1. 概述
1.1 安全阀的功能
安全阀是靠入口介质静压驱动,在出现工况不正常或事故时开启,排出一定数量介质,以防止被保护设备或系统内的压力超过预定的安全值。当压力恢复接近正常后,安全阀自行关闭,阻止介质继续流出。
1.2 安全阀分类 可按以下三种方法分类:
1.2.1 按国家标准《安全阀的一般要求,GB12241-89》分类
A、直接荷载式
一种直接用机械载荷加重锤、弹簧等克服阀瓣下介质压力所产生作用力的安全阀;
B、带动力辅助装置式
系一专用安全阀类型,在阀杆处加一个动力辅助装置,如果需要,可在低于正常开启压力下开启,不适用于炼厂;
C、带补充载荷式
该安全阀系一专用类型,在阀杆处加一向下外力,在达到开启压力前,始终保持有一增强密封的附加力,不适用于炼厂;
D、先导式
先导式是由一个导阀排出的介质来控制主阀开启的安全阀,有活塞式和隔膜式两种基本类型。
活塞式由装浮动活塞的主阀和一个导阀构成,活塞的顶部有效面积大于底部有效面积。当主阀关闭时,底部承受系统的压力,其顶部有一气室,通过导管与入口系统相通,顶部同样受系统的压力。由于顶部面积较底部大,因而主阀被紧紧地压在阀座上。系统压力升高到定压时,导阀开启,将顶部气室介质排出,压力降低,当主阀底部压力能克服顶部压力时,主阀开启,工艺介质流过主阀排至泄压系统或大气。系统压力降低到接近正常操作压力时,导阀关闭,气室压力上升,从而关闭主阀。
膈膜式与活塞式的机能相似,只是活塞用柔性隔膜和阀盘组成的整体所取代。在定压下,隔膜顶部放空,主阀开启,压力恢复到接近正常状态时,隔膜重新充压,主阀关闭。
先导式安全阀可用于各种工况,但由于其价格过高,一般宜用于背压超过30%定 6
压和腐蚀性介质或易堵塞阀孔的介质等工况。
1.2.2 按阀片开启高分类
A、全启式
h≥1/4do
h—开启高度,cm;
do—喷嘴直径,cm。
全启式安全阀泄放量大,在相同的泄放面积条件下,全启式的泄放量为微启式泄放量的许多倍。
由于全启式与微启式的性能不同,按全启式方法计算出的泄放面积不可用相同的微启式泄放面积代用。
全启式安全阀一般用于排放介质为气体的条件下,当到达开启压力时瞬时全启。
B、微启式
1/4do>h≥1/40do
微启式安全阀一般用于排放介质为液体的条件下,当到达开启压力时,开始开启,并随压力的升高而继续开大。
介质为气体时,一般选用全启式。介质为液体时,可以选用微启式,也可选用全启式。介质为液体选用全启式安全阀时,它的动作性能则变为微启式,其喷嘴内径应按微启式计算(见式4-1-3B)。
1.2.3 按结构不同分类
A、封闭和不封闭弹簧式
易燃易爆和有毒介质应选用封闭式,蒸汽、空气和惰性气体可选用不封闭式;
B、带扳手和不带扳手
扳手的作用主要是检查阀瓣的灵活程度,有时也可用作紧急泄压;
C、带散热片和不带散热片
介质温度大于300℃时应选用带散热片式;
D、平衡式和非平衡式
普通型安全阀一般为非平衡式,其弹簧校正压力受背压影响,即弹簧压力应校正为定压Ps减去背压P2之值。平衡式有两种基本类型——活塞式和波纹管式,国内生产波纹管式。波纹管能防止背压变化所产生的不平衡力,因而弹簧力所平衡的压力值即为定压值。波纹管还能将导向套、弹簧和其它顶部工作部件与通过的介质隔开。
6
1.2.4 按平衡内压的方式分为弹簧式、杠杆式和先导式。
1.3 安全阀结构
安全阀的典型结构见下面图1-3-1~7
6 图1-3-1 图1-3-2 图1-3-3 图1-3-4 图1-3-5 图1-3-6 图1-3-7 弹簧封闭全启式 弹簧封闭带扳手全启式 弹簧封闭微启式 弹簧封闭带扳手微启式 波纹管式 先导式(I) 先导式(II)
图1-3-1弹簧封闭全启式安全阀 1-保护罩;2-调整螺杆;3-阀杆;4-弹簧 5-阀盖;6-导向套;7、阀瓣;8-反冲盘; 9-调节阀;10-阀体;11-阀座
