一、计划环境
运输系统
运输过程是供应链中很重要的部分,这一过程实现了企业和其供应方、企业和其需求方之间的货物流动。运输、生产和库存持有的各个过程的一体化观念正是现代供应链(SCM)概念的特征。
一个运输系统的结构合适与否主要取决于单次运输批量的多少:大的运输批量可以用整车或整集装箱等运输单位直接从货源地运送到目的地,小的运输批量则必须放在运输网络中整合运输,可能要转运一次或若干次,运输过程在转运点(transshipment points,TP)被打断。小批量运输的有效整合可以通过物流服务提供商(logistics servlce provider,LSP)或我们称第三方物流来实现,它能够将来自许多发货人的货物整合起来。
运输流量的整合降低了运输成本。因为在某条路线上某种运输工具单程运输的成本与其载重几乎是无关的,所以充分利用载重能力显然是有利的。而且,每载重单位的相对成本随着运输工具载重量的增大而减小。但是即便通过有效整合,如使用一个LSP,实现了货物满载,小批量也会造成相对高的成本,因为整合运输要求绕路到不同的装运地、额外的停靠站及转运地.
供应链中发生的运输过程如下:
1、从外部供应商或从自己远方的工厂向生产地的原材料供应,这两种情况从物流的角度来看是没有分别的。
2、从工厂向消费者的产品配送。配送系统因产品类型不同而不同:
-投资性物品,,如工业用户的机器或设备,这类货物在某条运输线上只运输一次或有数的几次。
-原材料也是向工业用户运输,但它很有规律也经常出现在相同的运输线上。
-生活消费品向批发商或零售商运输,常常以很小的订单批量(一些行业平均每单低于100kg),需要进行整合。
要注意的是,物料从工厂到工厂的运输既是供应方配送功能的一部分,也是接货方采购功能的一部分。制定运输计划一般是供应方的责任,但也有一些重要的例外情况,比如在汽车行业,制造商控制着来自其供应方的运输。在这种情况下,运输计划由采购方制定。
物流服务商LSP可以在其自有的网络中整合若干个“托运人”的运输流,它们分别发生在不同的供应链中,于是物流服务商LSP就会负责规划怎样进行运输,即用什么运输工具,走哪条路线。但是,有关运输订单内容的决定,即每批货物的数量、起始地、目的地等,仍然是托运人APS系统的任务。但是,一个物流服务商LSP将所有其他托运人的货物流通都包括在自己的APS系统之内是个挑战。因为其他的货物流对运输成本是有影响的,应该通过恰当的运输成本函数来考虑其影响。
配送系统
一个典型的生活消费品制造商的配送系统包含着许多产品从若干个工厂向大量消费者的流动。按库存生产的产品首先根据预测运送到各个配送中心(DC),随后消费者订货的交付可以通过以下配送途径实现:
一个订单的货物可以直接从工厂或DC运送到消费者处。这种最简单的分拨方式只对那些能使运输工具满载的大订单有效。小订单可以用联合运输驹方式从工厂或DC运送到不同的消费者手中。小批量运输的更强大的方法是通过从DC到TP的联合运输及从TP出发的短途递送实现的。
生产所用的原材料的运输,即使是由供应商的控制的,绝大多数也都直接运输到工厂。最近有一个关于标准原材料供应的观念:供应商管理库存(vendor managed inventory,VMI),即供应商决定向客户运输的时间和数量,但是必须保证客户的库存保持在允许的最小库存量和最大库存量之间。在这种情况下,客户的仓库具有和DC相同的功能,于是VMI供应的计划就类似于DC补货计划。
采购物流系统
