测量系统分析
在日常生产中,我们经常根据获得的过程加工部件的测量数据去分析过程的状态、过程的能力和监控过程的变化;那么,怎么确保分析的结果是正确的呢?我们必须从两方面来保证,一是确保测量数据的准确性/质量,使用测量系统分析(MSA)方法对获得测量数据的测量系统进行评估;二是确保使用了合适的数据分析方法,如使用SPC工具、试验设计、方差分析、回归分析等。
测量系统的误差由稳定条件下运行的测量系统多次测量数据的统计特性:偏倚和方差来表征。偏倚指测量数据相对于标准值的位置,包括测量系统的偏倚(Bias)、线性(Linearity)和稳定性(Stability);而方差指测量数据的分散程度,也称为测量系统的R&R,包括测量系统的重复性(Repeatability)和再现性(Reproducibility)。
一般来说,测量系统的分辨率应为获得测量参数的过程变差的十分之一。测量系统的偏倚和线性由量具校准来确定。测量系统的稳定性可由重复测量相同部件的同一质量特性的均值极差控制图来监控。测量系统的重复性和再现性由GageR&R研究来确定。
分析用的数据必须来自具有合适分辨率和测量系统误差的测量系统,否则,不管我们采用什么样的分析方法,最终都可能导致错误的分析结果。在ISO10012-2和QS9000中,都对测量系统的质量保证作出了相应的要求,要求企业有相关的程序来对测量系统的有效性进行验证。
测量系统特性类别有F、S级别,另外其评价方法有小样法、双性、线性等.
分析工具
在进行MSA分析时, 推荐使用Minitab软件来分析变异源并计算Gage R&R和P/T。并且根据测量部件的特性,可以对交叉型和嵌套型部件分别做测量系统分析。
另外,Minitab软件在分析量具的线性和偏倚研究以及量具的分辨率上也提供很完善的功能,用户可以从图形准确且直观的看出量具的信息。
APQP
什么是APQP? APQP=Advanced Product Quality Planning
中文意思是:产品质量先期策划(或者产品质量先期策划和控制计划)是QS9000/TS16949质量管理体系的一部分。
定义及其他知识点:
产品质量策划是一种结构化的方法,用来确定和制定确保某产品使顾客满意所需的步骤。
产品质量策划的目标是促进与所涉及每一个人的联系,以确保所要求的步骤按时完成。
有效的产品质量策划依赖于高层管理者对努力达到使顾客满意这一宗旨的承诺。
理解要点
· 结构化、系统化的方法;
· 确保使产品满足顾客的需要和期望;
· 团队的努力,(横向职能小组是重要方法);
· 从产品的概念设计、设计开发、过程开发、试生产到生产,以及全过程中的信息反馈、纠正措施和持续改进活动;
· 不断采取防错措施降低产品风险(见“8.APQP与防错”);
· 持续改进;
· 制定必要的程序、标准和控制方法;
· 控制计划是重要的输出;
· 制定、实施时间表。
APQP的益处
—引导资源,使顾客满意;
—促进对所有更改的早期识别;
—避免晚期更改;
—以最低的成本、及时提供优质产品。
APQP的基础
1 组织小组
·横向职能小组是APQP实施的组织;
·小组需授权(确定职责);
·小组成员可包括:技术、制造、材料控制、采购、质量、销售、现场服务、供方、顾客的代表。
2 确定范围
具体内容包括:
·确定小组负责人;
·确定各成员职责;
·确定内、外部顾客;
·确定顾客要求;
·理解顾客要求和期望;
·评定所提出的设计、性能要求和制造过程的可行性;
·确定成本、进度和限制条件;
·确定需要的来自顾客的帮助;
·确定文件化过程和形式。
3 小组间的联系
· 顾客、内部、组织及小组内的子组之间;
· 联系方式可以是举行定期会议,联系的程度根据需要。
4 培训
·APQP成功取决于有效的培训计划;
·培训的内容:了解顾客的需要、全部满足顾客需要和期望的开发技能,例如:顾客的要求和期望、Working as a team 、开发技术、APQP、FMEA、PPAP等。
5 顾客和组织参与
· 主要顾客可以和一个组织开始质量策划过程;
·组织有义务建立横向职能小组管理APQP;
·组织必须同样要求其供方。
6 同步工程
·同步工程:横向职能小组同步进行产品开发和过程开发,以保证可制造性、装配性并缩短开发周期,降低开发成本;
理解要点
· 同步技术是横向职能小组为一共同目标努力的过程;
· 取代以往逐级转递的方法;
· 目的是尽早使高质量产品实现生产;
· 小组保证其他领域/小组的计划和活动支持共同的目标;
· 同步工程的支持性技术举例;
—网络技术和数据交换等相关技术;
—DFX技术;
—QFD;
—此外,同步工程还大量用到田口方法、FMEA和SPC等技术。
7 控制计划
控制计划—控制零件和过程的系统的书面描述。每个控制计划包括三个阶段;
·样件——对发生在样件制造过程中的尺寸测量、材料与性能试验的描述;
·试生产——对发生在样件之后,全面生产之前的制造过程中的尺寸测量、材料和性能试验的描述;
·生产——对发生在批量生产过程中的产品/过程特性、过程控制、试验和测量系统的综合描述。
8 问题的解决
·APQP的过程是解决问题的过程;
·解决问题可用职责—时间矩阵表形成文件;
·遇到困难情况下,推荐使用论证的问题—解决方法;
·可使用附录B中的分析技术。
9 产品质量先期策划的时间计划
·APQP小组在完成组织活后的第一件工作—制定时间计划;
·考虑时间计划的因素—产品类型、复杂性和顾客的期望;
·小组成员应取得一致意见;
·时间计划图表应列出—任务、职责分配及其它有关事项(参照附录B关键路径法):
·供策划小组跟踪进度和设定会议日期的统一格式;
·每项任务应有起始日期、预计完成时间,并记录实际情况;
·把焦点集中于确认要求特殊注意的项目,通过有效的状况报告活动支持对进度的监控。
10 与时间计划图表有关的计划
·项目的成功依赖于——以及时和价有所值方式;
·APQP时间表和PDCA循环要求APQP小组竭尽全力于预防缺陷。APQP的过程是采取防错措施,不断降低产品风险的过程;
·缺陷预防——由产品设计和制造技术的同步工程推进;
·策划小组应准备修改产品策划计划以满足顾客期望;
·策划小组的责任——确保进度满足或提前于顾客的进度计划。
APQP进度图
·五个过程;
·五个里程碑;
·前一个过程的输出是后一个过程的输入;
·各个过程在时间上重叠,体现同步工程;
·“反馈、评定和纠正措施”过程贯穿始终;
·一个策划循环的结束,另一个策划循环的开始;
时间进度表的一种常见形式——甘特图
甘特图举例
任务 时间进度
1月 2月 3月 4月5月 6月 7月 8月9月 10月 11月12月
计划与定义
产品设计与开发
过程设计与开发
产品与过程确认
反馈、评定和纠正措施
·关键路径法:在甘特图上以粗线表示需要最长时间完成的任务;同时以细线表示需并进行的任务子项,以提供以下重要的信息:
——各项任务之间的关系
——明确责任
——对问题及早预测
——资源分配
产品质量策划循环
·是著名的戴明PDCA质量循环概念在产品质量策划中的应用;
·持续改进是APQP循环的要点;
·APQP是QS—9000系统中不可或缺的重要子系统;
·APQP子系统中还包含其它许多系统,如FMEA,控制计划。
APQP的五个过程
1 计划和定义
本过程的任务:
·如何确定顾客的需要和期望,以计划和定义质量大纲;
·做一切工作必须把顾客牢记心上;
·确认顾客的需要和期望已经十分清楚。
2 产品的设计与开发
本过程的任务和要点:
·讨论将设计特征发展到最终形式的质量策划过程诸要素;
·小组应考虑所有的设计要素,即使设计是顾客所有或双方共有;
·步骤中包括样件制造以验证产品或服务满足“服务的呼声”的任务;
·一个可行的设计应能满足生产量和工期要求,也要考虑质量、可靠性、投资成本、重量、单件成本和时间目标;
·尽管可行性研究和控制计划主要基于工程图纸和规范要求,但是本章所述的分析工具也能猎取有价值的信息以进一步确定和优先考虑可能需要特殊的产品和过程控制的特性;
·保证对技术要求和有关技术资料的全面、严格的评审;
·进行初始可行性分析,以评审制造过程可能发生的潜在问题。
3 过程设计和开发
本过程的任务和要点:
—保证开发一个有效的制造系统,保证满足顾客的需要、要求和期望;
—讨论为获得优质产品而建立的制造系统的主要特点及与其有关的控制计划。
4 产品和过程的确认
本过程的任务和要点:
—讨论通过试生产运行评价对制造过程进行验证的主要要点。
—应验证是否遵循控制计划和过程流程图,产品是否满足顾客的要求。
并应注意正式生产前有关问题的研究和解决。
5 反馈、评定和纠正措施
本过程的任务与要点:
—质量策划不因过程确认就绪而停止,在制造阶段,所有变差的特殊原因和普通原因都会表现出来,我们可以对输出进行评价,也是对质量策划工作有效性进行评价的时候。
—在此阶段,生产控制计划是用来评价产品和服务的基础。
—应对计量型和计数型数据进行评估。采取SPC手册中所描述的适当的措施。
APQP先期产品质量策划
1、APQP新旧版本的区别
Ÿ结合客户强调之流程方法
Ÿ更新术语和概念
2、 产品质量先期策划(APQP)概述
APQP的定义和目的
APQP的十大基本原则
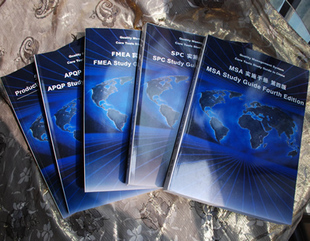
APQP和其他核心工具的关系
3、 产品的设计和开发
DFMEA定义
设计验证计划与报告
产品和过程特殊特性研究
