低成本是中国企业的传统优势,但是在2008年,中国企业依赖生存与发展的一些环境变量和外部条件发生了重大变化,石油、粮食等基础性原材料持续涨价、土地使用成本不断提高、人力成本也随着通货膨胀以及新劳动合同法的实施也有持续走高的趋势,这些变化导致中国企业固有的成本优势面临着重大的挑战。低成本是中国企业的传统优势,不可能丢弃。但在新的竞争环境下,对中国大量企业来说,必须去探索新的成长模式。丰田汽车的低成本+差异化战略模式也许最值得中国企业深思。将成本降低50%在很长一段时间,中国企业主要是通过降低原材料、劳动报酬等可变成本来实现总成本的降低;或是向上游供应商转嫁成本压力;或是压低工人的工资。现在,直接压缩成本这样一条途径已经走不通了,必须转变思路通过生产组织方式的转变,通过运行流程管理的提升,来提高企业的运营效率,实现成本的相对降低。比如说,降低产品品质成本;使生产、运营更加均衡顺畅以减少波动成本和系统成本;提高设备、生产线的利用率;等等。这种成本节约方式的卓越代表是日本丰田汽车。日本国内的要素成本基本上是降无可降的,但丰田汽车在全世界保持着成本竞争力。1999年,时任丰田社长的张富士夫对外公布了“丰田CCC21——21世纪成本竞争力建设计划”,目标是连续三年将成本削减的幅度控制在平均的30%的水平。这一计划震惊了世界汽车业,在外界看来成本水准已接近极限的丰田再次大幅度降低成本几乎是不可能完成的任务。2005年6月 ,渡边捷昭接替张富士夫出任丰田汽车株式会社社长。在过去的5年里,作为丰田CCC21计划具体执行人的渡边为丰田节约了100亿美元的开支。一提到成本削减,大多数人都会将目光锁定在帐面的数字操作上,会首先考虑降低材料购进价格、精简人员或是将生产转向人工成本较低的国家等。这些方法在丰田看来都过于简单。渡边捷昭秉承了丰田汽车的一贯理念:“从工人或从购买者身上获取利润都不是好的经营管理,不要降低产品质量,不要降低工人工资,不要增加消费者负担。把脑子用在发现更好的方法上。成本削减不只是削减生产成本的问题,而必须力争掌握不输给对对手的成本竞争力。”博锐管理在线|www.aihuau.com|在消减成本的方法上,渡边捷昭也并没有惊天动地的大措施,只是将丰田的“持续改善”贯彻地更为彻底与平衡。渡边捷昭认为,如果要实现30%的成本消减,必须让员工们将成本减半作为目标,并且这种改善必须以客户价值为核心,以整体改善作为目标。在实际的执行中,丰田各部门是将成本消减50%作为了努力的目标。
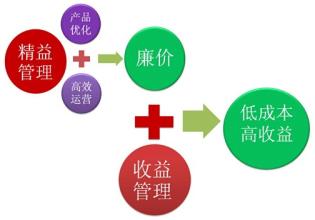
很多人对改善的作用半信半疑,认为改善不过是小范围的成本节约或者是简单的工作方法的调整。实际上,丰田的改善是是一种不断追求更高目标的自我挑战,改善的终极目标是消除一切不创造客户价值的浪费。所谓的浪费,是指那些能够提升附加价值的一切现象及结果。丰田最初的改善主要集中在生产环节。比如生产现场的作业,丰田将工人的动作分解为作业和无用功两部分,进而又可以将作业分解为能够提升产品附加价值的实际作业和不能提升产品附加价值、只是为了维持现行作业条件的附带作业。所说的附带作业是指类似更换磨具、提取零件、拆解包装等附属于生产加工的行为。改善的首要着眼点就是将无用功、可视化等核心问题提炼、统一,然后制作标准作业书,实现工作流程的标准化,从而推进作业的改善,并逐渐降低附带作业的比例。现在丰田的改善不再局限于单一环节,也不再局限于生产环节,而是强调整体效率的提高。用渡边捷昭的话来说:“从购进原材料到将产品送往客户手中,需要一气呵成的改善,也可以说是整体改善。”一个典型的变化就是对待机器设备的态度:丰田相信未来制造业的发展,一定是以人为中心;丰田要求发挥人的智慧和创造力去更好地利用现在设备。制造业发展至今,大多数的手工作业都已经被机器所取代。