本年表现出众的制造企业有一个共同之处:为了应对危机,它们都彻底改变了生产方式。Autoliv 公司为了抵御气囊制造业强劲的竞争对手,改造了生产流程;生物技术巨头安进公司为了对付急剧上升的药品需求,设计出新的解决办法;雷神公司为了满足对武器装备的需要,将导弹产量翻了两番。
Autoliv 公司
学习精益方法,坚守精益之道,强化精益生产
1998 年 4 月,丰田汽车公司(Toyota Motor Corp.)的原田节(Takashi Harada)来到 Autoliv 公司的气囊模块生产厂,对工厂的生产情况做了快速考察。这位日本生产专家向生产主管比尔8226;韦伯(Bill Webb)提了一个问题:“按 10 分制算,这个工厂能得几分?”这个问题令韦伯陷入沉思。Autoliv 是汽车气囊制造业的龙头老大,占有绝大部分市场份额,丰田也是它的一大客户。Autoliv 的生产系统是在线性自动生产线上组装安全气囊模块,虽说可能还有待改进,但公司还是很成功的。“3 分?”韦伯不确定地说。他态度谦逊,有意在他的新导师面前低估分数。原田节回答:“应该到不了 3 分吧?”
于是,Autoliv(总部位于美国犹他州奥格登市)开始学习存在大量改进余地的丰田生产系统。公司建立了征求和落实员工建议的制度,发挥职工队伍的创造力,以促进效率和安全性的提高。在韦伯负责的库存管理和物流业务上,公司制定了拉式系统,可随时按照需求更换装配线上的零部件。当然,这一切并不是什么新鲜的东西。丰田公司一直在实行和传授看板库存管理、零部件及时交付和精益生产等方法,这已经有十年了。但是,要学起来并不容易。Autoliv 过去曾独立做过一些改变,但效果并没有像预期的那么明显。由于生产出的残品数量日渐增多,Autoliv 接受了丰田的帮助。双方的合作取得了成功。去年,犹他州立大学授予 Autoliv“新乡制造业卓越奖”。
Autoliv 原名莫顿汽车安全公司(Morton Automotive Safety),创办于 1956 年。它开发出了技术含量很高的充气气囊发火装置,成为气囊制造业早期的领头羊(1996 年,该公司为瑞典的安全带伸缩装置和安全限制系统的领先企业 Autoliv AB 所收购)。但是,竞争对手追了上来。Autoliv 迫于汽车制造厂家客户要求降价的压力,曾大幅削减成本以维持利润。
在迫不得已要提高利润之前,Autoliv 没有动机长期提高生产力,生产效率因而降低。例如,韦伯的库存里有价值 2,300 万美元的零部件,相当于 7-10 天的用量。这些零部件存放在大库房里,由自动引导车(AGV)调度,但运作起来并不灵活方便。后来,采用叉车代替自动引导车。韦伯把堆积如山的库存推到装配间,但他从未确切地知道这些库存什么时候会用得上,有时候收工后又把它们拉回到仓库里。有一天,原田节对韦伯说:“Autoliv 一定很富有,你有许多哪都用不上的材料。”
在原田节的指导下,韦伯制定了向生产车间运送零部件的规则,改用一种叫“周转箱”的小塑料箱来代替大板条箱,用高尔夫车一样大小的小拖板车取代巨大的叉车。这就意味著拖板车操作员要多跑几趟,须在 45 分钟内搬运 55 个周转箱,与生产更好地保持了同步。韦伯还重新布置了库存房间,使之切合生产车间的情况。后来,他又开发出自动跟踪零部件使用情况的软件。仓库一收到数据,补货订单便会被自动地发送给各个生产单元,并同时转送给厂外供应商,让他们发货。拖板车操作员每隔 24 分钟送货一次,每天送货 36 趟。这些次数的确定不是随意的,是为了保证灵活和便于分割。