图1-3-3弹簧封闭微启式安全阀
1-保护罩;2-调整螺杆;3-阀杆;4-弹簧 5-阀盖;6-导向套;7、阀瓣;8-衬套; 9-调节阀;10-阀体
6 图1-3-2 弹簧封闭带扳手全启式安全阀 注:各部件名称同图1-3-1 图1-3-4 弹簧封闭带扳手微启式安全阀
注:图中各部件名称同图1-3-3
6 图1-3-5 波纹管安全阀
图1-3-6先导式安全阀(I) 图1-3-7 先导式安全阀(II)
1.4 操作参数
1.4.1 最高操作压力P(表) 设备运行期间可能达到的最高压力,一般应按不同工艺过程确定。
1.4.2 设备设计压力PD(表) 在一般条件下,设备的设计压力应按下列要求确定: 当P≤1.8MPa(表)时,PD=P+0.18 当1.8<P≤4MPa(表)时,PD=1.1P 当4<P≤8MPa(表)时,PD=P+0.4 当P>8MPa(表)时,PD=1.05P
1.4.3 安全阀定压Ps(表) 系安全阀开启压力,定压Ps必需等于或稍小于设备的设计压力PD(表)。
1.4.4 积聚压力Pa(表) 安全阀排放介质过程中,允许压力增加超过设备的设计压力的数值,可按表1-4-1选取
表1-4-1 定压和积聚压极限
* 对设计压力的百分数。
1.4.5 容许过压Ph(表)容许压力增加超过定压的数值,如果定压等于设计压力,则过压等于积聚压。如果定压小于设计压力,过压为积聚压力+设计压力与定压的差值,即: Ph=Pa+PD-Ps
1.4.6 最高泄放压力Pm(绝) 安全阀达到最大泄放能力时的压力,即定压加上容过压+0.1。
6
当定压等于设计压力时
Pm=Ps+Pa+0.1=PD+Pa+0.1
当定压小于设计压力时
Pm=Ps+Ph+0.1=PD+Pa+0.1
式中 Ps、Pa、Ph—定压、积聚压力、过压,MPa(表)
Pm—最高泄放压力,MPa(绝)
1.4.7 背压P2(安全阀出口压力)
背压是由于排放系统有压力而存在于安全阀出口的压力,它是迭加背压和积聚背压的总和,积聚背压是在安全阀开启后,由于介质流动所增加的压力,迭加背压是在安全阀开启后存在于其出口的静压,它是由其它原因在排放系统中产生的压力。
1.4.8 回座压力
它是安全阀的定压与关闭压力的差值,以定压的百分数或压力单位表示。回座压力必须小于定压并大于操作压力。
1.4.9 安全阀的压力等级关系(即容器设计压力,安全阀容许积聚压、定压、过压)见图1-4-1。
6
6
注:1、与ASME锅炉压力容器规程和《压力容器安全技术监察规程,1990》 基本一致; 2、所示压力条件是安装在容器的安全阀条件; 3、操作压力可高于或低于90%; 4、回座和压差应参照ASME规程有关章节。
1.4.10 确定单阀、多阀泄放压力示例见表1-4-2。
表1-4-2 确定单阀、多阀泄放压力示例(操作事故)
1.4.11 温度 按工艺操作温度考虑。
2 安全阀设置原则
2.1 属于下列情况之一的容器和设备必须设置安全阀(或爆破片)。
2.1.1 在生产过程中,由于火灾、物料的化学反应、动力故障或操作故障等原因,可能导致容器或设备的内压超过设计压力;
2.1.2 顶部操作压力大于0.07MPa的压力容器;
2.1.3 顶部操作压力大于0.03MPa的蒸馏塔、蒸发塔和汽提塔(汽提塔顶部蒸汽通入另一蒸馏塔者除外);
2.1.4 往复式压缩机各段出口或电动往复丞、齿轮泵、螺杆泵等容积式泵的出口(本身已有安全阀者除外);
6
2.1.5 凡与鼓风机、离心式压缩机、离心泵或蒸汽往复泵出口连接的设备不能承受其最高压力时,上述机泵的出口阀后;
2.1.6 可燃的气体或液体受热膨胀可能超过设计压力的设备;
