布鲁斯。汉德森是一家美国公司的董事长,他的公司主要生产空调系统和设备控制器,同时也是丰田公司的供应商。在为丰田公司生产设备的经历中,布鲁斯。汉德森逐渐成为丰田生产方式的拥护者,并写了一本名为《精益企业》的书来进行推广。在书里,他列出了企业推行丰田生产方式(又称“精益生产”)所面临的困难,其中第一条就是“高层管理者缺乏对精益企业的战略性了解”。
然而,布鲁斯。汉德森穷尽一书,也没有显明而有力的逻辑来说服那些高层管理者。精益生产,这一丰田公司制胜全球的法宝,虽然广为业界所知晓,而且众多研究者都熟知它的基本目标是降低成本,但管理者们往往会问,成本到底降在哪里?换言之,精益生产的成本效应如何体现?这一问题并未明朗,即使是精益生产的创立者大野耐一也未曾向大家详解背后的真意。
事实上,从管理会计学的角度重新审视精益生产,我们会发现长期以来潜藏的成本秘密,这一秘密足以触动更多的管理者更加深入地了解精益生产,进而加速其推广和普及。
节拍优先
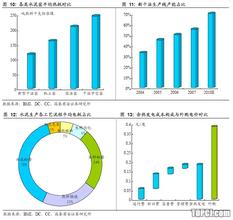
精益生产似乎并不是一个规律性的东西,有很多只可意会不可言传的地方。
一个直观的感受是,对生产节拍的控制是丰田公司一个铁的原则。所谓节拍(tact time),是指将生产时间细化到每一件产品之上。比如,如果月产量为4000辆车,作业时间为20天,每天两班制工作共16个小时,那么生产节拍即是每辆4.8分钟。
在丰田公司,构筑每辆4.8分钟的持续出货机制比什么都重要。为保证生产节拍,即使用人海战术,或者加大设备投资,或者在易产生次品的工序准备安全库存也在所不惜,而绝对不会妥协于成本的制约。如果丰田公司也将成本优先于节拍,恐怕就会变成“普通公司”了。丰田公司曾在它的一个制造厂制定了发动机的出品时间,早上开始铸铁,晚上就要组装为成型汽车,在院子里能开动起来。
在确保节拍的基础上,大野耐一提出了“不管是生产1辆还是1000辆,单位成本都要一样”这一与传统观点完全相悖的口号。人们通常认为,小批量生产的单件产品成本会较高,而且,如果工序与工序之间的换线时间不为零的话,这一看法似乎也不容辩驳。
实际上,若从资金的角度来考虑,大野耐一的口号是有其合理性的。假设两家汽车公司的月产量都是30辆,A公司每天生产1辆并出货,B公司以“汇总生产”的方式生产,最后第30天一次出货30辆。批量大的B公司因换线时间少,单位成本似乎更低。但在现金流和资金占用率方面,A公司显然有更大的优势,它每天都只需投入1辆汽车的材料费,而B公司在月初就要投入30辆车的材料费。此外,若B公司的月平均库存量是15辆(30辆/2),就要多准备15辆车的资金作为周转资金,而A公司可以拿这15辆车的资金再投资或用于其他用途。
这个资金节约策略的结果,就是实现了“只生产必要的东西”的订单式生产,并可将“零库存”理念付诸实施。丰田公司之所以对节拍如此重视,力保实施严格的即时化生产,就是因为它不一样的成本观。
纳入“阴成本”
21世纪的企业竞争是“人、钱、物、信息、时间”的竞争,尤其以“时间”的竞争为核心。
丰田公司很早就意识到了这一点,并将“时间”要素统筹考虑进生产系统中。在传统的会计理论里,一提到降低成本,人们想到的就是减少材料费,降低劳务费,因此,只有人或机器作业的加工时间才进入成本核算的视野。而在丰田公司,生产时间的范围则宽得多,从取得材料到制成产品,再到获得金钱收益,除了加工产品的时间,产品停滞的时间(包括产品在各个生产环节的停顿以及库存时间)也要纳入成本的考察范畴。
某种程度上,停滞时间与加工时间的关系类似道家的“阴阳”。许多企业在计算成本时,更多掐算的是加工时间“阳”,而忽视了等待、搬运、库存等“阴”的一面。这些看不见的时间都会造成浪费,影响反而更大,因此要以同等态度对待看得见的时间和看不见的时间。
之所以将产品停滞时间也纳入成本考察范畴,这是因为在财务学上“货币有时间价值”,它跟产品是否加工没有关系。简单来说,产品只要一停滞就会占用资金,占用资金就会带来损失,这就是浪费的源头。在精益的世界里,单价乘以数量的的二元成本观不能真正反映成本的构成,只有综合考虑生产时间的三元成本观,才能反映成本的实际情况。
可以假设两种情形。一种情形是,一天生产出一件产品,第二天回收货款;另一种情形是,一天生产出一件产品,在仓库里存放99天,第100天后回收货款。按照传统的会计观,两者的成本相等。但实际上,传统的成本核算法存在一个致命的缺陷,因为后一种方式丧失了将投入的材料款在99天里反复活用的“利生利”的机会。这个“机会费用”, 在财务学领域里是要考虑进去的,因为即使是同一金额,进出账的时间不同,市场价也会不同。企业应当意识到,忽视“机会费用”会带来损失。
另一方面,对应“机会费用”,推行精益生产还会有“机会利润”:企业通过缩短生产时间,将多余的人、机器、空间资源找出来,在不增加固定费用的情况下接受追加的订单。这也正是20世纪70年代丰田公司在美国市场取得巨大胜利的最为强大的武器。