如果一个制造商控制来自供应商的原材料运输,那么它能够利用各种物流理念,这些理念中运输网络的结构和装运频率都有所不同。对于同一家工厂不同种类的原材料运输可能同时使用不同的物流理念。以几天到几星期间隔的循环采购(cyclical procurement)能够把运输量组合成更大的运量.但会给接货工厂带来周期库存。至少每天都装运的JIT 采购(JIT: Just in time procurement)能避免原材料经过仓库输入,取而代之的是要增加一小段时间的缓冲区。如果原材料的送达和生产进程是同步的,那么原材料可以马上放到使用它们的生产线上,这种情况叫做同步采购(synchronized procurement )或顺序同步(JIS: Just in sequence )
现有的有关采购的运输理念如下:
1、从供应方直接运输(direct transports)适合于循环供应,需求量非常大,这种运输方式也适合每天供应的模式。只有当距离很短时,直接运输才可能用于满足同步采购的需要。
2、一个地区性的物流服务商LSP在指定区域内集合来自所有供应商的在途原材料,在转运点TP集中并整车运输到接货的工厂。这种理念支持频繁供应,甚至频繁到每天供应,即便供应商距离很远,运输量又很小也同样适用。如果路线连接的合适,还可以用铁路运输来代替货车运输。
3、离接货工厂近的物流服务商的仓库适合同步采购:物流服务商LSP负责通过同步运输来满足接货方短期的要求。供应方必须通过合理的运输安排将库存量保持在最低和最高水平之间,这就如同在VMI理念中提到的一样。
与APS系统的其它模块集成的联系
常见的说法运输和配送计划代表着一系列与其他APS模块重叠的功能。恰当地说,运输计划是一个普通的术语,如前所述,它可以出现在采购方方面,也可以出现在配送方面。而且,它的含义由作为供应链主计划模块(Master Planning)一部分的中期运输过程的综合计划延伸到了最短期的计划:已知客户订单的交付计划是需求满足模块(Demand Fulfilment)的最后一步,而认库存发出订单是ATP功能的一部分。和运输配送计划通过下列数据流和其他模块相联系:
战略网络计划(SNP:Strategic Network Planning)模块提供运输网络的结构,即
-工厂、供应商、DC和TP的地址;
-运输模式和可能路径;
-供应商和客户在各地区之间的分配及各地区在各工厂、DC、TP之间的分配;
-物流服务商LSP的使用。
供应链主计划(Master Planning)模块决定了:
-汇总每条运输线上的运量;
-工厂仓库和DC的季节库存的增加和减少。
其中,第一点也可以看作中期运输计划的一部分。为了保证第二点的灵活性,不应该把总运输量当作像短期运输计划中那么严格的指令。计算总运输量主要是为了提供合适的资源和能力并考虑不同运输线的运输时间。但是,在有多个运输来源的情况下,如一种原材料可以从几个供应商处订购,或一种产品在几家工厂都生产,或一个客户的需求可能由几个DC供应.所以总运输量就反映主计划的一个总体概念。那么它们就代表着短期运输的重要指导方针,例如可用来衡量来自各地的需求在总需求中所占的比例。
需求计划(Demand Planning)模块也为运输计划提供基本的数据:
-需交付的客户订单;
-DC的需求预测;
-DC的安全库存。
运输计划(Transport Planning)与生产排程(Production Scheduling)的关系是双重的:
一方面运输计划可以决定:工厂运输计划出发时刻的净需求是生产计划的输入。 另一方面,生产排程模块提供:计划中的和已发出的生产订单作为运输计划的输入,用于有关出货的超短期决定。
中期计划任务
交易双方定期运输的频率(frequency)是一个关键的成本因素。它是分拨方面DC补货和采购方面原料供应的一个中期决策变量。目标是要权衡运输成本和库存量,使其综合结果最优,由此得到的频率就为装运数量的短期决策设定了目标值。而且,它还决定了必要的运输批量库存,这应该是主计划模块以及生产计划与排程模块中最小库存水平的一部分。 .
