剂的白纸条)。如有泄漏,在纸条或硼带的相应位置上,将呈现黑色斑纹(用酚酞纸时为红斑点),这种方法比较准确,效率高,适用于环境温度较低的情况下检查焊缝的致密性。
(2)密封性检验 检查有无漏水、漏气和渗油、漏油等现象的试验称为密封性检验。常用的密封性检验方法是煤油试验,试验时在焊缝的一侧涂石灰水,干燥后再于焊缝另一侧涂煤油,由于煤油表面张力小,具有穿透极小孔隙的能力,当焊缝有穿透性缺陷时,煤油即渗过去,在石灰粉上出现油斑或带条。为正确地确定缺陷大小和位置,涂上煤油后应立即进行观察,最初出现油斑或带条的位置即为缺陷的位置,观察时间为15~30min,在规定时间内不出现油痕即认为焊缝合格。
27.试述不锈钢耐腐蚀试验方法的种类和试验步骤。
根据国家标准,不锈钢耐腐蚀试验方法可分为下列几种:
(1)不锈钢10%草酸浸蚀试验方法(GB4334.1-84) 适用于检验奥氏体不锈钢晶间腐蚀的筛选试验方法,试样在10%草酸溶液中电解浸蚀后,在显微镜下观察被浸蚀表面的金相组织,以判定是否需要进行硫酸-硫酸铁、65%硝酸、硝酸-氢氟酸以及硫酸-硫酸铜等长时间热酸试验。必要时也可以作为独立的无损检验方法。
试验步骤:
1)将100g草酸溶解于900ml蒸馏水或去离子水中,配制成10%草酸溶液。对含钼钢种可将100g过硫酸铵溶解于900ml蒸馏水或支离子水中,制成10%过硫酸铵溶液,代替10%草酸溶液。
2)把浸蚀试样作为阳极,倒入10%草酸溶液,以不锈钢板或不锈钢片作为阴极,接通电路。电流密度为1A/cm2,浸蚀时间90s,浸蚀溶液温度20~50℃。用10%过硫酸铵溶液浸蚀时,电流密度为1A/cm2,浸蚀时间5~10min。
3)试样浸蚀后,用流水洗净。在金相显微镜下观察试样的全部浸蚀表面,放大倍数为200~500倍,根据其组织特征确定是否进行其它耐腐蚀试验。
(2)不锈钢硫酸-硫酸铁腐蚀试验方法(GB4334.2-84) 适用于将奥氏体不锈钢在硫酸-硫酸铁溶液中煮沸试验后,以腐蚀率评定晶间腐蚀倾向的一种试验方法。
试验步骤:
1)将硫酸用蒸馏水或去离子水配制成50±0.3%(质量百分比)的硫酸溶液,然后取该溶液600ml加入25g硫酸铁加热溶解配制成试验溶液。
2)测量试样尺寸,计算试样面积(取三位有效数字)。
3)试验前后称质量(准确到1mg)。
4)溶液量按试样表面积计算,其量不小于20ml/cm2。每次试验用新的溶液。
5)试样放在试验溶液中用玻璃支架保持于溶液中部,连续沸煮沸120h。每一容器内只放一个试样。
6)试验后取出试样,在流水中用软刷子刷掉表面的腐蚀产物,洗净、干燥、称重。
试验结果以腐蚀率评定为
W前-W后
腐蚀率=────── (g/m2.h)
St
式中 W前──试验前试样的质量(g);
W后──试验后试样的质量(g);
S──试样的表面积;
t──试验时间(h) 。
(3)不锈钢65%硝酸腐蚀试验方法(GB4334.3-84) 适用于将奥氏体不锈钢在65%硝酸溶液中煮沸试验后,以腐蚀率评定晶间腐蚀倾向的试验方法。
试验步骤:
1)试验溶液的配制 将硝酸用蒸馏水或去离子水配制成65±0.2%(质量百分比)的硫酸溶液。
2)、3)、4)同硫酸-硫酸铁试验方法。
