开磷集团认真落实科学发展观,围绕节能、降耗、减污、增效,大力发展循环经济,坚持资源开发与节约并重、把节约放在首位,以资源的高效和循环利用为核心,优化产业结构,“十五”期间投入技术改造和装置更新资金近10亿元,进一步转变经济增长方式和消费模式,实现节能减排,促进企业经济可持续健康发展。
2000年以来,以董事长、总经理屈庆麟,党委书记成元明为首的开磷集团领导班子,结合实际,制定了开磷“三步走”发展战略目标,决定用三个五年时间,使企业销售收入分别达到20亿元、50亿元和100亿元,把开磷建设成为现代化的大型企业集团。2005年,开磷集团圆满实现第一步发展目标,实现销售收入23.2亿元,超计划3.2亿元,比2000年翻了两番,实现了企业跨越式发展。2006年和2001年相比,近5年时间,开磷集团销售收入从6.48亿元增长到30.54亿元,年平均增长率36.37%;实现利润从0.11亿元增长到1.75亿元,年平均增长率73.13%;上缴税费从0.45亿元增长到2.1亿元,年平均增长率36.4%;资产总额从17.4亿元增长到52亿元,年平均增长率24.58%。今年1至8月份,企业生产经营同比也有较快增长,实现销售收入25.04亿元,比去年同期增长20.6%;实现利润1.23亿元,比去年同期增长56.13%;实现税收2.98亿元,比去年同期增长45.37%;出口创汇7223万美元。到今年8月底,集团资产总额已达65亿元。
由于开磷集团产业结构行业跨度大,原材料开采和后续深加工并存,磷化工和煤化工能源消耗占集团能耗总量比例达90%以上,又以煤化工最为突出。2005年,集团公司年综合能耗总量达41.44万吨标准煤,以煤化工为主的剑化公司占26.62万吨,达64.24%;集团公司万元工业产值综合能耗2.56吨标准煤,剑化公司高达18吨标准煤,节能减排任务十分繁重。
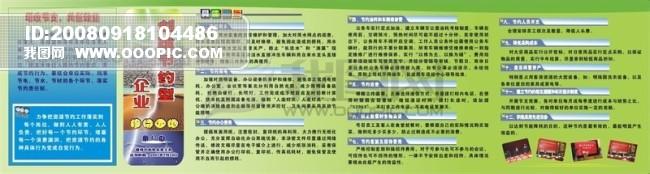
为此,集团领导一班人认为,经济总量的大幅增长,不能以大量消耗资源能源为前提。创建“资源节约型、环境友好型”企业,走循环经济和可持续发展之路,是开磷生存发展的必由之路。为此,在集团领导采取切实有效措施发展循环经济,实现节能减排,取得了明显效果。 在磷化工生产方面,开磷公司年产10万吨重钙自1995年建成投产以来,由于装置设计缺陷与管理经验不足等诸多因素,生产一直不正常。到1996年,装置腐蚀损坏严重,经营亏损高达7000多万元,又支付了大量的污染赔偿、排污及环境治理费用。为改变落后的经济增长方式,实现由粗放型增长方式向集约型增长方式转变,注重抓好节能减排,彻底改变企业污染现象。从1999年开始,按照清洁生产工艺要求,加大技术改造,淘汰了落后的硫铁矿制酸传统工艺,实施先进的硫磺制酸工艺,仅拆除硫铁矿生产装置改建硫磺制酸装置一项,成品硫酸电度单耗从91度/吨降到现在的31度/吨,全年节约电能近6000万千瓦时,逐步实现了装置大型化、工艺技术先进化、生产管理智能化。在技术改造工作中,从项目选择、论证、工艺流程确定到建成生产的全过程,严格遵照国家的建设项目管理规定,确保环境保护和社会效益。现在生产规模扩大10多倍,而“三废”排放却大幅度减少,先后建成20万吨、60万吨、80万吨和40万吨硫磺制酸装置,使硫酸生产能力由2000年前的10万吨,扩大到目前的200万吨以上,基本实现了清洁生产。厂区和周边山野恢复了生机,受到各级政府和社会的广泛赞誉。