塑料成型模具课程总复习知识总结
1、塑料成型模具的分类:(1)压塑成型模具;(⒉)注射成型模具;(⒊)传递成型模具(压铸成型模具);(⒋)挤塑成型模具;(⒌)中空制品吹塑成型模具;(⒍) 热(真空或压缩空气)成型模具;
2、注塑模具设计的主要问题:(⒈) 塑料的充模顺序;(⒉)塑件冷却过程中的收缩与补缩;(塑料加工工艺)(⒊)塑件脱模和横向抽芯的问题;(⒋) 决定塑件的分型面及型腔的镶拼结构。(模具结构 )
3、注射模具分类:(⒈按安装方式:移动式、固定式。(⒉按所用注射机类型:卧式或立式注射机用模具、角式注射机用模具。(⒊按模具型腔数目:单型腔和多型腔注射模具。(⒋按注塑模具的总体结构特征:⑴单分型面(两板式)注塑模具: 由动模(型芯)与定模(型腔)组成。
⑵双分型面(三板式)注塑模具: 指浇注系统凝料和制品由不同的分型面取出。
⑶带活动镶件的注塑模具:利用手工或简单工具将成型侧凹(凸)的镶件或哈夫在模外取出的模具。该模具应注意镶件在模具内的可靠定位。
⑷横向分型抽芯注塑模具:利用开模、液压或气压等动力使成型塑件侧凹(凸)的型芯或哈夫与塑件分离的模具。
⑸ 自动卸螺纹注塑模具:在模具上设置可转动的螺纹型芯或型环 使带螺纹的塑件可自动脱模。
⑹多层注塑模具:由数个两(三)板式模具或无流道模具重叠而构成,它适合生产小而薄的塑件。
⑺无流道注塑模具:利用加热或绝热的方法使注塑机喷嘴到型腔浇口之间的塑料呈熔融状态,在成型过程中只需取出塑件而没有浇注系统凝料。
4、注塑机有关工艺参数的校核:
(⒈ 型腔数量的决定 :
影响型腔数的主要因素:注塑机的规格、塑件的质量、塑件的成 本及交货期。
(⒉ 注射压力的校核:
注射压力的影响因素:注塑机的类型、喷嘴类型、塑料流动 性、浇注系统及型腔中的流动阻力。
(⒊ 锁模力的校核:
(⒋ 模具与注射机装模部位相关尺寸的校核:⑴ 喷嘴尺寸;⑵ 定位环尺寸;⑶模具外形尺寸;⑷ 最大模具厚度;⑸ 最小模具厚度;⑹模板上的安装螺孔尺寸。
(⒌ 开模行程和塑件推出距离的校核:
5、注射机的分类:按驱动方式分:液压、机械。按工作方式分:全自动、半自动、手动。按结构形式分:立式、卧式、直角式。
6、注射机的特点:
立式:占地小、安装嵌件方便,塑件不能自动坠落、加料困难。
卧式:塑件能自动坠落,安装模具较麻烦,动模嵌件应卡紧。
直角式:主流道设在分型面上,适于生产单件板状的在制件中心部位不允许留下浇口痕迹的制件。
7、多型腔模具浇注系统的组成:
主流道:指紧接注塑机喷嘴到分流道为止的部分,物料在其中不改变流动方向。
分流道:将从主流道来的塑料沿分型面引入各个型腔的部分。
浇口:从流道末端将塑料引入型腔的狭窄部分,具有调节料流速度、控制补料时间的作用。
冷料井:设在主流道末端,去除料流中的前端冷料。
8、主流道衬套:避免模板间的拼缝处溢料。
定位环:安装模具时起定位作用。
9、冷料井类型和结构:
⑴ 冷料井底部带推料杆的冷料井:
根部固定在推出板上,Z型取产品时需 侧向移动,其余两种需用弹性较好的塑料。
⑵ 带球形头拉料杆的冷料井:
用于以推件板脱模或三板式模具中。
⑶ 无拉料杆冷料井:
利用分流道上的侧凹、动模边的哈夫将主流道脱出或主流道衬套装弹簧。
10、浇口断面形状:
圆形:点浇口、潜伏式浇口、主流道型浇口。
矩形:侧浇口、轮辐式浇口。
狭缝形:扇形浇口、薄膜式浇口。
11、小型薄壁制品常采用小尺寸浇口。
12、小浇口的优点: ⑴增加流速,使充模容易; ⑵提高熔体温度制品表面质量;
⑶提高制品质量; ⑷ 缩短成型周期;⑸ 容易平衡各型腔的进料速度;⑹ 便于制件修整。
