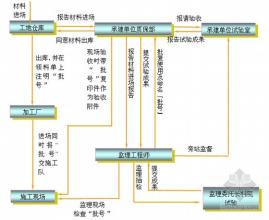
国内很多中小企业的质量管理工作还基本处于质量管理的初期阶段,主要工作还局限于质量检验,企业内部的大部份管理人员和生产一线的操作人员品质意识还比较低,还没有真正意识到“产品质量”对企业发展的重要性。对“量”的关注远远大于对“质”的关注,生产出来的产品只要能用就行。在其看来“能用”就是“符合要求”,就是合格产品。特别是中小包装企业普遍存在这一现象,在质量管理上还未形成一套有效的控制程序和相应的“检验标准”,或者说检验标准还很不完善,对其生产的纸包装产品如“瓦楞纸板和瓦楞纸箱”还局限于人为的“主观”判断,在市场上无法形成一定的竞争力,主要的客户群在很大程度上还依靠于“人际关系”来维护。
鉴于目前中小包装企业在质量控制及改善方面存在的薄弱情况,在短期内要实现“全面质量管理”或“零缺陷管理”在实际当中确实还存在暂时无法解决的困难,这一点从质量控制理论及质量的发展历程也都是可以看得出来的。多少知名企业都是经过了“阵痛”之后才明白,质量管理能力的提升不是一朝一夕的事。因此在质量管理方面,除了要建立一套有效的质量控制体系之外,首先可从质量的源头开始进行控制,与供方协商一致明确验收准则,也就是在“订购合同”中明确质量标准,并制定进货检验规程,因为合格的原材料投入,是生产出合格产品的前提,其次再辅以过程质量控制和成品的质量把关,基本上可以将60%~80%的质量问题在事前及企业内部得到有效控制。只要注重事前的预防和控制工作,才有可能从根本上提高产品的质量,降低生产成本。例如:在箱纸板和瓦楞原纸进货检验时,常规情况下可从两个方面进行,即“外观检验”与“物理性能检验”。但很多中小包装企业不具备“物理性能检验”的能力,没有相应的检验设备,因此只能从外观上来判定箱纸板和瓦楞原纸的合格情况。如:箱纸板和瓦楞原纸表面平整情况、纤维组织均匀,纸幅间厚薄一致,每批箱纸板应色泽基本一致,不许有明显的毯印和露底现象。箱纸板和瓦楞原纸应切边整齐,不许有折子、洞眼、硬杂物、破孔、裂口、缺边、缺角、薄边、毛边、褶皱及其它影响使用的外观纸病。卷筒纸断头是否作明显标志等等来判定质量的好坏。但由于箱纸板和瓦楞原纸的特殊性,使检验人员无法在事前,仅靠简单的外观检验来真正发现或检查出原纸的内部不良情况,最终影响生产的正常运行。对此类问题可先通过对协商认可(合格)的原纸小批量试生产来进行检验,试生产过程中作好各类反应质量现象等数据、信息收集。如在原纸预热时通过观察蒸发的“雾气”来确定水分含量的大小;纸筒接头是否用胶带纸牢固粘接好,每个卷筒纸接头有多少个,纸筒的松紧边情况及上面谈到的各类纸病,生产出来的箱片面纸是否存在外观不良等等。并将存在的质量情况记录下来,作为后续质量检验的参照;同时将每一次的质量记录情况进行比较,通过分析其中存在的连续波动情况来确定原材料的质量稳定情况,进而综合评定检验批原纸的合格情况,进而确定是否继续进货。
此外还可利用对库存量及库存周期的管理来做好对原纸的进货检验。很多中小包装企业由于原纸仓库比较小,本身就限制了原纸的库存量。在实际运作过程中,又忽视了对原纸仓库的有效管理,将仓库的原纸库存量当作“备货”对待,没有做到“先进先出”的仓库管理。习惯于对刚到的原纸经初步的外观检验后,立即投入生产使用,结果导致不断的出现原纸的质量问题而与供应商进行频繁交涉。为了有效解决以上存在的问题,同时又考虑到中小包装企业“现金流”需求快速周转的现状,并合理的降低采购成本与检验成本。可将仓库的“先进先出”管理与进货检验有效的结合起来,让每次进货的原纸先暂放于规定区域(待检区),经初步外观检验合格后,采用科学的抽样方法将样品(原纸筒)投入生产线试生产,及时记录质量情况并与以前的记录进行比较,来确定本批原纸合格与否。经外观检验和生产试用合格的原纸再予以入库,不合格的原纸按不合格品方式进行处理。这样即解决了库存原纸长期不用而导致的质量下降,又实现了对原纸质量的有效控制,何乐而不为呢!