交付客户订货的配送路径(distribution paths)的选择常常遵循中期决策确定的一般规则。这些规则大多基于对订单规模的限制,如低于30kg的订单用包裹服务,低于1000kg的从DC通过TP递送,低于3000kg的直接从DC递送,更大规模的直接从工厂递送。
就采购方面而言,原材料的供应安排:直接递送或通过地区TP或LSP仓库递送,必须基于中期的决策。这些决策都与供应频率相关。
决定供应链中每条运输线上的汇总运输量是一项基本的中期计划任务。就配送方面而言,这是运输和配送计划中的配送计划。但是为了保证供应链中生产和运输流的紧密协调,这项任务应该在主计划模块中进行整合。
短期计划任务
短期运输计划一般每天都要进行,计划的时间跨度从一天到几天不等。这项任务也叫做部署(Deployment),包括以下决策:
必须决定当天要装运的数量,这在配送系统中是为了补足每个DC和VMI客户在各项产品上库存,而在采购系统中是为了保证各项原料的供应。关于装运频次和汇总运数量的中期决策能够影响这里的装运数量。
运输工具装运任务会将同一条运输线上各项货物的总运量调整为一整车或它的倍数。如果像在这些情况下常见的一样,运输工具只用于我们所考虑的供应链,那么它与DC补货及物料供应都相关。
对于向客户交付,交付数量是客户订单里规定的,但是可能有多个交付来源和多个路径。这些选择一般遵循主计划数量和配送路径的一般规则。
对于按库存生产的产品,部署功能与ATP功能密切相关:客户希望产品能够在承诺的非常短的提前期从库存中交付过来,提前期大多在24h和72h之间,包括必要的订单接收、装载、运输等环节。如果当天收到的订单中某项货物的总量超过库存量,那么订单就不能按照标准原则处理了,而必须对以下措施做出决定:
-寻找其他可供选择的货物来源满足部分订单;
-如果客户同意,用现有的其他产品代替缺货产品;
-减少用于DC补货的产品数量,DC补货往往和客户争夺从工厂运来的货物;
-减少一些客户订单的订货量,延迟交货或取消订单:这种下下之选通常也不能完全避免。即便必须做此决定的订货量只占非常小的比例,也要谨慎的选择相关订单。
运输调度排程:(vehicle scheduling)包含两个不同的任务:
-用小型货车从TP运送小批货物安排短途运输,
-安排从工厂到DC,从DC到TP及从工厂、DC到客户直接运输的货车。
对于短途运输和工厂、DC、TP间货车流动的常规线路安排,可由固定地区较长期的计划再次对以上措施作出决定。但是,除了运输工具仅供所考虑的供应链专用的情况,运输调度安排是典型的由物流服务商LSP负责的任务。至于LSP为所考虑的供应链之外的客户提供运输时,这是提高运输过程效率的一种做法,则运输调度安排不能整合到高级计划中去。
二、建立模型
运输与库存
运输计划对供应链中的库存有着很大的影响。它直接创造了运输批量存货和在途库存,并影响着必要的安全库存量。运输批量库存是由运输频次的决策决定的,目前APS已经能支持涉及库存的中期运输计划的优化。因为一些普通的计划模型所得出的频次和库存也是其他APS模块很重要的数据。在设定这些数据时,应该考滤以下关系,如有关联合运输和库存计划的情况。
单一运输线,单一产品
最简单的情况就是将某种产品在A地的生产过程与B地的消费过程联系起来的运输过程。在生产和需求都连续而稳定的情况下,最佳的运输方案就是每批运量相同的规则运输。
单一运输线多种产品
现在,有多种产品i在A处生产,在B处消费,生产和消费都有相应的稳定比率d,持有成本是hi。如果每批的运输成本F仍是固定的,那么一起装运所有产品总是最优的选择,
即便需求有波动,在某次运输中,最优的选择是将接下来的周期有正净需求量的所有产品一起运输。
运输手段的选择
主要是时间和成本的最优选择.
1,公路
2,铁路
3,水路
4,航空
5,管道
最小化Min:运输成本+交货期滞后成本, (运输手段变化成本+运输中库存管理的成本+早到引起的库存成本+缺货罚款)
配车问题VRP
主要用基因算法和探索法
1,箱柜包装问题:达到卡车或集装箱使用优化.