4、 过程的设计和开发
过程开发与过程流程图
PFMEA 定义
控制计划和包装规范
5、 产品和过程的确认
测量系统分析
初始过程能力研究
生产件批准
质量策划认定
6、APQP五个阶段的输入和输出
计划和确定项目
产品设计和开发验证
过程设计和开发验证
产品和过程确认
反馈、评定和纠正措施
7、APQP实用技巧
APQP检查清单的使用
APQP审核中的常见问题
8、控制计划方法论(CP)
控制计划的三个阶段
控制计划的制定依据
控制计划栏目描述及填写要求
变差及其控制方法
控制计划的输入文件
控制计划编制技巧
控制计划的练习
SPC(1)
是Statistical Process Control的简称统计过程控制
利用统计的方法来监控制程的状态,确定生产过程在管制的状态下,以降低产品品质的变异
SPC(质量管理与控制)
统计工序控制 即SPC(Statistical Process Control)。它是利用统计方法对过程中的各个阶段进行控制,从而达到改进与保证质量的目的。SPC强调以全过程的预防为主。
SPC能解决之问题
1.经济性:有效的抽样管制,不用全数检验,不良率,得以控制成本。使制程稳定,能掌握品质、成本与交期。
2.预警性:制程的异常趋势可即时对策,预防整批不良,以减少浪费。
3.分辨特殊原因:作为局部问题对策或管理阶层系统改进之参考。
4.善用机器设备:估计机器能力,可妥善安排适当机器生产适当零件。
5.改善的评估:制程能力可作为改善前後比较之指标。
利用管制图管制制程之程序
1.绘制「制造流程图」,并用特性要因图找出每一工作道次的制造因素(条件)及品质特性质。
2.制订操作标准。
3.实施标准的教育与训练。
4.进行制程能力解析,确定管制界限。
5.制订「品质管制方案」,包括抽样间隔、样本大小及管制界限。
6.制订管制图的研判、界限的确定与修订等程序。
7.绘制制程管制用管制图。
8.判定制程是否在管制状态(正常)。
9.如有异常现象则找出不正常原因并加以消除。
10.必要时修改操作标准(甚至於规格或公差)。
分析用管制图主要用以分析下列二点:
(1)所分析的制(过)程是否处於统计稳定。
(2)该制程的制程能力指数(Process Capability Index)是否满足要求。
-控制图的作用
1.在质量诊断方面,可以用来度量过程的稳定性,即过程是否处于统计控制状态;
2.在质量控制方面,可以用来确定什么时候需要对过程加以调整,而什么时候则需使过程保持相应的稳定状态;
3.在质量改进方面,可以用来确认某过程是否得到了改进。
应用步骤如下:
1.选择控制图拟控制的质量特性,如重量、不合格品数等;
2.选用合适的控制图种类;
3.确定样本容量和抽样间隔;
4.收集并记录至少20~ 25个样本的数据,或使用以前所记录的数据;
5.计算各个样本的统计量,如样本平均值、样本极差、样本标准差等;
6.计算各统计量的控制界限;
7.画控制图并标出各样本的统计量;
8.研究在控制线以外的点子和在控制线内排列有缺陷的点子以及标明异常(特殊)原因的状态;
9.决定下一步的行动。
应用控制图的常见错误:
1.在5M1E因素未加控制、工序处于不稳定状态时就使用控制图管理工作;
2.在工序能力不足时,即在CP< 1的情况下,就使用控制图管理工作;
3.用公差线代替控制线,或用压缩的公差线代替控制线;
4.仅打“点”而不做分析判断,失去控制图的报警作用;
5.不及时打“点”,因而不能及时发现工序异常;
6.当“5M1E”发生变化时,未及时调整控制线;
7.画法不规范或不完整;
8.在研究分析控制图时,对已弄清有异常原因的异常点,在原因消除后,未剔除异常点数据。
分析用控制图
应用控制图时,首先将非稳态的过程调整到稳态,用分析控制图判断是否达到稳态。确定过程参数
特点:
1、分析过程是否为统计控制状态
2、过程能力指数是否满足要求?
控制用控制图
等过程调整到稳态后,延长控制图的控制线作为控制用控制图。应用过程参数判断
SPC的作用
1、确保制程持续稳定、可预测。
2、提高产品质量、生产能力、降低成本。
3、为制程分析提供依据。
4、区分变差的特殊原因和普通原因,作为采取局部措施或对系统采取措施的指南。
1. 贯彻预防原则是现代质量管理的核心与精髓。
2. 质量管理学科有一个非常重要的特点,即对于质量管理所提出的原则、方针、目标都要有科学措施与科学方法来保证它们的实现。这体现了质量管理学科的科学性。保证预防原则实现的科学方法就是:SPC (统计过程控制) 与SPD (统计过程诊断)。
SPC不是用来解决个别工序采用什么控制图的问题,SPC强调从整个过程、整个体系出发来解决问题。SPC的重点就在于“P(Process,过程)”
产品质量具有变异性
“人、机、料、法、环” + “软(件)、辅(助材料)、(水、电、汽)公(用设施)”
变异具有统计规律性
随机现象;统计规律
随机现象:在一定条件下时间可能发生也可能不发生的现象。
管制和一般的统计图不同,因其不仅能将数值以曲线表示出来,以观其变异之趋势,且能显示变异系属于机遇性或非机遇性,以指示某种现象是否正常,而采取适当之措施。
解析用控制图
?决定方针用
?制程解析用
?制程能力研究用
?制程管制准备用
管制用控制图
?追查不正常原因
?迅速消除此项原因
?并且研究采取防止此项原因重复发生之措施。
? 普通原因指的是造成随著时间推移具有稳定的且可重复的分布过程中的许多变差的原因,我们称之为:“处於统计控制状态”、“受统计控制”,或有时简称“受控”,普通原因表现为一个稳定系统的偶然原因。只有变差的普通原因存在且不改变时,过程的输出才可以预测。
? 特殊原因:指的是造成不是始终作用于过程的变差的原因,即当它们出现时将造成(整个)过程的分布改变。除非所有的特殊原因都被查找出来并且采取了措施,否则它们将继续用不可预测的方式来影响过程的输出。如果系统内存在变差的特殊原因,随时间的推移,过程的输出将不稳定。
? 局部措施
? 通常用来消除变差的特殊原因
? 通常由与过程直接相关的人员实施
? 大约可纠正15%的过程问题
? 对系统采取措施
? 通常用来消除变差的普通原因
? 几乎总是要求管理措施,以便纠正
? 大约可纠正85%的过程问题
? 合理使用控制图能
? 供正在进行过程控制的操作者使用
? 有於过程在质量上和成本上能持续地,可预测地保持下去
? 使过程达到
? 更高的质量
? 更低的单件成本
? 更高的有效能力
? 为讨论过程的性能提供共同的语言
? 区分变差的特殊原因和普通原因,作为采取局部措施或对系统采取措施的指南。
SPC的作用:
1、确保制程持续稳定、可预测。
2、提高产品质量、生产能力、降低成本。
3、为制程分析提供依据。
4、区分变差的特殊原因和普通原因,作为采取局部措施或对系统采取措施的指南。
SPC的焦点
──制程(Process)
Quality,是指产品的品质。换言之,它是著重买卖双方可共同评断与鉴定的一种「既成事实」. 而在SPC的想法上,则是希望将努力的方向更进一步的放在品质的源头──制程(Process)上.
因为制程的起伏变化才是造成品质变异(Variation)的主要根源.
1) 异常变动
过程中变动因素是不在统计管理状态下的非随机性原因,由于异常因素不是过程所固有,固不难除去,一般情况现场人员对异常因素的消除可以自行决定采取措施,而不必要请示更高级的管理人员,所以也称之为减少变动的局部措施。
2)偶然变动
过程中的变动因素是统计管理的状态下,其产品的特性有固定的分布,即分布位置、分布及分布形状三种,由于偶然因素是过程所固有的,难于消除,要消除偶然因素必须涉及到人、机、料、法、环境等整个系统的改造问题,需要投入大量的资金,故不是现场人员所能决定的,而必须经过深入的调查研究和做出全面的可行性报告后,再经高层领导做最后的定夺,所以称之为减少变动的系统措施。
特殊原因
一种间断性的,不可预计的,不稳定的变差来源。有时被称为可查明原因,存在它的信号是:存在超过控制线的点或存在在控制线之内的链或其他非随机性的情形。
普通原因
造成变差的一个原因,它影响被研究过程输出的所有单值;在控制图分析中,它表现为随机过程变差的一部分。
合理使用控制图的益处
• 供正在进行过程控制的操作者使用
• 有助于过程在质量上和成本上能持续的、可预测的保持下去
• 使过程达到:
• 更高的质量
• 更低的单件成本
• 更高的有效能力
• 为讨论过程的性能提供共同的语言
• 区分变差的特殊原因和普通原因,作为采取局部措施或对系统采取措施的指南
在实际应用中,当各组容量与其平均值相差不超过正负25%时,可用平均样本容量( )来计算控制限.
在什么条件下分析阶段确定的控制限可以转入控制阶段使用:
? 控制图是受控的
? 过程能力能够满足生产要求
控制图是根据稳定状态下的条件(人员、设备、原材料、工艺方法、测量系统、环境)来制定的。如果上述条件变化,则必须重新计算控制限,例如:
? 操作人员经过培训,操作水平显著提高;
? 设备更新、经过修理、更换零件;
? 改变工艺参数或采用新工艺;
? 改变测量方法或测量仪器;
? 采用新型原材料或其他原材料;
? 环境变化。
使用一段时间后检验控制图还是否适用,控制限是否过宽或过窄,否则需要重新收集数据计算控制限;
过程能力值有大的变化时,需要重新收集数据计算控制限。
对于p,np图, 过程能力是通过过程平均不合格品率 来表示,当所有点都受控后才计算该值.
