感应电炉在国内铸造企业中的应用可以追溯到上世纪七十年代,那时候工频感应电炉开始逐渐推广使用,在巅峰的时候曾经有过10t 2.8MW和20t4MW这样规格的工频感应电炉投入运行,然他们有很多的缺陷,并且最终也没有被大面积的推广,但是他们的出现开创了使用电力,以电磁感应的方式进行铸铁熔化的先例,为以后更先进的熔化方式指明了发展方向。
同期,随着电力半导体器件的出现,中频感应电炉在国外被发明并逐步完善(不包括中频发电机组),随后传入国内,从上世纪七十年代末开始国内也有研究和试验性质的应用,规模都不大。直到上世纪九十年代以后,在欧美一些公司的大力推广下,中频感应电炉在我国铸造行业才进入大规模的实际应用阶段。当时的主要设备都产自国外,有以老牌传统公司为代表的,采用并联谐振技术的中频感应电炉和以一些新兴公司为代表的,采用串联谐振技术的一拖二变频感应电炉。西安机电研究所也是在那时候开始从事于中频感应电炉技术的研究和推广,并且于世纪之初推出了基于IGBT器件的一拖二变频感应电炉,开创了国产高功率一拖二变频感应电炉的应用先例。
目前我国中频电炉行业发展非常迅猛,技术上,国产设备的水平已经接近国际最高水平。就中频电源来说,主电路采用的都是交流-直流-交流的换流方式,即先用整流器把工频市电整流成脉动直流电,再用滤波器把他变成平滑直流电,最后由逆变器逆变成单相中频。根据补偿电容器与负载联接形式的不同,可以分为串联谐振中频电源和并联谐振中频电源二种。
并联谐振电源因为补偿电容器和电炉的感应线圈自成振荡回路,流过逆变电力半导体器件的电流通常是负载电流的1/6—1/10(熔化负载),这使得并联谐振中频电源在相同的逆变电力半导体器件的条件下容易做到更大的功率。
串联谐振中频电源应用的比较晚,上世纪90年代以后才开始在国内推广应用。因为其独特的功率调节方式,可以实现一拖二输出,连续生产铁水而受到用户的青睐。通常中频电源的功率调节是在最前面的整流器上完成,通过控制整流可控硅的导电角来控制输出电压,达到调节输出功率的目的。串联谐振中频电源采用改变逆变器工作频率的方式来调节输出功率,当工作频率接近谐振频率时输出功率增加,远离时输出功率减小,而整流器的输出电压恒定不变,这也是串联谐振中频炉被称为变频炉的原因。正是因为这个特性,在一个整流器上面可以挂载多个逆变器,通过适当的功率互锁控制,只要保证所有逆变器的输出功率之和不超过整流器的有效负载能力,每个逆变器都能够独自控制各自的输出功率以满足需求。典型的应用就是一拖二变频炉,一台整流器带了二个逆变器驱动二台规格相同的电炉,这样可使一台变频电源的功率能灵活的分配给两台炉体,即把一台电源的大功率分配给熔化炉,余下小功率分配给保温炉,从而实现一熔化一保温,使电炉系统具备连续生产铁水的能力。
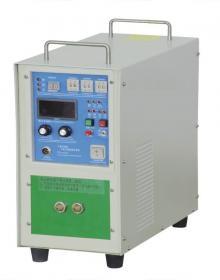
这二种类型的中频电源各自有其优点和缺点。因为整流器不需要控制,或只需浅度控制,使得串联谐振中频电源的网侧功率因数很高且与输出功率无关,这使他的应用不会增加电网的无功损耗。在连续的造型线上采用串联谐振一拖二电炉是典型的选择,一拖二工作方式为造型线连续供应铁水,串联谐振的原理使得保温的那个电炉不会给电网带来额外的无功。串联谐振使得逆变可控硅要通过全部的负载电流,相同的输出功率就需要更多的可控硅并联,这造成了二个问题,一是使设备的造价上升,二是更多的可控硅带来了更多的损耗,相同的设计规范下,每吨铁水的熔化成本将上升。并联谐振中频电源因为在整流器上控制输出功率,当输出功率降低的时候会产生较大的无功损耗,因此他适合于纯熔化的应用(基本不保温或很短的保温操作),类似于一班造型,一班熔化浇注,一班清理的生产流程就是其典型应用,高功率熔化完毕后铁水马上去浇注,中频电源基本没什么低功率工作的时间,也就不会产生额外的无功损耗。
回顾一百多年来感应熔化电炉的技术发展历程,从工频电炉(沟槽式和坩埚式)、倍频电炉、中频电炉发展到今天的可控硅变频电炉。可以看到它的技术发展一直围绕着三个目标进行的,这三个目标是:(1)适应于不断发展和完善的铸造熔化工艺的要求;(2)降低熔化单耗和提高生产率;(3)降低劳动强度,简化操作,满足社会对人文和环保的要求。这也是今后感应熔化技术的发展方向。具体表现在以下几个方面。
一、更先进的温度控制技术
感应熔化对温度的控制主要表现在出炉温度的控制,熔化中间过程的温度是没有意义的。传统的方法是在固体料全部熔化后的升温过程中,目测炉料的温度,人工判断接近出炉温度时,多次采用快速热电偶测量,直到温度符合要求后出炉。这种方法有很多弊端:(1)需要经验丰富的操作工人,(2)消耗很多的快速热电偶,(3)如果疏忽,炉料可能持续升温导致过热,造成化学成分的烧损或烧坏炉衬。