2,集中覆盖问题:选择的路线有关的总成本最小
3,设施配置问题:物流网点最佳配置
4,巡回推销员问题:最短距离(时间)巡回路径问题
5,日程安排问题:实现生产日程最佳化
运输模式转换(联运)优化
1,在所给的运输其间范围内,货物可以组合成批运输.
2,考虑承运者的时间范围(如铁路运行时间)
3,以单个承运者所花费的总运输成本最小化目的.
更为复杂的是:把网点库存最佳配置问题与模式转换问题同时处理,能把往点位置、订单间隔及运输路线各自最优化。
一般情况
有关稳定需求的假设对于生活消费品可能是真实的,而生产原材料的消费和产品的生产大多是以批计的。不同供应网络中的生产和运输计划对库存的影响,并强调了独立计划和同步计划的区别。运输和物料消费的同步是JIT采购的基本思想。生产和配送同步是按订单生产和按订单组装的原则。按库存生产是生产与客户订单的运输不同步。
但是从工厂到远距离DC或VMI客户的运输可能与按库存生产同步。然而当有多种产品在共同的生产线上循环生产并配送到几个目的地时,同步可能很困难或不切实际。在同步计划的情况下,生产批量是运输量的整数倍。请注意生产率比需求率大,是因为生产线在所描述的批次之间的间隔内还必须生产其他产品。很明显,同步计划降低了总体平均库存水平(包括工厂的和DC的)。
运输和安全库存,在按库存生产产品的配送系统中,是否保证一定的服务水平所必需的安全库存,决定于从工厂到DC的运输策略:在强大的推动对系统(push system)中,任何生产批次都立即配送到DC。一种修正的做法是在工厂的仓库中保留一定量的中心安全库存,用来应付一些DC将面临的库存短缺。在拉动式系统(pull system)中,当每个DC库存量达到给定的再订货点时,就激发了运输。在推动式系统中,中心控制需要每个DC有关需求和库存情况的总体信息。而在拉动式系统中,总体信息同样能改进瓶颈处的库存分配。在APS中,这样的总体信息应该在整个供应链共享.
推动式系统符合同步生产和配送的情况,因而通常要求保有较少的周期霪亨,但通常要求有较高的总安全库存或更频繁的DC之间的交叉运输。DC甜:安全库存必须能应付运输提前期内当地需求的不确定,而系统总安全库存⊥页能应付生产提前期和周期内总需求的不确定。在生活消费品的配送系统=,因为DC的库存一般每天都要补货,运输周期通常很短,但是如果一条三±线上生产多种产品,那么生产周期可能持续几周到几个月。因此,系统女全库存的计算应该基于周期盘存模型,盘存周期与生产周期相同。
分配
分配的主要任务是让短期需求和下一天或几天内可获得的、预期的库存匹配。因为持有库存的物品来源地(工厂、供应商)通常与需求地(DC,消费者)不是同一个地方,所以必须决定从哪个来源地向哪个需求地运输及运输多少。 '
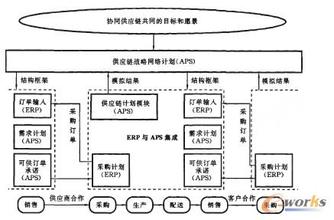
网络流模型
这项任务可以建模为一个网络流问题,所需数据如下:
货物来源地S的库存量
需求地D的需求量
从来源地到需求地的单位运输成本;
决策变量:从S到D的运输量X。
这是一个特殊的线性规划(LP)问题,可以扩展到多个产品和运输能力限制的情况。事实上这是从整个供应链的主计划线性规划中抽取出来的,仅限于运输过程和一个更短的时间范围。很容易将这些整合到一个APS系统中,大多数APS供应商都能提供这种功能。接下来,我们考虑单次运输发出的更详细的情况,这在某些情况下可由上述模型来支持。
已知客户订单的交付
在按订单生产的情况下,在预定的时间完成订单是生产计划与调度安排的责任。分配只能处理那些完成的订单,装运量是由客户订单决定的。
在按订单生产的情况下,同一库存要满足许多客户订单。如果每个货物来源地的库存都能充分满足向各订单的正常分配,所有的订单量就都可以发出递送。