当Cpk指数值降低代表要增加:
? 控制
? 检查
? 返工及报废,
在这种情况下,成本会增加,品质也会降低,
生产能力可能不足。
当Cpk指数值增大,不良品减少,最重要是产品/零件接近我们的“理想设计数值/目标”,给予顾客最大满足感。
当Cpk指数值开始到达1.33或更高时对检验工作可以减少,减少我们对运作审查成本。
? 普通原因变差
? 影响过程中每个单位
? 在控制图上表现为随机性
? 没有明确的图案
? 但遵循一个分布
? 是由所有不可分派的小变差源组成
? 通常需要采取系统措施来减小
? 特殊原因变差
? 间断的,偶然的,通常是不可预测的和不稳定的变差
? 在控制图上表现为超出控制限的点或链或趋势
? 非随机的图案
? 是由可分派的变差源造成该变差源可以被纠正
? 工业经验建议为:
? 只有过程变差的15%是特殊的可以通过与操作直接有关的人员纠正
? 大部分 (其余的85%) 是管理人员通过对系统采取措施可纠正的
? 控制图可以区分出普通原因变差和特殊原因变差
? 特殊原因变差要求立即采取措施
? 减少普通原因变差需要改变产品或过程的设计
控制图 - 过程的声音
? 试图通过持续调整过程参数来固定住普通原因变差,称为过度调整,结果会导致更大的过程变差造成客户满意度下降
? 试图通过改变设计来减小特殊原因变差可能解决不了问题,会造成时间和金钱的浪费
? 控制图可以给我们提供出出现了哪种类型的变差的线索,供我们采取相应的措施
? 能力指数的计算基于以下假设条件:
? 过程处于统计稳定状态
? 每个测量单值遵循正态分布
? 规格的上、下限是基于客户的要求
? 测量系统能力充分
? 如果理解关满足了这些假设后,能力指数的数值越大,潜在的客户满意度越高
过程能力分析的用途
-设计部门可参考目前之制程能力,以设计出可制
造的产品
-评估人员、设备、材料与工作方法的适当性
-根据规格公差设定设备的管制界限
-决定最经济的作业方式
过程控制和过程能力
◎目标:过程控制系统目标,是对影响过程的措施作出经济合理的决定, 避免过度控制与控制不足
◎过程能力讨论:必需注意二个观念
○由造成变差的普通原因来确定
○内外部顾客开心过程的输出及与他
们的要求的关系如何。
SPC就是利用统计方法去:
1.分析过程的输出并指出其特性.
2.使过程在统计控制情况下成功地进行和维持.
3.有系统地减少该过程主要输出特性的变异.
统计制程管制 (SPC)
它可用统计管制图及时监督与控制线场作业 .
它可用统计计算制程能力及规格 .
它可防止制程的偏差去影响产品的良率与品质 / 可靠性.
它可消除非机率原因的变异来改善制程.
SPC 就是依据 统计的逻辑来判断制程是否正常及应否采取改善对策的一套控制系统
简介 FMEA是一种可靠性设计的重要方法。它实际上是FMA(故障模式分析)和FEA(故障影响分析)的组合。它对各种可能的风险进行评价、分析,以便在现有技术的基础上消除这些风险或将这些风险减小到可接受的水平。
缩写
FMEA(失效模式与影响分析)
Failure Mode and Effects Analysis
潜在失效模式与后果分析
历史
50年代初,美国第一次将FMEA思想用于一种战斗机操作系统的设计分析;
60年代中期,FMEA技术正式用于航天工业(Apollo计划);
1976年,美国国防部颁布了FMEA的军用标准,但仅限于设计方面。
70年代末,FMEA技术开始进入汽车工业和医疗设备工业。
80年代初,进入微电子工业。
80年代中期,汽车工业开始应用过程FMEA确认其制造过程。
1988年,美国联邦航空局发布咨询通报要求所有航空系统的设计及分析都必须使用FMEA。
1991年,ISO-9000推荐使用FMEA提高产品和过程的设计。
1994年,FMEA又成为QS-9000的认证要求。
产品分类
概要
由于产品故障可能与设计、制造过程、使用、承包商/供应商以及服务有关,因此FMEA又细分为:
DFMEA:设计FMEA
PFMEA:过程FMEA
EFMEA:设备FMEA
SFMEA:体系FMEA
其中设计FMEA和过程FMEA最为常用。
DFMEA:设计FMEA
设计FMEA(也记为d-FMEA)应在一个设计概念形成之时或之前开始,并且在产品开发各阶段中,当设计有变化或得到其他信息时及时不断地修改,并在图样加工完成之前结束。其评价与分析的对象是最终的产品以及每个与之相关的系统、子系统和零部件。需要注意的是,d-FMEA在体现设计意图的同时还应保证制造或装配能够实现设计意图。因此,虽然d-FMEA不是靠过程控制来克服设计中的缺陷,但其可以考虑制造/装配过程中技术的/客观的限制,从而为过程控制提供了良好的基础。进行d-FMEA有助于:
· 设计要求与设计方案的相互权衡;
· 制造与装配要求的最初设计;
· 提高在设计/开发过程中考虑潜在故障模式及其对系统和产品影响的可能性;
· 为制定全面、有效的设计试验计划和开发项目提供更多的信息;
· 建立一套改进设计和开发试验的优先控制系统;
· 为将来分析研究现场情况、评价设计的更改以及开发更先进的设计提供参考。
PFMEA:过程FMEA
过程FMEA(也记为p-FMEA)应在生产工装准备之前、在过程可行性分析阶段或之前开始,而且要考虑从单个零件到总成的所有制造过程。其评价与分析的对象是所有新的部件/过程、更改过的部件/过程及应用或环境有变化的原有部件/过程。需要注意的是,虽然p-FMEA不是靠改变产品设计来克服过程缺陷,但它要考虑与计划的装配过程有关的产品设计特性参数,以便最大限度地保证产品满足用户的要求和期望。
p-FMEA一般包括下述内容:
· 确定与产品相关的过程潜在故障模式;
· 评价故障对用户的潜在影响;
· 确定潜在制造或装配过程的故障起因,确定减少故障发生或找出故障条件的过程控制变量;
· 编制潜在故障模式分级表,建立纠正措施的优选体系;
· 将制造或装配过程文件化。
EFMEA:设备FMEA有待完善
SFMEA:体系FMEA有待完善
活动目的目的
FMEA可以描述为一组系统化的活动,其目的是:
认可并评价产品/过程中的潜在失效以及该失效的后果;
确定能够消除或减少潜在失效发生机会的措施;
将全部过程形成文件.
在进行FMEA时有三种基本的情形,每一种都有其不同的范围或关注焦点:
情形1:新设计,新技术或新过程.FMEA的范围是全部设计,技术或过程.
情形2:对现有设计或过程的修改(假设对现有设计或过程已有FMEA).FMEA的范围应集中于对设计或过程的修改,由于修改可能产生的相互影响以及现场和历史情况.
情形3:将现有的设计或过程用于新的环境,场所或应用(假设对现有设计或过程已有FMEA).FMEA的范围是新环境或场所对现有设计或过程的影响.FMEA—8D流程的介绍
QS9000、ISO/TS16949、ISO9001、TL9000、ISO14001、OHSAS18001等管理体系中都有涉及到“预防措施”;依据“ISO9001:2000质量管理体系—基础和术语”的定义,“预防措施”是指“为消除潜在不合格或其他潜在不期望情况的原因所采取的措施”,或者简单地定义为:采取预防措施是为了防止发生。
在企业实际的管理体系运作中,虽然都会去编制一份有关“预防措施”的形成文件的程序,但真正可以达到预见性地发现较全面的潜在问题通常存在较大难度,也即:这样作业的可操作性不强;取而代之的主要是“纠正措施”;但“纠正措施”与“预防措施”的确是两个不同的概念,“纠正措施”是为了防止同样的问题再次出现所采取的措施。
为能有效地实施“预防措施”,使可能存在的潜在问题无法出现,需要一个从识别问题到控制潜在影响的管理系统,对于这一点,各企业都可能制定各自不同的方法以对应,这些方法也许都是适用的;但这里所要介绍的是一种行之有效且便于操作的制定和实施“预防措施”的方法,即:美国三大车厂(戴姆勒克莱斯特、福特、通用)制定的“潜在失效模式及后果分析”,或简称为FMEA。
FMEA于2002年推出第三版本,该第三版本较第二版本更具备简便的可操作性。FMEA在汽车零组件生产行业已被广泛的应用,同时这也是美国三大车厂对所属供应商的强制性要求之一。并于2008年6月推出第四版,第四版变动包括:格式更易于阅读;手册内增加的示例使人更易于理解和使用FMEA;强调FMEA过程和结果需要管理者支持、关注和评审;定义并强化对DFMEA和PFMEA的联系的理解,同时也定义和其他工具的关联;改进了严重度、发生频度、探测度的评级表;介绍了行业内目前使用的可选方法,如不再强调“标准表格”;建议不把RPN作为风险评估的首要方法。
FMEA 事实上就是一套严密的“预防措施”之识别、控制、提高的管理过程;其不仅可在汽车零组件行业可予使用,也可应用于任何期望能严格控制潜在问题出现的行业,尤其是产品(或服务)质量的好坏可能会极大影响到顾客利益的领域;因此,FMEA能在QS9000及ISO/TS16949一类的汽车业质量管理体系中运用,其同样可应用于其他管理体系之中,而且同样可以在企业内部形成一种严密的“预防措施”系统。
设备FMEA分析管理办法
1.目的:
对设备潜在失效模式及后果 (FMEA)分析的方法作出了规定,它是一种预防性分析技术, 目的是使设备得到有针对性的预测性维护.它是提高设备可靠性的有效方法.
2.范围:
本管理办法适用于重点设备的设备潜在失效模式及后果 (FMEA)分析.
3.术语:
3.1 预见性维护:基于过程数据,通过预测可能的失效模式以避免维护问题的活动.包括设备FMEA分析,精度测试,计划更换易损件,更新报废等.
3.2 设备FMEA:基于过程数据,通过预测可能的失效模式,依据其可维修性以及安全评价影响的每一失效严重程度和原因未被发现或某一失效模式正侵袭设备的使用者的可能性,对设备进行《设备/设施失效模式及影响分析》,即对作业性的可靠性(安全,可靠性,可维修性,有效性)进行预见性分析,以避免维护问题事故原因的可能性和主要失效模式发生.
3.3 重点设备:指对产品产能,质量,环保,安全,能源起关键作用的设备.
