最近,有些顾问问我,参观工厂现场主要看什么?实际上,主要留意七个浪费,就可以大概了解此工厂的管理水平了。而每次上完“筑就中国成长企业的精益之道”课,很多高层都在询问如何彻底杜绝浪费,踏上精益之路。
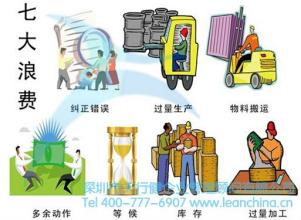
博大精深的丰田生产和精益思想是从最基础的消灭浪费开始的,精益就是建立杜绝浪费的长期理念。真正的成功是找出浪费并改进流程,了解问题的根本原因,找出解决此根本问题的对策。我们知道丰田公司已识别出企业制造流程中的7个浪费既未能创造价值的活动。 它们是:1、过量生产。2、等待。3、不必要的搬运。4、过度加工。5、库存过剩。6、多余的动作 7、不合格品。这里面有两个是关于物料的浪费:过量生产;;库存过剩。有四个是关于劳动力和时间的浪费:多于的动作;不必要的搬运;等待;过度加工。一个是关于质量方面的:不合格品。 两个是关于物料的浪费:过量生产:不仅是超出客户的需求,而且是生产量多于下道工序的需求。这个浪费最严重。库存剩余:现有的库存多于了拉式系统所规定的最小数量。而不是片面的追求零库存。四个是关于劳动力和时间的浪费:多于的动作:没有增值的动作,如找零件。不必要的搬运:不必要的运输和搬运零件和产品。过度加工:多余的加工步骤,不适当的工具或返工。等待:等候下一个处理,如看机器。等待零件运到。一个是关于质量方面的:不合格品:质量瑕疵的浪费。 一,如何消除过量生产的浪费 我们需要考虑生产计划的制定方法是否实行了标准化,是否简明合理。生产计划数和产出数是否相符合,是不是按天进行平准化(均衡化)。有没有比计划数的绝对数值生产多的情况(不允许有能力多先提前生产的想法)。实施看板生产时,是不是没有看板绝对不能生产。在批量生产的设备上是不是小批量。毎次的生产批量是否一定。是否以材料更换和换产效率不高为理由、使生产的批量比销售的批量大很多。是否下工夫解决换产时间没有。从工序计划状况和销售的状況,能不能判断看板张数和生产计划数是否贴切。 实行生产管理板,有没有随意提前生产的计划。按标准作业进行不下去的时候,本来应该空手等待的时间,是否去做了后面的工作。所有作业等待的时候,不允许作业人员主观判断后边的工作。在实施作业改善中的所有生产线上,发生作业等待的时候,原则上不让作业人员做其他工作,而明确存在空手等待的事实。有没有不断进行改善。有没有生产不足的时候,又有没有因担心生产不足所以预先生产的情况。有差别的产品在同一生产线上流动时,为吸收时间差,不得已进行一些补充工作,其最大值是否有明确设定(缓冲量的设定)。加工件的容器的容量数量(1箱、1盒、1台、1卷等的数量)是否根据不同产品有不同设定。并且是否尽力采取了最小设定。批量小型化的换产改善是否一直进行。是否单次换产(顺序换产)。中间在制品和完成品是否都是除规定数量以外不许多放置。 二、如何消除等待的浪费 是否认为重复作业的标准作业中的即使很少的等待也是浪费、并不断努力排除。是否各项作业中都没有等待。标准作业中,在机械加工的时候,有没有在旁边站着、看着、等着的情况。在装置型设备工序中是否有专门的巡视人员(监视)。有没有孤岛作业和定员制的工序。有没有努力使所有的浪费都转换空手等待加以显现,如工序作业前进不下去的时候,让作业人员空手等待。作业出现间歇时,是否让作业人员空手等待,如不允许安排其他工作,禁止“填空工作”。标准作业改善使整体生产线的时间得到缩短时,是否采取措施让每个作业人员的作业时间都短于TT(TaktTime)以使生产线获得平衡。(给予作业人员充满TT的作业内容.最后的人员出现不饱满时,让其空手等待。在装备型工序,作业人员在规定作业以外的时间是不是在指定的位置上待命。装备型工序及外部巡回的人员是否总在向别人问这问那。(不允许无原则地走动和干涉)。作业人员发生空手等待时,监督者、责任人是否迅速前去处理并采取措施彻底防止再次发生。对等待的发生和改善的过程是否都有记录。在标准作业中,发生很短的延误时,作业人员可在互助区域范围内互助,防止等待发生。有没有这样的规定和机制(有分寸的互助)。前工序的零件或材料断档时,作业人员是否空手等。后工序发生问题、作业无法进展时,作业人员是否空手等待。 三、如何消除搬运的浪废 搬运的方法与规则是否确定,如路径、时间、内容、量、场所、方法、人。是否有独自的搬运方式,如水鼓虫方式、出租车方式、包租车方式、换乘车方式、混载方式。是否采用后拉动的搬运原则如谁需要谁领取。搬运是否原则上根据取货看板在进行,当看板摘掉是搬运的指示。没有使用看板的工序上是否也有关于搬运方法的规则。是否在遵守“物品”与“看板”一起动的原则(物品与信息的一致)。搬运是否有专职人员。生产线上的作业人员是否随意离开生产线去取物品。