采访·撰文/刘扬
为了在中国实现2015年20万辆的销量目标,奥迪拿出了新武器——“全数字化”工厂。
9月19日,一汽大众新奥迪总装车间在长春正式投产,赶来参观的人们惊讶地发现:这个汽车工厂居然是个“玻璃房子”,在一汽大众一片封闭式的车间中格外显眼。
这并不是于秋涛最想要的效果,作为一汽大众奥迪平台高级经理,他是建设新车间的主要负责人。新总装车间正式投产日期比原定时间提早了半年,这期间还经历了4个月不能施工的东北封冻期,这对于秋涛和整个奥迪的销售团队来说,是一个更大的好消息。因为这可以尽快解决年初上市的奥迪A4L严重缺货问题,南方部分城市的消费者甚至要比以前多等一两个月才能提到车。
提车时间已经成为奥迪销量增长的羁绊之一。今年1~8月,奔驰、宝马的销售额增长率分别为50%和32%,奥迪的增长幅度仅为17.5%。
事实上,如何更快速地提升产能已经成为所有豪华汽车厂商的关键诉求。近日,华晨已与宝马商定在沈阳建设一个全新的第二工厂,年产能超过7.5万辆。北京奔驰也计划改造原有克莱斯勒车间,设计产能8万~10万辆。中国高端汽车厂商已经在产能上开始新一轮角力了。
尽管奥迪在销售绝对量上仍然领先于竞争对手,但如何保持这种优势,让巨额投资更快速地转化为销量,是奥迪接下来的重要任务。现在,它最新的武器就是这座“全数字化”工厂。
“数字化”工厂提前投产 减少“修修补补”省成本
两年前,一汽大众奥迪建设新总装车间的设想刚刚确立,于秋涛就开始一个人不断来往于中国和德国之间。
一位奥迪车间工程师告诉记者,在老总装车间,奥迪A4L、A6L和一汽大众捷达混线生产,一个工位摆放的零件已经非常繁杂了,如果明年即将上市的新车型Q5加入的话,不仅会让厂房拥挤不堪,也会影响工人的熟练程度,最终影响销量。
奥迪建设新总装车间的核心是,在提高产量满足消费者需求的同时,提升产品质量和品牌。
今年是奥迪进入中国第21个年头,也是奥迪品牌诞生百年。奥迪推出了A4L、A6L10年纪念版车型,还在原有品牌标识中增加了“突破科技,启迪未来”的理念。而设计、建设新总装车间正是这一理念的一个重要注脚。
统筹新总装车间对于秋涛来说也是一次不同寻常的经历。1993年开始,于秋涛就在一汽大众工作,参与建设一汽大众一厂,主管建设二厂。“最早建厂是走一步看一步地做,先把这个设备装完,然后看管路怎么走,电线怎么过来,母线槽怎么安排。”现在于秋涛建厂的“玩法”已经完全不同了。
在与德国奥迪所有的部门进行了近两个月的充分研讨后,2007年年底奥迪确定了新车间的设计方案。规划工程师采用3D数字工厂技术,模拟出整个车间的样子,甚至包括玻璃屋顶下的每一根网架的结构。
比如汽车生产中,吊具会吊起汽车,以不同的高度来适应工人对汽车不同方位的操作。以前建厂房时,会预先在房顶上设置吊具来控制吊点的强度,有时车间建好后发现强度富裕太多,没有利用价值;或者是吊点的强度不够,还要加强立柱支撑。这都会拖延生产、制造等一系列环节,而且费用也很高。
通过3D模拟技术后,这些费用昂贵的“修修补补”大大减少了,同时也缩短了从建厂到正式投产的时间。
一汽大众奥迪新车间把德国奥迪在德国本土、匈牙利以及比利时所有的建厂经验集纳于一身。同时,德国奥迪还通过中方了解了日系、韩系汽车品牌精益生产的经验,也包括一汽大众建设一厂、二厂多年总结出的适用于中国企业的生产模式。
“这是奥迪在全球最先进的总装车间,也将成为今后奥迪建厂的标杆。”于秋涛提起新总装车间颇为自豪。
全数字化车间全面运行后,每两分钟可以下线一辆奥迪A4L。不过由于生产线正处于磨合期,目前的下线时间为4分钟一辆。即使这样,每天下线的奥迪A4L也可达到200辆左右。
世界首创“物流超市” 每个螺栓数据保存15年
新总装车间让所有的参观者都大开眼界:整个车间让人感觉一尘不染,屋顶的漫反射玻璃均匀地洒下阳光,节省了2/3的照明能源,遍布车间的大型通风管道让车间的空气和室外一样清新。
不过,这其中世界首创的“物流超市”概念最让于秋涛得意。接近1.9万平方米的“物流超市”,集中了所有生产装配过程中所需的零部件,电子看板可以实时显示生产线各工位的零部件需求,并提示物流人员及时补充生产线零件。这个“超市”占据了新奥迪总装车间近1/3的地面面积。
这是奥迪第一次大规模地使用这一操作系统。在于秋涛和德国奥迪工作人员共同探讨生产方案时,形成了“物流超市”这一新理念。他们先在德国的生产线上做了一个小范围的实验,在几个工位中进行了模拟,总结经验后,在中国的新总装车间第一次进行了全面实施。
“超市”中存放了各种小尺寸零件的部分,物流人员只需通过扫描装配单,相对应的零部件储存盒上的指示灯就会自动亮起,可实现分拣“零错误”。高效的“物流超市”使车间生产线上的标准化供货零件储备周期只有两小时,生产效率大大提高。
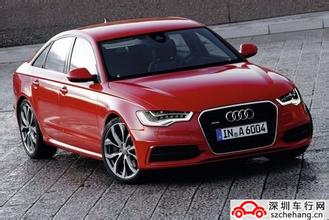
与以往不同的是,新车间生产汽车时,涉及到重要的安全性螺栓都采用了电控拧紧机,这大大减少了工人的劳动强度。比如拧紧一些螺栓需要100牛顿的力,一个工人一天下来胳膊可能就抬不起来了,而使用电动拧紧机只要把机器推到位就可以了。
“人是情绪化动物,可能因为不同的情绪随时随地影响工作,我们需要在设备上把人的情绪对质量的影响规避掉。”于秋涛说。拧紧机还会将每个螺栓的拧紧记录保存在中央服务器里,最低保存期为15年,可以对未来维修提供可追溯的数据。
新车间的“数字化”还体现在生产的质量控制上。于秋涛认为,奥迪新车间具有世界上最先进的设备。以前车轮定位的测量系统是3道激光束,但是现在奥迪汽车的轮胎从9英寸~16英寸都有,3道激光束已经不够精确了。新车间采用了64道激光束,可以测出整个轮子的结构,通过数据监测保证车轮定位在最精确值上。
新车间大大改善了工人们的生产环境,不过越来越多等候的车主让他们很难轻松下来。从9月中旬开始,他们很难有休息日了,而且工厂都是“10+8”两班倒生产制,等生产磨合得更充分,还有可能像原有的总装车间那样工作三班倒。
但是,新总装车间的生产还受制于生产线上游的焊装、喷漆车间的产能,因此年产10万辆的产能很难一下子释放出来。近期,奥迪工厂准备利用节假日改造焊装、喷漆等车间,提高产能。
“我会尽力将最新的产品推向中国市场,从而在2015年实现20万辆销量的目标。”一汽大众奥迪销售事业部总经理唐迈说,奥迪正在不断向人们展示争夺中国这个世界第一大市场的决心。