3.4可靠性:一定条件和一定时间内完成要求功能的能力.
3.5失效:不能正常工作.
3.6可维修性:故障出现后在给定时间被修复的概率.
3.7
3.8 作用时间:主动纠正的维护时间(诊断,修理,恢复).
4,职责
4.1装备部负责确定重点设备,形成《重点设备清单》并要求生产厂其《设备台帐》上予以注明,汇总各生产厂《重点设备备件计划》,编制公司所有《重点设备的备件计划》,并予以实施.
4.2装备部负责组织各生产厂进行重点设备的FMEA分析,并依据FMEA的分析结果提报备件计划及进行预见性维护.
5.相关的ISO/TS16949:2002标准条款:
相关条款
内容
7.5.1.4
预防和预见性维护
6.作业规范:
6.1准备阶段
-收集重点设备的厂商资料,包含设备技术参数等.
-收集重点设备此前出现的故障及维修记录.
-收集重点设备的日定修记录.
6.2建立FMEA分析小组
工作组由对进行FMEA有帮助的人员组成,包括但不限于:
-设备维护人员
-生产设备的使用人员.
-厂商维修代表(如必要).
6.3 设备FMEA 分析
6.3.1分析对象:重点设备(分类别).
6.3.2分析内容包括但不限于以下内容:
设备的功能要求,失效模式,失效后果,失效原因,现行措施,严重度,频度,探测度;
6.3.2.1失效模式:终止运行或运行不正常,达不到功能要求
-功能的完全丧失.
-功能退化,不能达到规定的性能.
-需求时无法完成其功能.
-不需求其功能时出现无意的作业.
6.3.2.2 失效原因:可能导致失效模式的最初的事件.
-某一失效模式可能有多种不同的原因引起,某一原因也可引起多种失效模式.
6.3.2.3 失效后果:
-对设备操作人员的影响;
-由该设备完成的生产停止任务;
-所制造的产品质量问题;
-人身或财产安全问题.
6.4 风险顺序数分析:
由装备部组织各生产厂的设备管理,技术及点检,维护人员,负责对重点设备进行FMEA分析,对风险特性评价,评价的结果至少要经上述人员共同评审过,方可被正式采用.具体评价规则如下:
风险顺序数的计算公式:RPN=S×O×D
S:严重度系数:后果的严重性(1-5);
O:频度系数,出现的概率(1-4);
D:不易探测度:早期发现的概率(1-4).
6.4.1严重度S:评价每一失效模式对应的后果,其依据是设备的可维修性,生产产品的质量以及安全性. 严重度系数S
影响选定条件
1.较小的失效,对设备的使用无主要影响,修复时间TI<60 min
2 .一般的失效,需要短期的修理,60 min ≤ TI<480 min
3 主要
主要的失效,需长期的行动,480 min ≤TI<1440 min或影响到设备的精度,被设备的使用者注意到并在设备人员的作用下得到纠正.
4 灾难性的
严重失效,TI>=1440 min 或出现因设备精度下降产生废品.
5 安全/质量
事故可能使在故障或操作期间涉及到个人的安全问题;或不适合该生产线继续从事生产任务.
6.4.2频度O:导致事故发生的原因出现的频率,失效模式发生的频率.
频度系数O
频率
确定条件
1
实际不存在
在设备的生命周期内,失效在相似的设备中不出现,或最多只出现一次.
2
罕有的
在类似的设备或现有的设备中,失效的发生比较罕见.可能每年出现一次故障;或部件应用了新技术,在理论上可以确信避免失效,但无类似设备运行的经验.
3
偶然的
失效偶然出现,在类似的,正在运行的设备中失效是每季度出现一次.
4
频繁的
某一部件或类似的现有设备失效频繁发生,失效每月出现一次或更多.
6.4.3探测度D:失效原因未被发现的可能性,或某一失效模式正在侵袭设备而未被发现的可能性.
探测度D
分级
发现难度
选择条件
1
总发现
该手段确保总能发现最初的原因,或在设备运转过程中的失效模式所引起的大多数主要因素都可得以避免.(操作者可探测到)
2
便于发现
失效的原因或模式是可发觉的,但有一种或少数几种不能被探测到.(设备维护检修人员可探测到)
3
难于发现
失效模式或原因被发现是很困难的,或探测元件几乎不能使用.(设备专业技术工程师可探测到)
4
内部不能发现
没有任何手段可以在该失效模式发生前被探测到.(设备厂商可以检测到)
6.5 纠正措施
6.5.1采取纠正措施的条件:
6.5.1.1 风险排序,按照RPN值高的.
6.5.1.2 S ≥4 或 O=4
6.5.2纠正措施
1)在以下几个方面,从设计到操作开始对设备进行调整或要求供应商采取相应措施:
-工作条件与人身安全要求;
-可靠性;
-内在的可维修性.
2)通过用户在后勤方面采取措施:
-维修政策;
-备用件组织;
-内在的可维修性.
3)优先采用设计纠正措施,然后采用后勤纠正措施.
4)设计纠正措施优先改进可靠性,然后改进可维修性.
5)对影响可靠性的关键零件,使用条件,系统化的预防维修采取措施.
6)设计确认(计算和实验),监督,预防性维修.
7)可维修性方面,快速诊断和维修跟踪;
6.6检查
设备FMEA必须附到生产设备或者提交给维修和技术部门的设备资产文件中.
7.本办法产生的记录:
重点设备清单
重点设备的备件计划
设备潜在失效模式及后果分析表
设备潜在失效模式及后果分析表(EFMEA)
设备名称:
核心成员/部门:
设备FMEA 编号:
编制日期:
共 页
适用产品:
编制:
审核:
修订日期:
第 页
项目/功能
潜在失效模式
潜在失效后果
严重度S
级别
潜在失效的起因/机理
频度O
现行设计控制
探测度D
R P N
建议措施
责任和目标完成日期
措施结果
预防
探测
采取的措施
S
O
D
R P N
包含内容
FMEA 是由美国三大汽车制造公司(戴姆勒-克莱斯勒、福特、通用)制定并广泛应用于汽车零组件生产行业的可靠性设计分析方法。其工作原理为:(1)明确潜在的失效模式,并对失效所产生的后果进行评分;(2)客观评估各种原因出现的可能性,以及当某种原因出现时企业能检测出该原因发生的可能性;(3)对各种潜在的产品和流程失效进行排序;(4)以消除产品和流程存在的问题为重点,并帮助预防问题的再次发生。
有关FMEA原理的应用主要体现在美国三大汽车制造公司制定的《潜在失效模式和后果分析》表格中。该表的内容包括:
(1)功能要求:填写被分析过程(或工序)的简要说明和工艺描述;
(2)潜在失效模式:记录可能会出现的问题点;
(3)潜在失效后果:推测问题点可能会引发的不良影响;
(4)严重度(S):评价上述失效后果并赋予分值(1-10分,不良影响愈严重分值愈高);
(5)潜在失效起因或机理:潜在问题点可能出现的原因或产生机理;
(6)频度(O):上述潜在失效起因或机理出现的几率(1-10分,出现的几率愈大分值愈高);
(7)现行控制:列出目前本企业对潜在问题点的控制方法;
(8)探测度(D):在采用现行的控制方法实施控制时,潜在问题可被查出的难易程度(1-10,查出难度愈大分值愈高);
(9)风险顺序数(RPN):严重度、频度、探测度三者得分之积,其数值愈大潜在问题愈严重,愈应及时采取预防措施;
(10)建议措施:列出“风险顺序数”较高的潜在问题点,并制定相应预防措施,以防止潜在问题的发生;
(11)责任及目标完成日期:制定实施预防措施的计划案;
(12)措施结果:对预防措施计划案实施状况的确认。
从上述内容不难看出,FMEA原理的核心是对失效模式的严重度、频度和探测进行风险评估,通过量化指标确定高风险的失效模式,并制定预防措施加以控制,从而将风险完全消除或减小到可接受的水平。因此FMEA原理不仅适用于汽车零配件生产企业的质量管理体系,也可应用于其他类似管理体系。D1-第一步骤:建立解决问题小组
若问题无法独立解决,通知你认为有关的人员组成团队。团队的成员必需有能力执行,例如调整机器或懂得改变制程条件,或能指挥作筛选等。D2-第二步骤:描述问题
向团队说明何时、何地、发生了什么事、严重程度、目前状态、如何紧急处理、以及展示照片和收集到的证物。想象你是FBI的办案人员,将证物、细节描述越清楚,团队解决问题将越快。D3-第三步骤:执行暂时对策
若真正原因还未找到,暂时用什么方法可以最快地防止问题?如全检、筛选、将自动改为手动、库存清查等。暂时对策决定后,即立刻交由团队成员带回执行。D4-第四步骤:找出问题真正原因
找问题真正原因时,最好不要盲目地动手改变目前的生产状态,先动动脑。您第一件事是要先观察、分析、比较。列出您所知道的所有生产条件(即鱼骨图),逐一观察,看看是否有些条件走样,还是最近有些什么异动?换了夹具吗?换了作业员?换了供应商?换了运输商?修过电源供应器?流程改过?或比较良品与不良品的检查结果,看看那个数据有很大的差?,尺寸?重量?电压值?CPK?耐电压?等等不良的发生,总是有原因,资料分析常常可以看出蛛丝马迹。这样的分析,可以帮助您缩小范围,越来越接近问题核心。当分析完成,列出您认为最有可能的几项,再逐一动手作些调整改变,并且观察那一些改变可使品质回复正常及影响变异的程度,进而找到问题真正的原因。这就是著名田口式方法最简单而实际的运用。D5-第五步骤:选择永久对策
找到造成问题的主要原因后,即可开始拟出对策的方法。对策的方法也许有好几种,例如修理或更新模具。试试对可能的选择列出其优缺点,要花多少钱?多少人力?能持续多久?再对可能的方法作一最佳的选择,并且确认这样的对策方法不会产生其它副作用。D6-第六步骤:执行及验证永久对策
