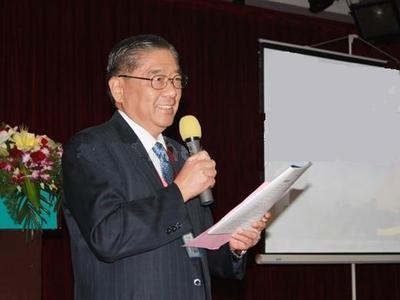
20世纪后半期,高分子材料在用量上已超过金属与陶瓷材料,成为人们衣、食、住、行等生活中不可或缺和替代的材料。高分子材料覆盖了从医用到食品,从包装、家居到交通工具等各个领域,但其也带来了环保及回收方面的问题。
进入21世纪,面对全球性的环境、能源、医药等诸多挑战,高分子材料将更加凸显其轻质、多功能等特点,在能源、水资源、石油资源的可持续发展及环境保护等方面提供更多的解决方案,但这同时也对高分子科研及发展提出了新的要求和挑战。
记者:聚烯烃材料的研究热点与未来方向是什么?我国聚烯烃技术基础研究和工程化进展情况如何?
韩志超:聚烯烃的合金化、高性能化及多样化是主要的发展方向。虽然天然及可降解高分子材料研究在近十几年来取得了许多进展,但在市场应用上仍然仅限于一些简单的包装及一次性用品上,其原因既有价格问题,也有消费者的习惯问题。在结构高分子材料方向,聚烯烃的合金化、高性能化及多样化成为我们在汽车、轨道交通及家电、居家建筑材料等家用材料领域的主要选择。
聚烯烃的合金化可以获得聚烯烃釜内合金材料。聚烯烃釜内合金材料的设计与合成,涵盖了催化化学、聚合工程学、高分子物理学等一系列学科内容,也代表了一个国家石化技术的发展水平。目前国际各大石化公司和科研机构都以聚烯烃釜内合金催化剂和聚合工艺的研发作为占据高性能石化产品合成领域高点的重要策略,其科研投入巨大,新技术、新产品层出不穷。然而,我国聚烯烃釜内合金的基础和工程化研究均处于起步阶段,要想成功突破国外专利技术封锁、获得自主创新的聚烯烃釜内合金技术,面临极大挑战。
记者:高分子材料在太阳能高效利用方面有什么独特优势?
韩志超:聚合物太阳能电池的发展将为高分子材料提供新的应用空间。太阳能作为大有前途的清洁能源,其有效开发利用的关键在于电池材料。目前太阳能电池应用技术分为两大类,即晶体硅片和薄膜。尽管眼下薄膜太阳能电池的市场份额不到10%,但这种新的薄膜半导体有望很快找到它的特殊应用市场。高分子材料因为具有质量轻、柔韧易加工、制作工艺简单、成本低、可大面积制备等突出优点,在太阳能电池材料中极具竞争力。
自从在本体异质结器件中发现光伏效应后,聚合物太阳能电池得到了较大的发展。这种类型的太阳能电池结构由Heeger小组在1995年提出,之后的10多年里,给体/受体本体异质结器件已成为聚合物太阳能电池研究的主流。文献报道的最高能量转换效率到2009年时已达到6.77%。但是相对于无机半导体太阳能电池而言,效率还很低,而且性能不够稳定。
为了提高其能量转换效率,众多的科学家从材料合成、器件结构、器件制备等角度入手,对聚合物太阳能电池相关材料和器件进行了深入研究,目前研究热点是聚合物光伏材料的设计与合成,可编程系统芯片(PSC)器件结构的改进,制备过程和界面修饰及其他因素对界面、光敏活性层形态和器件性能的影响,PSC光电转换机理等,希望最终获得高能量转化效率的PSC器件。而作为聚合物太阳能电池的主要组成部分,光敏活性层材料的改进、尤其是共轭聚合物光伏材料的结构和性能改进是PSC研究的一个重点。
近年来,大量用于光敏活性层的共轭聚合物材料被设计、合成出来,并被应用到光伏器件中。目前国际上聚合物太阳能电池领域的研究十分活跃,新一代光伏技术开发在美国国防先进研究项目局(DARPA(DefenseAdvancedResearchProjectsAgency)的简称,的支持下得到了很大发展,结合MichaelGraetzel博士开发的“燃料激活”电池和AlanHeeger博士开发的聚合物电池两种技术的新一代光伏电池,被认为是继晶体硅和薄膜光伏电池后的第三代光伏电池,有望开发出转换效率达到或者超过20%的低成本薄膜电池。国内在聚合物太阳能电池方面的研究起步较晚,但是目前许多科研机构在从事这方面的研究。
记者:聚合物太阳能电池发展还需要攻克哪些技术瓶颈?