2.1.7 由几个容器组成的一个压力系统但中间设有隔断阀时,应视为几个独立的容器,每个容器均应按上述要求设置安全阀。
2.1.8 减压阀后,且减压阀后的设备或管道不能承受减压阀前的压力时。
2.2 属于下列情况之一的容器或设备不需设置安全阀。
2.2.1 加热炉炉管;
2.2.2 离心泵出口(连接的设备不能承受其最高出口压力者除外);
2.2.3 对于设计压力不低于压力来源,且不因介质化学反应或受热而使其压力超高的容器;
2.2.4 由几个容器组成的一个压力系统且中间不设隔断阀时,可只按一个压力系统考虑,如在前端设置安全阀,后面的容器可不设安全阀。
2.3 有可能被介质堵塞或腐蚀的安全阀,应在其入口前设爆破片或在其出入口管道上采取吹扫、加热或保温等防堵措施。
2.4 有突然超压或发生瞬时分解爆炸危险介质的反应设备,如安全阀不能满足要求时,应设置爆破片或爆破片和导管。
2.5 因介质爆聚、分解造成超温超压可能引起爆炸的反应设备,应设报警信号和泄压排放设施,以及自动或手动遥控的紧急切断进料的设施。
3 泄放量的确定
在计算安全阀时,应先确定工艺所要求的泄放量。
导致设备超压的原因: 一是操作故障,二是火灾。确定安全阀的泄放量时,应根据工艺过程的具体情况并按可能发生危险情况中的最大一种考虑,但不应机械地将各种不利情况考虑在同一时间发生。
3.1 操作故障时的泄放量
在一般情况下,可参考表3-1-1所列基准确定,此表取自APIRP520(第五版,1990)。如果掌握同类装置的最大实际泄放量,则可按该值确定泄放量。
6
表3-1-1 几种选定条件泄放量基准
6
续上表
表3-1-1与中石化总公司标准《炼油装置工艺设计技术规定SHJ1076-86》表7.1.2基本相同。
3.2 换热器管破裂时,安全阀泄放量可按式3-2-1~式3-2-2计算。 介质为气相时
Gv=246.3×104×di2(△P·ρv)0.5 (3-2-1) 介质为液相时
GL=16.8×104×di2(△P/ρ 式中:
Gv—气体泄放量,kg/h; GL—液体泄放量,m3/h; di—换热器管内径,m; △P—高低压侧压力差,MPa;
6
γ
)0.5 (3-2-2)
3
ρ ρ3.3 液体膨胀
v—气体密度,kg/m
γ
;
—液体相对密度。
充满液体的容器或长管道由于液体膨胀而要求的泄放量,可按式3-3-1计算: GL?0.00361?
式中:Q—传入热量,W;
Cp—液体比热,KJ/kg·℃;
ω—液体每升高1℃体积膨胀系数,见表3-3-1; 其它符号意义同前。
表3-3-1 各种烃液体和水在15.6℃下的膨胀系数ω
3.4 气体储罐等压力容器的安全泄放量,按式3-4-1计算: Gv=2.83×10-3ρv·V·di2 (3-4-1) 式中:Gv—安全泄放量,kg/h; ρ
v—泄放条件下气体密度,kg/m
3
wQ
(3-3-1)
???CP
;
di—容器进口管内径,mm;
6
V—容器进口管内流速,m/s。
3.5 火灾条件下容器的安全泄放量
由于容器内液体润湿的表面积,在受到火焰辐射时全产生蒸气。为了确定蒸气产生量,先要确定受火焰源辐射影响的润湿表面积,一般系指等于或低于火焰源7.5m的那部分容器表面积。而火焰源是指地面火源,但也可能是受到大量火点的任何标高位置,应根据具体情况确定。容器的安全泄放量可按式3-5-1~3-5-3计算。
3.5.1 介质为易燃液化气体或装在有可能发生火灾的环境下工作时的非易燃液化气体:
A、对无绝热材料保温层的压力容器
25.5?104F?A0.82
Gv? (3-5-1) Hv
式中Gv—安全泄放量,kg/h;
F—系数,容器设在地面下用砂土覆盖时,取F=0.3;容器在地面上时,取F=1;
容器设置在大于10L/m2min喷淋设施下时,取F=0.6。
