服装企业的烦恼
青岛某日资服装企业接到日本客户80件4个不同型号服装的订单后,开始做生产准备工作。8天后生产线开始正式投料组织生产。仅仅在2个小时后,这80件服装已经被装载到开往日本的飞机上,经过2个小时的旅程,到达日本东京的飞机场。日本客户的运货车早已经等在飞机场,并且迅速装载上这80件衣服,火速赶往客户商铺。2个小时后,这80件不同型号的衣服已经被摆在客户的商铺,等待顾客的挑选。
从开始投料生产、到装上飞机、运抵客户商铺,仅仅需要6个小时的时间,而且这个过程中,产品从原材料到成品、从生产现场到销售现场,跨越了两个国度,足可见这个企业的功力之深。为了达到尽快将畅销的服装运抵店铺,客户承诺:只要能保证按期交出这80件4个型号的服装,可以以较高的价格签单。而这家企业也积极响应客户,按约定的交货期及时交货,满足了客户的要求,日本客户由此决定进一步增加给这家青岛日资服装企业的订单量。
华安盛道管理咨询有限公司在咨询过程中,也曾经服务过青岛的另外一家服装企业。这家企业从接单到交货,通常需要38天的时间,而客户可以承受的交货期是25天。这家企业由于不能按时交货,经常不得不改变交货方式,由海运改为空运,企业为此每年支出空运费数十万。企业的生产部门为了赶上生产交货期,不得不经常加班;生产计划部门也经常抱怨生产订单完成率低,生产系统没有弹性;而业务部门的跟单员更是苦恼,由于不能按时交货,经常遭到客户的抱怨和投诉;人力资源部门抱怨加班费数额不断提高,工资支出超出控制限。这家企业的总经理时常因为漫长的交货期问题焦头烂额、苦恼不已。另外,与交货期相伴而生的生产效率低下的问题、质量水平低、成本居高不下的问题等,也是此企业成长过程中挥之不去的顽症。
服装企业的特点
服装企业所面对的市场具有明显不同于其他企业的特点:
一、交期短
客户一般会在服装畅销时,立即向生产企业发出订单,并且要求在短期内交货,避免由于气候的轻微变化而引起的服装滞销,最后不得不淡季降价促销,或者积压至第二年时销售。淡季降价促销会引起客户利润降低甚至赔本,而积压至第二年销售一般会占用较多的资金,使客户的资金链紧张,甚至断裂。所以客户坚决要求服装生产企业按期交单,从而保证在服装销售旺季获得市场。
二、花样繁多
当前的社会是个性化十足的社会,每个消费者都希望自己所穿着的服装能够彰显个性,甚至希望在全世界不存在完全相同的两件服装。客户总希望店铺中所陈列的服饰花样繁多,能够满足不同消费者的不同需求,并且也希望竞争对手店铺中没有自己店铺中陈列的服装式样。所以客户在和服装企业的业务联系中,提交的订单常常是花样百出。这对传统的服装企业是一个很大挑战。
三、批量小
由于穿着服装的消费者身材各异,客户在订单中均要求大小型号不同数种,且数量较小,以避免造成成品的积压。如在文章开头中提及的80件产品4个不同型号,就是很好的佐证。批量小的订单在服装企业中常常不能被认真对待,甚至在实行以计件制为主的中国服装企业中组织生产时被忽略掉,而可能引起客户的恶性投诉。
服装企业所具备的行业特点,使得满足现代客户的各项需求十分不容易,但这家日资企业为什么能在如此之短的2小时的生产周期内完成生产、按时交货呢?它实行了什么样的运营方式呢?
