耐腐蚀泵适用于化工厂,用来输送不含固体颗粒,粘度类似于水的腐蚀性液体,被输送介质温度一般为20℃~105℃。泵的最高工作压力为1.6 Mpa,进口压力不高于0.6Mpa。
耐腐蚀泵_耐腐蚀泵 -简介
耐腐蚀泵就是输送带腐蚀性介质的泵,要求对流部件采用耐腐蚀性材料,如氟塑料,不锈钢等材质。南方泵业生产的耐腐蚀泵具有结构简单,性能平稳,转速高,体积小,重量轻,效率高,流量大,容易操作和维修等优特点。
耐腐蚀泵_耐腐蚀泵 -用途
耐腐蚀泵广泛适用于化工、制酸、制碱、冶炼、稀土、农药、染料、医药、造纸、电镀、电解、酸洗、无线电、化成箔、科研机构、国防工业等行业输送任意浓度的酸性、碱性、油类、稀有贵重液体、毒性液体、挥发性的腐蚀性化学介质。耐腐蚀泵_耐腐蚀泵 -分类
耐腐蚀泵按照安装方式可分为卧式和立式两种。 卧式耐腐蚀泵不同于传统的离心泵,它具有结构简章、可靠、维修方便的特点。泵叶轮与泵壳之间间隙大,固体物不受任何阻碍即可排出,且完全无堵塞。适用于输送固液混合液体,悬浮固体 和纤维状织物的介质。固体颗粒直径不大于排出口径的60%,纤维长度不大于排出口径的五倍。耐腐蚀泵_耐腐蚀泵 -耐腐蚀泵性能曲线图
塑宝SD型耐腐蚀自吸泵
塑宝SD型耐腐蚀自吸泵性能曲线图
塑宝TD型耐腐蚀立式泵特性曲线图
塑宝TD型耐腐蚀立式泵
耐腐蚀泵_耐腐蚀泵 -安装方法
1、安装前的准备工作
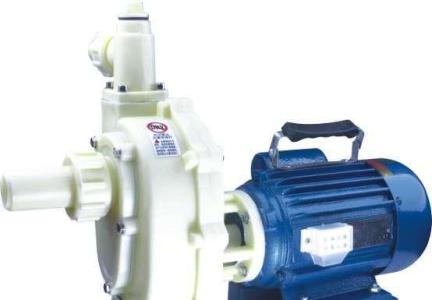
耐腐蚀泵
1)检查水泵和电机,确认在运输和装卸过程中没有损伤
2)准备工具和起重机械,并按图检查机器的基础
2、安装顺序
1)整套水泵运抵现场时,都已装好电机,找平底座时,可不必卸下水泵和电机
2)将底座放在地基上,准备找平后填充混凝土之用。
3)用水平仪利用泵的吐出口平面检查底座的水平度,找平后,安上地脚螺栓,用混凝土灌注地脚螺栓。
4)将钢尺放在联轴器上(上、下、前、后测量),检查泵与电机的轴心线是否重合。
5)待固定地脚螺栓的混凝土完全干固后,拧紧地脚螺栓的螺母,最后再检查一下整台机组的水平度,稍有不平时,可用楔铁找平。
6)安装吸水和出口管路,当管路与泵结合时,应注意勿使管路的重量和压力增加到泵上,以免泵出现变形。
7)清理环境,保持卫生。
水泵的装配和拆卸
(一)装配顺序
1、在热油中加热滚动轴承直至80度,取出装在轴的轴户处。
2、把带有轴承的轴压装在悬架内。
3、在两个轴承端盖放上纸垫,用螺栓紧在悬架上,注意利用纸垫调整轴承与轴承端盖的间隙(即轴在悬架内的窜动量)0.2-0.4毫米。
4、将挡水圈、填料压盖、填料环装在轴上,再把泵盖与悬架紧固在一起。
5、在轴套内孔的沟槽放上“0”型密封圈,将轴套装在轴上。
6、镶上叶轮键,装上叶轮,止退垫圈,用叶轮螺母拧紧,再折弯止退垫圈的露出部分,防止叶螺母松动。
7、将完整的转子部件装入泵体中,用螺钉和螺母坚固住。
8、用螺钉和弹簧垫圈把支脚固定在悬架上。
9、镶上泵联轴器键,装上泵联轴器。
(二)拆卸:按装配的相反顺序进行。
耐腐蚀泵_耐腐蚀泵 -使用及维护保养方法
1、检查泵及管路各结合处有无松动现象。用手转动泵试看泵是否灵活,然后试试看电机转向。
2、向悬架内加入轴承润滑机油,观察油位应在油标的两刻线之间。
耐腐蚀泵
3、拧下泵体的引水螺塞,灌引水。
4、关好出水管的闸阀和出口压力表和进口真空表。
5、开动电机,当泵正常运转后,打工出口压力表和进口真空表,视其显示适当压力后,逐渐打开闸阀,同时检查电机负荷情况。
6、尽量控制泵的流量和扬程在泵标牌上注明的范围内,保证泵在高效率点附近长期运转,以便获得最大的节能效果。
7、水泵的运转过程中,轴承升温不超过环境温度35度,最高温度不超过80度。
8、如发现泵有异常声应立即停车检查原因。
9、泵要停止使用时,先关闭闸阀、压力表,然后停止电机。
10、泵在工作的第一个月内,经100小时更换润滑油。以后每隔500小时,换油一次。
11、经常调整填料压盖,保证填料室内的滴漏情况正常。
12、泵在寒冬季节使用时,停车后,须将泵体下部放水螺塞拧开将水放净,防止冻裂。
13、泵长期停用,须将泵全部拆开,擦干水份,将转动部位及各结合处涂以油脂装好,妥善保存。
耐腐蚀泵_耐腐蚀泵 -渗漏原因及解决方法
一、常见的渗漏现象
1、定期渗漏
