亦称高温干馏或炼焦。煤干馏方法之一,指以煤为原料,在隔绝空气条件下在焦炉中加热(900~1100℃)以制取焦炭的过程。最重要的特性是要求具有一定的粘结性,即粉状煤料加热时能软化、熔融,经过胶质状态,使煤粒彼此结合,固化成坚实的块状焦。
焦化_焦化 -焦化
焦化_焦化 -正文
亦称高温干馏或炼焦。煤干馏方法之一,指以煤为原料,在隔绝空气条件下在焦炉中加热(900~1100℃)以制取焦炭的过程。焦化过程除获得产品焦炭外,还副产焦炉煤气和多种炼焦化学产品。每吨干配煤可得焦炭约0.7~0.8t,焦炉煤气300~350m,炼焦化学产品约0.03~0.06t。
沿革煤焦化技术大规模用于工业生产始于18世纪。当时,传统的木炭炼铁因木材日益紧缺而受到限制,需要寻找代用燃料。1735年,在英国用烟煤制得的焦炭炼铁,这标志着焦化工业发展的开始。此后,焦化技术不断变革,从原始的成堆干馏,经过窑炉、倒焰炉、废热式焦炉、蓄热式焦炉等各发展阶段,形成了现代的炼焦过程。
炼焦用煤炼焦用煤最重要的特性是要求具有一定的粘结性,即粉状煤料加热时能软化、熔融,经过胶质状态,使煤粒彼此结合,固化成坚实的块状焦。此外,要求灰分、硫分杂质含量低。按中国煤分类方案,炼焦用煤主要的牌号是焦煤、肥煤、气煤和瘦煤(见煤化学)。其中只有焦煤能单独炼成质量较好的焦炭,但这类煤的贮量很少。为扩大炼焦用煤来源和改善焦炭质量,通常采用配煤炼焦。即根据各牌号煤的结焦特性,通过配煤实验,找到合适的配合比例,炼出合格的焦炭。除了配煤炼焦以外,在炼焦工艺上采用捣固炼焦,配型煤炼焦以及仍在继续改进的干燥、预热煤料直接入炉的工艺,这些提高入炉煤料堆密度的方法,都能有效地增加弱粘煤的用量。此外,在较瘦煤料中配入粘结剂,在较肥的煤料中配入瘦化剂,对于非炼焦用煤则先制成型煤、再进行单独焦化等,均可获得有一定强度的块焦型焦。
成焦过程煤由常温经过干馏到焦炭成熟,要经历煤干燥和预热、形成胶质体、缩合结焦等阶段。煤在炭化室中成焦过程实际是成层结焦,因为热量是从两侧炉墙供给,而煤的热导率又低,平行于炉墙的各层煤料之间有较大的温度差。这样,在同一时间内,离炉墙不同距离的各层煤料处于不同的成焦阶段,靠近炉墙的煤层先成焦,而后一层层地向炭化室轴线中心推移,当焦炭层从两侧扩展到炭化室中心并会合时,成焦过程即结束,整个成焦时间大约13~18h。
近年来,已提出了一种新的成焦理论,即所谓中间相理论。它是从光学物理的角度研究成焦过程,认为在煤热解的胶质体液态中存在一种液晶(中间相)结构,而这种液晶是来源于镜煤,并与焦炭的结构有密切的关系。
焦化_焦化 -炼焦化学产品
有煤焦油、粗苯、氨等化学产品。
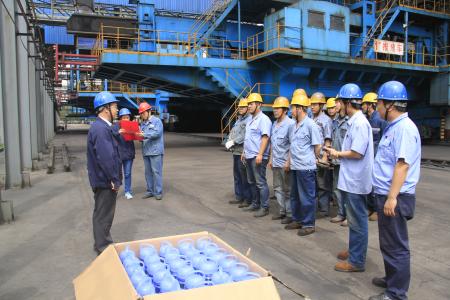
各种炼焦化学品的产率与原料煤质和焦化条件有关,每吨干煤可得煤焦油25~45kg,粗苯7~14kg,氨2.4~4.5kg。炼焦化学品的回收流程(见图)一般包括煤气与焦油的分离、氨吸收和粗苯回收几部分。
由焦炉导出的粗煤气经喷水激冷后,在初冷器中冷凝出煤焦油和氨水,经分离槽分离,氨水入蒸氨塔。蒸出的氨和气体中未溶于水的氨一并在饱和器中与硫酸进行中和反应生成硫酸铵。由饱和器来的气体,经酸分离器除酸及终冷塔降温后,入苯吸收塔用洗油吸收气体中的粗苯,洗油中的粗苯在脱苯塔蒸出。脱出粗苯后的气体即焦炉煤气,经脱除有害的硫化物等后,作为燃料煤气或化工原料。(见煤干馏)