A—容器的受热面积(m2),按下列公式计算(Do外径,m; L长度m; L’容器内最高液位,m);
对半球形封头的卧式容器A=π·Do·L;
对椭圆形封头的卧式容器A=π·Do(L+0.3Do);
对立式容器A=π·Do·L’;
对球形容器A=1/2π·D0或从地平面起到7.5m高度以下所包括的外表面积,
取二者中较大的值;
Hv—在泄放压力下液体的蒸发潜热,kJ/kg。(低于93kJ/kg不能用)。 如果在没有灭火设备的场合,式3-5-1应改为3-5-2:
2
41.9?104F?A0.82
Gv? (3-5-2) Hv
B、对有完善的绝热材料保温层的液化气体压力容器
6
9.4(650?t)??A0.82
Gv? (3-5-3) ??Hv
式中:Gv—容器的安全泄放量,kg/h;
t—泄放压力的饱和温度,℃;
λ—常温下绝热材料的导热系数,W/m·k;
δ—保温层厚度,m;
其他符号同前。
3.5.2 介质为非易燃液化气体的容器,而且装在无火灾危险的环境下,安全泄放量可根据其有无保温层分别选用不低于按公式3-5-1~3-5-3计算值的30%。
4. 喷嘴面积计算
4.1 介质为气体
气体通过安全阀喷嘴时,其速度和比容随下游压力的减少而增大,一直增大到极限速度为止,此极限速度即为该气体的声速,相当于极限速度的相应流率,称为临界流率。
声速下的喷嘴喉管压力Pcf与入口压力(即最高泄放压力)Pm之绝压比称为临界压力比,Pcf称为临界流动压力。
气体的临界压力比可用理想气体关系的公式计算
2k?1 ?[] (4-1-1) PmK?1
式中:K—气体的绝热指数(Cp/Cv);
Pcf—临界流动压力,MPa(绝);
Pm—进口处压力(即最高泄放压力),MPa(绝),
即安全阀定压+容许过压+大气压。
一般烃类气体Pcf/Pm值大都在0.5~0.6之间,其与K值的关系见下表4-1-1。
6 Pcfk
表4-1-1 K值与Pcf/Pm值关系表
如果喉管下游压力P2(即安全阀出口压力)高于临界流动压力,此时的流动状态为亚临界流动。
4.1.1 临界流动状态下喷嘴面积计算,可按式4-1-2计算 Ao? 对全启式
do? 对微启式
do? 式中:
Ao—喷嘴面积,cm2; h—安全阀开启高度,cm; φ—锥形密封面的半锥角度,°; do—喷嘴内径,cm;
Gv—气体最大泄放量,kg/h; Pm—最高泄放压力,MPa(绝); T 1—进口处气体温度,K; M—气体分子量;
Z—在Pm压力下气体的压缩系数;
KF—流量系数,应由制造厂提供,参见附录二。
C—气体特性系数,仅与气体的绝热指数K有关,可用下式计算
0.13?0GvC?KF?Pm?Kb
T1Z
(4-1-2) M
Ao
(4-1-3) 0.785
Ao
(4-1-3B)
?hsi?n
2K?1
C?52K( (4-1-4) )
K?1
也可用表4-1-2查得;
6
K?1
Kb—背压校正系数,对普通型安全阀,随着P2值增大,安全阀的理论泄放量
将随之减少。但当P2<Pcf时,对泄放量的影响较小,而普通型安全阀
的P2值要求小于0.1Ps,在此条件下,Kb值可取为1。当P2值大于 0.1Ps时,一般应选用波纹管(平衡型)安全阀,当P2值大于0.3Ps可
选用先导式安全阀。波纹管安全阀的Kb值见表4-1-3。
表4-1-2 不同K值与C值关系
* 内插值因在K接近于1时,C变为不定的无穷数。
6
表4-1-3 波纹管安全阀Kb值
表4-1-3是国外制造商提供的平均值(见API RP520-90),背压低于0.34MPa(表)时,不应选用上表数值,而应由制造厂按背压条件提供Kb值。
4.1.2 亚临界流动状态下喷嘴面积计算为了简化计算,仍然采用式4-1-2计算,对普通型安全阀,Kb校正系数需改用表4-1-4值;对波纹管安全阀,Kb值应由制造厂提供。其它符号意义和取值与临界流动状态相同。
