目录
(1)产品名称,物化性质,技术标准及作用;
(2)原料名称及质量标准;
(3)生产基本原理及反应式;
(4) 生产工艺流程叙述;
(5) 岗位操作法及控制:a.岗位操作范围;b.开车前准备;c.开停车操作;d.各岗位控制要点;
(6)某些不正常现象及消除方法;
(7) 安全生产要点;
(8)生产过程中的三废排放和处理;
(一)产品名称,物化性质,技术标准及作用
(1)产品名称:三氯氢硅SiHCl3
(2) 物理性质:常温下纯净的三氯氢硅是无色、透明、挥发性、可燃液体,有较四氯化硅更强的刺鼻气味。分子式:SiHCl3,分子量:135.4 ,液体密度:1.318kg/l(常温状态),气体密度:6.5g/l(标准状态),1atm下沸点:31.5℃ ,1atm下熔点:-128℃
(3)化学性质:易水解、潮解、在空气中强烈发烟,生成HCl和H2,HCl遇水立即转化为盐酸,盐酸具有很强的腐蚀性;H2易燃易爆。
更易挥发、更易气化、更沸点低;
易着火、易爆炸、着火点28℃、着火温度220℃,燃烧时产生氯化氢和氢气;
其蒸汽具有弱毒性,与无水醋酸和二氯乙烯毒性程度相同。
(二)原料名称及质量标准
1.氯化氢(Hcl):氯化氢含量92%∽94%,氯气不过量;
2.硅粉:冶晶级多晶硅(95%∽99%),块密度约2.0×103kg/m3,硬度为7,其颗粒大小为80∽120目。
(三)生产基本原理及反应式
1. 基本原理:
80∽120目的硅粉与干燥的92%∽94%的氯化氢在催化剂(催化剂用量si:cucl2=100(0.4∽1))作用下,在280∽320℃、小于0.05Mpa条件下生成三氯氢硅。合成SiHCl3必须先将硅粉预热到250℃以上。不过,该反应是放热反应,只要启动后就不再需要补充热能,而是带走热量。
2. 主要反应
Si+3HCl→SiHCl3+H2+Q
当温度不再上述制控制范围内,怎发生下列副反应:
A.温度大于350℃时:Si + 4HCl → SiCl4 + 2H2 +Q
B.温度小于280℃时:Si + 4HCl → SiH2Cl2 + 2H2 +Q
C.硅粉与HCl反应过程中,硅粉中的少量杂质Ca、Fe、Al、Zn、Ti、P、B等主要生成CaCl2、FeCl3、AlCl3、ZnCl2、TiCl4、PCl3、BCl3化合物,这些物质大部分以固相在除尘时分离出去,仅少量随SiHCl3的混合气(液滴)进入冷凝器被溶解在料液中,这部分ppm级含量的杂质需通过精馏分离
(四)生产工艺流程叙述
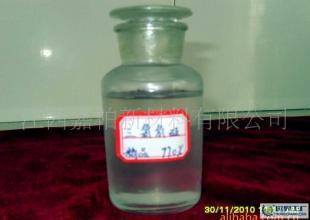
三氯氢硅合成工艺简图
硅粉加料系统是由三个串联的料仓〔一个干燥仓 一个硅粉料仓一个计量仓组成〕和一台硅粉自动加料机组成。根据合成炉设计的参数,连续向合成炉加入硅粉。干燥的氯化氢气体经缓冲罐稳压压后,由合成塔下部经分布管均匀进入合成塔中。
SiHCl3合成炉由带水冷夹套的反应段,炉的上方带有扩大部分,反应段安装有多个测温口,炉的上部与下部均安装有测压仪表。合成炉加入干燥的硅粉后,将合成炉加热到250-300℃,通入HCL气体,在炉内进 行化学反应,生成SiHCl3、SiCl4、SiH2Cl2,反应的混合气送到旋风干法除尘器,经除尘器出去其中的硅粉及催化剂颗粒。
除尘后的气体通入冷凝器中,将气体中的三氯氢硅冷凝下来,经计量器计量后通入三氯氢硅储存罐中储存。
其余气体进入尾气吸收塔中去除。
(五)岗位操作法及控制
a.岗位操作范围:温度、压力、流量。
b.合成炉开车前准备:
1.检查整个系统管道、阀门、设备、仪表、电路和压力表等是否正常好用。
2.用N2(1.5*105∽2*105Pa)试压,用氨水(或用肥皂水)检查系统所有的连接处,确保无漏气和堵塞现象。
3.沸腾炉升温(用电加热器)至200℃左右烘干,同时自炉底通N2,流经全系统至水淋洗中排出,使系统处于干燥和正压状态。
c. 开车操作:
1.向合成炉中投入竟是当温度干燥好的硅粉。
2.沸腾炉继续升温,使中、下部温度维持在380∽400℃之间,除尘器保持在100℃左右。
3.水冷却器中通入自来水,冷凝器中通入-60∽-40℃的盐水,随后向合成炉内通入HCl气体。
4.反应后停止送点,靠反应放出的热量维持炉内的温度。在炉内换热器中通入热水以带走多余热量,使炉内温度控制在280∽320℃范围内。
正常情况下,操作人员可根据各个测量点的压力和压差、炉内各点温度、产量的变化来判断炉内反应情况。
定时加入硅粉以维持炉内有足够的硅粉料层,保证沸腾床的形成。每隔固定时间用压力为(2.5*105∽3*105Pa)氮气吹渣一次,残渣吹至除渣罐水封口排出。
d. 停炉操作:
1.停止加入硅粉。当炉内剩余硅粉不在反应后,温度自行下降,同时不再有看、冷凝产物流出。炉内降温可以采用自然降温和通入自来水降温两种方法。