参考书目
姚昭章主编:《炼焦学》,冶金工业出版社,北京,1983。
焦化_焦化 -存在问题
企业数量众多,规模小,布局分散,产业集中度低,技术装备整体落后,排放污染重、化工产品回收和综合利用与集中加工不足,精深加工技术落后,产品品种少,质量水平低,产能过剩、经济效益不高。
焦化_焦化 -延迟工艺
延迟焦化与热裂化相似,只是在短时间内加热到焦化反应所需温度,控制原料在炉管中基本上不发生裂化反应,而延缓到专设的焦炭塔中进行裂化反应,“延迟焦化”也正是因此得名。
延迟焦化装置主要由8个部分组成:
⑴焦化部分,主要设备是加热炉和焦炭塔。有一炉两塔、两炉四塔,也有与其它装置直接联合的。⑵分馏部分,主要设备是分馏塔。
⑶焦化气体回收和脱硫,主要设备是吸收解吸塔,稳定塔,再吸收塔等。
⑷水力除焦部分。
⑸焦炭的脱水和储运。
⑹吹气放空系统。
⑺蒸汽发生部分。
⑻焦炭焙烧部分。国内选定炉出口温度为495――500℃,焦炭塔顶压力为0.15――0.2Mpa。
焦化_焦化 -焦化原料
延迟焦化原料可以是重油、渣油、甚至是沥青。延迟焦化产物分为气体、汽油、柴油、蜡油和焦炭。对于国产渣油,其气体收率为7.0――10%,粗汽油收率为8.2――16.0%,柴油收率为22.0――28.66%,蜡油收率为23.0――33.0%,焦炭收率为15.0――24.6%,外甩油为1――3.0%。焦化汽油和焦化柴油是延迟焦化的主要产品,但其质量较差。焦化汽油的辛烷值很低,一般为51――64(MON),柴油的十六烷值较高,一般为50――58。但两种油品的烯烃含量高,硫、氮、氧等杂质含量高,安定性差,只能作半成品或中间产品,城经过精制处理后,才能作为汽油和柴油的调和组分。焦化蜡油由于含硫、氮化合物、胶质、残炭等含量高,是二次加工的劣质蜡油,目前通常掺炼到催化或加氢裂化作为原料。石油焦是延迟焦化过程的重要产品之一,根据质量不同可用做电极、冶金及燃料等。焦化气体经脱硫处理后可作为制氢原料或送燃料管网做燃料使用。
焦化_焦化 -焦化发展
正是由于延迟焦化的上述优点,使得延迟焦化在中国得到了迅速的发展,这主要是因为:
⑴延迟焦化是解决柴汽比供需矛盾的有效手段。这是由于中国原油普遍偏重,且含蜡量高,柴油的收率低,国内原油的柴油馏分收率比国外原油平均低5――7百分点。因此目前中国每年大约进口80×104t柴油,同时不得不出口30×104t汽油,以求国内供需平衡。其次是由于中国炼油企业二次加工均以催化裂化为主,柴汽比低(延迟焦化为1.94,催化裂化为0.56),因此发展延迟焦化是解决柴汽比供需矛盾,增产柴油的有效办法。⑵延迟焦化与加氢裂化相比,延迟焦化尽管存在轻质油产品安定性差、操作费用低(加工费约为加氢裂化操作费用的1/2――1/3),使其具有较强的竞争力。
由于延迟焦化具有投资少,操作费用低,转化深度高等优点,延迟焦化已发展成为渣油轻质化最主要的加工方法之一。因此,在目前中国资金紧张,轻油产品尤其是柴汽比供需矛盾突出的情况下,延迟焦化是解决这一矛盾的较理想的手段之一
焦化_焦化 -安全技术