韩志超:聚合物太阳能电池能量转换效率与硅基太阳能电池相比还比较低,这也是聚合物太阳能电池市场化的瓶颈。这迫切需要我们合成效率较高的光伏材料,并完善光伏材料和太阳能电池的光电转换机制和相关理论。只有将光电转换效率提高,增加稳定性,才可能大规模应用。
目前太阳能电池的总体价格主要受两个因素影响:材料成本及加工过程成本。相比把材料加工成几百纳米厚的器件的过程成本而言,材料本身的成本并不算太高。有机半导体可以通过印刷技术将溶液加工成大面积的薄膜。这些技术本身也比较便宜,并且比较容易实现。
从影响太阳能电池效率的因素考虑,目前太阳能电池效率不高主要是由于使用的共轭聚合物存在太阳能光吸收效率低和电荷载流子传输效率低的问题。可通过分析和优化聚合物溶液结构及分散程度,得到均匀的薄膜结构。通过分析器件的微相结构,可以发现在给体-受体复合层中形成带微相分离的连续的网络互穿结构,连续的网络结构提供了载流子分离并在相应电极收集的途径,因此可通过给体和受体的相形态来促进高效的聚合物太阳能电池和高效的光电探测器的设计和制作工艺。
记者:医用高分子材料带动了功能性高分子产业链的深化发展,这主要表现在哪些方面?
韩志超:生物医用材料是人工器官和医疗器械的基础,迄今已有几千年的发展历史,而生物医用高分子作为生物医用材料中发展最早、应用最广泛、用量最大的材料,鉴于其具有原料来源广泛、可以通过分子设计改变结构、生物活性高、材料性能多样等优点,是目前发展最为迅速的领域,已经成为现代医疗材料中的主要部分。
对医用高分子材料的深入研究不但对探索人类生命奥秘具有重大意义,也可以带动功能性高分子产业链的深化发展。现代医学的进步已经越来越依赖于生物材料器械的发展,医用高分子材料的应用更加广泛,需求量也随之越来越大。主要体现在以下几个方面:
一是用于人造器官,如心脏瓣膜、人工肾、人造皮肤、疝气补片等。我国在此领域起步较晚,仅在初级的组织工程支架材料方面投入较大,浙江大学、清华大学、中科院成都有机所等均有课题小组进行相关研究,他们通过多层复合、共聚等手段将聚乳酸、聚乙内酯、海藻酸钠等生物相容性材料制备成支架材料,但仅考察了其潜在应用价值,距离实际使用仍有漫长的道路要走,尤其是完整的人工器官研发还完全处于仿制阶段,缺乏自主创新的产品。
二是用于医疗器械,如手术缝线、导尿管、检查器械、植入器械等。目前的手术缝线多数来自于丝素蛋白,其纤维不但具有优良的生物相容性,也具有良好的力学强度;而可吸收缝线则主要采用聚乳酸,我国目前已经可以完全自主生产这几种缝线,同时在国内拥有较大的市场份额。植入防粘连材料、外用抗菌伤口包覆材料我国也有多个研究小组投入研究,开发的聚乳酸防粘连薄膜、银离子纳米抗菌敷料等均已获得中国国家食品药品监督管理局许可进入市场。
三是用于药物助剂,如药物控释载体、靶向材料等。我国在这方面的研发位于世界前列,中科院长春应化所研究人员利用静电纺丝技术制备的聚乳酸超细纤维可以包埋油溶、水溶药物,同时实现控制释放。中科院化学所研究人员通过调节嵌段聚合物的组成及比例,有效控制了材料的降解时间;通过修饰聚合物功能基团制备的微球作为药物载体,能够实现随温度、pH值变化的选择性释放;通过将放射性核素与纤维膜材料联合,实现了术后防粘连和灭杀残余肿瘤细胞的双重功效。
记者:我国医用高分子材料技术处于什么水平?未来的重点攻关方向有哪些?
