以往内高压成形装备不改变合模力,在初始合模时就施加了最大的合模力,对于大吨位内高压成形装备来说,需增加模具的体积才能避免模具变形和破坏,增加了模具成本。
内高压成形原理及过程
(1)成形原理
管材内高压成形技术通常用管坯作为原材料,通过对管坯型腔内施加高压液体压力,轴向施加载荷作用,使其在给定模具型腔内发生塑性变形,管壁与模具内表面贴合,从而得到所需形状零件的技术。
(2)成形过程
管材内高压成形过程如图2所示。模具由上模和下模组成。下模固定在工作台上,先将管坯弯曲到要求的形状,在成形工艺中成为预成形,由单独的一台油压机完成这一道工序,然后放人下模腔内,闭合压力机。
管的两端用左右冲头密封,同时施加适当的预推力。胀形用乳化液由b经右冲头内中间孔道,引人管坯腔内,管坯内气体经左冲头上部孔道由a排出,管坯内充满乳化液即完成冲液过程。接着将a孔封住,由b孔向管坯内充以高压。与此同时,左右冲头同步向内推进补料,这样在内压和轴向力联合作用下使管坯贴靠模具而成形。左右冲头推制到位,内压到一定值后,b孔停止供压,冲头后撤放掉乳化液,上模抬起,取出工件即可。
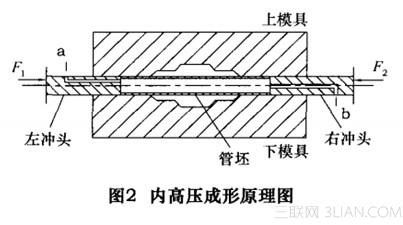
(3)可变合模力
以往内高压成形装备不改变合模力,在初始合模时就施加了最大的合模力,对于大吨位内高压成形装备来说,需增加模具的体积刁‘能避免模具变形和破坏,增加了模具成本。
因此本设备采用可变合模力技术,通过传感器检测管材内的压力和主缸内的压力,并根据内高压成形过程中管材内部的液体压力变化调整伺服阀动作,实现合模力可变,合模力跟随内压在成形过程中的变化见图3。
由于管材内的压力是逐渐建立起来的,并根据工艺要求按一定的加载曲线上升,采用可变合模力后,合模力平衡内压反力的部分随内压增大,使模具受到的压力保持在一个较低的水平,可避免模具体积过大,因此可降低模具成本,如图4所示。
由大天数控加工中心 http://www.hzdtsk.com 整理发表,转载请注明