5)每周期连续煮沸48h,试验五个周期。
试验结果以腐蚀率评定,同硫酸-硫酸铁试验方法。
焊接试样发现刀状腐蚀即为具有晶间腐蚀倾向,性质可疑时,可用金相法判定。
(4)不锈钢硝酸-氢氟酸腐蚀试验方法(GB4334.4-84) 适用于检验含钼奥氏体不锈钢的晶间腐蚀倾向。用在70℃、10%硝酸-3%氢氟酸溶液中的腐蚀率的比值来判定晶间腐蚀倾向。
试验步骤:
1)试验溶液:将硝酸和氢氟酸试剂,用蒸馏水或去离子水配制成质量分数为10%的硝酸-3%的氢氟酸试验溶液。
2)、3)同硫酸-硫酸铁试验方法。
4)将支架放入容器中,溶液量按试样表面积计算,其量不少于10ml/cm2。
5)装有试验溶液的容器放入恒温水槽中,试验溶液的温度加热到70±0.5℃时再将试样放入容器内的支架上,使试样处于溶液中部,连续保持2h。每一容器内只放一个试样。
6)同硫酸-硫酸铁试验方法。
7)试验两个周期,每周期为2h。每周期必须使用新的溶液。
试验结果以腐蚀率评定,同硫酸-硫酸铁试验方法。
将两周期的腐蚀率相加,然后按下式求腐蚀率的比值,取两位小数:
对于一般含碳量的钢种为
交货状态试样的腐蚀率
腐蚀率的比值=──────────────
再固溶处理后试样的腐蚀率
对于超低碳钢种(也用于焊接的非超低碳钢种)为
敏化处理后试样的腐蚀率
腐蚀率的比值=──────────────
交货状态试样的腐蚀率
(5)不锈钢硫酸-硫酸铜试验方法(GB4334.5-90) 适用于检验奥氏体、奥氏体-铁素体不锈钢在加有铜屑的硫酸-硫酸铜溶液中的晶间腐蚀倾向。
试验步骤:
1)试验溶液配制时将100g硫酸铜溶解于700ml蒸馏水或去离子水中,再加入100ml硫酸,用蒸馏水或去离子水稀释至1000ml,配制成硫酸-硫酸铜溶液。
2)试验前将试样用适当的溶剂或洗涤剂(非氯化物)去油并干燥。
3)在烧瓶底部铺一层铜屑,然后放置试样。保证每个试样与铜屑接触的情况下,同一烧瓶中允许放几层同一钢种的试样,但是,试样之间要互不接触。
4)试验溶液应高出最上层试样20mm以上,每次试验都应使用新的试验溶液。
5)将烧瓶放在加热装置上,通以冷却水,加热试验溶液,使之保持微沸状态,连续加热16h。
6)试验后取出试样、洗净、干燥、弯曲。
试验结果评定:焊接件试样弯曲角度为180°,沿熔合线进行弯曲。当试样厚度不大于1mm时,压头直径为1mm;当试样厚度大于1mm时,压头直径为5mm。弯曲后的试样在10倍放大镜下观察弯曲试样外表面,有无因晶间腐蚀而产生的裂纹。
(6)不锈钢5%硫酸腐蚀试验方法(GB4334.6-84) 适用于测定含钼奥氏体系不锈钢在沸腾5%硫酸溶液中的腐蚀失重,以试验不锈钢耐均匀腐蚀性能。
(7)不锈钢三氯化铁腐蚀试验方法(GB4334.7-84) 适用于测定不锈在35或50的6^三氯化铁溶液中的腐蚀率,以试验不锈钢耐点蚀性能。
(8)不锈钢42%氯化镁应力腐蚀试验方法(GB4334.8-84) 适用于试验不锈钢在沸腾42%氯化镁溶液中应力腐蚀裂纹敏感性的方法。
(9)不锈钢点蚀电位测量方法(GB4334.9-84) 适用于动电位法测量不锈钢在中性3.5%氯化钠溶液中的点蚀电位
分享:
0
喜欢