汽缸体是发动机的关键部件,在汽缸体缸孔的加工过程中,精镗涉及到的尺寸精度与形位误差将直接影响发动机的各项性能。过去,由于我们国家没有掌握缸孔精镗专用机床与加工中心的核心技术,而不得不从国外购买这种用于加工汽车发动机汽缸体缸孔的专用镗床及加工中心,因为技术垄断,这些机床的价格往往非常昂贵。十几年来,通过各机床厂商、汽车企业与各高校的共同努力,取得了一定的进步,但是由于工艺、技术等问题,研制的机床并不尽如人意。通过多年的研究试制,我们实验室团队人员在汽缸体缸孔加工技术上取得了较大的进展,开发研制的精镗缸孔双轴精密锁床处于国内领先水平,完全可以替代这类机床的进口。
1主要参数及技术难点分析
1.1主要参数
汽缸体名称:4缸直线型汽缸体
材料牌号:HT250
工件外形尺:311 mmx298 mmx237 mm
缸孔尺寸:直径栖5.5 mm,深度118 mm
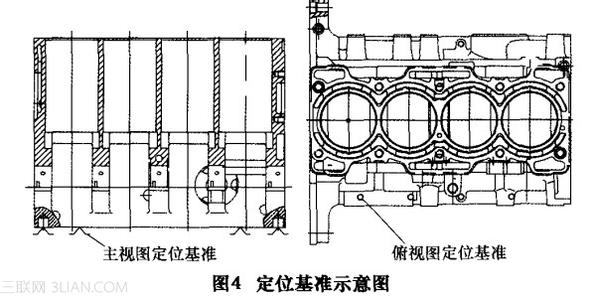
工件硬度:179-247 HBW
工件质量:30 kg
1.2技术难点分析
企业对汽缸体缸孔的尺寸精度及形位误差提出了较高要求,给出了图样,见图1。
(1)四缸孔 4xφ5.5 mm的形状位置公差要求较严格,既要保证四缸孔圆度0.008 mm、圆柱度0.008mm,又要保证缸孔轴线对曲轴孔公共轴线的垂直度0.04 mm.
(2)四缸孔直径要求φ65.5土0.02 mm.
(3)四缸孔听磨后的表面粗糙度要求Ra=0.32μm。
要达到以上所有的技术要求,加工难度很大。 首先对其技术难点进行分析:
2缸孔精镗加工工艺选择
在缸体加工中,缸孔精镗涉及的各项精度将会直接影响发动机的性能,因而企业在规划这道工序时会结合企业及产品实际情况而选择最合适的方案。缸孔精镗加工工艺选择涉及到加工设备、切削工艺、镗刀等因素。目前,缸体加工生产线应用最广的有两种,一种是完全由加工中心组成的自动缸体线;另一种则是由组合/专用机床和加工中心相混合的柔性线,即“混合型柔性自动线”,这种生产模式为众多汽车企业与机床厂商看好并优先采用,其优点是既具有相当的柔性又具有较高的生产效率,采用这种模式加工缸体时,缸孔的镗削工序由专用镗床完成。本课题缸体生产线采用的是“混合型柔性自动线”,即设计缸体缸孔加工专用镗床,缸孔的镗削工序由此专机完成。本课题设计的缸孔专用膛床见图20
镗孔是箱体类工件中加工孔的常用工艺方法之。对于长径比较小的孔,传统的工艺一般是采用刀具从工件的一端镗进,这是一种非常经济且应用极为广泛的孔加工方法。对于长径比较大的孔,如果采用传统工艺加工缸孔,由于锁轴呈悬臂状态,镗削时,由于镗臂的悬伸量较长,很容易造成被加工孔尺寸精度和形位精度超差,因而不采用这种加工方法,一般采用调头镗孔的方法。此缸体缸孔的孔径比为1.8,孔径比较小,故采用刀具从工件的一端镗进的传统工艺。为提高生产效率,将镗床设计为双镗头的专用立式镗床。镗削过程示意图见图3。
由于缸孔精镗后尺寸精度及形位精度要求均较高,在此专机上配备了带自动补偿系统的镗头,用以改善和提高缸孔加工质量。
为进一步提高缸孔加工质量,减小切削热带来的缸孔尺寸与形位偏差,提高切削速度,延长刀具使用寿命,缸孔精镗时采用湿式加工。
3缸孔精镗加工工艺设计
3.1基准的选择
合理正确地选择定位基准,是保证缸孔加工精度及提高加工生产效率的前提。工件定位基准的选择一般有以下4方面的基本原则:
(1)尽量使用工件上的设计基准作为定位基准,可以避免因基准不重合而引起的定位误差,保证加工精度;
(2)确保工件一次装夹能完成尽可能多的关镗部位的加工;
(3)属于批量加工时,对刀基准与工件定位基准重合;
(4)工件必须多次安装时应遵守基准统一的原则。
依据以上原则并结合缸孔加工实际,缸孔精镗加工时采用“一面两削”作为定位基准,限制缸体的6个自由度,如图4。
4结语
通过机床的成功试制,并对汽缸体缸孔进行加工实验,经过实测,缸孔的尺寸精度与形位精度均达到了图纸设计指标,机床投人使用一年多以来,各项性能均保持良好。缸体生产线项目在重庆某机械制造企业实施后,汽车发动机缸体生产线的生产节拍为2.5 min/件,缸体年生产量达到12万件,产值达到约1.2亿元,由于经济效益显著及生产线的成功研制,企业随即投人第二条生产线,实现了汽车发动机缸体大规模生产。 由佳密特高速加工中心http://www.giamite.com.cn 上传