另外,必须实施应付缺货的ATP决策。如果有几个货物来源地的库存总量都很充实,就可以进行再分配,通过货物来源地之间的转运或直接将某些客户订单从正常货物来源地再分配到其他货物来源地。后一种方法更快也更廉价,特别是在客户临近相关货物来源地交付区域之间的分界线的情况下。虽然这在只进行地区性控制的常规配送系统中是很困难的,但在拥有总体信息和分配的中心控制能力的APS系统中很容易实现。
要应付由所有客户争夺某项货物库存引起的库存短缺,最佳的方法组合是由上述的网络流模型决定的,以下是几点解释:
-每个客户在模型中都是一个需求地;
-除了有库存量的真正地点,货物来源地地址包括其他可能方法,特别是库存不限的“货物来源地”,代表订单的减少或取消。
-成本包括延迟交货、客户订单的减少或取消的惩罚,决定于客户的优先权。
DC的补货和采购 ∵
补货和采购的装运量都不是由客户订单决定的,而必须由需求计划得出。而且,计算需要预先清楚每对关系的运输周期(transport cycle time)的详细清况,每次运输的净需求是:在接下来的运输周期和运输提前期内目的地的需求预测+目的地的安全库存/目的地可获得的库存。
在拉动式系统中,如果所有目的地对应的货物来源地都有充实的库存,那么装运量就与净需求相等。运输量可能按汽车装运过程做修正。如果货物来源地的库存不充足,就采用“公平分配”原则向各个目的地分配,这一原则要考虑到每个目的地的需求和库存情况,因此需要总体信息和中心控制。公平分配的基本思想是平衡不同的需求地的库存,使得所有需求地在货物来源地(如生产批量)新的供应到达前的期望服务水平相同。如果当地的库存包括在分配程序内,可能导致的结果是:对一些目的地,分配所得比可得的库存量小,表明库存必
须通过横向转运来移动。
如果网络中的每个节点只由一个固定的货物来源地供应,那么配送需求计划(Distribution Requirements Planning,DRP)就可用于将净需求向上游传递。它是MRP需求计算向配送网络的延伸,并像MRP一样能够将分时间段的动态需求和节点间的提前期考虑进去。
在推动式配送中,供给到达货物来源地后都能按公平分配马上配送到目的地。假设运输提前期较短而货物来源地供应周期较长的情况下,在货物来源地保留一定的中心安全库存是有利的,这样可以在稍后按最新的公平分配原则配送。
在缺货的情况下,DC补货数量的确定也能够和客户订单的交付一起整合到网络流模型中,这时DC作为具有上述净需求的需求地。
运输装运
运输量都是对每个产品分开计算的,而没有考虑按适当运输单位(如整货盘)联合装运多种产品。联合装运是运输装运的任务,从确定运输量开始,到将这些运输量按运输工具的能力整合。既然运输量代表净需求,那么它只能增加,但通常需求的计算能给出低于要求数量的最小运量。其上界是为装运而准备的库存。运输装运包含以下几步:
-将每种产品的运输量凑整为整个运输单位(如货盘);
-调整联合运输的量,即单个产品数量的总和,以使运输工具满载,这些运输工具最终
都是从给定车队中选出的。
-两个步骤必须考虑最小运量和现有库存量,在这些限制之下,第二步应该努力平衡产品增加(或减少)的比例。
运输调度安排
运输调度安排对于高级计划的重要性比较有限。因此,由于大量的关于运输调度安排的文献、模型和算法,在这里就不再讨论这个问题了,可以参考有关文献回顾。大多数文献都涉及到起点和终点为同一仓库的往返运输安排。这种情况的例子有从转运点TP向消费者递送小规模的订货或通过地区物流服务商从供应商搜集小规模的原料订单。已开始研究拖车运输的调度安排,这种情况发生在工厂到DC,DC到TP之间的,直接向消费者交付的和采购运输中。
摘自APSS协会《研究APS系统的运输和配送计划的白皮书(3)》