因为这家日资服装企业已经开展“精益生产”(LeanProduction)变革长达四年,对这种交货期短、价格高的订单已经相当从容,能够保证顺利交货,同时也获得了较高的利润回报。
精益生产方式:打造企业经营优势的最佳武器
精益生产(LeanProduction)是源于日本丰田汽车公司的生产组织管理方式。1990年,美国麻省理工学院教授詹姆斯·P·沃麦克等专家通过“国际汽车计划(IMVP)”对全世界90多个汽车制造厂的调查和对比分析,认为日本丰田汽车公司的生产方式最适用于现代制造企业的一种生产管理方式。在其《改变世界的机器》一书中以丰田生产方式(TPS--ToyotaProductionSystem)为基础提出了精益生产。他们指出“精益生产综合了大量生产与单件生产方式的最佳特征,将成为21世纪标准的全球生产体系”。
这种精益生产管理的基本特征包括:
—实现准时生产。执行在必要的时间(不迟也不早)、生产必要的品种与数量(不多也不少)之生产计划管理产品的生产,其生产管理的指令系统就是Kanban系统。
—实施拉式生产方式。按照订单或顾客的需求,利用kanban指令系统使生产指令信息从生产线的最终工序(或作业)逆着物流流动的方向向前一道工序传递。
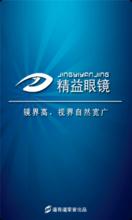
—连续优化生产流程,通过培养多面手员工由生产作业者完成质量检测,保证及时发现质量缺陷,不断改进流程与作业,消除生产过程中一切不能附加价值的活动。
—实现公示管理。
—按照顾客价值对供应商进行管理,以“零库存”为奋斗目标实现准时供货,努力降低公司的库存。
—实施人与技术结合的自治管理,发挥小组的集体作用。
实践证明,与大量生产方式相比,日本所采用的精益生产方式的优越性主要表现在以下几个方面:所需人力资源——无论是在产品开发、生产系统,还是工厂的其他部门,与大量生产方式下的工厂相比,最低能减至1/2;生产过程的在制品库存——最低可减至大量生产方式下一般水平的1/10;成品库存——最低可减至大量生产方式下平均库存水平的1/4;工厂占用空间——最低可减至采用大量生产方式下的1/2;新产品开发周期——最低可减至l/2或2/3;产品质量——可大幅提高。
2005年,精益生产的原型企业——丰田汽车公司由于其长期的与众不同的经营获得了历史上最高的经营业绩——2005年的净利润,比欧美三大汽车公司(通用、克莱斯勒、福特)的利润总和还多!目前推行精益生产的企业已经遍布世界各地,并且已经取得了非凡的成果,如电脑业巨擘——美国戴尔公司,其完全以订单需求拉动的运营方式使得其稳稳居于电脑行业老大的位置;中国海尔在中国各地建设的工业园,并不单单是为了自己的生产建设的,海尔的供应商大部分均入驻海尔工业园,为海尔的多系列产品建立了优秀的精益供应链。
中国的潜力:精益让您更强
经过上世纪八九十年代的冲刺,依靠各地兴建的经济特区、经济开发区,中国已经成为世界经济中举足轻重的力量,中国的很多官员更愿意称中国为“世界工厂”。最近的一项统计显示:2006年,中国500强中,制造业有278家,其利润占28.7%,这说明制造业仍为我国经济的主导。但是中国真得已经成为“世界工厂”了吗?
目前在中国的各个制造业企业中,运用的各项管理技术,仍旧为美国、欧洲、日本的多年经济发展的产物,如IE、SPC、5S、TPM、PDCA等,中国作为“世界工厂”,尚未诞生如上类似的“经典的管理技术”,而引进多年的ISO9000族标准,尚未成为引导企业质量提升的重要工具,更多的仅仅作为一个基础质量管理形式。中国的制造企业中诞生的各项专利,虽然很多,但在世界专利中不过是沧海一粟,并且大多数也没有成为日本、欧美等企业购买的商品。以彩电产品为例,其中大多数专利都是美国人的,中国的彩电制造企业不得不为每一台彩电产品向美国交纳数额不菲的专利费。实际上,中国的很多制造工厂,仍旧停留在以较低的人力成本为基础的经营中。
进入21世纪,经济的全球化和区域经济的一体化,以及国际产业的战略转移,使“十一五”期间制造企业的优化升级,成为极其迫切的任务,同时,WTO的全面解禁,使中国制造业企业不仅仅面对本土企业的竞争,也要面对大型跨国巨企的竞争,这对于中国管理底蕴和技术底蕴并不丰厚的制造企业可谓压力巨大。“十一五”期间,制造企业要适应经济全球化和区域经济一体化的要求,顺利承接国际产业转移,就必须学习世界经济巨头的先进管理经验——精益生产,实施变革,成功实现战略转型。
目前已经成功推行精益生产的中国本土企业包括海尔、海信等著名品牌企业。通过推行精益生产,这些企业已经形成自己企业的核心竞争力,如海信的“资金周转”、“经营革新”,成为其他企业无法追赶的行业楷模和金牌企业。中国制造企业必须以他们为榜样,脚踏实地,认真学习精益管理,结合本身实际,实施变革,彻底从交货期、较低的质量水平、较高的成本、不具竞争力的价格怪圈中解放出来,让自己更强,真正的把中国变为“世界工厂”。