I,Pencil
My Family Tree as told toLeonard E. Read
Iam a lead pencil—the ordinary wooden pencil familiar to all boysand girls and adults who can read andwrite.*
Writing is both myvocation and my avocation; that's all Ido.
You may wonder why Ishould write a genealogy. Well, to begin with, my story isinteresting. And, next, I am a mystery—more so than a tree or asunset or even a flash of lightning. But, sadly, I am taken forgranted by those who use me, as if I were a mere incident andwithout background. This supercilious attitude relegates me to thelevel of the commonplace. This is a species of the grievous errorin which mankind cannot too long persist without peril. For, thewise G. K. Chesterton observed, "We are perishing for want ofwonder, not for want of wonders."
I, Pencil, simplethough I appear to be, merit your wonder and awe, a claim I shallattempt to prove. In fact, if you can understand me—no, that's toomuch to ask of anyone—if you can become aware of the miraculousnesswhich I symbolize, you can help save the freedom mankind is sounhappily losing. I have a profound lesson to teach. And I canteach this lesson better than can an automobile or an airplane or amechanical dishwasher because—well, because I am seemingly sosimple.
Simple? Yet, not asingle person on the face of this earth knows how to make me. Thissounds fantastic, doesn't it? Especially when it is realized thatthere are about one and one-half billion of my kind produced in theU.S.A. each year.
Pick me up and lookme over. What do you see? Not much meets the eye—there's some wood,lacquer, the printed labeling, graphite lead, a bit of metal, andan eraser.
InnumerableAntecedents
Just as you cannottrace your family tree back very far, so is it impossible for me toname and explain all my antecedents. But I would like to suggestenough of them to impress upon you the richness and complexity ofmy background.
My family tree beginswith what in fact is a tree, a cedar of straight grain that growsin Northern California and Oregon. Now contemplate all the saws andtrucks and rope and the countless other gear used in harvesting andcarting the cedar logs to the railroad siding. Think of all thepersons and the numberless skills that went into their fabrication:the mining of ore, the making of steel and its refinement intosaws, axes, motors; the growing of hemp and bringing it through allthe stages to heavy and strong rope; the logging camps with theirbeds and mess halls, the cookery and the raising of all the foods.Why, untold thousands of persons had a hand in every cup of coffeethe loggers drink!
The logs are shippedto a mill in San Leandro, California. Can you imagine theindividuals who make flat cars and rails and railroad engines andwho construct and install the communication systems incidentalthereto? These legions are among myantecedents.
Consider the millworkin San Leandro. The cedar logs are cut into small, pencil-lengthslats less than one-fourth of an inch in thickness. These are kilndried and then tinted for the same reason women put rouge on theirfaces. People prefer that I look pretty, not a pallid white. Theslats are waxed and kiln dried again. How many skills went into themaking of the tint and the kilns, into supplying the heat, thelight and power, the belts, motors, and all the other things a millrequires? Sweepers in the mill among my ancestors? Yes, andincluded are the men who poured the concrete for the dam of aPacific Gas & Electric Company hydroplant whichsupplies the mill's power!
Don't overlook theancestors present and distant who have a hand in transporting sixtycarloads of slats across the nation.
Once in the pencilfactory—$4,000,000 in machinery and building, all capitalaccumulated by thrifty and saving parents of mine—each slat isgiven eight grooves by a complex machine, after which anothermachine lays leads in every other slat, applies glue, and placesanother slat atop—a lead sandwich, so to speak. Seven brothers andI are mechanically carved from this "wood-clinched"sandwich.
My "lead" itself—itcontains no lead at all—is complex. The graphite is mined inCeylon. Consider these miners and those who make their many toolsand the makers of the paper sacks in which the graphite is shippedand those who make the string that ties the sacks and those who putthem aboard ships and those who make the ships. Even the lighthousekeepers along the way assisted in my birth—and the harborpilots.
The graphite is mixedwith clay from Mississippi in which ammonium hydroxide is used inthe refining process. Then wetting agents are added such assulfonated tallow—animal fats chemically reacted with sulfuricacid. After passing through numerous machines, the mixture finallyappears as endless extrusions—as from a sausage grinder-cut tosize, dried, and baked for several hours at 1,850 degreesFahrenheit. To increase their strength and smoothness the leads arethen treated with a hot mixture which includes candelilla wax fromMexico, paraffin wax, and hydrogenated naturalfats.
My cedar receives sixcoats of lacquer. Do you know all the ingredients of lacquer? Whowould think that the growers of castor beans and the refiners ofcastor oil are a part of it? They are. Why, even the processes bywhich the lacquer is made a beautiful yellow involve the skills ofmore persons than one can enumerate!
Observe the labeling.That's a film formed by applying heat to carbon black mixed withresins. How do you make resins and what, pray, is carbonblack?
My bit of metal—theferrule—is brass. Think of all the persons who mine zinc and copperand those who have the skills to make shiny sheet brass from theseproducts of nature. Those black rings on my ferrule are blacknickel. What is black nickel and how is it applied? The completestory of why the center of my ferrule has no black nickel on itwould take pages to explain.
Then there's mycrowning glory, inelegantly referred to in the trade as "the plug,"the part man uses to erase the errors he makes with me. Aningredient called "factice" is what does the erasing. It is arubber-like product made by reacting rape-seed oil from the DutchEast Indies with sulfur chloride. Rubber, contrary to the commonnotion, is only for binding purposes. Then, too, there are numerousvulcanizing and accelerating agents. The pumice comes from Italy;and the pigment which gives "the plug" its color is cadmiumsulfide.
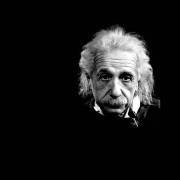