1.石油钻井用DQ70齿轮箱输出轴 石油钻井用DQ70齿轮箱输出轴及相关推力轴承工作于春晓油田。断时转速90rpm,工作扭矩15~20KN-m,出厂约4年后于2011年9月29日下午断裂。断裂位于轴Φ270/Ф520台阶圆角R1处。相关部位的推力轴承静盘(位于动盘下方)有约3/4滚道面积,严重剥落,其余1/4磨损。共计21只滚子,表面均产生严重磨损。 1.1 轴。轴所用锻件的材料为40CrNiMo,进所时光谱结果符合相关标准。锻件该部位尺寸约Φ540左右,粗车后调质处理。精加工,磨削后装配。Φ520端面垂直度0.03,同心度0.02,R1挖入Φ520内。由于有轴向静拉应力(钻柱自重造成),断口并未产生严重的挤压磨损,应力水平略高于轴疲劳限。单纯轴开裂后,在裂纹深达10%内,对刚度影响较小,相应应力有所释放,并不加剧振动。相反垂直安装状态时会使运行变得平稳些,裂纹扩展直到断裂前,直到动平衡,不再把过大钻柱的振动、弯曲力矩等传到推力轴承上。有利于保护推力轴承。 1.2 轴承。轴承的主要失效形式及分析:轴承制造缺陷软点多发于拐角液流不畅处,油气泡造成,对平面轴承可能性极小。如果是磨削裂纹多为表面较大面积(磨削条件差)网状裂纹,很浅,造成早期剥落,轴承寿命不会如此长,且动盘并未损坏。疑点是一批或一套轴承为何单定盘严重剥落,如果是硬度偏低时越向内越低应在表层下有碾压形态。未见这些现象说明不应是制造问题。这只轴承符合轴承的破坏规律;因为轴承往往是内圈旋转,外圈破坏;外圈旋转、内圈破坏。加工及安装中必须保证每个滚子和定盘接触的锥线V=0(要求随时随地)。 2 受力分析 钻柱的设计分析:由于地下工况复杂,目前仍沿用静强度设计,设计钻压W=5T,安全系数为1.2。W计=6T,FP=450-6=444(T),钻柱的安全系数取1.3 ,FP计=444×1.3=577(T),轴的静拉力 可见安全系数偏低,当叠加交变附加剪应力时,平均应力作用略有变化。单独作用的安全系数比正应力为高。合成的综合安全系数略有变化。 4.分析结果 1)轴为弯扭复合疲劳断裂,裂纹源位于Ф270/Ф520过渡圆角R1内,轴上圆角R1过小,会较大降低轴的疲劳强度(有效应力系数最高可达5),造成轴早期断裂。经两个不同扩展区后断裂,终断区相对较小,表明应力水平不高,破坏周期属高周疲劳破坏。轴的静态安全系数在工作载荷下远高于钻杆,说明轴的断裂是由附加的动载荷形成的,而且轴承所能承受静载荷约2000吨,其安全裕度4倍以上,正常条件是不应产生这种破坏,破坏本身显示其抗接触应力能力降低,表明有附加载荷,破坏指向额外负荷。 2)经过检查表明,轴承定盘至少经两次安装或调整,留下两组支撑盘安装螺钉头弓形的痕迹,两组圆周相距约5~10o,其相邻两个的大小差异显示,不是运转中形成的。A组的大小不均,远比B组大,而B组比A组挤压重,显然A组“支撑”时偏心大,B组支撑不平大,如图3。支撑不平是造成事故的主要原因。还有该轴承定盘采用的侧向不定位支撑方式,相对较大偶然过负荷难保不偏,这是设计上的弱点和难点,完全侧向固定的刚性支撑难于适应可能侧向微动,加大了冲击。 3)较大浪涌、风载及洋流都可能产生偶然过负荷,而钻井(直井)偏斜是必然动负荷,这些因素又加剧了两者的疲劳破坏。
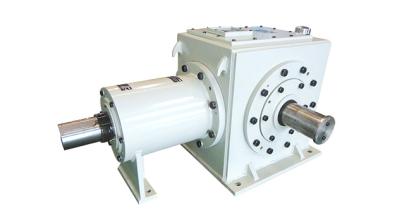
5.改进意见 加大Ф270/Ф520过渡圆角到R6-8,其轴承内圆角加大到R10。这样可使轴有效应力集中系数成倍下降大约到2.5—3。成倍提高了轴的疲劳强度,提高了可靠度;圆角采用滚压也可成倍提高疲劳寿命,但其位置及工艺应试验确定;推力轴承的支撑方式建议对推力轴承定盘做适当限位,但不固定;安装时保证螺钉头不露头避免支撑不平。