新的温度控制方法是采用基于能量平衡的控制技术。这是一个电脑软件,可以是内置于中频电源控制CPU中的简单的能量计算程序,或是安装在熔化管理计算机中,采用高级语言编制的复杂的软件。它的基本功能是不断监测中频电源的输出功率,统计出送入电炉的能量,同时,它还对环境温度,冷却水温度和流量进行连续监测,这用来计算电炉消耗的能量。送入电炉的能量和电炉消耗的能量的差就是炉料获得的能量,它和炉料的温度有着固定的关系,用适当的数学模型,就能够计算出炉料的温度。这类软件往往具备误差修正功能,能够根据计算和实测的误差,调整自己的计算模型,使以后的计算结果更加趋近实际结果。在生产实践中,良好的计算模型能够得到小于15度(熔化铸铁到1450度时)。
采用这样的温度控制技术后,熔化过程变得非常简单。不再需要人工判断温度,不再需要很多次的测温,也避免了炉料过热的危险。当炉料的温度达到要求时,控制软件能够自动的把中频电源的输出功率降到保温功率,然后提示操作人员温度已经符合要求。
二、恒功率控制技术
在一个完整的熔化过程中,电炉的阻抗不是恒定的,而是随炉料温度和炉料密实程度的变化而变化。通常,炉料温度越低,加料越密实,则电炉的阻抗就越小。如果以满炉额定温度的工况为基准的话,熔化过程中电炉阻抗的变化范围是这个数字的35%左右。电炉阻抗的变化有二个极端,一是冷态加满料,刚开始送电的时候,这时由于炉料温度低,电阻率小,所以电炉阻抗最小;另外一个极端发生在炉料的温度达到居里点的时候,这时候铁开始失去导磁性,但是又没有熔化,炉料的密实程度没有得到改善,这个时候电炉的阻抗最大。在这以后,随着温度的上升,熔化的铁水逐渐填满固体料之间的空隙,电炉的阻抗趋于稳定。串联谐振电源可以通过调节中频电源的工作频率,实现阻抗的调节。工作频率的变化能够直接改变电炉的阻抗,当电炉阻抗太低时,适当的升高工作频率,而阻抗太高时,则降低工作频率。通过这样的调节,能够使整个熔化过程中,电炉的阻抗基本一致,从而保证中频电源始终在额定功率下工作。并联谐振电源逆变器是用微控制器控制的,其逆变控制部分采用了人工智能控制程序,该程序在需要时可以小范围改变逆变器的逆变角(在可控硅关断时间允许范围内),因此使并联逆变器具有了小范围调节负载等效直流电阻的能力,和整流器的电流余量相配合,使这种可控硅并联逆变中频电源具有接近恒功率输出的能力(不能完全达到)。
三、负载匹配研究
中频电源和电炉及补偿电容构成了一个有机体,不可分割。负载的变化,或负载阻抗匹配的是否合适,会直接影响电源的额定功率;频率是否能达到设计的目标,也会影响感应加热的效率。感应线圈(负载)的设计计算十分复杂,要设计出一个满意的负载线圈并非易事。目前采用的计算方法是忽略次要参数,或依靠经验修正过的公式来设计,有较大误差。今后为方便这方面的设计,需要在理论指导下建立精确的数字模型,特别是利用计算机的仿真技术,以便更大范围地适应各种型式负载的计算精度。在国外,特别是美国,在负载感应器(线圈)用计算机辅助设计和仿真方面已开发了专用的软件,值得我们借鉴。
四、高功率因数与低谐波
IGBT串联谐振电源采用二极管整流,任何功率下功率因数都在0.95以上,可控硅串联谐振电源功率因数也在0.9以上,但是并联谐振电源的功率因数就很低了,在满功率情况下才能达到0.8-0.9。另外还有不可避免的谐波,对电网构成了一定的污染,电源功率越大,这种问题越突出。新一代电源必须是高功率因数,低谐波的电源。现在发展的技术有:多重化整流技术、全控功率管加上矩阵控制或PWM控制等技术、串联线路、斩波技术等。同时也催生了电源谐波的滤除和功率因数补偿的消谐装置的开发和生产。
五、节能减排
现代设计良好的中频电源(无论可控硅或IGBT)其变换效率一般都可达到98%以上。感应器—炉料系统的电效率仅取决与感应器—炉料系统自身,与中频电源的输出电压或逆变型式无关。设计良好的感应电炉的电效率通常可以达到78%以上。因此,在现有技术思路下提高感应电炉的熔化效率,不太可能取得很大幅度的提高。要做到比较大幅度的节能减排,就要在感应器和炉料系统上做文章,突破现有的框架,建立全新的设计模型,把系统电效率提高到90%以上。
以上探讨的技术和想法,有些已经初步实现,有些还在研究和实验中。随着技术的进步,一定还会有更先进,更理想的方法被发明和使用,使感应熔化技术向节能,清洁和高效方向持续发展。