脲醛树脂胶粘剂是以脲素与甲醛生成的以树脂为主体的胶粘剂,脲醛树脂几乎是所有合成树脂中最廉价的,又因具有较好的性能(如较高的胶接强度,耐热性和耐老化性等),且固化快,毒性低,原料易得,制造工艺简单,使用方便,胶层色浅且不污染板面而广泛应用于刨花板、胶合板、纤维板和细木工板等人造板的制造及矿物棉、矿物纤维和铸体砂型等材料粘接,是竹、木加工纸张粘接,钢化涂料等行业应用广泛的一种胶粘剂,是市场上需求量最大的胶粘剂之一[1]。
本研究采用添加聚乙烯醇对脲醛树脂胶加以改性,得出了其适宜的工艺条件和添加比例,所得改性脲醛树脂胶性能优于一般的脲醛树脂,尤其在粘接速度、耐水性、强度等方面有较大的提高。1 实验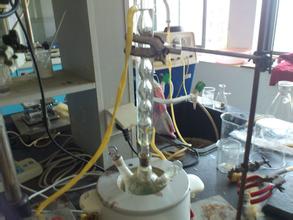
1.1 原料及仪器原料:(1)脲素;(2)甲醛,化学纯;(3)六次甲基四胺,分析纯;(4)氢氧化钠;(5)聚乙烯醇。仪器:250 mL三颈烧瓶,球形冷凝管,电动搅拌器,200℃温度计,粘度计,电热套。1.2 实验原理1.3 步 骤① 在带有电动搅拌器的250 mL的三颈烧瓶中,加入1 g PVA和30 g质量分数为35%甲醛水溶液。加热至4O℃左右,反应5 min,使PVA基本溶解,溶液透明,允许有少量悬浮物;② 升温至5O℃ 左右,加1.5 g六次甲基四胺,全溶后用质量分数为2O%的氢氧化钠调pH值至8.0左右;③ 尿素5O g,按7:2:1质量比,分3次投料,升温至6O℃ ,投入第一批,并加0.5 g PVA,缓缓升温到8O℃ ,反应30 min;④ 用氢氧化钠调节pH=7.0,加入第二批尿素,保持温度8O℃ 以上。反应30 min;⑤ 再用氢氧化钠调节pH=8.0,加入第三批尿素,反应2O min;⑥ 降温至4O~5O℃ ,用NaOH调pH值至7.5-8.0,冷却出料得产品[2]。2 结果与讨论2.1 各因素对反应的影响2.1.1 原料量比(A)的影响固定其他条件,选定不同的甲醛与脲素的质量比,得实验数据见表1。甲醛/脲素的量比降低,则胶粘剂羟甲基及游离醛含量降低,导致产品粘接力下降,储存稳定性下降。质量比升高,胶液中游离甲醛含量增多。同样对树脂质量造成不利影响。在配比中适当增加脲含量,可提高产品的固含量,增加体系的粘度,脲醛树脂的稳定性与缩聚物分子中的-NH2基的数量有关,-NH2基比较活泼,很容易和羟甲基发生缩合作用。所以若反应后剩余的-NH2基越多,中间缩聚物则越容易发生交联,树脂液的稳定性也越差。可见 (甲醛):n(脲索)=1.5:1较适宜。2.1.2 聚乙烯醇用量对反应的影响应用最佳原料配比,固定其他条件,选定不同的聚乙烯醇的用量,得实验数据见表2。改性聚乙烯醇的影响也较重要,聚乙烯醇与甲醛反应生成聚乙烯缩甲醛,改善了树脂结构,使树脂的胶联度下降,脆性降低,增加挠性,改善了耐老化现象。由于聚乙烯醇较贵,所以其用薰应加以控制,经过大量实验考察,得出其质量比为1.0%时效果最佳[3]。2.1.3 反应温度对反应的影响选择最佳原料配比和聚乙烯醇用量,固定其他条件,选择不同的反应温度,得实验数据,见表3。在酸性介质中,升高温度,反应速率迅速增加,树脂聚合度迅速增大,甚至造成凝胶。但温度太低,则反应速度太慢,聚合度偏低,导致树脂固化困难,因此温度控制应适当。因此反应温度选用100℃ 。2.1.4 反应时间对产品的影响选择最佳原料摩尔配比、聚乙烯醇的质量和反应温度,选定不同的反应时间,实验数据见表4。反应程度对体系粘度影响也较大,即反应时间越长,树脂聚合度越高。要达到最佳的粘接性能,应控制反应的终点,过早停止反应粘度就小,反应时间延长粘度增大。因此反应时间选用60m in[4].。2.2 最佳条件稳定实验在上述4个因素的最佳工艺参数条件下,进行了稳定实验,其结果见表5。2.3 采用多次缩聚工艺在合成树脂过程中,脲素分段加入。在实际操作时可以采用二次、三次甚至四次缩聚工艺,将相同量的脲紊分成的批量越多,生成的树脂的粘性越好。这样在第一次缩聚时,脲素与甲醛的摩尔比较高,有利于形成二羟甲基脲。第一次缩聚时剩余的游离甲醛在以后各次缩聚时,逐次与按比例加入的新脲素结合,使游离甲醛含量降到最低程度,采用这种工艺生产的树脂胶一般为乳白色粘稠液体。3 结论(1)本实验以脲索、甲醛为基料,采用聚乙烯醇为改性剂,进行加成缩聚反应,制备改性脲醛树脂胶粘剂。通过对胶液固含量及粘度的测定可确定最佳实验条件: (甲醛): (脲素)=1.5:1。(聚乙烯醇)=1.0%,反应温度100℃ ,反应时间60 min。(2)在最佳工艺条件下,生产的产品质量稳定, (固体含量)>55%,粘度=120 150 S,产品质量达到国家规定的指标。