当永久对策准备妥当,则可开始执行及停止暂时对策。并且对永久对策作一验证,例如观察不良率已由4000PPM降为300PPM,CPK由0.5升为1.8等,下游工段及客户己能完全接受,不再产生问题。D7-第七步骤:防止再发
对类似的其它生产,虽然尚未发生问题,亦需作同步改善,防止再发,即我们说的”他石攻错”。同时这样的失效,也应列入下一产品研发段的FMEA中予以验证。D8-第八步骤:团队激励
对于努力解决问题之团队予以嘉勉,使其产生工作上的成就感,并极乐意解决下次碰到的问题。无论是产发段发现的问题,或是量产、客诉问题,若公司每年有近百项的工程问题依照8D的方式来解决,对工程人员实力的培养着实可观,成为公司重要的资产,这也是很多公司将8D制式化的原因。
8D的运用,其实不只在工程上,您工作上,生活上碰到的很多问题,不妨也用8D的逻辑来思考看看
设计方法 FMEA实际是一组系列化的活动,其过程包括:找出产品/过程中潜在的故障模式;根据相应的评价体系对找出的潜在故障模式进行风险量化评估;列出故障起因/机理,寻找预防或改进措施。
故障模式、影响、分析模块
其核心部分是对特定系统进行分析研究,确定怎样修改系统以提高整体可靠性,避免失效。
为了准确计算失效的危害性,在分析时,提供了系统化的处理过程,自动编制FMEA任务,包括确定所有可能失效的零部件及其失效模式,确定每一种失效模式的局部影响、下一级别的影响以及对系统的最终影响,确定失效引起的危害性,确定致命失效模式以消除或减少发生的可能性或剧烈程度。
功能特点FMEA可完成以下功能
失效模式、影响分析(FMEA)
危害性分析(Critically Analysis)
功能FMEA(Functional FMEA)
破坏模式和影响分析(DMEA)FMEA具有以下特点
丰富的故障模式数据库
完善的企业FMEA规范定制功能
自动由FMEA生成原始的FTA(故障树)
故障树分析(Fault Tree Analysis)模块
利用FTA模块,在系统设计过程当中,通过对造成系统故障的各种因素(包括硬件、软件、环境、人为因素等)进行分析,画出逻辑框图(即故障树),从而确定系统故障原因的各种可能组合方式及其发生概率以计算系统故障概率,采取相应的纠正措施,以提供系统可靠性的一种分析方法。它以图形的方式表明了系统中失效事件和其它事件之间的相互影响,是适用于大型复杂系统安全性与可靠性分析的常用的有效方法。利用FTA,用户可以简单快速地建立故障树,输入有关参数并对系统进行定性分析和定量分析,生成报告,最后打印输出。
事件树分析(Event Tree Analysis)模块
ETA是一种逻辑的演绎法,它在给定一个初因事件的情况下,分析该初因事件可能导致的各种事件序列的结果,从而定性与定量地评价系统的特性,并帮助分析人员获得正确的决策。
ETA不仅适应于多因素,多目标,而且适用于大型的复杂系统。
ETA 主要有以下功能
非常友好简便的初因事件和事件序列的定义
简单快速的事件树中事件序列的概率计算
事件树报告的生成
ETA 为用户提供的是完全图示化的界面
ETA 与其它模块完全集成,如可直接故障树中的门和事件直接联接
支持多级分支分类
可处理多个事件树
FMEA有三种类型,分别是系统FMEA、设计FMEA和工艺FMEA,本文中主要讨论工艺FMEA。
1)确定产品需要涉及的技术、能够出现的问题,包括下述各个方面:
需要设计的新系统、产品和工艺;
对现有设计和工艺的改进;
在新的应用中或新的环境下,对以前的设计和工艺的保留使用;
形成FMEA团队。
理想的FMEA团队应包括设计、生产、组装、质量控制、可靠性、服务、采购、测试以及供货方等所有有关方面的代表。
2)记录FMEA的序号、日期和更改内容,保持FMEA始终是一个根据实际情况变化的实时现场记录,
需要强调的是,FMEA文件必须包括创建和更新的日期。
3) 创建工艺流程图。
工艺流程图应按照事件的顺序和技术流程的要求而制定,实施FMEA需要工艺流程图,一般情况下工艺流程图不要
轻易变动。
4)列出所有可能的失效模式、效果和原因、以及对于每一项操作的工艺控制手段:
4.1 对于工艺流程中的每一项工艺,应确定可能发生的失效模式.
如就表面贴装工艺(SMT)而言,涉及的问题可能包括,基于工程经验的焊球控制、焊膏控制、使用的阻焊剂
(soldermask)类型、元器件的焊盘图形设计等。
4.2 对于每一种失效模式,应列出一种或多种可能的失效影响,
例如,焊球可能要影响到产品长期的可靠性,因此在可能的影响方面应该注明。
4.3 对于每一种失效模式,应列出一种或多种可能的失效原因.
例如,影响焊球的可能因素包括焊盘图形设计、焊膏湿度过大以及焊膏量控制等。
4.4 现有的工艺控制手段是基于目前使用的检测失效模式的方法,来避免一些根本的原因。
例如,现有的焊球工艺控制手段可能是自动光学检测(AOI),或者对焊膏记录良好的控制过程。
5)对事件发生的频率、严重程度和检测等级进行排序:
5.1 严重程度是评估可能的失效模式对于产品的影响,10为最严重,1为没有影响;
事件发生的频率要记录特定的失效原因和机理多长时间发生一次以及发生的几率。
如果为10,则表示几乎肯定要发生,工艺能力为0.33或者ppm大于10000。
5.2 检测等级是评估所提出的工艺控制检测失效模式的几率,列为10表 示不能检测,1表示已经通过目前工艺控
制的缺陷检测。
5.3 计算风险优先数RPN(riskprioritynumber)。
RPN是事件发生的频率、严重程度和检测等级三者乘积,用来衡量可能的工艺缺陷,以便采取可能的预防措施
减少关键的工艺变化,使工艺更加可靠。对于工艺的矫正首先应集中在那些最受关注和风险程度最高的环节。
RPN最坏的情况是1000,最好的情况是1,确定从何处着手的最好方式是利用RPN的pareto图,筛选那些累积
等级远低于80%的项目。
推荐出负责的方案以及完成日期,这些推荐方案的最终目的是降低一个或多个等级。对一些严重问题要时常
考虑拯救方案,如:
一个产品的失效模式影响具有风险等级9或10;
一个产品失效模式/原因事件发生以及严重程度很高;
一个产品具有很高的RPN值等等。
在所有的拯救措施确和实施后,允许有一个稳定时期,然后还应该对修订的事件发生的频率、严重程度和检测
等级进行重新考虑和排序。
FMEA应用
FMEA实际上意味着是事件发生之前的行为,并非事后补救。
因此要想取得最佳的效果,应该在工艺失效模式在产品中出现之前完成。产品开发的5个阶段包括:
计划和界定、设计和开发、工艺设计、预生产、大批量生产。
作为一家主要的EMS提供商,Flextronics International已经在生产工艺计划和控制中使用了FMEA管理,在产品的
早期引入FMEA管理对于生产高质量的产品,记录并不断改善工艺非常关键。对于该公司多数客户,在完全确定设计和
生产工艺后,产品即被转移到生产中心,这其中所使用的即是FMEA管理模式。
手持产品FMEA分析实例
在该新产品介绍(NPI)发布会举行之后,即可成立一个FMEA团队,包括生产总监、工艺工程师、产品工程师、测试工
程师、质量工程师、材料采购员以及项目经理,质量工程师领导该团队。FMEA首次会议的目标是加强初始生产工艺MPI
(Manufacturing Process Instruction)和测试工艺TPI(Test Process Instruction)中的质量控制点同时团队
也对产品有更深入的了解,一般首次会议期间和之后的主要任务包括:
1.工艺和生产工程师一步一步地介绍工艺流程图,每一步的工艺功能和要求都需要界定。
2.团队一起讨论并列出所有可能的失效模式、所有可能的影响、所有可能的原因以及目前每一步的工艺控制,并对这些
因素按RPN进行等级排序。例如,在屏幕印制(screen print)操作中对于错过焊膏的所有可能失效模式,现有的工艺
控制是模板设计SD(Stencil Design)、定期地清洁模板、视觉检测VI(Visual Inspection)、设备预防性维护PM
(Preventive Maintenance)和焊膏粘度检查。工艺工程师将目前所有的控制点包括在初始的MPI中,如模板设计研
究、确定模板清洁、视觉检查的频率以及焊膏控制等。
3. FMEA团队需要有针对性地按照MEA文件中的控制节点对现有的生产线进行审核,对目前的生产线的设置和其他问题进
行综合考虑。如干燥盒的位置,审核小组建议该放在微间距布局设备(Fine-pitch Placementmachine)附近,以方
便对湿度敏感的元器件进行处理。
4. FMEA的后续活动在完成NPI的大致结构之后,可以进行FMEA的后续会议。会议的内容包括把现有的工艺控制和NPI大
致结构的质量报告进行综合考虑,FMEA团队对RPN重新进行等级排序,每一个步骤首先考虑前三个主要缺陷,确定好
推荐的方案、责任和目标完成日期。
对于表面贴装工艺,首要的两个缺陷是焊球缺陷和tombstone缺陷,可将下面的解决方案推荐给工艺工程师:
对于焊球缺陷,检查模板设计(stencildesign),检查回流轮廓(reflow profile)和回流预防性维护(PM)记录;
检查屏幕印制精度以及拾取和放置(pick-and-place)机器的布局(placement)精度.
