很多时候,很多人将精益生产与六西格玛进行对比,寻找而者之间的共同点和区别。本人以多年优秀日资公司的精益生产经验,以及实施六西格玛黑带的实践,再次谈谈两者之间的关系。
一.历史比较
1.精益生产历史
20世纪初,从美国福特汽车公司创立第一条汽车生产流水线以来,大规模的生产流水线一直是现代工业生产的主要特征。大规模生产方式是以标准化、大批量生产来降低生产成本,提高生产效率的。这种方式适应了美国当时的国情,汽车生产流水线的产生,一举把汽车从少数富翁的奢侈品变成了大众化的交通工具,美国汽车工业也由此迅速成长为美国的一大支柱产业,并带动和促进了包括钢铁、玻璃、橡胶、机电以至交通服务业等在内的一大批产业的发展。大规模流水生产在生产技术以及生产管理史上具有极为重要的意义。但是第二次世界大战以后,社会进入了一个市场需求向多样化发展的新阶段,相应地要求工业生产向多品种、小批量的方向发展,单品种、大批量的流水生产方式的弱点就日渐明显了。为了顺应这样的时代要求,由日本丰田汽车公司首创的精益生产,作为多品种、小批量混合生产条件下的高质量、低消耗进行生产的方式在实践中摸索、创造出来了。
1950年,日本的丰田英二考察了美国底特律的福特公司的轿车厂。当时这个厂是世界上最大而且效率最高的制造厂,每天能生产7000辆轿车,比日本丰田公司一年的产量还要多。丰田英二对这个庞大企业的每一个细微之处都做了审慎的考察。他在写给丰田总部的报告中说:“那里的生产体制还有些改进的可能”。
战后的日本经济萧条,缺少资金和外汇。怎样建立日本的汽车工业?照搬美国的大量生产方式,还是按照日本的国情,另谋出路,丰田选择了后者。日本的社会文化背景与美国是大不相同的,日本的家族观念、服从纪律和团队精神是美国人所没有的,日本没有美国那么多的外籍工人,也没有美国的生活方式所形成的自由散漫和个人主义的泛滥。日本的经济和技术基础也与美国相距甚远。日本当时没有可能全面引进美国成套设备来生产汽车,而且日本当时所期望的生产量仅为美国的几十分之一。“规模经济”法则在这里面临着考验。
丰田英二和他的伙伴大野耐一进行了一系列的探索和实验,根据日本的国情,提出了解决问题的方法。经过30多年的努力,终于形成了完整的丰田生产方式,使日本的汽车工业超过了美国,产量达到了1300万辆,占世界汽车总量的30%以上。
制造、电子、计算机、飞机制造等工业中。丰田生产方式是日本工业竞争战略的重要组成部分,它反映了日本在重复性生产过程中的管理思想。丰田生产方式的指导思想是,通过生产过程整体优化,改进技术,理顺物流,杜绝超量生产,消除无效劳动与浪费,有效利用资源,降低成本,改善质量,达到用最少的投入实现最大产出的目的。
日本企业在国际市场上的成功,引起西方企业界的浓厚兴趣,西方企业家认为,日本在生产中所采用的方式是其在世界市场上竞争的基础。80年代以来,西方一些国家很重视对丰田生产方式的研究,并将其应用于生产管理。首先推广应用的是美国的通用汽车,接着其他的汽车公司和其他产业的公司也开始实施精益生产。
随着各国对精益生产的理解和应用,加之由于市场的快速变化,迫使企业生产需要做出快速响应,这样,在精益生产的基础上,发展了敏捷制造(AM)思想,敏捷制造系统是以精益生产的设备,全面生产维护(TPM)以及设备各组合部之模块化为基础建立起来的高柔性生产系统。敏捷制造能对顾客的多样化和个性化的需求做出快速的反应,以满足顾客需求。目前,国际上一些专家把敏捷制造的优势大致归纳如下:
①由于快捷生产系统各组合部分都尽量模块与标准化,因而可以易于安装和重组,以减少设备的制造时间,同时也缩短了设备交货期;
②降低了与所加工产品的关联程度(可周期性设计);
③提高了生产单元的标准化程度;
④简化工具、夹具的支撑点;
⑤可以生产样品,试生产及正式批量生产以适应产量变化;
⑥可以在购置设备时逐步投资;
⑦设备使用时具有更强的柔性,可转换性也增强;
⑧可以低成本改造设备,以适应产品转型;
⑨易于转产其他产品。
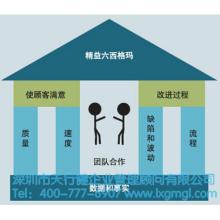
1990年,精益生产(LeanProduction)的英文概念由美国麻省理工学院中的国际汽车组织(IMVP)在经历了5年的汽车行业调查后而提出的。而实际上早在六七十年代日本的丰田汽车公司已经在这方面进行了研究与实践,提出了所谓的“丰田生产方式(TPS)”,这实际上就是精益生产的雏型。在90年代初各先进工业国纷纷研究精益生产:德国亚亨大学在原来研究的“独立制造岛”的基础上提出了精益屋的模型,其它如英国、芬兰、瑞典等国的企业亦成功地进行了精益改造,尽管所冠名称不一定就叫精益生产,但它本质上就是精益生产,而且也从汽车业发展到了其它行业。美国在20世纪90年代中,也在航空业中开始了飞机首创计划(LeanAircraftInitiative)的研究。这个研究的中心也是在麻省理工学院宇航系,斯隆管理学院和机械系则在精益理论上作了研究。
