催化裂解是在催化剂存在的条件下,对石油烃类进行高温裂解来生产乙烯、丙烯、丁烯等低碳烯烃,并同时兼产轻质芳催化裂解烃的过程。从一定程度上,催化裂解是从催化裂化的基础上发展起来的,但是二者又有着明显的区别。
催化裂解_催化裂解 -名词简介
催化裂解是在催化剂存在的条件下,对石油烃类进行高温裂解来生产乙烯、丙烯、丁烯等低碳烯烃,并同时兼产轻质芳
催化裂解烃的过程。由于催化剂的存在,催化裂解可以降低反应温度,增加低碳烯烃产率和轻质芳香烃产率,提高裂解产品分布的灵活性。
(1) 催化裂解的一般特点
① 催化裂解是碳正离子反应机理和自由基反应机理共同作用的结果,其裂解气体产物中乙烯所占的比例要大于催化裂化气体产物中乙烯的比例。
② 在一定程度上,催化裂解可以看作是高深度的催化裂化,其气体产率远大于催化裂化,液体产物中芳烃含量很高。
③ 催化裂解的反应温度很高,分子量较大的气体产物会发生二次裂解反应,另外,低碳烯烃会发生氢转移反应生成烷烃,也会发生聚合反应或者芳构化反应生成汽柴油。
(2) 催化裂解的反应机理
一般来说,催化裂解过程既发生催化裂化反应,也发生热裂化反应,是碳正离子和自由基两种反应机理共同作用的结果,但是具体的裂解反应机理随催化剂的不同和裂解工艺的不同而有所差别。
在Ca-Al系列催化剂上的高温裂解过程中,自由基反应机理占主导地位;在酸性沸石分子筛裂解催化剂上的低温裂解过程中,碳正离子反应机理占主导地位;而在具有双酸性中心的沸石催化剂上的中温裂解过程中,碳正离子机理和自由基机理均发挥着重要的作用。
(3) 催化裂解的影响因素
同催化裂化类似,影响催化裂解的因素也主要包括以下四个方面:原料组成、催化剂性质、操作条件和反应装置。
① 原料油性质的影响。一般来说,原料油的H/C比和特性因数K越大,饱和分含量越高,BMCI值越低,则裂化得到的低碳烯烃(乙烯、丙烯、丁烯等)产率越高;原料的残炭值越大,硫、氮以及重金属含量越高,则低碳烯烃产率越低。各族烃类作裂解原料时,低碳烯烃产率的大小次序一般是:烷烃>环烷烃>异构烷烃>芳香烃。
② 催化剂的性质。催化裂解催化剂分为金属氧化物型裂解催化剂和沸石分子筛型裂解催化剂两种。催化剂是影响催化裂解工艺中产品分布的重要因素。裂解催化剂应具有高的活性和选择性,既要保证裂解过程中生成较多的低碳烯烃,又要使氢气和甲烷以及液体产物的收率尽可能低,同时还应具有高的稳定性和机械强度。对于沸石分子筛型裂解催化剂,分子筛的孔结构、酸性及晶粒大小是影响催化作用的三个最重要因素;而对于金属氧化物型裂解催化剂,催化剂的活性组分、载体和助剂是影响催化作用的最重要因素。
③ 操作条件的影响。操作条件对催化裂解的影响与其对催化裂化的影响类似。原料的雾化效果和气化效果越好,原料油的转化率越高,低碳烯烃产率也越高;反应温度越高,剂油比越大,则原料油转化率和低碳烯烃产率越高,但是焦炭的产率也变大;由于催化裂解的反应温度较高,为防止过度的二次反应,因此油气停留时间不宜过长;而反应压力的影响相对较小。从理论上分析,催化裂解应尽量采用高温、短停留时间、大蒸汽量和大剂油比的操作方式,才能达到最大的低碳烯烃产率。
④ 反应器是催化裂解产品分布的重要影响因素。反应器型式主要有固定床、移动床、流化床、提升管和下行输送床反应器等。针对CPP工艺,采用纯提升管反应器有利于多产乙烯,采用提升管加流化床反应器有利于多产丙烯。