2.关闭器和HCl控制阀门,炉内维持正压(2.5*105∽3*105Pa)或者通入N2以赶出炉内气体。吹渣赶气,关闭尾气。
3.停止系统送电。
4.停止输送冷却水和冷冻盐水。
e. 各岗位控制要点
1.反应温度
由前面的分析可知,硅粉与HCl合成SiHCl3的反应对温度的选择性很高,反应温度对生产影响较大。温度过低则反应缓慢,达不到足够的启动温度就有使炉内的反应平衡崩溃的可能,要维持反应必须使炉温控制在220℃以上。反应温度过高,则SiCl4的含量会明显增加,这是因为它的结构具有高度的对称性,有很好的热稳定性,高达600℃也不会引起热裂解。而SiHCl3的分子结构是不对称的,热稳定性差,在400℃就开始分解,550℃剧烈分解。因此,为了获得高含量的SiHCl3产品,温度宜控制在280~320℃。
2.1.5.2,氧和水份的影响
氧和水份对合成反应为害很大。因为Si-O键比Si-Cl键更稳定,进入系统的氧元素都会与硅合成硅胶或硅氧烷类物质,一方面在硅粉表面形成一层致密的氧化膜,影响反应的正常进行,使产物中的SiHCl3含量降低(见下图),此外还形成硅胶类物质堵塞管道,使系统发生故障
3游离氯的控制
游离氯对合成炉的影响主要是两方面:一是含量过高有爆炸危险,另外是影响合成的质量。通过HCl合成炉反应时氢过量4%左右来控制游离氯,并用含量检测仪连续检测合成HCl质量来确保游离氯含量低于要求。
4.硅粉粒度
硅粉与HCl气体反应是在硅的表面进行的,硅粉比表面积越大越有利于反应,即要求硅粉粒度应该较小。但是,粒度过小,流化时容易形成聚式流化床,有较多的气泡,将抑制传质的进行,使HCl的一次转化率降低。同时,较小的颗粒迅速反应,很快就达到带出粒径范围,使硅粉的利用率降低。因此,选用粒度适中的硅粉是很重要的。
5.硅粉料层高度和HCl流量
硅粉料层高度和HCl流量是影响SiHCl3产量和质量的重要因素,料层过高压力降增加,要求进气压力相应提高。过高的压力降造成炉内的稳定性变差,有形成“喷泉”或“沟流”的可能,更有形成“管涌”的可能性,这都会影响设备和原料的利用率,不利于生产的正常进行。如果料层过低,产生不均匀沸腾,反应的接触时间也缩短,产量会降低。HCl的流量决定了颗粒床的流化状态。具体的床层高度和HCl流量需通过生产实践确定。
(六)某些不正常现象及消除方法
1.沸腾床层不沸腾。出现该种情况可能有两种情况:
a.气流量正常,但料层过厚。此时就要适当减小进料量,同时增加一定气流量,以保证床层沸腾,然后逐步减小进气量、增加进料量至正常水平。
b.床层高度正常,但气流量过小。此时是,只要怎加气流量到床层发生沸腾。
c.床层高度过低,气流量过小。此时气体与硅粉接触不好,无法是床层沸腾。这就需要同时逐步调节进料量和进气量至正常水平。
2.床层沸腾过于剧烈。出现该现象,一般是由于气流量过大,但床层高度正常,使硅粉被气体大量带出合成塔。此时要逐步调节气流量至正常水平。
(七)安全生产要点
(1).可能发生的危险情况
1.HCl气体的泄漏;
2.SiHCl3泄露、燃烧甚至爆炸;
3.硅粉粉尘泄露;
4.HF腐蚀;
5.管路、设备高空维修作业坠落伤人;
6.水解物撞击着火伤人;
7.维修过程机械伤人。
(2)预防、处理措施
1.生产SiHCl3车间内、储料区应防火、防爆、通风,严禁烟火。
2.上班前必须按照各岗位特点佩戴相应劳保用品及专用工具才能上岗作业,并定期检查劳保包用品是否正常,发现过期或有损伤的劳保用品应及时更换。
3.若发生故障必需马上时停车维修时,应先断电,将SiHCl3、HCl等气体排净,在淋洗塔内用大量水吸收或水解,直至气体浓度较小时,方能拆开检修。
4.操作室内严禁烟火,设备不许敲打撞击。
5.由于三氯氢硅物性限制,生产过程中一旦发生爆炸,首先切断三氯氢硅料源,隔离着火点,然后用CCl4、CO2灭火器灭火,少量可用大量水水注灭。
6.系统和管路均应密封闭,操作人员应定期检查,不容许设备发生跑、冒、滴、漏等情况;一旦发现泄露,应立即且断源,及时进行处理。
7.一旦发现皮肤沾染化学品时,应先用抹布将化学品擦掉,让后用大量清水冲洗,然后按医嘱治疗。
8.设备、场地需动火时,应先检查动火地是否有易燃易爆的气、液体,只有当空间环境低于爆炸极限时,并且准备好相应的灭火装置才能动火。
9.检查尾气淋洗塔时应先用N2吹扫或水淋洗后,在进行检修,以防着火伤人。
10.高空作业时,要先做好安全防护措施才能作业。
(八) 生产过程中的三废排放和处理
三氯氢硅合成过程中主要产生四氯化硅、氯化氢、二氯二氢硅、硅渣等废料,其中,四氯化硅、二氯二氢硅经气液分离后回流送入三氯氢硅合成塔中,与氯化氢、氢气反应继续生成三氯氢硅;氯化氢气体经干燥后也送入合成塔中参加反应;硅渣用3%盐酸浸泡后,经过滤器过滤,将其中的硅粉过滤出来,干燥后投入合成塔中循环利用;过滤下的无用废渣进行深度掩埋处理。