在做了这些原田节极力主张的变革后,韦伯发现他原来的库存量太大了。他把库存减少了一半,这让会计很高兴。工厂经理马克8226;詹金斯(Mark Jenkins)说:“我们做了这些变革后,就不再订购零部件了,而是直接把现金打入银行。”
如今,走进 Autoliv 这个 3,252 万平方米的厂房,你会感到就像走进了一座钟表,总是能听到滴答滴答的声音。88 个紧凑的 U 型生产单元已经取代了主车间的原有装配线,每个生产单元都包括一组工作站,配有少量工人。工人在拧紧螺丝钉后,检查一下成品件,登记入册,然后转交给下一位同事打上标签,放进货箱。接著,有人会把货箱搬走。这些单元生产的产品包括司机气囊、乘客气囊和防侧撞缓冲气囊,在过去 3 年里,它们的销售量每年增加 50%。
每隔 24 分钟,广播系统就会高声播放 70 年代的摇滚乐队 Steam 的歌曲《Na, na, na, hey, hey, hey, goodbye》,表示换工的时间到了。每人依次轮转到下一岗,装载周转箱的拖板车嘟嘟地鸣叫两声,轰鸣著驶出库房。
在工厂中实施及时配送只是其中一项工作。随后,Autoliv 还得说服供应商也要跟著他们改变,有些供应商离 Autoliv 有 2,414 公里之遥。Autoliv 在印第安纳州建了一个转运站,每天 7 次接收东部供应商送来的货物,再用拖车送往奥格登,每辆拖车的载货量都相同。拖车的抵达时间均匀地隔开,每 72 分钟抵达一辆,像钟表一样准时,总是在相同时候按相同的次序送来相同的货物。对于抵达的每辆货车,有 3 台拖板车负责接货并转送到工厂车间。Autoliv 工厂只保持两天生产所需的库存。
现在,公司继续对其“Autoliv 生产系统”进行改造。每百万件模件中残品的数量急剧下降,从 1998 年的 1,100 多件减少到去年的仅 16 件。新乡奖负责人罗丝 罗布逊(Ross Robson)说:“他们的工厂现在比世界上任何一家工厂都不差。”去年,Autoliv 营业收入达 53 亿美元,实现利润 10 亿美元。
韦伯从丰田学到的经验之一是精益生产之路没有尽头。2001 年,在离开 Autoliv 工厂返回日本之前,原田节再次向韦伯提出了他的问题:“这个模块厂能打几分?”韦伯回答说:“现在该有 3 分了吧?”“不,现在它是 0 分,”原田节说。只要相信改进是无止境的,就总能找到提高的余地。
安进公司 Amgen
要应对药品需求的急剧上升,就必须大幅提高蛋白质产量
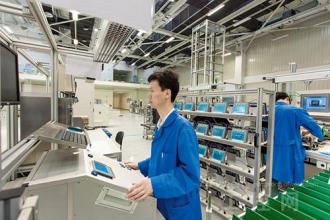
这不是火箭科学,但比火箭科学竟然还要复杂。安进公司重量级的重组蛋白质药物 Enbrel 专治类风湿性关节炎,去年销售额高达 13 亿美元。生产该药所需的生物学专业知识和技术造就了全世界最复杂的生产流程之一。眼下,安进在其位于罗得岛西格林威治的工厂里采用了这种极为先进的工艺流程。不仅如此,它还对其加以改进,准备在已经破土动工、将于明年投产的新工厂中使用。 2002 年,安进收购了 nbrel 的生产商 Immunex 公司。当时,有 4 万名病人正等著用这种药物,但 Immunex 生产这种药物的工厂尚未完工。安进不得不接管生产任务,迅速将 Enbrel 投放美国市场。为此,它要将破旧的罗得岛生物实验室改造成现代化的蛋白质生产厂。在短短四个月内,它就对这家名为 BioNow 的工厂进行了改造,并且得到了美国食品药物管理局的批准投入运营。BioNow 还没有完全达产,安进公司就利用从 BioNow 得来的经验,在 BioNow 旁边建设另一家新厂,取名 BioNext。安进有 1.3 万名员工,营业收入高达 100 亿美元,是世界上最大的生物技术公司。但对它来说,这仍然是一项艰巨的任务。