对于墓石(tombstone)缺陷,检查屏幕印制精度以及拾取和放置(pick-and-place)机器的布局(placement)精度;
检查回流方向;研究终端(termination)受污染的可能性。
工艺工程师的研究报告表明,回流温度的急速上升是焊球缺陷的主要原因,终端(termination)受污染是墓石
(tombstone)缺陷的可能原因,因此为下一个设计有效性验证测试结构建立了一个设计实验(DOE),设计实验表明
一个供应商的元器件出现墓石(tombstone)缺陷的可能性较大,因此对供应商发出进一步调查的矫正要求。
5. 对于产品的设计、应用、环境材料以及生产组装工艺作出的任何更改,在相应的FMEA文件中都必须及时更新。
FMEA更新会议在产品进行批量生产之前是一项日常的活动。
批量生产阶段的FMEA管理
作为一个工艺改进的历史性文件,FMEA被转移到生产现场以准备产品的发布。
FMEA在生产阶段的主要作用是检查FMEA文件,以在大规模生产之前对每一个控制节点进行掌握,同时审查生产线的有
效性,所有在NPI FMEA阶段未受质疑的项目都自然而然地保留到批量生产的现场。
拾取和放置(pick-and-place)机器精度是工艺审核之后的一个主要考虑因素,设备部门必须验证布局机器的Cp/Cpk,
同时进行培训以处理错误印制的电路板。FMEA团队需要密切监视第一次试生产,生产线的质量验证应该与此同时进行。
在试生产之后,FMEA需要举行一个会议核查现有的质量控制与试生产的质量报告,主要解决每一个环节的前面三个问题。
FMEA管理记录的是一个不断努力的过程和连续性的工艺改进,FMEA文件应该总是反映设计的最新状态,包括任何在生产
过程开始后进行的更改。
结语
使用FMEA管理模式在早期确定项目中的风险,可以帮助电子设备制造商提高生产能力和效率,缩短产品的面市时间。
此外通过这种模式也可使各类专家对生产工艺从各个角度进行检测,从而对生产过程进行改进。
所推荐的方案应该是正确的矫正,产生的效益相当可观。为了避免缺陷的产生,需要对工艺和设计进行更改。使用统计
学的方法对生产工艺进行研究,并不断反馈给合适的人员,确保工艺的不断改进并避免缺陷产生。
现在流行的PFMEA主要由(RPN (Risk Priority Number) )来量化各项风险. RPN是由问题可侦测性(Probability of detection),问题严重性(Severity),问题发生频率(Probability of occurrence)三项的乘积来确定
产品案例 手持产品FMEA分析案例
在该新产品介绍(NPI)发布会举行之后,即可成立一个FMEA团队,包括生产总监、工艺工程师、产品工程师、测试工程师、质量工程师、材料采购员以及项目经理,质量工程师领导该团队。FMEA首次会议的目标是加强初始生产工艺MPI (Manufacturing Process Instruction)和测试工艺TPI(Test Process Instruction)中的质量控制点同时团队也对产品有更深入的了解,一般首次会议期间和之后的主要任务包括:
1.工艺和生产工程师一步一步地介绍工艺流程图,每一步的工艺功能和要求都需要界定。
2.团队一起讨论并列出所有可能的失效模式、所有可能的影响、所有可能的原因以及目前每一步的工艺控制,并对这些因素按RPN进行等级排序。例如,在屏幕印制(screen print)操作中对于错过焊膏的所有可能失效模式,现有的工艺控制是模板设计SD (Stencil Design)、定期地清洁模板、视觉检测VI(Visual Inspection)、设备预防性维护PM (Preventive Maintenance)和焊膏粘度检查。工艺工程师将目前所有的控制点包括在初始的MPI中,如模板设计研究、确定模板清洁、视觉检查的频率以及焊膏控制等。
3. FMEA团队需要有针对性地按照MEA文件中的控制节点对现有的生产线进行审核,对目前的生产线的设置和其它问题进行综合考虑。如干燥盒的位置,审核小组建议该放在微间距布局设备(Fine-pitch Placementmachine)附近,以方便对湿度敏感的元器件进行处理。
4. FMEA的后续活动在完成NPI的大致结构之后,可以进行FMEA的后续会议。会议的内容包括把现有的工艺控制和NPI大致结构的质量报告进行综合考虑,FMEA团队对RPN重新进行等级排序,每一个步骤首先考虑前三个主要缺陷,确定好推荐的方案、责任和目标完成日期。对于表面贴装工艺,首要的两个缺陷是焊球缺陷和tombstone缺陷,可将下面的解决方案推荐给工艺工程师:
对于焊球缺陷,检查模板设计(stencildesign),检查回流轮廓(reflow profile)和回流预防性维护(PM)记录;
检查屏幕印制精度以及拾取和放置(pick-and-place)机器的布局(placement)精度.
对于墓石(tombstone)缺陷,检查屏幕印制精度以及拾取和放置(pick-and-place)机器的布局(placement)精度;
检查回流方向;研究终端(termination)受污染的可能性。
工艺工程师的研究报告表明,回流温度的急速上升是焊球缺陷的主要原因,终端(termination)受污染是墓石(tombstone)缺陷的可能原因,因此为下一个设计有效性验证测试结构建立了一个设计实验(DOE),设计实验表明一个供应商的元器件出现墓石(tombstone)缺陷的可能性较大,因此对供应商发出进一步调查的矫正要求。
5. 对于产品的设计、应用、环境材料以及生产组装工艺作出的任何更改,在相应的FMEA文件中都必须及时更新。FMEA更新会议在产品进行批量生产之前是一项日常的活动。
批量生产阶段的FMEA管理作为一个工艺改进的历史性文件,FMEA被转移到生产现场以准备产品的发布。
FMEA在生产阶段的主要作用是检查FMEA文件,以在大规模生产之前对每一个控制节点进行掌握,同时审查生产线的有效性,所有在NPI FMEA阶段未受质疑的项目都自然而然地保留到批量生产的现场。
拾取和放置机器精度是工艺审核之后的一个主要考虑因素,设备部门必须验证布局机器的Cp/Cpk,同时进行培训以处理错误印制的电路板。FMEA团队需要密切监视第一次试生产,生产线的质量验证应该与此同时进行。在试生产之后,FMEA需要举行一个会议核查现有的质量控制与试生产的质量报告,主要解决每一个环节的前面三个问题。
FMEA管理记录的是一个不断努力的过程和连续性的工艺改进,FMEA文件应该总是反映设计的最新状态,包括任何在生产过程开始后进行的更改。
Process FMEA: Used to analyze transactional processes. Focus is on failure to produce intended requirement, a defect. Failure modes may stem from causes identified.
System FMEA: A specific category of Design FMEA used to analyze systems and subsystems in the early concept and design stages. Focuses on potential failure modes associated with the functionality of a system caused by design.
Design FMEA: Used to analyze component designs. Focuses on potential failure modes associated with the functionality of a component caused by design. Failure modes may be derived from causes identified in the System FMEA.
Other:
FMECA (Failure Mode, Effects, Criticality Analysis): Considers every possible failure mode and its effect on the product/service. Goes a step above FMEA and considers the criticality of the effect and actions, which must be taken to compensate for this effect. (critical = loss of life/product). A d-FMEA evaluates how a product can fail, and likelihood that the proposed design process will anticipate and prevent the problem. A p-FMEA evaluates how a process can fail, and the likelihood that the proposed control will anticipate and prevent the problem.
FMEA的实施程序 1)制定确认加工工序合格与否的标准
2)决定各工序的机能分析级别
3)作成加工程序的组合图
4)列举在每个加工工序中的不良类型
5)整理不良类型,选定一种作为研究讨论的对象
6)将所推测到的造成不良的各种原因列举出来
7)将不良类型按等级分类
8)研究讨论是否要进行设备的改善或工序的变更
(1)加工程序的确认
参考作业标准书作业指导书构成图,确认加工工序的流程,明确各工序的基准,规格。工程间的移动保管时间经过等在程序中要明确。
(2)工序的机能分析级别
工序的机能分析级别是根据生产线编成的分割出的1个工序的作业量(或设备的使用量)。因此,可根据需要变更分解的级别。
(3)加工程序的明确化
一般的FMEA的解析对象多为加工(O)和检查(口)工序,因为有工序间的物流方式,贮藏方法等作为解析对象被遗漏的情况,因此要特别注意。
(4)加工程序的流程图
加工程序的流程图的制作重点是品质及其影响方面的考虑,注意不要遗漏地记入全部工序。物流,贮藏工序也不例外。
PPAP
生产件批准程序(PPAP)规定了包括生产和散装材料在内的生产件批准的一般要求。PPAP的目的是用来确定供应商是否已经正确理解了顾客工程设计记录和规范的所有要求,以及其生产过程是否具有潜在能力,在实际生产过程中按规定的生产节拍满足顾客要求的产品。