因此应该有很多的企业管理者都在为机械化带来的效率提高,生产率提高,进而成本降低而对待高兴。与此相反,丰田思考的却是自动化的普及正在产生着全新类型的浪费。设备的引进,感觉好像是节约了人工成本,但它实际上造成了其它方面的浪费。这种单项工作的效率提高,改变了前序工程及后序工程的操作方法,很可能会引起整条生产线的混乱。这不仅会提高成本,还会造成整体效率的降低。正是由于这样的理念,在丰田公司很多在其他企业看来有些老化的生产线创造的价值却远远超过了所谓的高科技新设备,这一点出乎了大多数人的意料。丰田的整体改善观也体现在供应链的改善上。同其他汽车制造商不同,丰田并没有依靠对供应商的压榨——压低零部件的购货价格来实现成本消减,而是与供应商一起积极地思考降低成本的办法。丰田会派遣专业人员到供应商的生产现场去进行指导,推进改善,绝不吝惜在这些方面的投入与付出。丰田做到了所有合作伙伴实现了不同的程度的盈利。以客户价值作为改善的核心在渡边捷昭时代得到了进一步的强化。渡边捷昭言:如果有人问我,应该从哪里开始改善,答案一定是从接近客户的地方开始。时刻将“这是为了客户的利益吗”作为衡量工作好坏的标准。丰田认为,价格、品质、交货期这三个要素密不可分,其中任何一个出现问题,都不可能让客户非常满意。不能在成本削减的过程中降低品质或是延期发货,这样必然会失去顾客的信任与支持。在刚刚好的时间里提供高品质的产品,是对客户最大的负责,也是降低成本的最有效的方法。丰田模式的另一面:创新丰田模式使得丰田享有了低成本的竞争优势,但是丰田汽车之所以成就今天的地位,在于其杰出的取悦消费者的能力。这其实是丰田模式的另一面。渡边捷昭 :丰田公司可以创造出比其他公司更高的生产效率 ,并成为其他公司学习的榜样。但如果丰田模式仅停留于生产过程 ,可能早已经过时了。汽车业是强调不断创新、不断变化的产业 ,所以仅仅提高生产效率 ,以更低的成本进行批量生产已经不合时宜。在我看来 ,丰田模式是一种不断改进、强调持续创新的企业精神。这种精神早已渗透到丰田的各个层面 ,而不仅是生产层面。 多年来,丰田汽车执着于产品的性价比:同样的价格性能最优,同样的性能,价格最具竞争力。渡边捷昭:丰田并非廉价品牌,它以卓越的质量著称,因而价格也不便宜,在新兴市场中,它甚至属于高价位汽车。然而消费者终将承认它物有所值,他们会说:“下次我一定要买辆好车棗就像丰田那样的。”我们非常希望“丰田汽车”是家庭购买的第二辆汽车。杰出的性价比成为丰田产品最为核心最为直接的竞争力。正式依靠这一差异化的竞争力,丰田公司成为世界上最赚钱的汽车生产商,从2003年起,其盈利水平就超过了所有的汽车公司,纯利润连续数年超过了"底特律三大"的总和。渡边捷昭在接受美国记者采访时曾言:我们须关注两个方面:其一是提高质量,其二市降低成本。我们的产品必须是全世界最好的,推出新产品的速度必须是最快的,生产成本必须是最低的。我们所关注的就是,丰田公司如何才能同时达到这些目标。这就是我们投资开发新技术、新流程、以及培养人力资源的原因。我的首要任务就是确保公司脚踏实地、坚定不移地切实完成上述目标。当然,质量不是丰田汽车产品性价比的唯一要素,围绕客户价值进行持续进行创新才是全部。丰田拥有近50多个著名的品牌,既有面向全球的车型,又有针对各地市场的车型。丰田于1997年开始销售的混合动力车普锐斯是典型的丰田式创新。石油资源日益紧张、价格节节攀升、全球变暖广受关注,丰田果断推出了世界首款混合动力车,截至2008年4月底,由其推出的混合动力车普锐斯(Prius)全球销量已102.77万辆。丰田汽车公司2007年全球销量达936.6万辆,美国通用汽车公司2007年全球销量达936.9万辆,丰田以3500辆之差未能改朝换代,通用汽车保住了拥有76年之久的全球汽车制造业老大的头衔。但是,从盈利能力、从发展前景来看,丰田汽车是毫无争议的世界第一。