对安进而言,生产 Enbrel 就意味著要大量培养一种复杂的有机体,数量之多将超过以往。生产哺乳类蛋白质(即从经技术处理的哺乳动物细胞中培育蛋白质),过去一直都是以千克来计量生产的,而现在,安进高级副总裁博纳尼(Fabrizio Bonanni)却说,公司需要成吨生产蛋白质的能力。去年,Enbrel 销量上升了 400%,在美国食品药物管理局批准将这种药品用于治疗牛皮癣后,销量继续攀升。
收购 Immnux 后不久,安进公司就投入 5 亿美元改造 2,272 平方米的 BioNow 工厂。工程完成后,安进公司又立即扩张,在邻近建设了一座 4,645 平方米的 BioNext。这是一家全新的工厂,生物反应槽的大小是行业标准的十倍,计划在 2005 年启动投产,将成为世界上最大、也许是效率最高的重组蛋白质生产厂。
重组蛋白质来自经生物技术处理的克隆细胞(Enbrel 来自于仓鼠),这些克隆细胞要经过预先以发育成熟并分泌出特定的蛋白质才能形成。安进对其主要基因产品线(凭这些,安进才能占据 Enbrel 的 17 亿美元市场)的冷藏地点从来秘而不宣,不
过培养合格的克隆细胞确实是在西格林威治进行的。让细胞在繁殖过程中保持健康,需要有绝对无菌的环境,还需要加入蛋白质作养分并予以照料。当细胞数增长到一定程度,安进便会中止其生长,催化蛋白质生产,并去除余下的细胞物质。
这样的过程能进行一次,就可算得上是一大成就,而安进却擅长在工厂里反复进行这样的过程。贝恩公司(Bain)咨询师、医疗保健品制造专家查尔斯8226;法尔卡斯(Charles M. Farkas)说:“就大分子而言(Enbrel 分子的大小约是阿斯匹林这类化学药物分子的 2,000 倍),Enbrel 的生产是最复杂的,因而也特别昂贵。生产过程就像烹调,每次制造出来的 Enbrel 都可能稍有差异。这是因为它是活著的有机体。”
BioNow 工厂核心区的面积约 465 平方米,其清洁度至少要达到 10 万级。这意味著每个人都要穿戴从头到脚连为一体的无尘工作服,以控制粉尘污染,保证空气中微粒数量不超过规定的范围。每次细胞在反应槽之间移动,都要流经由数百个接头和圆形封口组成的一系列管道和阀门。质量高级主管金保尔8226;霍尔(Kimball Hall)说:“只要有一个就全完了。”他说的是,如果封口不严密,就可能被人体皮肤上或呼出的细菌分子穿过,从而把整批细胞都毁了。“只要一个分子,就能破坏整个生产环境。”
新工厂借鉴了公司厂区中各种建筑积累下来的经验,表现出了设计上的成熟,它的生产流程、甚至大部分硬件都与 BioNow 相同。但是,BioNext 的布局、组织和交通条件都经过了精心的规划,生产效率得到了提高,成本也节约了(他们不愿说成本是多少)。安进公司不愿承认成本和生产率给本行业带来了沉重的压力,但它还是对工厂采取了多项改进措施,期望能将产能增加 300%(在 BioNext,22 个批次的药品可同时生产,BioNow 只能同时生产 8-10 个批次),也使能源、清洁等各项运营成本能有所降低。
