我国是家电制造大国,国内有众多的家电厂,产品不仅在国内销售,还有很多企业的产品出口到全球,并承接国外的制造订单。家电产品制造有共同的特点,那就是产品的各组成配件需要经由各分厂/车间进行生产,另有部分配件要由外部采购,最后再组装为成品。
我们以一个大型空调制造企业为例说明。首先要由几个分厂生产空调的配件,主要包括注塑成型、控制电路板生产、钣金加工等,另外,压缩机和电机要从外部采购。工厂的需求包括市场预测和外部订单两种。市场预测的需求以月为单位,客户订单的需求则精确给出日期,出口的订单因为要考虑交货船期因素,不能延迟。每个分厂负责自己的生产排程,配件厂的生产计划以总装厂的工作计划为订单,而总装厂的排程以分厂的生产排程为条件。
需求计划不等于生产计划,家电销售和制造是有淡季和旺季的,空调夏天是销售旺季,电视可能春节前是销售旺季,在销售旺季来临之间的几个月是生产的旺季,旺季和淡季的产量会相差数倍。在旺季,全部生产线开动、日夜加班都不能满足要求,而淡季可能需要停掉部分产线、工人部分时间休假或需要裁减员工。
过多的休假和加班对企业和员工都非常不利,企业的生产应该尽量连续而均匀。要达到这个目的,就需要对需求进行很好的规划,将需求转换为生产计划,确定什么时间应该生产什么产品,产量与工作时间如何安排。同时,也要考虑库存成本,避免库存过大,使生产与库存取得平衡,企业才能得到最大的利益。
要将市场预测/订单转换为生产计划,要考虑几个方面的问题:
1.员工的工作时间,在淡季要保证基本工作时间,旺季不超过最大允许加班时间。
2.主资源(生产线,机器设备)的最大生产能力,瓶颈资源是什么,使用瓶颈资源的产品配件要优先提前生产。
3.模具、贵重的测试仪器限制,这些虽是辅助资源,但采购的成本比较高,又需要较长的时间,因此要考虑这些资源的限制,资源比较紧张的配件要提前较长时间生产,例如,注塑厂对于模具数量有限的配件要提前生产作为库存
4.配件生产与总装的配合。总装厂要生产马上出货的订单,也要生产出一定的库存。各配件厂在淡季即要配合总装厂的装配计划,又要生产出一些库存的配件,用于旺季组装。
5.物料采购要按实际的生产计划,最好精确到天或周,不要以月为单位,以降低材料库存。
很多大型企业产品种类繁多,有的达到数百种,配件有几千种之多。各种产品交叉共用配件,不同产品的部分配件又会共用模治具等资源。对于这种企业,将长期需求转换为实际的生产任务,协调各分厂的生产计划和外购物料的采购计划,是一个致关重要而又复杂艰巨的工作。
传统的企业工作计划模式:
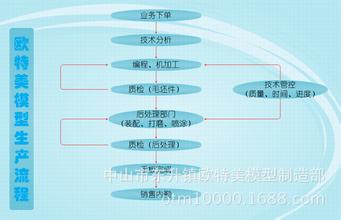
目前大部分企业的生产计划都是生管凭经验手工编制。首先总装厂的生管根据需求,查看各种配件的库存,考虑分厂的配件供货能力,决定近几天可以生产什么产品,并通知各分厂总装的生产计划。由于计算量的关系,详细排程一般不会超过一周,长期的计划只能估算。
在大部分工厂,由于模具的限制,影响总装排程的瓶颈是注塑成型,注塑每日可以供应的各种配件数量是有限的。分厂与总装的计划编制是互相依赖的关系,但是在人工作业模式下很难提供精确的数据供对方使用,结果就会造成一方面半成品的库存偏高,另一方面工厂为了完成出货产生很多紧急插单,生产线上的切换过多,影响了设备利用率,浪费资源。
从采购方面分析,例如压缩机的采购,空调厂是每月下一次订单,但是供应商会将月订单拆开成不同时间段的周订单,分多次交货。如果不给供应商明确的时间表,供应商的交货顺序并不能与工厂的生产计划顺序相匹配,如果交货延期,就有可能造成生产延误,另外,还会有些提前交货的材料要在仓库中放置很久。工厂为了避免欠料引起交货延期,通常采取高库存的策略,即提前下单。如果能够给供应商精确的日期,按照实际的生产需求日期交货,就可以大大降低库存,减少欠料概率。
从上面的分析可以看出,在人工编制计划的方式下,总装厂与各分厂的生产计划、物料采购计划很难完全配套,虽然各分厂都要生产库存,但是要生产什么、提前多久合适、生产多少、这些配件何时可以装配等都没有明确的数据。这样会造成很多问题,包括交货延迟多、库存水平偏高、计划的稳定性不好、紧急切换过多等。交货延期直接影响产品的市场销售,而过多的切换会造成资源的浪费(比如注塑机上的产品切换会造成材料和工时的浪费)。另外,提前生产过多的半成品,不止增加库存成本,半成品有可能因长时间不用造成报废。虽然企业很清楚这些问题的存在和损害,在当前这种计划模式下,这些缺陷是无法克服的。