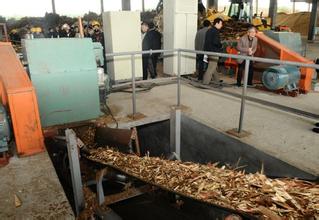
看板制度从一块零部件流程板和字条变成了液晶显示,TPS(丰田生产方式)越来越现代。看惯了丰田工厂章鱼一样忙碌的人,很难再想象现代化的丰田生产方式,这简直是背叛。 但事实就是事实。空气中依然弥漫着甜丝丝的鳗鱼饭香气,年轻的工人们依旧挥汗如雨地做着机械手一样的动作,只有下班后的习习晚风,和热气腾腾的清酒能够解除疲劳。日本岛上的一切仍然熟悉,可是生产线两旁的料架却看不见了,它们变成一辆辆小车跟随着生产线悄无声息地前进着。 前进,前进,好的方式好的品质,TPS来到中国。一汽天津丰田二厂的工人们站在皇冠车前宣誓,他们要保证车子的质量。但是TPS对每一个装配动作的标准化能否在中国工人这里不折不扣地执行?中国能否对TPS的未来有所助益呢? 从推到拉 只能在必要时进行补充,对于未雨绸缪的中国人来讲,这一点难以理解。 按照美国的生产方式,一个工厂计划时的生产能力必须在建成后一次达标。如果市场不支持,那么就减产、关工厂。直到现在,通用和福特也是通过减产、关厂来协调产销平衡。这是一种置之死地而后生的推式制度(PUSH),它只能滋生在资源丰富的美国;日本以丰田为代表的生产方式是拉动式的,即只提供一个相对较小的生产能力,当市场需求增大时,再增加工人的劳动生产率,然后再考虑延长生产线,最后才是开设新的工厂。这就是根据需求来拉动生产的“拉式制度”(PULL),每一个流程只提供下一个流程所需的数量。 一汽丰田的基础是天津丰田工厂,天津是中国最早的工业基地之一,但计划经济时代以产量多少为考察标准的思维模式根深蒂固,把产品推给用户,再把需求的部件数量推给供应商,它类似于美国的推式制度,但盲目性更强,而且很难通过关、停来减少损失,这种“推”造成了迄今为止最大的浪费。 由于人们的思维是对TPS的反动,一汽和丰田对天津工厂的接手,很难在短时间内改变企业的文化传统,这是TPS执行前最重要的障碍,不改变人就无法把中国工厂以生产为导向的“推”,变为以需求为导向的“拉”。 先制造人,再造汽车 改变的确是从人开始的。就像丰田人常说的“制造汽车前先要制造人”。对员工的培训延续丰田的领导风格,一直以来,丰田强调“问题式”的培训,即很少发号施令,而强调以苏格拉底式的简单提问诱导员工进行工作。比如,“你觉得问题出在哪里,你认为自己怎样才能改正”。 保证自己的责任,精确而无误。这在中国传统工厂中没有形成统一认识。最明显的例子是,一些中国工人的标准化操作不足,随意性工作较多。比如在轮辋的紧固过程中,标准化操作的要求应该是拧12次的话,过去工人通常会按照9~12次来执行。这对最早进入中国的汽车外企大众来讲,感触最深。天津工厂在最初也有这样的问题,以致威驰在最初的生产时也出现过车门密封条脱落的现象。TPS的最早执行人大野耐一说:“在拉式制度中,前一个制造流程必须遵照后一制造流程的需要与指示来操作,否则,就无法做到准时生产。” 如何理解机械和人的关系?一方面,一汽丰田把机械的标准化概念传输给人,强调每一个动作的幅度与标准化。但这不排斥工人的创造,过去奔驰的工程师认为中国工人的创造性过强,而忽略了标准化操作。但丰田认为中国工人的创造性在此时也能体现出优势,他们的合理化建议模式成为中国生产方式的内生因子。 TPS要解决八大瑕疵:没有根据订单生产造成过剩;工人要等零部件或者设备检修;物流出现不必要的运输;不必要的要求和动作;存货过剩;某一工序的返工;工人在车间里有大量不必要的走动;最后是未被调动起来的员工创造力。当丰田发现最后的一项是中国的优势时,前面的七项瑕疵迎刃而解了。 TPS与中国onmouseover=displayAd(3);onmouseout=hideAd(); onclick=linkClick(3);>企业文化的融合正在更多的企业体现。在广州本田,工人们都要学习PPT等软件工具以便随时向生产部门提出自己的改进方案;在上海通用,工人们发明了发动机安装工具,同时由于仪表板组装时要坐在车里极不方便,工人们还把中控台水平放置,在车外完成组装。