适用范围 PPAP的全文翻译:Production part approval process。
PPAP必须适用于提供散装材料、生产材料、生产件或维修零件的内部和外部供应商现场。对于散装材料,除非顾客要求,PPAP可不作要求。
PPAP.exe为PPTV(原PPLIVE)的视频加速进程。即PPTV Accelerate Progress。
条文解释
本文中出现“必须”(shall)一词表示强制执行的要求。“应该”(should)一词表示强制执行的要求,但在执行方式上允许一些灵活性。
段落中标有“注”的词句是就所涉及的要求在理解方面和明确性上给予解释。标有“注”的语句中出现“应该”(should)一词表示仅供参考。
第一部分
I.1 总则
针对如下情况,供应商必须获得顾客产品批准部门的完全批准。
1. 新零件或产品(以前从未提供给顾客的特殊零件、材料或颜色)。
2. 对以前提交零件的不符合之处进行了纠正。
3. 由于设计记录、技术规范或材料方面的工程更改所引起的产品更改。
4. 第I.3节要求的任何一种情况。
I.2 PPAP的过程要求
I.2.1生产件:用于PPAP的产品必须取自有效的生产过程。
所谓有效的生产过程:
l 一小时至八小时的生产。
l 且至少为300件连续生产的部件,除非顾客授权的质量代表另有规定。
l 使用与生产环境同样的工装、量具、过程、材料和操作工进行生产。
l 每一独立生产过程制造的零件,如相同的装配线和/或工作单元、多腔冲模、铸模、工装及仿形模的每一腔位的零件都必须进行测量,并对代表性的零件进行试验。
I.2.2 PPAP要求
l 供应商必须满足所有规定要求,如设计记录、规范,对于散装材料,还需要有散装材料要求的审核清单。
l 任何不符合要求的检测结果都会成为供应商不得提交零件、文件和/或记录的理由。
l PPAP的检验和试验必须由有资格的实验室完成。所使用的商业性/独立的实验室必须是获得认可的实验室机构。
l 供应商委托商业性实验室做试验时,必须用带有实验室名称的报告格式或是采用正规的实验室报告提交试验结果。报告中必须填写清楚实验室名称、试验日期、试验所采用的标准。对任何试验结果只笼统性地描述其符合性是不可接受的。
l 无论零件的提交等级如何,供应商必须对每个零件或同族零件保存相应的记录。这些记录必须在零件的PPAP文件中列出,或在该类文件中有所说明,并随时备查。
l 供应商若想获得例外或偏离PPAP要求,必须事先得到顾客产品批准部门的认可。
I.2.2.1 设计记录
供应商必须具备所有的可销售产品的设计记录。
注:无论谁负责设计,任何可售产品、零件或部件将只有一份设计记录,设计记录可以引用其它文件,并使之成为设计记录中的一部分。
I.2.2.2 授权工程更改文件
针对未在设计记录上体现,但已在产品零件或工装上体现的一切更改,供应必须获得授权工程更改文件。
I.2.2.3 要求的工程批准
在设计记录有规定时,供应商必须具有顾客工程批准的证据。
I.2.2.4 设计失效模式及后果分析(设计FMEA)
如果供应商负责设计,应进行设计失效模式及后果分析(DFEMA)。
I.2.2.5 过程流程图
供应商必须以特定格式设计一份过程流程图,并能清晰地描绘出生产工艺步骤和顺序,且满足特定顾客的需求和期望。
I.2.2.6 过程失效模式及后果分析(过程FMEA)
供应商必须遵循QS-9000第三版要求进行过程FEMA的分析。
I.2.2.7 尺寸检验结果
l 提供尺寸验证已经完成,以及其结果表明符合规定要求的证据
l 标明设计记录的日期、更改等级和全尺寸结果清单、经批准的工程更改文件。
l 在所测量的零件中指定一件为标准样件。
l 在所有的辅助文件上记录更改的等级、绘图日期、供应商名称和零件编号。
l 供应商必须提供每个独立的加工过程尺寸结果。
I.2.2.8 材料/性能试验结果记录
供应商必须保存设计记录或控制计划中规定的材料和/或性能试验结果记录。
I.2.2.8.1 材料试验结果
设计记录或控制计划规定有化学、物理、金相要求时,供应商必须对所有的零件和产品材料进行试验材料试验报告必须标明:
l 试验零件的设计记录更改级别、编号、日期和试验技术规范的更改级别。
l 进行试验日期。
l 材料分供商的名称,以及当顾客提出要求时,注明他们在顾客批准的分供商名单上的材料供方代码号。
I.2.2.8.2 性能试验结果
当设计记录或控制计划规定有性能或功能要求时,供应商必须对所有零件或产品材料进行试验试验报告必须标明:
l 试验零件的设计记录更改级别、编号、日期、试验零件依据的技术规范更改级别。
l 还未体现在设计记录的授权工程更改文件。
l 进行试验的日期。
I.2.2.9 初始过程研究
I.2.2.9.1 总则
l 对于顾客或供应商指定的所有特殊特性,必须在提交之前确定其初始工序能力或性能是可接受的。
l 供应商必须进行系统分析来了解测量误差对研究测量结果的影响。
注1:此项要求是为了确定生产过程是否可能生产出满足顾客要求的产品。初始工序分析重点是在计量值数据而非计数值数据。
注2:工序能力或性能的评价指数是经顾客和供应商双方同意的。在下文中将介绍CPK和PPK指数。对于某些工序或产品,其它方法更适用,在事先得到顾客批准的情况下可替代上述方法。
注3:初始工序分析是短期的,它不能预测到时间的变化和人员、材料、方法、设备、测量系统和环境的改变所产生的影响。尽管是短期分析,采用控制图,按照顺序收集和分析数据也很重要。
注4: 对于可以采用X-Bar和R图的那些特性、短期分析应该是在从批量试生产过程中进行采样,零件的样品量最小为25,含有至少100个读数的基础上进行。
I.2.2.9.2 质量指数
如果适用,初始工序研究应该采用能力或性能指数来最终体现CPK-稳定过程的能力指数。σ的估计值是依据子组内的变差确定的(R-bar/d2或S-bar/C4)PPK-性能指数。根据总变差估计σ值(所有单个样本数据使用标准偏差(均方根等式),“S”) 短期研究。初始过程研究的目的是了解过程变差,而不是达到一个规定的指数值。当可能得到历史的数据或有足够的初始数据来绘制控制图时(至少100个个体样本),可以在过程稳定时计算CPK。对于输出满足规范要求且呈可预测的波形,长期不稳定过程使用PPK。
I.2.2.9.3 初始研究接收准则
供应商必须采用下面接收准则评价稳定过程初始过程研究结果:
结果 说明
指数值>1.67 该过程目前满足顾客要求。批准后开始生产并执行控制计划。
1.33≤指数值≤1.67 该过程目前可接受,但可能还需要一些改进。与顾客联系并评审结果。如果在开始批量生产之前没有改进,则需要更改控制计划。
指数值<1.33 该过程目前没有达到满足顾客要求的接收准则。评审分析结果请与相关的顾客代表联系。
I.2.2.9.4 不稳定过程
根据不稳定的性质,不稳定过程可能不满足顾客的要求。供应商必须进行鉴定和评价,尽可能在提交PPAP前消除引起波动的明显原因。供应商必须通知顾客不稳定过程的情况,必须在提交PPAP前提供一份纠正措施计划。
I.2.2.9.5 单侧公差或非正态分布的过程
对于单侧公差或非正态分布的过程,供应商必须和顾客共同确定接收准则。
I.2.2.9.6 不符合接收准则时的对策
如果过程不能改进,供应商必须与顾客取得联系,如果在PPAP提交允许的日期之前仍不能达到接受准则,那么供应商必须向顾客提交一份纠正措施计划、一份通常包含100%检验的修改的控制计划。持续进行减少变差的努力,直到PPK或CPK达到1.33或更大时,或直到从顾客那里获得了完全批准为止。
I.2.2.10 测量系统分析研究
供应商必须对所有用于生产的新量具、修正量具、试验设备进行适当测量系统分析研究,如量具的双性、偏倚、线性、稳定性研究等。
I.2.2.11 合格的实验室文件
供应商必须有一份实验室范围和说明所使用的实验室遵循QS-9000第三版,4.10.6和/或4.10.7节的证明文件
I.2.2.12 控制计划
供应商必须制订一份控制计划来规定所有过程控制内容,此控制计划必须遵循QS-9000要求
I.2.2.13 零件提交保证书 (PSW)
圆满完成了所有要求的测量和试验后,供应商必须填写零件提交保证书(PSW) 对于每一个零件编号都必须完成一份单独的PSW,除非顾客同意采用其他的形式。 如果生产零件是采用多模腔、铸模、工装、冲模或仿形模或生产工艺(例如,生产线或加工单元)加工出来的,供应商必须对每个零件进行完整的尺寸评价。供应商必须在保证书或附件中的“铸模/型腔/生产工艺”栏中注明提交零件的特定型腔、铸模和生产线等。
I.2.2.13.1 零件重量(质量)
供应商必须在PSW上记录要发运的零件重量,除非顾客另有规定,否则一律用千克(kg)表示,并精确到小数点后4位(0.0000)。重量不能包括运输时的保护装置、装配辅具或包装材料。为了确定零件重量,供应商必须随机选择10个零件分别称重,然后计算并报告平均重量。用于生产实现的每个型腔、模具、生产线或过程都必须至少选取一个零件进行称重。
I.2.2.14 外观批准报告(AAR)
如果在设计记录上某一要求提交的零件或零件系列有外观要求,则必须完成该产品/零件一份单独的外观批准报告(AAR)。
I.2.2.15 散装材料要求检查清单(仅适用于散装材料的PPAP)
对于散装材料,散装材料要求检查清单必须经顾客和供应商达成一致。所有规定的要求必须满足,除非在检查清单上特别指明“没有要求”(NR)。
I.2.2.16 生产件样品
供应商必须按照顾客的要求和提交要求规定内容提供零件样品。
I.2.2.17 标准样品
供应商必须保存一件标准样品与生产件批准记录保存时间相同。
I.2.2.18 检查辅具
如果顾客提出要求,供应商必须在提交PPAP时同时提交零件特殊装配辅具或部件检查辅具。
供应商必须确定检查辅具的所有内容与零件尺寸要求一致。提交时,供应必须将纳入检查辅具的工程设计更改形成文件。供应商必须在零件寿命期内,对任何检查辅具提供预防性维护。
必须按照顾客要求进行测量系统分析研究,如:量具的双性、偏倚、线性和稳定性研究。
I.2.2.19 顾客的特殊要求
供应商必须有与所有适用的顾客特殊要求相符合的记录。
对于散装材料,在散装材料要求检查清单上必须对所有的顾客特殊要求形成文件。
I.3 顾客通知和提交要求
I.3.1 顾客通知
以下情况发生时,供应商必须通知顾客负责产品批准部门。顾客可能因此会决定要求提交PPAP批准。
1. 和以前批准的零件或产品相比,使用了其它不同的制造或材料;
