虽然大规模和高水平的技术改造让瓦轴集团的装备水平无以匹敌,但是王路顺认为,除了硬件,企业要在市场立足必须依靠自主创新,设计、工艺和检测都要靠自己,靠别人的只能使企业流于低端的恶性竞争。
瓦轴集团提出实施“品种全、品质优、品牌响”的“三品”市场战略后,在提高产品的先进性、稳定性和可靠性上下苦功,以“生产一代,储备一代,研制一代,构思一代”的新产品滚动开发模式,开发具有自主知识产权的新产品。
瓦轴集团技术中心产品研发所王劲松说:“我们有近200人的研发团队,加上车间的技术人员,有近2000人的技术团队。集团所有的产品都是我们自己设计研发的,研发一直被看做集团的重中之重。”“十五”期间,集团共完成新产品开发3800种,改造老产品1100种,替代进口产品1200种,填补国内产品空白200多种;填补国内检测空白51项;获得国家专利81项;有41项成果获得国家和省市的技术进步奖项。2002年,瓦轴集团以EMQ轴承为代表的国际一流水平的电机轴承实现批量生产,创造了中国轴承史上的又一个新纪录,从2001年到2007年,瓦轴集团有13项成果成为“中国企业新纪录”。目前,瓦轴集团有16000种产品具有自主知识产权,平均每天研发出2种新产品。
建立大型检测试验中心的轴承企业寥寥无几,瓦轴集团对检测中心的投入之大在世界上也很少见,这是企业对产品负责的表现,也表明了瓦轴集团立足全球轴承市场的信心和决心。
瓦轴集团检测试验中心是集检测、试验、分析、研究、鉴定、评价为一体的轴承检测实验室。2004年3月,检测试验中心正式通过了国家实验室认可委员会的检测能力认可,标志着检测试验中心的检测能力和检测水平达到国内轴承行业领先水平。
2007年,以检测试验中心为建设主体的“大型重载精密轴承研发和试验平台建设”项目顺利通过国家发改委的验收。瓦轴集团技术中心检测试验中心陈澍说:“这个项目的建立使试验能力大幅度提高,目前我们每年可以进行300多个轴承规格的试验,是项目建设前的试验能力的5倍左右,可试验范围和试验能力都在全国轴承行业列第一位。”
由于检测实验能力的提高,可实验检测项目的增加和实验检测范围的扩大,改变了以往大部分产品设计完成后无法进行试验分析验证,只能根据用户在使用过程中反馈的情况进行产品设计改进的不利状况,一大批新产品在用户装机使用前都可以在公司的实验室内得到充分的实验验证,产品设计、工艺等部门可以依据实验验证的结果对设计、工艺进行优化,确保了产品在用户的装机质量,提高了瓦轴集团产品的声誉。
同时,瓦轴集团积极借助“外力”与大学、院所联合研发:与大连理工大学合作,进行产品设计CAD工程改造,极大地提高了产品设计效率,缩短了产品设计周期;与大连海事大学联合对瓦轴集团检测试验中心寿命试验的监测分析系统进行技术改进,轴承寿命试验实现了振动信号自动采集处理、自动监控,轴承损坏自动报警,提高了寿命试验的准确性;与西安交通大学签订技术合作协议,共同建立研发中心,实现“国内一流、国际先进”的目标。
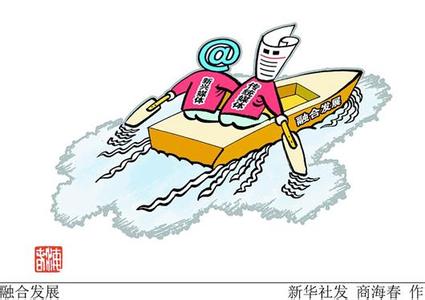
瓦轴集团技术中心是认定的国家级企业技术中心,负责整个集团的技术发展、产品开发研究、工艺工装设计、轴承装备的开发设计、产品的试验检验、信息服务、计算机开发应用、行业与企业以及科研项目管理等工作。
瓦轴集团技术中心在不断进步和完善的过程中,取得了中国轴承行业瞩目的成果,为中国轴承行业的技术进步做出了重大贡献,对瓦轴集团来讲,技术进步与技术创新所取得的成果也推动了产品的销售和公司利润的提高,技术中心近几年成功开发出一批具有高技术含量的轴承产品,以产品拉动市场,引领了中国轴承技术发展的方向,占领了高新轴承产品绝大部分市场。目前,瓦轴集团在风电系列轴承、轧机轴承、高精密机床轴承、高速铁路轴承等一系列高精尖轴承的市场中,全面实现国产化并为众多客户配套。
“现在,国家已把瓦轴集团确定为重大技术装备制造业配套轴承的生产基地。我们将通过对国家16个关键领域重大技术装备轴承技术改造项目的实施,不断加大研发的投入和研发的力度,为振兴民族装备制造业做出贡献。”王路顺满怀信心地说。