(4) 催化裂解工艺介绍
烃类催化裂解的研究已有半个世纪的历史了,其研究范围包括轻烃、馏分油和重油,并开发出了多种裂解工艺,下面对其进行简要的介绍。
① 催化裂解工艺(DCC工艺)。该工艺是由中国石化石油化工科学研究院开发的,以重质油为原料,使用固体酸择形分子筛催化剂,在较缓和的反应条件下进行裂解反应,生产低碳烯烃或异构烯烃和高辛烷值汽油的工艺技术。该工艺借鉴流化催化裂化技术,采用催化剂的流化、连续反应和再生技术,已经实现了工业化。
DCC工艺具有两种操作方式――DCC-Ⅰ和DCC-Ⅱ。DCC-Ⅰ选用较为苛刻的操作条件,在提升管加密相流化床反应器内进行反应,最大量生产以丙烯为主的气体烯烃;DCC-Ⅱ选用较缓和的操作条件,在提升管反应器内进行反应,最大量地生产丙烯、异丁烯和异戊烯等小分子烯烃,并同时兼产高辛烷值优质汽油。
② 催化热裂解工艺(CPP工艺)。该工艺是中国石化石油化工科学研究院开发的制取乙烯和丙烯的专利技术,在传统的催化裂化技术的基础上,以蜡油、蜡油掺渣油或常压渣油等重油为原料,采用提升管反应器和专门研制的催化剂以及催化剂流化输送的连续反应-再生循环操作方式,在比蒸汽裂解缓和的操作条件下生产乙烯和丙烯。CPP工艺是在催化裂解DCC工艺的基础上开发的,其关键技术是通过对工艺和催化剂的进一步改进,使其目的产品由丙烯转变为乙烯和丙烯。
③ 重油直接裂解制乙烯工艺(HCC工艺)。该工艺是由洛阳石化工程公司炼制研究所开发的,以重油直接裂解制乙烯并兼产丙烯、丁烯和轻芳烃的催化裂解工艺。它借鉴成熟的重油催化裂化工艺,采用流态化“反应-再生”技术,利用提升管反应器或下行式反应器来实现高温短接触的工艺要求。
④ 其它催化裂解工艺。如催化-蒸汽热裂解工艺(反应温度一般都很高,在800℃左右)、THR工艺(日本东洋工程公司开发的重质油催化转化和催化裂解工艺)、快速裂解技术(Stone & Webster公司和Chevron公司联合开发的一套催化裂解制烯烃工艺)等。
⑤ 石蜡基原料的裂解效果优于环烷基原料。因此,绝大多数催化裂解工艺都采用石蜡基的馏分油或者重油作为裂解原料。对于环烷基的原料,特别针对加拿大油砂沥青得到的馏分油和加氢馏分油,重质油国家重点实验室的申宝剑教授开发了专门的裂解催化剂,初步评价结果表明,乙烯和丙烯总产率接近30 wt%。
催化裂解_催化裂解 -区别简介
从一定程度上,催化裂解是从催化裂化的基础上发展起来的,但是二者又有着明显的区别,如下:
① 目的不同。催化裂化以生产汽油、煤油和柴油等轻质油品为目的,而催化裂解旨在生产乙烯、丙烯、丁烯、丁二烯等
催化裂解基本化工原料。
② 原料不同。催化裂化的原料一般是减压馏分油、焦化蜡油、常压渣油、以及减压馏分油掺减压渣油;而催化裂解的原料范围比较宽,可以是催化裂化的原料,还可以是石脑油、柴油以及C4、C5轻烃等。
③ 催化剂不同。催化裂化的催化剂一般是沸石分子筛催化剂和硅酸铝催化剂,而催化裂解的催化剂一般是沸石分子筛催化剂和金属氧化物催化剂。
④ 操作条件不同。与催化裂化相比,催化裂解的反应温度较高、剂油比较大、蒸汽用量较多、油气停留时间较短、二次反应较为严重。
⑤ 反应机理不同。催化裂化的反应机理一般认为是碳正离子机理,而催化裂解的反应机理即包括碳正离子机理,又涉及自由基机理。
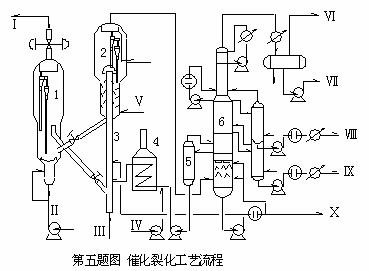