这让人联想到丰田工人发明的可旋转座椅,工人可以在车子内外自由活动,但中国工人能够以更简单、更便宜的方式解决相同的问题。TPS的精益、准时生产在中国工人的细节发明中得以完善。 从皇冠开始的TPS中国版,将在一汽丰田第三工厂得到光大,但是一汽丰田销售公司副总经理董海洋却认为:“最能体现丰田生产方式的仍然是一厂,它从设计3万台扩展到现在的12万台,本身就是一个精益概念的最大化。”这里面,既有最初丰田工程人员培训的功劳,也有中国工人基于自身特点的改进。他们不再仅停留在TPS的工具上,而是在理解它内核的基础上提出自己的建议和意见。 在中国,以建立现代企业制度为目标,天天为降低成本而头疼的中国企业选择TPS是一种必然。现在,把讲求和谐的中国式管理融入TPS,不仅对一汽丰田这样的企业有意义,对丰田自身来讲也是一种面向未来的承诺。改变同样是一种必然。 (配发)将TPS进行到销售端 ——专访一汽丰田销售公司副总经理董海洋文/张炤虎当我们把TPS从看板、拉绳、及时生产和工作小组这些工具中拿出来的时候,它的原则浮出水面,而这些原则正在被一汽丰田销售公司里的工作人员所应用和改进。这是超越TPS的理念,它是丰田模式的本地化。顾客第一的丰田销售模式其实正是来自于及时、高效的丰田生产方式,它是TPS在销售端的延续。 《商学院》:利用今年没有全新车型的机会,一汽丰田怎样做网络方面的提升工作,它的原则是什么? 董海洋:现地现物的原则是丰田销售模式的体现,就是要更多地了解市场上的实际情况。我们今年着重要做三件事:其中第一件就是要增强地区经理一级人员,我们称之为地区担当的执行力。比如在访店频次上,我们要求地方担当要保证每个月至少访问每家店两次,加上他的上级大区经理每个月每家店跑一次,平均到店面上几乎每个月就要有三次地区负责人的考察,了解用户需求和市场变化。沟通的频次能够得到保障。 再下一步,今年夏天我们考虑建一个经营支援室,因为国内的经销店投资方往往同时投资几个不同品牌,难免拆东补西,影响店面的现金流。我们这个支援室会随时考察每家店面每天的现金流报表、资产负债表,然后配合一汽、丰田金融公司,以及与各商业银行的合作,向这些经销商提供资金支持,每家店每个月的曲线监控我都有,这样就能保证持续地解决问题。 《商学院》:丰田从多渠道经营到今年开始整合渠道,变化的原因在哪里? 董海洋:丰田在美国有三套体系,除了个性化的SUV和皮卡品牌赛扬、雷克萨斯之外,其他丰田品牌都是一个渠道,而在日本,丰田原有五个渠道也有整合。这主要是从规模发展考虑。 分渠道是不是精益?全国所有的乘用车4S店有6500多家,去年全国乘用车销量在313万台,平均下来每家不过卖400台,今年估计销量在400万台,平均也就是600台。现在店多投资又热,各品牌建4S店的价码偏高,通常都在千万元水平,运营费用每年至少要650万元。这个压力很大,国内卖二手车环境不好,只能靠新车,平均销量不到1200台很难盈利。而且现在国内佣金返利水平只有五六个点,美国是12%以上,经销商不做维修等关联业务几乎赚不了多少。这些客观原因要求我们从现地现物出发,解决问题。 《商学院》:在订单制的需求下,丰田生产方式一直强调低库存会带来等待时间延长,现在买花冠要等多长时间?库存多少合适?所谓零库存的概念是不是像无籽西瓜一样只是一种追求? 董海洋:花冠平均等一到两周。丰田追求低库存,要客观看待这个概念。今年一季度,一汽天津丰田的工厂平均工业库存是0.3个月,也就是说一个月周转三次,店头的渠道库存是0.8个月,二者再平均一次,整体库存水平是0.5个月,一个月从清库到充满再到清库,要周转两次。这个数字相对工厂15万台的生产规模不是大了,而是库存系数偏少,如果新产品需求多的情况下店头存货少反而不利。整体上要辩证地分析问题。按照丰田模式,生产均衡化是重要的一环,必须保证一定的库存水平,以保证生产的平稳,不会因为个性化订单的突变而波动。