辅助密封与轴耐腐蚀泵转子轴向运动量大,干扰能力,动环不能移动和灵活的轴。耐腐蚀泵转动,固定环的磨损,没有补偿位移。耐酸泵密封,轴向跳动应小于0.1,辅助密封与轴的干扰量要适中,确保径向密封和卡环装配确保在轴上移动(移动环压力的弹簧可以自由地弹了回来);密封表面的润滑油量不足而造成干摩擦或磨损密封。
反应:润滑油表面腔室高度应添加到高于动、静环密封面。
(1)耐腐蚀泵转子轴向窜动量大,辅助密封与轴的过盈量大,动环不能在轴上灵活移动。在耐腐蚀泵翻转动、静环磨损后,得不到补偿位移。
对策:在耐腐蚀泵装配机械密封时,轴的轴向窜动量应小于0.1mm,辅助密封与轴的过盈量应适中,在保证径向密封的同时,动环装配后保证能在轴上灵活移动(把动环压向弹簧能自由地弹回来)。
(2)密封面润滑油量不足引起干摩擦或拉毛密封端面。
对策:油室腔内润滑油面高度应加到高于动、静环密封面。
(3)转子周期性振动。原因是定子与上、下端盖未对中或叶轮和主轴不平衡,汽蚀或轴承损坏(磨损),这种情况会缩短密封寿命和产生渗漏。
对策:可根据维修标准来纠正上述问题。
2、小型潜污泵机封渗漏引起的磨轴现象
(1)715kW以下小泵机封失效常常产生磨轴,磨轴位置主要有以下几个:动环辅助密封圈处、静环位置、少数弹簧有磨轴现象。
(2)耐腐蚀泵磨轴的主要原因:①BIA型双端面机械密封,反压状态是不良的工作状态,介质中的颗粒、杂质很容易进入密封面,使密封失效。②磨轴的主要件为橡胶波纹管,且是由于上端密封面处于不良润滑状态,动静环之间的摩擦力矩大于橡胶波纹管与轴之间的传递转矩,发生相对转动。③动、静环辅助密封由于受到污水中的弱酸、弱碱的腐蚀,橡胶件已无弹性。有的已腐烂,失去了应有的功能,产生了磨轴的现象。
(3)为解决以上问题,现采取如下措施:①保证下端盖、油室的清洁度,对不清洁的润滑油禁止装配。②机封油室腔内油面线应高于动静环密封面。③根据不同的使用介质选用不同结构的机封。对高扬程泵应重新设计机封结构,对腐蚀性介质橡胶应选用耐弱酸、弱碱的氟橡胶。机封静环应加防转销。
二、由于压力产生的渗漏
(1)高压和压力波造成的机械密封渗漏由于耐腐蚀泵弹簧比压力及总比压设计过大和密封腔内压力超过3MPa时,会使密封端面比压过大,液膜难以形成,密封端面磨损严重,发热量增多,造成密封面热变形。
对策:在装配机封时,弹簧压缩量一定要按规定进行,不允许有过大或过小的现象,高压条件下的机械密封应采取措施。为使端面受力合理,尽量减小变形,可采用硬质合金、陶瓷等耐压强度高的材料,并加强冷却的润滑措施,选用可*的传动方式,如键、销等。
(2)真空状态运行造成的机械密封渗漏耐腐蚀泵在起动、停机过程中,由于泵进口堵塞,抽送介质中含有气体等原因,有可能使密封腔出现负压,密封腔内若是负压,会引起密封端面干摩擦,内装式机械密封会产生漏气(水)现象,真空密封与正压密封的不同点在于密封对象的方向性差异,而且机械密封也有其某一方向的适应性。
对策:采用双端面机械密封,这样有助于改善润滑条件,提高密封性能。
三、由于介质引起的渗漏
(1)大多数潜污泵机械密封拆解后,静环和动环的辅助密封件无弹性,有的已经腐烂,造成了机封的大量渗漏甚至有磨轴的现象。由于高温、污水中的弱酸、弱碱对静环和动环辅助橡胶密封件的腐蚀作用,造成了机械渗漏过大,动、静环橡胶密封圈材料为丁腈―40,不耐高温,不耐酸碱,当污水为酸性碱性时易腐蚀。
对策:对腐蚀性介质,橡胶件应选用耐高温、耐弱酸、弱碱的氟橡胶。
(2)固体颗粒杂质引起的机械密封渗漏如果固体颗粒进入密封端面,将会划伤或加快密封端面的磨损,水垢和油污在轴(套)表面的堆积速度超过摩擦副的磨损速度,致使动环不能补偿磨耗位移,硬对硬摩擦副的运转寿命要比硬对石墨摩擦副的长,因为固体颗粒会嵌入石墨密封环的密封面内。
对策:在固体颗粒容易进入的位置应选用碳化钨对碳化钨摩擦副的机械密封。
四、因其他问题引起的机械密封渗漏
耐腐蚀泵机械密封中还存在设计、选择、安装等不够合理的地方。
(1)弹簧压缩量一定要按规定进行,不允许有过大或过小的现象,误差±2mm,压缩量过大增加端面比压,摩擦热量过多,造成密封面热变形和加速端面磨损,压缩量过小动静环端面比压不足,则不能密封。
(2)安装动环密封圈的轴(或轴套)端面及安装静环密封圈的密封压盖(或壳体)的端面应倒角并修光,以免装配时碰伤动静环密封圈。