在煤化工生产方面,企业投入1300多万元进行水洗脱碳装置改造,甩掉高能耗多事故的水洗脱碳,年创经济效益823万元;投入226万元进行型煤技改,综合利用过去无法使用的粉煤,年创经济效益420万元;投入30万元对合成车间凉水塔及再生气回收系统进行技改,操作工艺得到明显改善,合理地利用了有效气体;投资450万元进行35吨循环流化床锅炉技改,合理使用造气炉渣,平均每年可创直接经济效益270万元;投入591万元进行二气回收技改,对企业经济效益的增长起到了推动作用。在矿山生产方面,矿业总公司对用沙坝矿实施竖井改溜井工程,拆除了矿山井下主、副井提升机(2×500KW)系统,每年节电320万千瓦时。改造了马路坪35KV和高磅35KV两个变电站,改造极乐南矿、两岔河矿区民用供电线路、矿区公共照明系统等,降低线路电力损耗,提高供电质量。矿山还对部分井下供风设备进行升级改造,采用较为先进的供风设备,提高了供风设备利用率,降低了电耗。机电设备公司采用PLC可编程技术对立式车床原电气系统进行技术改造,去掉了原立式车床的中间断电器、时间继电器以及部分电容电阻,减少了机床的故障率,节约了电耗,提高了效率。
不仅如此,开磷公司以节电节水为重点,大力推进清洁生产,以及清洁生产和节能的先进工艺,实施热电联产节能技改工程,利用硫酸生产过程中产生的高温、高压蒸汽进行热电联产,投入3500万元新建2×1.25万千瓦余热发电装置,利用压差发电,实现热能的分级综合利用,每年节能可达9万吨标煤,年余热压差发电1.7亿度,节能效益达1亿多元。既节能又环保,降低能源消耗20%以上。
对新建磷铵、复合肥等工程项目开磷实行节能降耗设施与主体设施同时设计、同时施工和同时使用的“三同时”原则,对做不到“三同时”的项目坚决不予开工。为使企业节能降耗工作水平上新台阶。近年来,开磷集团投入1.32亿元,先后完成250立方米/小时污水处理站、工业废水集中处理系统、矿浆站回水系统、渣场回水系统和相关隧道工程。目前,厂区工业废水综合利用率达95%以上,基本实现零排放,磷肥生产新鲜水取水量已由改造前的3000立方米/小时减少到现在的1200立方米/小时,基本实现年回收利用工业废水1100万立方米的目标,取得了较好的经济效益、社会效益和环保效益。先后兴建了9个工业用水回收槽,对于生产过程中所产生的尚未受污染的水,进行分散回收、集中调度、循环使用,达到“零排放”标准,做到一水多用,优化了水资源的配置,节约了水资源和处理药剂成本。全厂可循环利用的循环冷却水总共可达15000吨/小时,极大地节约水资源,减少污水排放,每年回水利用约1100万吨,可实现经济效益1600余万元。为让磷石膏渣变废为宝,公司自主开发了以磷石膏为主要原料的年产1亿块高强耐水石膏标砖生产线,为磷石膏的综合利用开辟了一条经济、环保的利用途径,推动了建材产业的发展,实现了产业链的延伸。6000万块/年页岩制砖项目已完成项目前期工作,今年3月已进入实施阶段,计划于年底建成投产,每年可综合利用矿山开采废矸15万吨。
今年前7个月,开磷集团万元工业产值综合能耗为1.9吨标准煤,同比下降10.38%。其中,合成氨2484kgce/t,同比下降26.4%;磷酸一铵115.9kgce/t,低于政府考核指标5.39%;磷酸二铵144.7kgce/t,低于政府考核指标3.53%;重钙125.10kgce/t,同比下降26.4%。今年1至7月份,开磷集团实现节能6.52万吨标准煤,预计全年可节能10万吨标准煤,企业朝着“资源节约型和和环保友好型”目标迈进。