以2008年年初的市值计算,丰田公司的总市值超过了美国三大汽车公司通用汽车、福特汽车和戴姆勒棗克莱斯勒市值总和。外界对丰田何时成为世界第一津津乐道,但丰田显然并不看重市场份额的得失。正如渡边捷昭所说:我们绝不会在数量或收入上争第一,只要我们不断提高产品质量,规模自然会随之扩大。 对于我来说,成为行业第一并不在于我们能生产或销售多少辆车,也不在于每年的销售收入或利润要比其他汽车制造商高多少。对于我来说,行业第一意味着我们要在全世界范围内,做到持续的质量最优。我认为质量是最有价值和最最要的事情,这也是我管理风格的根本。对于丰田来说,关键是生产全球质量最佳的汽车棗各方面表现卓越、没有瑕疵的汽车。如果今天不提高质量,未来我们就不要期望实现增长。丰田模式的误读与本质著名学者齐二石教授曾言:“自20世纪80年代以来,中国许多制造企业一直在学习丰田生产方式,但大多照猫画虎,效果不佳。”其实不仅仅是中国企业,被丰田打得灰头土脸的美国汽车产业曾花了500万美元,请琼斯等三位教授考察全球汽车工业,探讨日本汽车生产方式的秘密(考察结果后来整理为名著《改变世界的机器》)。全世界都在学习探讨丰田模式,但如同盲人摸大象,丰田模式变得越来越模糊。洞悉丰田模式的本质是学习的基本前提。其实丰田模式的创始人大野耐一早就告诉我们:“丰田生产方式是一次思想革命,丰田成功的关键在于其管理思想而非管理工具”可惜太多人忽视了大师的警告。丰田现任社长渡边捷昭接受中国记者采访时对丰田模式的本质做了这样的解读:“尽管有那么多关于丰田模式的书籍,降低成本、看板生产、共赢等可能都是丰田模式的内容,但丰田公司内部并不是提倡用数字和条条框框进行管理的。因为管理过程中的量化流程是西方的东西,我们更强调一种思维,即持续研究和创新的思维。”“学习丰田模式不在于你模仿。因为零库存、看板在欧洲和中国等市场可能是不适用的。丰田模式在每个地方实施方法也不尽相同。举一个例子,在日本本土,如果丰田的生产中出现问题,生产线就应该立即停止,检查生产过程中差错。我们当时在美国进行生产时,也提倡看板生产。一名美国工人发现生产发动机配件时工序出了问题,他拉停板,但心中充满了恐惧,原因在于他认为是由于个人原因导致了生产线出现问题,并担心由于个人问题而被老板炒鱿鱼。后来丰田的看板生产并没有在美国本土实施,也不再提倡工人发现问题时就拉停看板,而是通过即时统计,以三个小时生产标准统计结果进行反馈。这样既保障了生产的精确性,又符合了美国当地的习惯。所以在生产过程中,一定考虑当地的实际情况,在借鉴中学习丰田模式,可能会比较理想。丰田模式并非千篇一律,即使在中国不同地方,丰田生产模式都是不完全相同的。”丰田模式或者丰田思想可以简要概括为“持续改进”和“尊重他人”两大支柱。正如渡边捷昭所言:管理过程中的量化流程是西方的东西 ,丰田更强调一种思维 ,即持续研究和创新的思维、系统与整体的思维。企业内部的每一个环节都是相互关联的,每一个局部的效率都会影响着整体的效率。丰田模式是整体的优化思想,以合理配置和长期利用企业生产要素消除生产过程中一切不产生附加值的劳动和资源,从而增强企业适应市场需求的应变能力,获得更高的生率效率和更大的经济效益。丰田思想还体现在强调人的主观能动性。丰田认为,人是有主观能动性,有创造性、有喜怒哀乐的。在企业管理中尊重人、尊重人性,让人有主动参与的积极性,从而调动人的主观能动性、创造性,才能最大限度地提高生产的效率,才能有持续创新的可能。丰田所实施的“管理参与制”、“终身雇佣制”、“合理化建议活动”等制度全部源于激发员工的主观能动性。丰田思维中的“人”,既包括员工,也包括客户员工和供应商。“客户优先”、不要把麻烦留给客户是丰田公司的核心原则之一,而客户这一概念也不并局限于最终用户。在流水线上,下一个工作站的用户就是前一个工作站的客户。