2. 使用新的或改进的工装(不包括易损工装)、模具、铸模、模型等,包括附加的或替换用的工装;
3. 在对现有的工装设备进行翻新或重新布置之后进行生产;
4. 生产是在工装和设备转移到不同的工厂或在一个新增的厂址进行的;
5. 分供应商对零件、非等效材料、或服务(如:热处理、电镀)的更改,从而影响顾客的装配、成型、功能、耐久性或性能的要求;
6. 在工装停止批量生产达到或超过12个月以后重新启用而生产的产品;
7. 涉及由内部制造的,或由供应商制造的生产件的产品和过程更改。这些部件会影响到适销产品的装配性、成型、功能、性能和/或耐久性;
8. 仅适用于散装材料:
l 新的或现有的分供应商提供的具有特殊特性的原材料的新货源;
l 在没有外观规范的情况下,产品外观属性的更改;
l 在相同的过程中变更了参数(属已批准的产品的PFMEA参数以外部分,包括包装);
l 已批准产品的DFMEA(产品组成、成分等级)以外部分的更改。
9. 试验/检验方法更改、新技术采用(不影响接受准则)。
I.3.2 顾客提交要求
在下列情况下,供应商必须在首批产品发运前提交PPAP批准,除非负责产品批准部门放弃了该要求。不论顾客是否要求正式提交,供应商必须在需要时对PPAP文件中所有适用的项目进行评审和更新,以反应生产过程的情况。
1. 新的零件或产品(例如:以前未曾提供给某顾客的一种特定的零件、材料、或颜色);
2. 对以前提交零件的不符合进行纠正;
3. 关于生产产品/零件编号的设计记录、技术规范、或材料方面的工程更改;
4. 只对散装材料:对于供应商来讲,在产品上采用了以前未曾用过的新的过程技术。
I.3.3 顾客不要求通知的情况
在下列情况下不要求通知顾客和提交(如:PSW)。供应商有责任跟踪更改和/或改进,并更新任何受到影响的PPAP文件。
注:任何情况下,一旦影响顾客产品的装配性、成型、功能、性能和/或耐久性,便要求通知顾客。
1. 对部件及图纸的更改,内部制造或由分供应商制造,不影响到提供给顾客产品的设计记录;
2. 工装在同一工厂内移动(用于等效的设备,过程流程不改变,不拆卸工装),或设备在同一工厂内移动(相同的设备、过程流程不改变);
3. 设备方面的更改(具有相同的基本技术或方法的相同的过程流程);
4. 同样的量具更换;
5. 重新平衡操作工的作业含量,对过程流程不引起更改;
6. 导致减少PFMEA的RPN值的更改(过程流程没有更改);
7. 只对散装材料:
l 对批准产品DFMEA(配方范围、包装设计)更改;
l 对PFMEA(过程参数)的更改;
l 不会严重影响到特殊特性(包括在批准的规范限值内改变目标值点)的更改;
l 对批准的商品成分的更改(在化学提纯服务(CAS)系列中CAS数字没有改变);
l 生产不涉及特殊特性的原材料的分供应商生产现场发生变化;
l 不涉及特殊特性的原材料的新货源;
l 加严的顾客/销售接受容差限值。
I.4 顾客提交要求-证明的等级
I.4.1 提交等级
供应商必须按照顾客要求的等级,提交该等级规定的项目和/或记录;
等级1-只向顾客提交保证书(对指定的外观项目,还应提供一份外观批准报告);
等级2-向顾客提交保证书和产品样品及有限的支持数据;
等级3-向顾客提交保证书和产品样品及完整的支持数据;
等级4-提交保证书和顾客规定的其它要求;
等级5-在供应商制造厂备有保证书、产品样品和完整的支持性数据以供评审。
如果顾客负责产品批准部门没有其它的规定,则供应商必须使用等级3作为默认等级,进行全部提交。只供应散装材料的供应商必须使用等级1作为默认等级,提交所有散装材料的PPAP文件,除非顾客负责产品批准部门另有规定。
I.4.1 保存/提交要求表
要求 提交等级
等级1 等级2 等级3 等级4 等级5
1.可销售产品的设计记录 R S S * R
- 对于专利部件/详细资料 R R R * R
- 对于所有其它部件/详细资料 R S S * R
2. 工程更改文件,如果有 R S S * R
3.顾客工程批准,如果要求 R R S * R
4.设计FMEA R R S * R
5.过程流程图解 R R S * R
6.过程FMEA R R S * R
7.尺寸结果 R S S * R
8.材料、性能试验结果 R S S * R
9.初始过程研究 R R S * R
10.测量系统分析研究 R R S * R
11.具有资格的实验室文件 R S S * R
12.控制计划 R R S * R
13.零件提交保证书(PSW) S S S S R
14.外观批准报告(AAR),如 S S S * R
果适用
15.散装材料要求检查清单 R R R * R
16.样品产品 R S S * R
17.标准样品 R R R * R
18.检查辅具 R R R * R
19.符合顾客特殊要求的记录 R R S * R
S =供应商必须向指定的顾客产品批准部门提交,并在适当的场所,包括制造场所,保留一份记录或文件项目的复印件。
R =供应商必须在适当的场所保存,顾客代表有要求时应易于得到。
*=供应商必须在适当的场所保存,并在有要求时向顾客提交。
I.5 零件提交状态
I.5.1 总则
顾客必须通知供应商关于提交的审批结果。获得生产件批准后,供应商必须保证将来生产继续满足顾客的要求。
I.5.2 顾客PPAP状态
I.5.2.1 完全批准是指零件满足顾客的所有技术规范和要求。因此,供应商要根据顾客计划部门定货计划按量发运零件。
I.5.2.2 临时批准允许按限定时间或零件数量运送生产需要的材料。供应商只有在下列情况,才给予临时批准:
- 已明确了影响生产批准不合格的根本原因;
- 已准备了一份顾客同意的临时批准措施计划。为获得“完全批准”需再次提交。
获得临时批准的材料,若到使用截止期或授权发货数量已满时,仍未满足即定改进措施计划,则拒收。如果没有同意延长临时批准,则不允许再次发运。
散装零件,供应商必须使用“散装材料临时批准”表格。
I.5.2.3 拒收是指从生产批次中选取用于提交的样品和文件不符合顾客要求。必须提交更改的产品和文件,并获得批准后,才能批量发运。
I.6 记录保存
无论按哪种等级提交,生产零件批准的记录必须保存的时间是零件在用时间再加一个日历年。
零件提交保证书的填写
零件资料
1. 零件名称
2. 顾客零件编号:工程签发的最终零件名称和编号。
3. 安全/法规项:若零件图上注明为安全/法规项,则选择“是”,否则为“否”。
4. 工程图样更改等级和批准日期:说明更改的等级和提交日期。
5. 附加的工程更改:列出所有在图样上没有纳入的,但已在该零件上体现的,并已批准的工程更改。
6. 图纸编号:规定提交的顾客零件编号的设计记录。
7. 采购订单代号:依据采购订单填入本代号。
8. 零件重量:填入用千克表示的零件实际重量,精确到小数点后四位。
9. 检查辅具代码:如果辅助工具用于尺寸检验,应填入其代号。
10. 工程更改等级和批准日期。
供应商制造厂信息
11. 供应商名称和供应商代码:填入在采购订单上指定的制造厂址代码。
12. 供应商制造厂地址:填入零件生产地的完整的地址。
提交信息
13. 提交类型:选择提交类型,并在相应的方框上划“√”。
14. 顾客名称:填入公司名称和分部或工作组。
15. 买方名称:和买方的代码:填入买方名称和代码。
16. 适用范围:填入年型、车辆名称、或发动机、变速器等。
提交原因
17. 选择合适的项目,并在相应方框上划“√”,在“其他”栏上加注细节说明。
要求的提交等级
18. 标明由顾客要求的提交等级。
提交结果
19. 选择合适的项目,并在相应方框上划“√”,包括尺寸、材料试验、性能试验、外观评价和统计数据。
20. 选择合适的项目,并在相应方框上划“√”。如果是“否”,应在下面“说明”栏中进行 解释。
21. 说明:提供关于提交结果的详细说明;适当时,可在附件中进行附加解释。
22. 在证实了各项结果符合所有顾客要求及顾客所要求的所有文件全部准备妥当后,供应商负责人必须对声明的内容进行签批,并提供职务、电话号码和传真号码。
仅供顾客使用 不填。
外观件批准报告的填写
1. 零件号:零件统一编号。
2. 图样号:如果与零件号不同,应填写绘有该零件的图样号。
3. 适用范围:填入使用该零件的车型的代号或其它项目名称。
4. 零件名称:填写按该零件图样已经完工的零件名称。
5. 买方代码:填入具体购买此零件的买方代码。
6. 工程更改水平日期:工程更改水平和本次提交的工种更改日期。
7. 供应商名称:负责提交的供应商(也适用分供应商)
8. 制造地点:制造和组装零件的地点。
9. 供应商代码:顾客指定的供应商生产和组装零件的地点的代码。
10. 提交原因:选择合适项目解释本次提交的原因,在相应的方框上划“√”。
11. 供应商的表面加工资料:列出所有第一层表面加工工具、磨料来源、磨粒类型、纹理以及用来检查的光泽度标准样品。
12. 表面预处理评价:由顾客所有代表完成(GM公司不使用)
13. 颜色标注:填入字母和数字或数字表示颜色的识别号。
14. 三色数据:对提交的零件,列出与顾客认可的标准样品相比的(色度计)数据。
15. 标准样品代号:填入字母和数字式的标准识别号(福特汽车公司不使用)。
16. 标准样品批准日期:填入标准样品批准的日期。
17. 材料类型:标明第一层表面处理和基底(如:油漆/ABS)。
18. 材料来源:标明第一层表面抛光和基底的供应商。如:Redspot/DOW公司。
19. 颜色评价、色彩、色调、色品度、金属光泽和亮度:由顾客目测。
20. 颜色供货标志:彩色零件号下标或色号。
21. 零件交接:由顾客决定(批准/拒绝)。
22. 说明:供应商或顾客的一般说明(任选项)。
23. 供应商签名、电话号码和日期:供应商证明资料准确并满足所有规定要求。
24. 顾客代表签名和日期:顾客批准签字。
PPAP产品件批准程序
1、产品件批准程序(PPAP)概述
?PPAP的定义和目的
–PPAP适用性
–PPAP过程要求
2、PPAP的提交
?提交要求
–概要
–顾客通知和提交要求
–何时需要提交
–何时不要求提交
–无论是否提交
?提交等级
?零件提交状态
–完全、临时批准
–再次提交PPAP情况
–顾客拒收情况
?向顾客提交PPAP证据的五个等级
3、PPAP 过程要求
?设计记录的尺寸编号
?授权的工程变更文件
?IMDS报告样
?初始过程研究的性能指数
?有资格的实验室
?外观件批准报告(AAR)
?生产件样品与批准样品
?检查辅具
?顾客设计记录规定的特殊性
?和顾客特殊要求的区别
4、记录的保存要求
?记录的保存时间
?使用记录的包括或引用