引入“货币的时间价值”这一概念后,大野的“生产过剩是最大的浪费”、“待工的时候就站着”这些迥异于传统会计理论的论断就不难理解了,他的“经济低成长期,过多生产就是罪恶”的名言也不再显得突兀,反而透出思辨的力量。
生产过剩是最大的浪费
大野耐一曾经警示:“如果对有余力的作业者或者富余的生产线置之不理,一定会多做一些工作,但这样做,许多浪费就会隐藏起来,也就是说,过多的生产就会产生无法计数的浪费。”时刻谨记这一警示是必要的,但是到底存在哪些浪费?从英国的丰田系零部件公司得知,当工人们问起“因为闲着待工所以把下一步要做的工作先给做了,为什么不好”时,管理者往往哑口无言。很多时候,丰田公司内部的人都很难说清这中间的道理。
其实,这些浪费都与“货币的时间价值”有关,它们之间是实际损失和机会损失的连锁反应。首先,如果不是“待工时就站着”,“有余力的作业者或者富余的生产线”就会生产出不需要的库存,就需要这部分材料的进货资金。此外,为了缩短换线时间把产品批量加大到所谓的“经济型”,也要提前投下一部分材料款。批量加大后,机器加工的时间也会变长,真正急需的产品却迟迟出不来,因此需要进行额外的生产进度管理,而这会产生多余的管理费用。生产过剩还要增加仓管、防锈等保管费用,如果竞争对手的新产品上市,库存就会陈旧,商品一旦滞销,全部相关成本都将难以收回。还有,如果批量生产中有次品,就不能回收全部成本,进行修补还要再追加支出。最后,为了填补以上发生的全部损失,还需要一定的流动资金,这又是一项资金成本。因此,生产过剩实质上是一种“亏损生亏损”的形式,说它是七大浪费之首(其余六项是指等待、搬运、不良品、动作、加工、库存的浪费),一点也不为过。
在现实中,要让企业家们普遍认同“生产过剩是最大的浪费”其实存在一定的困难。因为在一般的企业,所有的间接制造费用都要分摊到产品,分摊一般以作业时间为标准。如果作业时间不充分,就会出现分摊不足,单件产品的成本看上去更高,相应的收益也会减少,而只有完全作业,才会有相对好的成本核算。因此,这些企业如果采用精益生产,在由按计划生产转为按订单生产的会计年度,利润会出现大幅度的下降。
但是,要实施精益生产,就要遥望未来,不能只顾及一时一地的得失,即使最初账面利润会下降,只要坚持下去,现金流就会改善,再过一段时间利润情况也会变好。
重视潜在利润
“生产过剩是最大的浪费”昭示了企业的一种长远意识,“当前利润”和“潜在利润”(即获取将来利润的能力)到底哪个更重要?似乎应该明确地选择后者。因为忽视未来的代价是巨大的,就比如整个社会如果只重视当前利润而疏于人事安排,在一代能工巧匠退休后,技术传承就会面临危机。道理虽然如此简单,很多企业却还是只能看到眼前的利润。
事实上,在丰田公司内部,也存在着两种经营阵容。一种是“自己好,让下任总经理也好”,另一种则主张“在自己的任期内,只要利润不下降就可以了”。前者优先考虑潜在利润,后者优先考虑当前利润。由于实施精益生产,相比其他公司,丰田内部重视潜在利润的经营者比较多。
通过对丰田、本田、日产三家汽车企业的财务资料进行分析,可以发现重视潜在利润的价值所在。2001~2006年,本田的毛利率比丰田和日产高出10%以上(丰田和日产差不多),总资产利润率也高于丰田和日产,但因为库存资产的周转天数比丰田多10天,比日产多1周,其潜在利润(现金流/库存资产)值,反而大大低于丰田和日产。
由于大库存和批量生产的缘故,本田和其他企业一样,交出了一份漂亮的当前利润报表,但其资金利用率却在下降。这种通过牺牲资金周转率来增加利润的做法,在经济持续增长的情况下是有效的,但到了经济衰退期就经不起考验了。
潜在利润将利润概念和生产时间概念有机地统一在一起。重视潜在利润意味着企业在会计观方面要具备一种复合思维:为了长远目标,应该使库存越少越好,而不是当前利润越多越好。上述三家汽车企业的财务资料证明:如果库存资产的增加额超过了销售额的总利润,潜在利润就会遭受损失。
由此,我们不难理解为什么丰田公司要在新世纪引进“大幅度改善”、“零不良”等突破极限的概念了。诸如变革材料、聘任临时工为正式工这样的措施,效果可能并不会立刻在利润上得到反映,但这是在积蓄潜在利润。
一句话,精益生产不是一个简单的生产方式,它是企业经营管理的一套理念和方法,需要公司高层、财务和相关部门有效地融合与协调,各生产部门间的相互支持与沟通,以一个整体来推进。由于精益生产强调领导力的自上而下,只有管理者对精益生产的成本观有深刻的理解,对潜在利润充分重视,这一经典的生产方式在非精益的文化圈里才有可能取得成功。
[本文由刘铮铮根据作者论文整理。]
河田信(Kawada Makoto)
日本名城大学经营学部教授、经济学博士,名城流程管理研究所董事长,日本最受欢迎的专家顾问之一,长期从事管理会计、丰田系统与JIT管理会计、TPS的海外可移植性以及制造企业经营系统再设计等方面的研究。