13、 大浇口的适用范围: ⑴大型、厚壁或特厚制品; ⑵ 制品所用塑料为热敏性塑料; ⑶熔体流动行为接近牛顿型的高粘度塑料。
14、常见的浇口形式:
⑴边缘浇口(标准浇口、侧浇口);
⑵扇形浇口:适用对象—— 宽度较大的薄片状制品。
⑶平缝浇口(薄片浇口、膜状浇口):
特点:横向分配更均匀,降低内应力,但浇口去除麻烦。
⑷盘形浇口和圆环型浇口:适用对象:圆筒形或中间带孔的制品。
特点:进料均匀,无熔接缝,气体易排出;去除较麻烦。
⑸轮辐浇口:适用对象:圆筒形或中间带孔的制品。
特点:有熔接痕,强度降低,常用奇数个,浇口去除较易。
⑹爪浇口: ①适用对象:制件内孔较小和同心度要求高的制件。
② 特点:分流道与浇口不在一个平面。
(7)点浇口:特点:开模后制件与浇注系统分离。
适用对象:三板式模具。
⑻潜伏式浇口(隧道式浇口):适用对象:两板式模具。
特点:进浇点较隐蔽;顶出后制件与浇注系统分离;顶出时需较强的冲击力,不适用于强韧性塑料。
⑼护耳浇口(分接式浇口):特点:克服小浇口的喷射及内应力。
⑽直浇口(中心浇口、主流道型浇口):
①适用对象:大型制件或高粘度塑料。
15、浇口位置设计:
⑴浇口位置与制品翘曲变形的关系
原因:取向分子使制品产生内应力和收缩 不均匀。
改进方法:A、将中心浇口改为多点浇口;B、改变浇口位置; C、采用一端两点进浇。
⑵浇口位置与性能间关系:子取向制品各向性能有异。
①利用分子取向,提高使用性能;② 避免分子取向对性能的降低。
⑶注塑成型时的喷射现象与浇口位置和尺寸的关系
产生的条件:小浇口对大型腔。
避免方法:A、加大浇口断面尺寸,使流速降低; B、采用冲击型浇口。
⑷浇口位置应有利于充模流动、排气和补料
①当制件厚度相差较大时,应在避免喷射的前提下,把浇口开在接近截面最厚处,有利充模、补料。②塑料熔体首先充满阻力最小的空间,最薄处常是最后充满。
⑸减少熔接痕,增加熔接牢度
⑹浇口位置应防止料流将型芯或嵌件挤歪变形改变浇口位置或尺寸。
16、绝热流道注塑模具:
利用加热或绝热的方法,使从注射机喷嘴起到型腔入口为止这一段流道中的塑料一直保持熔融状态,从而在开模时只需取出产 品,而不必取出浇注系统凝料。
(1)优点: ⑴ 降低成本; ⑵ 缩短成型周期;⑶更有效地利用注塑机; ⑷ 减小流动阻力、提高产品质量。
(2 缺点:⑴开机时需要较长时间才能达到稳定操作; ⑵ 需要操作技能较高的专业人员; ⑶ 模具结构复杂,成本高,需增添辅助设备;⑷易产生热降解。
17、绝热流道注塑模具特点:流道相当粗大,以致于中心部位的塑料在连续注塑时来不及凝固而保持熔融状态,从而让塑料熔体通过它顺利进入型腔。
18、绝热流道注塑模具分类:⑴ 井坑式喷嘴;⑵ 多型腔的绝热流道模具;
19、热流道注塑模具
(⒈定义:在流道的外围或中心设有加热棒或加热圈,从注射机喷嘴到浇口的整个流道都处于高温状态,使流道中的塑料维持熔融。分流道带有加热器的模具是其主要形式。
(⒉ 特点:⑴ 不需取出流道凝料;⑵适用的塑料多;⑶ 分流道压力传递好,成型温度、压力低。
(⒊ 类型:(1)单型腔延伸式喷嘴模具;⑵ 多型腔热分流道模具;
20、 分型面:分开模具取出塑件的面,称为分型面。
21、 确定分型面应考虑的问题:
⑴ 塑件在型腔中放置方位的确定:应设法避免与开模运动方向垂直或倾斜的侧向分型和侧向抽芯。
⑵ 分型面的形状的决定: 与开模方向垂直的平面、斜面、折面、曲面。
⑶分型面位置的选择: 开设在制件断面轮廓最大的地方。 同时考虑:
① 分型面避免放在制件外表面或圆弧转角处;
② 从制件的推出考虑分型面要尽可能使制件留在动模边;
③ 从保证制件相关部位的同心度出发;
④ 机动侧向分型时,侧向抽拔距应较小,且优先考虑将其放在动模边;
⑤ 当分型面为主要排气面时,料流末端应在分型面上排气。
22、凹模(阴模)的结构设计:
(⒈)整体式凹模: 牢固、不易变形 。
(⒉) 整体嵌入式凹模: 适宜合模时对中性要求高和多型腔模中。
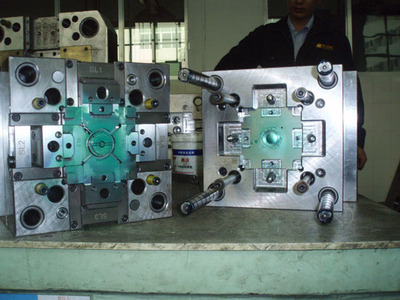
(⒊)局部镶嵌式凹模: 为了便于加工或某一部分容易损坏,需经常更换。
(⒋)底部大面积镶嵌组合式凹模:为了机械加工、研磨、抛光、热处理的方便而采用的方法。
(5.)四壁拼合的组合式凹模:用于大型复杂凹模。
23、型芯和成型杆的结构设计:
(⒈) 整体式:用于形状简单的型芯。
(⒉)组合式:适宜节省贵重材料、减少加工量的场合,注意成型部分为非回转体固定部分为回转体型芯的定位及热处理时的开裂变形。
24、螺纹型芯或螺纹型环的结构设计
(⒈) 分类:模内自动卸除、模外手动卸除。
25、排气方式及排气槽的设计
(⒈ 重要性:型腔内气体不能顺利排出,将在制品上形成气孔、银丝、灰雾、接缝、表面轮廓不清,型腔不能完全充满等弊病;也可引起溢料、灼伤制件;同时降低充模速度。
(⒉ 方式: (1)利用分型面或配合间隙排气;(2)开设专用排气槽;(3)用多孔烧结金属块排气;(4)负压及真空排气。
25、合模导向和 定位机构:
(⒈目地:保证模具闭合时型腔形状尺寸的准确性。
(⒉作用:⑴定位;⑵导向;⑶承受一定侧压力。
(⒊ 形式:导柱导向;锥面定位。
26、导柱位置的布置:
(1)布置原则:保证定模按一个方向合模。
(2)方式:径向尺寸相同的不对称布置,径向尺寸不同的对称布置,模具侧面打标记。
27、锥面定位机构设计:
(⒈使用对象:大型、深腔、精度要求高的模具。
(⒉特点:配合间隙为零,提高定位精度。
(⒊方法:安装锥形定位件(至少两副)、在型腔四周设锥型定位面。
28、脱模机构的要求: ⑴ 结构优化、运行可靠; ⑵不影响塑件外观,不造成塑件变形破坏; ⑶ 让塑件留在动模。
29、脱模机构的分类
⑴按动力源分类: 人力操作、机械推出、液压推出、气动推出。
⑵按机构结构特点分类:简单脱模机构、双脱模机构、顺序脱模机构、二级脱模机构、浇注系统脱模机构、带螺 纹塑件脱模机构。
30、简单脱模机构:
㈠ 推杆脱模机构
⒈特点:加工简单、安装方便、维修容易、使 用寿命长、脱模效果好。
⒉组成:推杆、复位杆、拉料杆、推板、推杆 固定板等。
⒊ 推杆脱模设计要点:
⑴推出杆位置的确定、推杆数量和断面形状的设计
位置:脱模阻力最大处,避免塑件最薄处。
形状:圆形、异形。
数量:以保证塑件质量为前提。
㈡ 推管脱模机构
⒈适用范围:环形、筒形或中间带孔的塑件。
⒉特点:塑件周边受力,推出时平衡可靠,制品不易变形,不会留下明显的接触痕迹。
⒊形式: ⑴主型芯固定在动模底板: 适用于型芯径向尺寸较大者。
4、主型芯固定在动模型芯固定板:适用于推出距离较小者。
(三)推件板脱模机构:
⒈ 适用范围:薄壁容器、筒形制品、大型罩壳及多孔 塑件。
⒉ 特点:推出力大而均匀,运动平稳,不留推出痕迹。
注意:避免推板与塑件的摩擦,软质塑料脱时易形成真空。
㈣ 活动镶件或凹模推出的脱模机构
特点:模具结构简单,推出时塑件受力均匀,劳动强度大,适于小批量生产。
㈤ 气压脱模机构:
特点:塑件受力均匀且简化模具结构。
㈥ 多种脱模方式联合脱模机构