在这儿,小事也至关重要。例如,在 BioNext 就建造了重力供给式反应槽,让物料由上层流到下层,不再需要管线和抽运设备,同时也节省了相应的能源及维护成本。BioNow 的所有设备都被包含在无菌空间中,清洁的工作量很大。和 BioNow 不一样,BioNext 的大型反应器建在清洁室内,清洁室开有出口。这样就节约了大量用不著的空间,使许多硬件设备可以摆放在维护费用极高的清洁室外面。安进估计,每平方英尺最多可节约资本 400 美元,并且还省去了耗能巨大的高能粒子空气过滤装置和制冷设备。集中式服务器收集全厂反应槽的数据,不必依靠手工转换和现场检查。甚至还以手动曲柄阀门逐步替换由计算机控制的液压释放装置。生产设备本身就安装在宽阔的超大型滑道上,进入滑道里面进行设备维护很容易。有了这些滑道,就可凭目视做质量检查。工厂经理马克8226;科瓦鲁比亚斯(Mike Covarrubias)说:“我们有充足的空间,我们利用了这一点”。
投产后,BioNext 生产的哺乳动物类重组蛋白质可达全世界总供应量的 10%。人们会需要它的。分析家们预测今后 3 年 Enbrel 的销量至少会增加 17%,到 2007 年,销售收入将增加到 25 亿美元。
雷神公司 Raytheon
想 8 分钟装配一枚导弹,就要进行全面的生产革新
2001 年 9 月 11 日,第二架被劫持的飞机刚刚撞上世界贸易中心大楼,美国雷神公司图森导弹制造厂的电话就响了起来。12 月,雷神公司得到了美国空军的一份价值高达 1.56 亿美元的合同,生产 1 万套宝石路(Paveway)激光制导炸弹的组件。这种组件长 2 英尺,包含激光和 GPS 制导设备,能告诉炸弹的攻击目标,并引导炸弹飞向目标。合同中的组件还没生产出来,订单数就翻了两番。
可惜,提高产量可不像要求工人工作加把劲、增加一个班次或多订购零部件那样简单。2001 年 8 月,图森工厂每月大约生产 350 枚导弹,大约是其最大生产能力的一半。工厂已经十分拥挤。从发货区和生产线间到处都堆积著库存,余下的空间很小,连叉车都难以挤过去。生产业务主任瑞奇8226;尼尔森(Ricky Nelson)说:“为了让公司按要求运转,我们手上的物资需要增加三倍,而现实情况是我们放不下这么多东西。”
为了找出路,雷神实施了精益生产。它精简了装配工艺,去掉了附加值不大的元件,消除浪费,比如用来寻找被放错位置的物件所花的时间,以及在厂内搬运材料所花费的时间。工厂还要求员工提建议,试验了一些新办法,比如让雇员来建造装配线。最终,存货周转率增加了 400%,导弹单位成本降低了 40%。凭这一成就,公司获得了 2004 年度新乡奖。
雷神公司是制导炸弹的发明者、世界上最大的武器装备生产商,拥有约 43% 的美国国内市场份额。在 2003 年伊拉克战争开战之夜发射的导弹中,有一半以上是雷神生产的。但是,它的精益生产方法却是从1997年收购的休斯电子公司(Hughes)以及其它工厂那里学来的。休斯公司曾花费 2,000 万美元改造自己的基础设施,把工厂车间的附属装置拆除,将排水管道、电线和通讯线路铺设在露天高架的设备上,使它们很容易变换位置。休斯还给每部机器都安装上轮子,制造了一个空间开阔、布置方便的车间,以适应不断变化的需要。这些主意对制造业界来说并不新鲜,但在雷神公司那里却是新东西。总裁路易斯8226;弗兰切斯科尼(Louise Francesconi)说,“现在看起来,精益生产没什么特别高深的地方。但是,我们的装配多年来一直沿袭著美国传统的制造方法。我把精益生产看成是打破传统,它确实是一场革命。”
在图森工厂里,工人们把全球定位与激光制导系统安装到外形像子弹一样的导弹战斗部里。主装配区大约有 4、5 个微型工作站和 10 多个工人。在 9.11 事件以前,宝石路导弹业务经营部经理帕特8226;麦金尼(Pat McKinney)已经致力于简化和减少分装配站。装配线的效率提高了,但其设计能力是每月只装配 350 枚导弹。要想在一月内装配 1,500 枚导弹,就得进行更深入的分析,采取更有力的措施。