值
*绝对背压%为P2/Pm%(以绝压计) 例题1≌ 已知下列泄放要求:
GV=24318kg/h,烃蒸气平均分子量M=65,K=1.1, T1=348K(75℃),PS=0.51MPa(表),即设备的设计压力, P2(背压)=0(表)。
计算出下列数据,容许积聚压为10%(由于定压即为设备压力,积聚压等于过压),最高泄放压力Pm=0.51×1.1+0.1=0.661MPa(绝),Z=0.84,临界压力比=0.59(查表4-1-1),临界流动压力Pcf=0.661×0.59≈0.39MPa(绝)=0.29MPa(表)。
因背压P2=0,小于Pcf,处于临界流状态,因此可用式4-1-2计算喷嘴面积
6
0.130?24318348?0.84
A0??31.9cm2
326?0.975?0.661?165
2
KF采用0.975,Kb=1,C=326(查表4-1-2)。
例题2 把例1中的迭加背压改为0.37MPa(表),其它数据与例1相同,选用普通型安全阀。
因迭加背压等于0.37MPa(表),大于临界流动压力0.29MPa(表),气体处于亚临界状态。
容许积聚背压0.1×0.51=0.051MPa
总背压P2=0.37+0.051=0.421MPa(表)=0.521MPa( 绝) P2/Pm=0.521/0.661=79%,从表4-1-4查得Kb=0.88
AO?
0.13?24318348?0.84
?36.25cm2
326?0.975?0.661?0.8865
4.2 介质为水蒸汽(压力小于10MPa)按4-2-1计算
AO?
GV
500Pm?KF?K?
式中GV--水蒸汽最大泄放量,kg/h; AO--喷嘴面积,cm2;
Pm--最高泄放压力,MPa(绝); Kφ--蒸汽过热度校正系数,见表4-2-1; KF--由制造厂提供。
6
4.3 介质为液体 按液体介质设计的安全阀应取得能力检验证,并给定流量系数,其喷嘴面积可按式4-3-1计算
A O ?
(4-3-1)
式中AO--喷嘴面积,cm2; GL--液体泄放量,m3/h;
??--泄放温度下液体相对密度(相对于20℃水); Pm,P2--最高泄放压力,出口压力,MPa(表);
KF--流量系数,应由制造厂提供,需要进行估算时,取KF=0.65;
Kb--背压校正系数,对于普通型安全阀,Kb=1,对于波纹管式安全阀,一般由制造厂给出Kb值,必要时,可从表4-3-1查得。 表4-3-1 波纹管式安全阀Kb值
K?--粘度校正系数 可从表4-3-2查得 表4-3-2 粘度校正系数K?
GL???0.5
15Kb?K??KF?Pm?P2
根据雷诺数Re选取K?值时,需要先按非粘性介质(K?=1)用式4-3-1确定喷嘴面积,再从有关制造厂的样本中选取接近或稍大的喷嘴面积的安全阀,按式4-3-2计算雷诺数
6
31300 G L ? ? ? (4-3-2)
Re??At
O
式中?--流动温度下介质的绝对粘度,MPa·S(其值与厘泊相等);
A’o--初选的安全阀喷嘴面积,cm;
其它符号见前。
根据计算的雷诺数从表4-3-2查得K?值,再按式4-3-1计算校正后的喷嘴面积。如果校正后的喷嘴面积大于初选的喷嘴A’O,则需选用较大A’o的面积重新进行计算,直到基本一致为止。
4.4 液体膨胀时喷嘴面积计算 可按式4-4-1计算:
A O (4-4-1) ? 0.5
式中GL--液体膨胀的泄放量,m3/h;
其它符号相同。
4.5 介质为气液两相流体 可按前述方法分别计算气体和液体排放所需的喷嘴面积,再将两者相加即为安全阀喷嘴的总面积。
5 安全阀的选用
