第一个挑战福特制的基本模式的是日本人——丰田公司的大野耐一,这位工业发展史上的第二位伟大的生产经理(非常凑巧的是,给工业社会带来革命性变化三位重要人物分别是:学徒工出身的工程师泰勒、福特公司的生产经理索伦森、丰田的生产经理大野耐一,都是从现场做出来的,而且原理极为朴素。书斋里的管理学家从来没有给工业带来这样重要的变革)。
丰田方式同福特方式一样,基本形式是流水作业。索伦森在放置零部件的仓库上颇费了一番苦心,他的后人发展出来的极端复杂的管理软件系统也是从库存管理发展起来的,然而丰田方式却不需要仓库。丰田方式的生命是“准时化”,就是使需要的零部件按需要的数量、在需要的时刻到达总装配工序的流水线上。
当丰田开始生产汽车的时候,并没有福特那么幸运,因为日本没有对汽车的大量需求,福特为了降低成本开发出来的“少种大量”生产汽车的方式深植于美国社会之中,在日本则水土不服。丰田必须在“多种少量”的情况下开发出降低成本的方法。
身为丰田生产经理的大野耐一受超市模型的启发,实行了拉动式准时化生产(JIT,像超市货架一样,只有被顾客取走货物才给货架上货)。所谓准时化,就是通过流水作业装配一辆汽车的过程中,所需要的零部件在需要的时刻,以需要的数量,不多不少地送到生产线旁边。从而把在物资和财务上给经营管理造成负担的“库存”问题几乎给解决掉了。
但是,汽车有几千个零部件,把它的全部工序加起来,就会得到一个庞大的数字。要使这一切工序的生产计划都保持一丝不乱的“准时性”的状态,那是极其困难的工作。因为造成生产计划出现变动的因素很多,其中估计上的错误、业务管理上的差错、出次品、返工、设备故障和出勤变化,等等。一旦前面的工序发生问题,后面的工序就必定出现停工待料的状况。这时如果不让生产线停产或变更计划,则前一道工序所生产的零部件就会同后一道工序脱节;另一方面,还会发生某些零部件短缺,而仓库里却有一大堆用不上或者不急需的零部件。这样,生产效率就会降低,最后会导致企业效率下降。更糟糕的是,在生产现场的各条生产线上,无法区分正常状态和异常状态。
因此,要满足准时化——将需要的零部件,在需要的时间,按需要的数量供给每道工序——的条件,采用福特制那套管理办法,即生产计划下达到每一道工序,由前一道工序把零件送到后一到工序,无法很好的完成工作。
大野耐一是一个喜欢逆向思维的人,他认为,生产流程就是物的移动,他试着逆向考虑物的传送问题。传统思考方法是“前一道工序向后一道工序供应工件”,在生产线上,材料经过加工成为零件,然后再将零件组装成一个部件,再朝最后的组装线移动的过程中,汽车主体逐步形成。大野耐一倒过来观察生产流程,设想由后一道工序在需要的时刻去向前一道工序领取需要数量的、需要的东西,前一道工序只要生产后一道工序所需要的数量就行了。只要明确提出“某种东西需要多少”,就可以把许多道工序联系起来。于是,大野耐一发明了“看板”(一个写明所需零部件需求数量的硬纸片,不是很多人所理解的展示板,其作用更类似于戴尔的“标签”)来控制生产量:以生产工序的最后一道“总装配线”为起点,开始给装配线提出生产计划;而装配线上用的零部件也改由后一道工序在需要时刻向前一道工序去领取需要的数量、需要的东西,而前一道工序则只生产所需要领取的数量。生产计划只下达给最后的组装线,指示什么时间、生产多少什么类型的车,这样组装线便依次向前一道工序领取所需要的各种零部件;用这种倒过来运送的管理方法一步一步逆着生产工序向上推进,一直上溯到原材料供应部门,并给以连锁性的同步化衔接,这样就可以满足“准时化”的条件,管理工作量变可简到最低限度。
事实上,丰田生产方式是建立在日本人的自律精神之上的理想化的生产方式,这一生产方式美国人理论化、结构化为“精益生产”,但在美国的推广却收效甚微,张西振人为,可能也是水土不服。
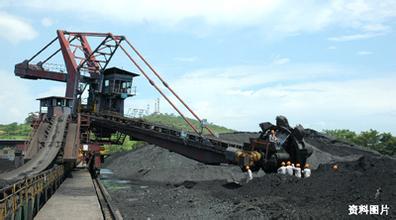