1)生产特点
焦化厂一般由备煤、炼焦、回收、精苯、焦油、其他化学精制、化验和修理等车间组成。其中化验和修理车间为辅助生产车间。
备煤车间的任务是为炼焦车间及时供应合乎质量要求的配合煤。炼焦车间是焦化厂的主体车间。炼焦车间的生产流程是:装煤车从贮煤塔取煤后,运送到已推空的碳化室上部将煤装入碳化室,煤经高温干馏变成焦炭,并放出荒煤气由管道输往回收车间;用推焦机将焦炭从碳化室推出,经过拦焦车后落入熄焦车内送往熄焦塔熄焦;之后,从熄焦车卸入凉焦台,蒸发掉多余的水分和进一步降温,再经输送带送往筛焦炉分成各级焦炭。回收车间负责抽吸、冷却及吸收回收炼焦炉发生的荒煤气中的各种初级产品。
2)焦化安全生产技术及事故预防措施
⑴防火防爆。一切防火防爆措施都是为了防止生产可燃(爆炸)性混合物或防止产生和隔离足够强度的活化能,以避免激发可燃性混合物发生燃烧、爆炸。为此,必须弄清可燃(爆炸)性混合物和活化能是如何产生的,以及防止其产生和互相接近的措施。
有些可燃(爆炸)性混合物的形成是难以避免的,如易燃液体贮槽上部空间就存在可燃(爆炸)性混合物。因此,在充装物料前,往贮槽内先充惰性气体(如氮),排出蒸气后才可避免上述现象发生。此外,选用浮顶式贮槽也可以避免产生可燃(爆炸)性混合物。其他非正常形成可燃(爆炸)性混合物的原因和预防措施如下:
⑵泄漏。泄漏是常见的产生可燃(爆炸)性混合物的原因。可燃气体、易燃液体和温度超过闪点的液体的泄漏,都会在漏出的区域或漏出的液面上产生可燃(爆炸)性混合物。造成泄漏的原因主要有两个:
一是设备、容器和管道本身存在漏洞或裂缝。有的是设备制造质量差,有的是长期失修、腐蚀造成的。所以,凡是加工、处理、生产或贮存可燃气体、易燃液体或温度超过闪点的可燃液体的设备、贮槽及管道,在投入使用之前必须经过验收合格。在使用过程中要定期检查其严密性和腐蚀情况。焦化厂的许多物料因含有腐蚀性介质,应特别注意设备的防腐处理,或采用防腐蚀的材料制造。
二是操作不当。相对地说,这类原因造成的泄漏事故比设备本身缺陷造成的要多些。由于疏忽或操作错误造成跑油、跑气事故很多。要预防这类事故的发生,除要求严格按标准化作业外,还必须采取防溢流措施。《焦化安全规程》规定,易燃、可燃液体贮槽区应设防火堤,防火堤内的容积不得小于贮槽地上部分总贮量的一半,且不得小于最大贮槽的地上部分的贮量。防火堤内的下水道通过防火堤处应设闸门。此闸门只有在放水时才打开,放完水即应关闭。
⑶放散。焦化厂许多设备都设有放散管,加工处理或贮存易燃、可燃物料的设备或贮槽,放散管放散的气(汽)体有的本身就是可燃(爆炸)性混合物,或放出后与空气混合成为可燃(爆炸)性混合物。《焦化安全规程》规定,各放散管应按所放散的气体、蒸气种类分别集中净化处理后方可放散。放散有毒、可燃气体的放散管出口应高出本设备及邻近建筑物4m以上。可燃气体排出口应设阻火器。
⑷防尘与防毒。煤尘主要产生在煤的装卸、运输以及破碎粉碎等过程中,主要产尘点为煤场、翻车机、受煤坑、输送带、转运站以及破碎、粉碎机等处。一般煤场采用喷洒覆盖剂或在装运过程中采取喷水等措施来降低粉尘的浓度。输送带及转运站主要依靠安设输送带通廓、局部或整体密闭防尘罩等来隔离和捕集煤尘。