当《改变世界的机器》面世以来,精益生产便得以在全球广泛传播和被光为学习。紧接着,《精益思想》便说明了怎样实施精益生产。今井正明的《改善》以及《现场改善》也讲解了精益生产的思想体系和实施方法。大野耐一的《丰田成功经营的精髓》更是详细说明了精益管理体系的思想来源和发展。
2.六西格玛历史
在70年代,Motorola面对日本严峻的挑战,其主席Bobgalvin决定在品质上改善,来迎战日本高品质的挑战。在1981年,他要求其产品必须在五年内有10倍的改善。于1987年,Motorola建立了六西格玛的概念,基于统计学上的原理,六西格玛代表着品质合格率达99.9997%或以上。换句话说,每一百万件产品只有3.4件次品,这是非常接近“零缺点”的要求。六西格玛计划要求不断改善产品、品质和服务,他们制定了目标、工具和方法来达到目标和客户完全满意(TotalCustomerSatisfaction)的要求。在过程上他们提供了黑带(BlackBelt)和绿带(GreenBelt)的有经验工程人员和顾问推行整个计划,并成为品质改善的先锋。
Motorola的“七步骤方法”(SevenStepMethod),“不断改善”(ContinuousImprovement)和客户完全满意(TotalCustomerSatisfaction)都是取材自TQM(全面优质管理概念)。他们提出新设计文化,简化生产步骤,采用机械臂、通用网络等来达到他们5“九”(99.999%)品质要求。
三年后该公司的六西格玛质量战略取得了空前的成功:产品的不合格率从百万分之6210(大约四西格玛)减少到百万分之32(5.5西格玛),在此过程中节约成本超过20亿美金。随后即有德仪公司和联信公司(后与霍尼维尔合并)在各自的制造流程全面推广六西格玛质量战略。但真正把这一高度有效的质量战略变成管理哲学和实践,从而形成一种企业文化的是在杰克?韦尔奇领导下的通用电气公司。该公司在1996年初开始把六西格玛作为一种管理战略列在其三大公司战略举措之首(另外两个是全球化和服务业),在公司全面推行六西格玛的流程变革方法。而六西格玛也逐渐从一种质量管理方法变成了一个高度有效的企业流程设计、改造和优化技术,继而成为世界上追求管理卓越性的企业最为重要的战略举措,这些公司迅速运用六西格玛的管理思想于企业管理的各个方面,为组织在全球化、信息化的竞争环境中处于不败之地建立了坚实的管理和领导基础。
六西格玛改善方法论的典型步骤是D-定义、M-测量、A-分析、I-改善、C-控制;而用于研发设计的典型步骤是D-定义、M-测量、A-分析、D-设计、V-验证或I-识别、D-设计、O-优化、V-验证。
其后,六西格玛在GE取的成功更是将其推向了学习热潮。
◆从历史来看,精益生产有着近70年的历史,从而形成了至今完善的管理系统。Motorola在提出六西格玛概念至今,也有了20年的历史。
二.思想系统比较
1.精益生产的起源历史环境就注定了它是一种系统的管理方法。从50年代丰田英二参观了福特当时世界最大的汽车生产厂后,“价值”二字就变成了精益生产的核心。
在希望“工厂每天的每一个工作都在创造价值”的思想支撑下,七大浪费(超量生产、不良品、库存、搬运、多余的动作、等待、多余的工序)被提了出来,而此七大浪费,简单到可以使一线员工很容易就理解其工作中的浪费,而公司高层管理者,则又可以从战略层面来进行消除七大浪费的活动。
丰田公司为了使自己的小工厂能快速应对市场的需求和反应,从50年代起,就坚持实行按照客户定单来生产,这便是后来拉动生产的思想起源。只有按照客户定单从事生产活动,才不会有多余的库存。当供应商被要求进行也按照这样的方式进行生产时,战略供应链从这个时候便开始建立起来了,直至后来发展到让客户参与设计的管理活动中来。
为了消除七大浪费,于是JIT(JustInTime)的生产方式被提了出来,并在丰田得以成功的运用,快速换模并是JIT里面诞生的一个有效工具。JIT在消除库存(含在制品)和生产平衡方面有着与传统流水方式截然不同的效果。为了改善质量和降低成本,QCC活动开始在工厂进行,并取得了很好的效果,当QCC被全面推广,应用到操作员级别的时候,全面质量控制(TQC)和零缺陷(ZD)运动被全面展开,品质管理的七大手法也在这个时候被得以运用到极致。随后将TQM的思想又运用到提高设备效率之上,TPM在日本电装取得的成绩使TPM又成为了精益生产系统中一个强大的管理工具。