5.1 石油化工装置所用安全阀一般均选用弹簧全启式,在一般情况下,可选用普通型安全阀。当背压变化较大时,可选用波纹管(平衡型)式或选导式安全阀。但波纹管型不适用于酚、蜡液、重石油馏分、含焦粉等介质以及往复式压缩机等场所。因为在这些情况下,波纹管有可能被污染或被损坏。如选用先导式时,导阀由制造厂配,故应将介质条件提交制造厂,以满足工艺要求。
5.2 根据介质的操作温度和安全阀定压值确定安全阀的公称压力和最高泄放压力Pm。
5.3 根据计算所得出的喷嘴面积,可从安全阀样本或其他资料中选用安全阀,选用的安全阀喷嘴面积必须等于或稍大于计算面积。如果一个安全阀的喷嘴面积不能满足需要,
6 GL??0.55.9(Pm?P2)
可选用两个或多个安全阀并联。由于多阀的定压和积聚压力与单阀不同,须按表1-4-1选取定压的积聚压计算所需喷嘴面积,再选用合适的安全阀,使其总面积等于或稍大于计算面积。对排入全厂性放空系统的直径较大的安全阀,若所选用安全阀的实际喷嘴面积比计算面积大得多时,应反算安全阀实际排放的最大瞬时量,以保证火炬系统的安全。
5.4 弹簧安全阀定压按不同结构的安全阀的要求确定。普通型安全阀在常压下调整弹簧时,其弹簧定压应调整为安全阀定压Ps减去其背压P2的差值,即弹簧定压值为Ps-P2;对波纹管安全阀,弹簧定压值即为安全阀的定压值Ps。
在选用安全阀时,应注明其定压范围或确定其弹簧号。
5.5 对排入全厂性公用放空系统的安全阀,当其定压低于0.5MPa(绝)时,一般应选用平衡型或先导式安全阀,以适应放空系统压力波动的要求。
5.6 安全阀进出口管道一般不设置阀门,但对易燃、有毒、粘性或含固体介质的容器,为便于安全阀的更换或清洗,可在容器与安全之间设置隔断用闸阀,正常运行时,偏阀必须保持全开,并加铅封。如装有隔断阀的安全阀的出口系排入全厂性放空系统,其出口也应设置隔断阀和副线阀,以防其它装置的安全阀排放时影响该安全阀系统,出口阀(全开)和副线阀(全关)均应予铅封。
5.7 普通型安全阀的总背压一般宜在10%左右,对有多个安全阀排入一个公用的总管时,背压变化范围要限制在最低定压安全阀的定压10%左右,据此原则确定出总管的直径。
5.8 安全阀的进口或出口接管的直径不得小于其进口或出口的直径。当几个安全阀并联安装在同一设备上时,进出口主管的截面积应等于或大于各管截面积之和。
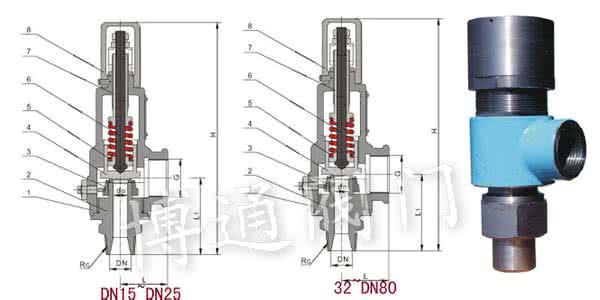
6 安全阀的安装设计
6.1 安全阀的安装
6.1.1 在设备或管道上的安全阀一般应垂直安装。但对设置在液体管道、换热器或容器等处的安全阀,当阀门关闭后,可能由于热膨胀而使压力升高的场所,可水平安装。
6.1.2 安全阀不应安装在长的水平管道的死端,因死端容易积聚固体物的和液体。
6.1.3 安全阀一般应安装在易于检修和调节之处,周围要有足够的工作空间,如:立式容器的安全阀,DN80以下者,可安装在平台内靠外侧;DN100以上者安装在平台外靠平台处,借平台可以阀门进行维护和检修。
6.1.4 由于直径安全阀重量大,故在布置时要考虑大直径安全阀拆开后吊装的可能,必
6
要时要设置吊杆。
6.2 安全阀入口管设计
安全阀入口管道最大压力损失一般不应超过安全阀的3%,它是按通过安全阀的最大流量计算得出的(包括入口压力损失、管道阻力和切断阀阻力之和)。为了减少入口压力降,可采取下列措施:
6.2.1 安全阀的安装位置应尺量靠近被保护的设备或管道。
6.2.2 管道或设备上安全阀接管公称直径可大于安全阀入口直径1~2级。
6.2.3 增大入口管径:安全阀入口管道的管径必须大于或等于安全阀入口管径,其连接大小头尽量设在靠近安全阀的入口处。
6.2.4 采用长半径弯头(R≥1.5DN) 。
6.2.5 考虑压力脉动的影响