韩志超:从科研人员在国际期刊发表的论文档次及引用频率来看,我国在某些生物医用材料领域已达到国际前沿水平。然而由于医用高分子材料的研发周期一般较长,需要经过体外实验、动物实验、临床实验等不同阶段的实验,材料市场化需要经过国家药品和医疗器械检验部门的批准,且报批程序复杂、费用高,所以生物材料的研发成本高、风险大,我国医用高分子材料的生产水平实际上依然十分低下,处于产量低、品种少、规格不全、且质量差、水平低的境地。
随着科学的发展,新的材料不断推出,不但要认真研究新材料的生产安全性和使用范围,更重要的是从借用和改性逐渐深入分子设计和结构设计层次开发新材料,同时也要结合实际临床需要,克服医用材料研发周期长,见效慢等缺点,真正做到产、学、研三者结合,推动我国医用高分子产业的发展,为中国的化学品研发开拓新方向。
记者:为解决水资源危机,水处理技术所需的高分子膜材料的未来发展方向是什么?
韩志超:高分子材料在水资源领域的一个重要应用是膜法水处理技术。膜法水处理技术是净化污水,再生水资源的一个有效途径,具有分离效率高、能耗低、占地面积小、过程简单、操作方便、无污染等特点。自上世纪60年代开始大规模工业化应用以来,膜技术发展十分迅速,其品种日益丰富,包括反渗透膜、纳滤膜、超滤膜和微滤膜等主要品种。微滤膜孔径0.1微米~1微米,能截留悬浮物、细菌、部分病毒及大尺度胶体;超滤能截留0.005微米~0.1微米的颗粒和杂质,能有效阻挡住胶体、蛋白质、微生物和大分子有机物;纳滤膜孔径1纳米~10纳米,能去除细菌、病毒及二价离子;反渗透是最精密的膜法液体分离技术,它能阻挡所有溶解性盐及分子量大于100的有机物,而允许水分子透过,但同时需要能量的消耗来达到反渗透的效果。
我国膜分离技术从上世纪60年代反渗透膜的研究开发,到70年代各种膜及相应膜组件的开发研究,再到80年代膜分离技术跨入实际应用,取得了巨大进展。目前全国膜科学与技术的研究与开发单位已有上百个,中科院许多研究所也相继开展了膜技术方面的研究。大连化学物理所、上海应用物理所等单位分别与公司合作成立了膜技术研究中心,将产研结合,不断研发具有自主知识产权的膜技术,开发超滤、反渗透等膜组件并推向大规模工业化应用。目前工业上应用最广泛的分离膜大多是复合膜结构,基本选用以浸沉凝胶相转化制备的聚砜膜作为支撑层,个别选用拉伸法制备的聚丙烯薄膜。中科院化学所在复合膜的结构设计及制备方面也开展了相关研究,利用电纺纳米纤维膜具有超大比表面积和孔隙率的特点,以其作为复合膜支撑层设计了不对称梯度膜结构,初步结果表明该结构的设计有利于提高膜的过滤效率,但此方法尚处于实验室阶段。
我国研发的尖端高分子复合材料应用于航空事业已有20多年的历史,目前此种材料在民用客机中的用量达10%~20%。
宇航员穿的太空服,既要耐高温又要防辐射,这离不开高强度高模量的高分子材料。