麦金尼开始计算一个工作日中有多少分钟,以确定最佳的产出间隔时间(Takt Time,即生产单个组件所需的时间),设定工厂的生产节奏。他回忆说:“要想实现月产 1,500 枚导弹,就必须每 8 分钟生产出一枚。”按照旧方法,宝石路在单个工作站完成全部装配,每个工作站各有一套自己的工具设备,需要单独的零部件供应。麦金尼将生产线分割成三个工段,每个工段只做一部分工作,然后再交接给下一个工作站。他还使各个工作站相互更靠近,便于工件往来传送。现在,每个操作站的工具数量和存货量只有原来的三分之一,占用的空间也少了。麦金尼说:“我们把多余的工具和工作台都拉走了,用半挂车拉了好几趟。”
即使采用了新的方法,还是需要有 4 名工人完全以人力搬运 45 磅重的制导装置,重复这项工作 150 次就意味著工人一天搬运的重量超过 3 吨。韦恩8226;梅纳德(Wayne Minnerd) 体壮如牛,留著灰色山羊胡子,身穿著无袖 T 恤,他说:“这完全是力气活,一个班下来,我能做的事就是拖著身子回家。”一天,麦金尼的手下在工作结束后到家得宝(Home Depot)的商店里买了大约 30 米的胶合板和 60 个橡胶脚轮。他们用这些东西造一个导弹手推车─一块安装了 60 多个轮子、用于宝石路装配线的细长木板。只花了不到几百美元,公司就取消了搬运工作,把装配周期缩短了 30%,而且还简化了生产,显著地降低了工伤几率。
但是,单靠这些胶合板和橡胶脚轮并不能让雷神公司达到生产目标。所以麦金尼把目光对准了非增值业务,如零部件的周转与运送。过去,导弹部件在到达发货站后,要走过 4.2 公里的距离,再经过装配,然后作为成品再送到发货站。现在它们只走 640 米。一个戴著计步器的工人说,现在他在一天工作中只走 1.6 公里路,而原先要走 48 公里。
供应商们也积极地配合。在过去,他们每生产一个零件,就用气泡衬垫包装,再塞进装运箱。零件到了图森工厂后,还要逆向操作这一过程。为了简化这道工序,雷神公司发明了可重复使用的集装箱。箱内带有按规格制作的充填式包装。运来的零部件一到公司,工人在几分钟内就能倒空零件,然后再把充填式包装还给供应商继续使用。
工厂中的其它部分也有所变化。原来,零部件都放在装配线旁边,现在则存放在运送零部件的拖车上。拖车一倒空就拖走去重新装货,另一台拖车紧跟著接替。存货由原来 4 个月的需要量减少到了现在的 10 天。每月存货周转次数由 2000 年 12 月的 3.2 次一下子上升到了今年 2 月的 12 次。总而言之,图森导弹厂现在已经能每月装配 1,500 枚导弹组件了,而材料的消耗量反而比其原来每月只能生产 350 枚导弹时还要少。
雷神公司从宝石路导弹生产中学到了经验,目前正在向其面积达 28,800 平方米的图森工厂的所有部门推广精益生产。现在,制造坦克用陶式(TOW)导弹的工厂采用了简约的精益设计,如可拆卸的组合式工作站,以适应多变的生产计划。如果工厂业务持续 6 个月萎缩,就取消陶式导弹生产,将空间改作它用。雷神还重新设计了战斧式导弹厂,采取了新型布局,对整个工作车间按照 8 小时单班作业做了重新规划。全公司的返工率下降了 20%,一次通过检验的成品率已由 2000 年初期的 87% 上升到现在的 95%。弗兰切斯科尼说,“随著我们不断地成长,我们的改进将越来越多地从小处著手。”这些改进当然是为了实现精益生产。