单元式生产,是指在一条生产线或一个机器设备单元内,由一个人或几个人组成的团队连续进行多道工序操作,完成某一单项产品(整件或组件)组装的生产方式。
单元式生产方式是与传统的流水线生产方式相对应的。传统的流水线按不同工序先分割、后整合,作业中每个劳动者都被固定在生产线的某个环节上简单而快速地重复某个动作,以期达到高效率、高质量地完成产品生产。
单元式生产是准时生产(拉动式生产)的主要生产线布局方式。在机械行业、电子行业、服装行业等都广泛应用,其具体操作形式略有差异,下面就电子行业的单元式生产方式做简单介绍。
一、生产线布局
电子行业单元生产方式,大体上可以分为三种:
1、分工方式:将生产线设计成U型生产线或短的直线生产线,产品的转移靠工人用手来传递(而不是自动生产线),产品动人不动。
这种方式中包括一个特殊形式,员工围坐在一个圆形桌或方形桌周围。小型电子产品部件及完成品放在桌上,员工进行多道工序的操作。
2、巡回方式:将零件放在呈U型或椭圆形的架子上,若干名工人在绕着架子行走并完成所有加工工作,人动产品不动。
员工站在U型、椭圆型工作台的内侧。有点像我们部分人家里的厨房,“L型”“U型”,刷碗、切菜、炒菜、拿佐料,都在一挪身或一转身之间完成工序切换。而且便与人员之间互相支援。
3、单人方式:以作业者为核心配备零件和加工工具,采取类似以前的手工作坊的形式由一名工人完成所有的加工工作。
以上三种方式各有利弊,在实际操作中采取哪种方式,取决于作业者的熟练程度、在工具等方面的投资金额、产品的特性和尺寸大小等多项因素。
无论是一个人或是多个人完成整套工序,都需要员工是多能工。
二、多能工
多能工的目的是为了实现“少人化”。从生产线到生产单元的过程,是一条生产线分为多个生产单元的过程,这很容易造成每个单元的人员冗余或不足,每个人能干多个工序的多能工就成了必然的方向。
那么,如何培养多能工呢?
1、企业内定期调动:指以若干年或月为为周期的工作场所(主要指班、工段或部门)的变动,工作内容、所属关系、人事关系都发生变化。主要以基层管理人员为对象。
2、班内定期轮换:根据情况进行班内调动,所属关系、人事关系基本不变。
3、作业交替:根据实际情况以适当的周期(半天、一天)进行有计划的作业交替。
4、流动班长:根据实际情况以适当的周期(每周)选举一名工人为辅助班长,协助班长开展工作。
三、员工积极性
在佳能,有员工独立完成1000个零件相机的组装调试工作。有企业允许将员工的名字贴在自己亲手组装成的产品上。这些都有助于提高员工的成就感,并影响到效率和效果。
从工业工程的角度,由多能工在单元式生产线进行生产的效率应该不如流水线单技能生产,而且质量保证也更具挑战性和难度。但在实际工作中,单元式生产的效率很高,而且质量很好。原因是更符合人的本性,不枯燥乏味,可以满足员工的成就感。这种快乐而积极的心态导致员工更用心工作,效率更好、质量更好。
四、松下的案例
下面让我们看一下松下的一家工厂的单元生产方式:
“3名女工站在不到3米长的工作台前组成一个单元,手机所有的装配流程都由她们完成。第一名女工的工作是把一块电路板装进上盖板,装好摄像头,拧紧螺丝,完成后放到第二名女工的手边;第二名女工用联线把上下盖板连接起来,传给第三名女工,同时顺手帮她拿上一块电路板;第三名女工把电路板装进下盖板,拧好螺丝,手机装配完成。整个过程不到半分钟。这样一个单元一天可装配手机900部,而以前一条流水线需要14个人作业,每天只能生产1300部。所需零部件都堆放在工作台上,工人不用移动位置,这就减少了机器、半成品和人员移动的损耗。”
1998年,正是松下这种单元生产方式刺激了佳能,使得佳能大幅度转向单元生产方式,取得了巨大的成功。现在,单元生产方式在日本已经变成一种普遍的方式。
五、单元式生产的优点:
作业调度更容易:根据订单的变化和工人的技术水平,随时调整团队的数量和规模,灵活调整加工工序和生产数量。在佳能日本工厂,客户以前必须提前3个月交单,采用单元式生产方式以后,这一时间缩短为2个月。而且即使在2个星期前接到变更样品的通知,佳能也能很好地满足客户的要求。
运送距离更短:每个作业者装配后的制品被放在后工序作业者很方便拿到的地方,一般是右前方。因为搬运的距离完全在每个作业者手臂够到的方便的范围内,也就根本不再需要传送带来完成搬运。
库存量和库存占地更少:整条生产线紧密连在一起,不需要在制品库存。自动化仓库也变得不必要。自动生产线和自动仓库的拆除,使得生产作业占地更小。
考核更容易:个人工作绩效和工作态度的评定与过去相比更加容易。
六、单元式生产的注意点:
生产效率不稳定:单元式生产与流水线相比,每个工人负责的工序较多,每个工人的技能水平不同,工作速度容易变得不稳定。这就意味着生产线的速度决定于工人。月产5~10台的产品还不成问题,但当月产量达到1000台左右时,速度不稳定带来的影响就会很大。所以,生产速度的每日跟踪变得非常重要。
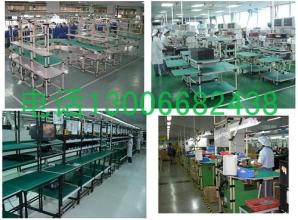
不良率较高:虽然单元式生产方式号称“更容易检验出不良品(因为更了解产品的全部以及更容易通知同单元的其他人员)”,但也不能一概而论,因为单元生产一个人干几个工序,员工自己没发现不良,产品就直接变成不良成品了。而对流水线方式,每人一个工序,即使自己没发现,后道工序发现的可能性也很大。这样单元生产对操作员自己的素质要求更高。