特点:受力部位分散、受力面积增大,可获 高精度制件。
31、定模脱模机构:
适用对象:因塑件的特殊形状而必须留在定模塑件外观质量要求高。
32、双脱模机构:
⒈适用范围:塑件对动模和定模的附着力和包紧力相差不多。
⒉分类:⑴ 压缩空气顺序脱模机构;⑵弹簧顺序脱模机构 ;⑶拉钩顺序脱模机构;(4)弹簧锁紧式顺序脱模机构。
33、二级脱模机构:
⒈适用范围:经一次脱模尚且不能自动坠落者薄壁深腔制件或经一次脱模易使塑件变形或破裂者。
⒉ 类型: ⑴机械气动式;⑵ 弹簧式;⑶凸轮推杆式;(4) 拉钩推杆式。⑸楔块滑块式;⑹ 杠杆增速式;⑺拉钩式;⑻套筒球槽式;⑼采用两级抬杠标准件;⑽其它形式。
34、浇注系统凝料脱出
⒈潜伏式浇口浇注系统的脱出
⒉三板式模具浇注系统凝料自动脱出
⑴ 浇注系统凝料自动脱出应完成的动作:
主流道凝料的脱出,浇口的拉断与脱出。
(2) 仅用限位拉杆拉开分型面
⑶ 顺序分型机构:① 利用斜孔拉断浇口脱出浇注系统凝料; ②利用拉料杆和凝料推板脱出浇注系统凝料; ③仅用凝料推板脱出浇注系统凝料
35、螺纹塑件脱模机构:
⒈ 非旋转脱出方式:⑴ 强制脱出; ⑵分瓣式可张缩型芯;(3)用内侧抽芯成型非连续的分断式螺纹。
⒉ 旋转式脱出方式
⑴结构分类及止转措施:①螺纹脱出方式:模外旋出; 模内自动旋出。
②止转措施:塑件和模具均应设止转花纹。
⑵螺纹型芯或型环一面旋转一面退
⑶ 螺纹型芯或型环只旋转不轴向退回
36、侧向分型与抽芯方式 :
⑴ 手动侧向分型抽芯:
特点:模具结构简单,劳动强度大,效率低。
⑵ 机械侧向分型抽芯机构
特点:经济合理,动作可靠,易实现自动化。
⑶ 液压或气动分型抽芯
特点:抽拨距离长,抽拨力大。
37、手动分型抽芯机构
⒈ 模外手动分型抽芯:特点:把侧型芯做成镶块,模具结构简单。
注意:镶块在模内要可靠定位。
⒉ 模内手动分型抽芯: ⑴丝杠手动抽芯; ⑵ 手动斜槽分型抽芯; ⑶手动齿轮齿条抽芯;(4) 杠杆抽芯;
38、机动式分型抽芯机构
㈠弹簧分型抽芯机构:—— 适用对象:抽拔距小、抽拔力不大的场合。
㈡ 斜销(斜导柱)分型抽芯机构
(1) 特点:借助开模力或推出力完成侧向抽芯,结构简单,制造方便,动作可靠。
⑵ 滑块:——A、作用:实施侧向抽芯。B、形式:整体式、组合式。
注意:滑块的底面和两侧为滑动面,应有足够的 硬度(稍低于导滑槽)和较低的粗糙度。
⑶导滑槽:A、作用:在抽芯过程中,保证滑块运动平稳,无上下串动与卡紧现象。B、形式:整体式和组合式。C、配合:动配合为H8/f7,其余为0.5~1mm间隙。 导滑槽与滑块间的配合
⑷滑块定位装置
A、作用:保证闭模时斜销顺利进入滑块斜孔。
B、 形式:与安装的方位有关。
⑸锁紧楔:A、作用:确保成型时滑块位置的准确。
B、形式:整体式与组合式(其区别在于锁紧力的大小不同)。
39、斜销分型抽芯机构的五种安装组合形式:
⑴斜销在定模、滑块在动模
注意:当顶杆与侧型芯在垂直与水平面的面上 的投影发生重叠时,合模时有可能发生干涉。
⑵斜销在动模、滑块在定模的结构;(3)斜销和滑块同在定模的结构;(4)斜销与滑块同在动模的结构;(5)斜销在动模固定板、滑块在动模的结构
㈢弯销分型抽芯机构:原理:同斜销抽芯机构。
40、冷却系统设计原则: ⑴ 冷却水通道在动定模均应设置; ⑵ 冷却水孔尽量大、尽量多; ⑶水孔与相邻型腔表面距离相等; ⑷ 采用并流流向,加强浇口处的冷却;(5) 降低入水与出水温度差。
更多资源,请大家访问我的新浪博客http://blog.sina.com.cn/kangver。欢迎光临!!