(1) 由于安全阀入口不宜受脉动压力影响,在往复式压缩机或往复泵出口处应采用脉冲衰减器,但此时对管道内介质的流动有一定的影响。若采用先导式安全阀,将脉冲衰减器加装在导阀取压管上时,介质在管道内的流动不受影响。
(2) 管道上安装的安全阀,应位于压力比较稳定,距波动源有一定距离的地方。见表6-1-1所示。
6.3 安全阀出口管设计
安全阀出口管的设计应考虑背压不超过安全阀定压的一定值。对于弹簧式安全阀,普通型的背压一般不宜超过安全阀定压的10%,波纹管型(平衡型)的背压不超过安全阀定压的30%;对于先导式安全阀,其背压不超过安全阀定压的60%。具体数值应查阅制造厂样本,由工艺计算决定。
安全阀出口管道在安装时,应注意下列各点:
6
6.3.1 非易燃易爆介质的安全阀排放管向大气排放时,要注意其排出口不能朝向设备、平台、梯子、电缆等,且在安全阀出口弯头附近的低处开φ6~φ10的小孔。
6.3.2 易燃易爆气体安全阀排放管排入大气时,端部切成平口。使排出物直接向上高速排出,排放速度不小于150m/s,并应远离平台等有人之处,减少对周围环境的影响。这种方法近年来得到广泛应用替代了管口切成45°斜口。此时,在安全阀出口弯头附近的低处设置φ500mm左右小罐(加液位指示),当液位升高到0.7罐径时,将液体排至安全设施内。
6.3.3 安全阀向大气排放的放空管管口高度应符合下列要求:
(1) 无毒、无危险性气体安全阀排放口应高于以排放口为中心的7.5m半径范围内的操作平台、设备或地面2.5m以上。
(2) 对有毒或易燃、易爆、有腐蚀性的介质,排放口的排放高度应符合《石油化工企业设计防火规范,GB50160-92》和国家环保及卫生规定。
6.3.4 对石油化工装置,大多数工艺介质的安全阀排出口都是接至火炬总管上,并要求顺流向45°斜接在泄压总管的顶部,以免总管内的凝液倒入支管,并可减少安全阀的背压,但对干气系统,不一定有要坡度。
6.3.5 气体泄压系统排放管内不应有袋形积液处,安全阀的安装高度应高于泄压系统。若安全阀出口低于泄压总管或排出管需要抬高接入总管时,应在低处易于接近处设置φ500mm左右小罐(加液位指示)当液位升高到0.7罐径时将液体排至安全设施,以免袋形管段积液。
6.3.6 泄压管道使用闸阀时,阀杆应水平安装,不可朝上,以免阀杆和阀板的销钉腐蚀松动时,滑板下滑。
6.3.7 对可能有液化烃类排入的泄压管道,因介质气化而导致低温的管道,应考虑采用低温钢,并保温和伴热。
6.3.8 对有可能蒸汽吹扫的泄压管道,应考虑由于蒸汽吹扫产生的热膨胀。
6.4 安全阀的反作用力
气体或蒸汽由安全阀出口排入大气时,在出口管中心线上产生与流向相反的作用称为安全阀的反作用力。反作用力的计算详见《石油化工装置工艺管道安装设计手册,第一篇》第十七章第四节,必要时可按此进行设计。
6
6 附录一 安全阀出厂必须随带产品质量证明书,并在产品上装设牢固的金属铭牌。 1、安全阀的质量证明书应包括下列内容: (1) 铭牌上的内容; (2) 制造依据的标准; (3) 检验报告; (4) 监检报告; (5) 其它特殊要求。 2、安全阀的金属铭牌上应载明下列内容: (1) 制造单位名称、制造许可证编号; (2) 型号、型式、规格; (3) 产品编号; (4) 公称压力,MPa; (5) 阀座喉径,mm; (6) 排放系数(即流量系数); (7) 适用介质、温度; (8) 检验合格标记、监检标记; (9) 出厂年月。 以上摘自《压力容器安全技术监察规程,1990》第八章第131条。
附录二
国内制造厂推荐的流量系数,KF(亦称额定排量系数,Kdr) 下面是目前收集到的部分国内制造厂提供的流量系数。
如果制造厂提供额定流量,可以按国标《安全阀的一般要求》GB12241-89中有关部分的规定计算安全阀排量。
6