破碎及粉碎设备等产尘点应加强密闭吸风,设置布袋除尘、湿式除尘、通风集尘等装置来降低煤尘浓度。
在焦化厂,一氧化碳存在于煤气中,特别是焦炉加热用的高炉煤气中的一氧化碳含量在30%左右。焦炉的地下室、烟道通廓煤气设备多,阀门启闭频繁,极易泄漏煤气。所以,必须对煤气设备定期进行检查,及时维护,烟道通廓的贫煤气阀应保证其处于负压状态。
为了防止硫化氢、氰化氢中毒,焦化厂应当设置脱硫、脱氰工艺设施。过去国内只有城市煤气才进行脱硫,冶金企业一般不脱硫。至于脱氰,一般只从部分终冷水或氨气中脱氰生产黄血盐。随着对污染严重性认识的提高,近年来,各焦化厂已开始重视煤气的脱硫脱氰问题。为了防止硫化氢和氰化氢中毒,蒸氨系统的放散管应设在有人操作的下风侧。
焦化_焦化 -危险因素
1从装置边生产边施工的主要内容分析危险因素
装置运行期间主要需完成的改造工程量为:新焦碳塔塔体、钢结构预制、安装;新加热炉钢结构预制、安装及加热炉的制作;新焦碳塔、加热炉部分管线的预制和安装;新增放空塔的安装;焦碳塔、加热炉及其他设备基础施工;新增换热器、空冷器的安装和配管;DN500、DN600管线的安装;泵区、分馏区部分管线、仪表槽盒的安装等。从施工内容分析主要存在的危险因素有:
1)碳塔、加热炉、放空塔、换热器、仪表槽盒安装时动火作业易引发火灾;
2)焦碳塔塔体、钢结构的安装、加热炉的制作、钢结构、管线的安装时上下交叉作业易发生设备、人员伤害;
3)碳塔塔体、管线、钢结构、加热炉的钢结构、管线、换热器、放空塔、DN500、DN600管线安装吊装作业,存在吊装危险及对周围设备和管线的损坏;
4)焦碳塔、加热炉及其他动设备基础土建施工地面开挖,装置通道出现沟、坑易造成人员伤害;
2从装置边生产边施工的周围环境分析危险因素
1)焦碳塔、加热炉的安装空间较小,安装高度大,最高达到了102m,吊装的重量大,最重达到了200t,同时东靠正在运行的炉――30l和塔――201,南侧紧邻装置的主马路,北边是高压泵房,西侧有焦池和沉降池。其施工的主要危险因素有:
①周围环境多为瓦斯、油气,一旦瓦斯泄漏或火星掉入沉降池,极易发生火灾爆炸事故;
②安装空间狭窄、施工交叉作业较多,易碰撞周围设备管线;
③焦碳塔及钢结构需动用500t大吊车吊装,吊装的高度和重量都较大,存在吊装危险及周围设备管线的损坏。
2)新增的放空塔南侧近邻气压机区,西侧靠近加热炉进料罐V-104,北侧有封油罐V-401。下方有运行地汽油泵B-111/112,紫油冲洗油泵B-113/114,封油泵B406/407。其施工地主要危险因素有:
①周围环境为汽油、柴油、瓦斯、油气及地漏和下水井,动火时易发生燃烧爆炸;
②吊装时有一根DN20的汽油线和DN50的风线进行处理,易破坏管线发生火灾。
③罐体吊装属大型设备吊装,存在吊装危险及对周围设备管线的损坏。
3)新增空冷器和换热器的安装在冷换区,高度从7m――22m,周围主要有换热器、管线、地漏和下水井以及汽油、柴油、油气。施工的主要危险因素有:
①地漏、地沟、下水井含油,汽油、柴油、油气的泄漏,施工动火易引燃;
②施工易碰撞周围设备管线。
4)DN500、DN600线以及仪表槽盒的安装,施工的区域多、面广,从加热炉到泵区、冷换区、气压机区,周围环境主要有机泵、管线、地漏、地沟、下水井,施工的主要危险因素有:
①地漏、地沟、下水井含油,施工动火易引燃;
②施工易碰撞周围设备管线;
③周围环境的油品、油气、瓦斯较多,施工动火易发生燃烧爆炸;
④施工的机具、设备、管架容易造成人员摔伤、碰伤等人身事故。
3从装置工艺、操作条件分析危险因素
延迟焦化是在高温条件下,热破坏加工渣油从而得到石油焦、汽油、柴油、蜡油和气体的二次加工装置。焦化过程是一种热分解和缩合的综合过程。装置属于高温(装置最高温度可达1000℃以上,介质温度最高500℃)、高压(最高压力3.8MPa),易燃、易爆的装置。装置所用原料为常减压的减压渣油,其自燃点为230――240℃,而装置的操作温度多在300℃以上,一旦泄漏极易发生火灾,生产的干气和汽油沸点和闪点都很低,与空气混合均能形成爆炸性混合气体,其爆炸极限分别为1.5%――15%(V/V)和1.4%――7.6%(V/V)。同时由于其产品柴油、蜡油的自燃点都低于装置的操作温度,极易发生火灾,存在较大危险。为了加大装置的处理量,装置实行单程+18h生焦,生产组织难度较大,操作变动频繁;同时设备运行时间较长,许多设备超负荷运行;尤其加热炉运行时间长,存在一定程度的结焦;受改造的影响,生产管理人员较少,部分设备带病运行。改造施工的危险因素有:燃烧爆炸对人员的伤害以及设备损坏、财产损失。
焦化_焦化 -行业发展现状
2014年上半年,全国规模以上焦化企业实现主营业务收入2614.46亿元,同比下降6.34%;盈亏相抵实现利润为-32.89亿元,同比下降420%;焦化企业的亏损面达53.04%,亏损企业合计亏损额99.67亿元。企业的生存与发展、生产经营陷入前所未有的困境。据国家统计局统计,1-6月全国累计生产焦炭2.3亿吨,同比下降1.1%;全国煤焦油产量约970万吨,粗(轻)苯产量约245万吨;焦炉煤气制甲醇约300万吨,相比2013年略有下降。
今年以来,焦炭价格持续下跌,出现了多年罕见的局面。2013年,焦炭平均价格为1396元/吨,其中最高价格为1632元/吨,最低价格为1260元/吨。1~6月份,焦炭平均价格为1122元/吨,其中最高价格为1268元/吨,最低价格为1069元/吨。焦炭平均价格同比下降274元/吨,下降幅度近20%;而部分地区焦炭价格最高下跌逾400元/吨。
《焦化行业深度评估及投资前景预测51report》分析认为,焦炭价格大幅下滑,既有炼焦煤价格下降的因素影响,更反映出国内焦炭市场需求疲软、产能严重过剩、定价机制不严谨的无序竞争状态。一些地区炼焦企业开工率较低、企业生产不稳定,对炼焦化工产品的生产和经营效益产生了很大影响;企业平均负债率高达77.8%、银行贷款难度加大等因素,使多数焦化企业生产经营陷入空前的困境。
目前影响焦化行业总体经济运行的原因,一方面是全球经济复苏仍在深刻调整之中,我国宏观经济运行反映出较为明显的下行压力,焦炭市场需求疲软,节能减排的刚性约束与日俱增。而另一方面则是焦化行业自身存在的问题,目前炼焦企业产能集中度偏低、规模偏小,产品同质化严重。尤其是煤焦油、苯精制等企业,加工规模小,产品质量不高,属低级粗加工层次,一些炼焦过程中独有的特种化工产品不能合理、有效地提取。