整个精益生产的思想都是围绕着“价值”来思考,“价值流设计”是在八十年代被丰田公司用来进行供应链改善的工具。以“价值流”为核心的精益生产方式在工厂运营管理、销售和供应商管理方面整合成为强有力的战略供应链。
而支撑精益生产得以不断创新和延续的一个核心便是“持续不断的改善”,在日语里常用“Kaizen”一词来表达这个意思。
正如丰田社长渡边捷昭所说“丰田公司内部并不是提倡用数字和条条框框进行管理的。因为,丰田毕竟是从日本发展起来的,管理过程中的量化流程是西方的东西,我们更强调一种思维,即持续研究和创新的思维。”
2.六西格玛的思想是通过统计的方法,按照一定的步骤对问题发生的可能原因进行分析,也从统计的角度,对发生频度高,影响大的因素进行改善。为了使六西格玛能被广泛学习,它强调将专业的统计作为一个黑匣子封闭起来,要求改善人员只要遵循一定的步骤进行即可。
六西格玛管理是:“寻求同时增加顾客满意和企业经济增长的经营战略途径。”即:
在提高顾客满意程度的同时降低经营成本和周期的过程革新方法;
通过提高组织核心过程的运行质量,进而提升企业赢利能力的管理方式;
在新经济环境下企业获得竞争力和持续发展能力的经营策略。
从六西格玛的实施步骤来看,它只一个有着一定固定步骤的改善工具。作为一种可以容易学习的工具,它强调改善的财务效益。
◆从思想系统来看,精益生产是一种综合的管理思想,设计企业内部的流程以及企业外部的供应商和客户组成的供应链系统,为了使系统连续地创造价值,精益生产不断创新出很多管理工具,如QCC、TQM、TPM、VSM等等。它强调包括供应商和顾客在内,以及企业内部一线员工的共同改善活动来消除整个供应链上不增加价值的浪费。它不强调改善的大小,也不把财务效益作为改善的重要标准,它视企业的经营活动为一个“系统”,任何细小的不良都将影响系统的运作效率。
六西格玛作为一个有着相对固定模式的改善工具,它是强调通过寻找一些难点,按照既定的步骤进行改善,相对而言,它缺乏对经营活动的的整个价值链进行优化的系统思想。它将财务效益作为衡量改善效果的重要指标。这使得六西格玛在实施过程中出现一味地追求财务效益和忽略了对流程和价值链本身的改善。虽然它将统计知识作为一个封闭的黑匣子来处理,但由于本身的核心也是统计知识,所以它很难运用到操作员工的层次。
三.实施过程的比较
1.从实施的基本步骤来看,精益生产并没有固定的模式,很多企业从5S做起,因为5S实施成功后,可以为精益生产的其他管理实施做很好的铺垫。也有的企业直接就从价值流图析(ValueStreamMapping)开始,或者先实施一些小范围的QCC活动。它是根据企业自身的管理水平来决定需要实施那些精益管理系统,只要围绕“价值流”来进行实施就是它的目的。
一个企业在进行了系统的精益生产培训后,便可以在企业各个地方实施,上到高层管理者,下到基层员工,都可以同时进行。由于没有固定的模式,以及精益生产本身是一个复杂的管理系统,这使的它的真正成功实施在很多企业难以实现。而一旦实施成功,它便成为企业的一种核心力,短期之内不会伤失,一般企业要完全实施成功,起码需要8年左右以上的时间。
它不强调改善的大小,而强调“只要是改善就是好事”。它通过简单的改善工具进行改善,这使的精益生产可以很容易推广到基层的员工。本人曾看到一个公司的一线操作员(高中学历),在自己的生产记事本上,运用柏拉图分析过去一周内自己所犯的作业错误,并在后面简单写出了一些改善措施。该企业的员工素质达到这样一种水平,可以想象,这个公司的整体运营管理该是什么水平。该公司是行业内的标杆企业,集团全球内效益和效率最好的公司。如果我们的企业也达到这样一种水平,可以想象会产生什么样的效果呢?所以精益生产的实施过程会变成一个愉快的,不断见到改善效果的过程。
六西格玛有固定的实施步骤,强调按照步骤进行,所以推行起来相对容易,另外,在学习此改善工具方面,相对而言较容易。由于大量的统计知识被运用到里面,它的实施很难被推广到企业基层员工面。另外由于强调财务效益,它的实施过程很多公司最后也变成了一个“为了六西格玛,所以六西格玛”的形式过程。这也使得六西格玛在很多公司并没有取得真正的成功。
综上所述,精益生产是一个复杂的管理系统,它是一种管理思维的集合。虽然复杂,却也有着很多简单的改善工具,它可在基层面也得到很好的实施。在改善方面,它的速度更快,但由于系统的复杂性,所以在实施上也较难,如果没有专家辅导,则容易做成形式,很多公司的5S到最后就变成了大扫除活动就是一个明显的例子。而六西格玛是一个高级的改善工具,模式固定,实施较容易,但它缺乏对流程和供应链进行系统性改善的管理思想。它的实施需要参与人员具有一定的知识水平,这限制它在企业内进行大范围的推广。