是否做到一次不拿很多物品。(勤拿、多次)。工厂内搬运原则是不是定量不定时。工厂间的搬运及外购品的接收原则是不是定时不定量。需要按顺序供给生产线的产品,特别是大型零件或特定零件,是否建立了顺序并根据顺序准备、搬运、供给。零部件类的物品有没有生产线旁供给的原则(用时立即能有的供给)。紧急需要某种材料的时候,生产线作业人员是否会发出信号呼叫负责人或专职搬运人员(呼叫按钮、呼叫灯)。零件材料的放置场所、放置方法、放置数量、供应生产线的方法、容器等,是否持续改善。成品超市的位置、大小、高度、样式是否合适。对搬运距离过长,是否不断改善。有无不产生任何价值的临时摆放、调整堆放等。位置编号与货架编号是否设计得简明易懂。是不是任何人都能很快找到要去的位置。是否使容器的容量尽量小(小容量化)。 搬运工具、搬运车的选定是否合适如型号式样、大小、易用性、维护状况等)。搬运工具自动化的研究的改善工作是否在做。有没有根据需要推广使用机器人,工序间搬运自动化的研究是否在进行,无意义的自动化不可取。产品、零件的容器除了特殊情况以外,是否做到了统一规格及体系化、所有箱子都可以按标准码放、易于搬运。 四、如何消除过度加工浪费 对于习惯性地进行的预备加工、试加工、粗加工、前处理加工、后处理加工、打磨加工、去除毛刺加工、喷涂加工、修正加工等,是否努力逐渐缩小乃至废止。是否对习惯的检查、记帐等工作不断更改和修正。如切削工序,在累计加工到规定的数量时,检查最初和最后的产品改为顺次检查,是否在加工工序之外的其他地方进行检查与包装如在工序中或者工序的最后进行。在线保证,无过剩的检查、记帐、包装。有无因为操作台、夹具、工具、刀具等的选择不合适而需要额外加工时间的情况,是否及时对应了材质与产品的形状变化。在手工作业中,是否也研发应用独自的专用器具,是否有效地将人的作业进行机器人化、自动化、机械化。自动化是否体现了对人的关怀,如优先考虑重体力劳动作业、不安全作业、需要持续高度注意的作业。如果无法细致地完成要素作业则工作分配、作业组合难进行。是否积极筹划在测定、记录、记帐等作业中实现IT化。工装工具是否总能够以完善的保养状态投入使用,有没有因为工装工具有问题导致工作无法顺利进行。有没有大量生产的设备(大舰巨炮型设备),假设有,是否在设法用它进行小单位的生产,能否在狭小空间内自如回旋。计划设备的时候,有没有要超过需要的高性能。如简便的单项功能最好。产品变化时,原则上手工修改使之符合新产品要求,有没有为提高开工率而盲目让设备运转的情况。如不需要的时候按计划停止。要提高的是可动率、设备完好率。设备是否一直状态正常如不因设备老化而降速度运行,也不添加多余的人。因故障与其他问题导致设备停止的事情是否基本没有。小故障对策是否健全如不需要生产线的“巡视员”。TPM、保全、工艺的结构体系是否齐备,对机械类结合实际,细处要进行符合本公司情况地改造,最大效用地使用。设备保全的数据与保全信息是否齐备,是否不断使工序更简洁。是否构造成U字型生产线,是不是在设计设备和工序时就考虑到了本企业产品的流动特点。解决机械故障及临时停线的对策有没有彻底推行。 五、如何消除库存的浪费 生产计划是否是只生产必要(能售出)产品的计划。量产产品的预测生产是否也在实施出货的平准化。定单产品是否没有库存,是否即使有量也极少。是不是原则上根据定单情况或出货状況进行生产。看板生产的地方,看板的发行张数是否限定在必要最小限量,库存是否受到限制。外购件是否库存极少。应客户要求暂停出货的产品,是否均衡化地从超市或放置地取出、与通常库存相区分地进行保管。预计出货多于通常的时候,是否也做到均衡化地从超市或放置地取出、与通常库存相区分地进行保管。有没有成品库存,是否即使有量也很少。是否完全没有死库存。生产批量规格是否相当小。换产时间缩短化进展怎样,挑战单次切换(顺序切换)。部件材料等调配物品是否只在需要的时候调配需要的量。看板或发单点管理是否健全。在分离的工序间进行后工序领取式生产时,中间在制品是否只有看板设定的数量。在不得已使用生产计划的生产线上,是否定有抑制中间在制品数量的计划数。生产的过程周期时间是否极短。有没有交货期投诉和交货遵守不好的情况。如有没有屡次三番调整交货期,为避免投诉随意处理的情况。交货期和库存的管理是否简洁明了并易于用眼看明白。外购管理和调配管理有没有問題如外购品、调配品是否也是适时只购进必要的量。进货交期、时机条件、质量等有无不合适。部件材料是否是从生产线旁边供給,材料仓库、部件仓库等是否可以取消。 六、如何消除动作的浪费 有没有作业人员监视设备加工的情况。如人与设备的工作是否区分开了。是否有作业人员无目的地来回走动的情况如不允许做标准作业规定的以外的事情。有没有步行距离不必要地长的地方。标准作业设定的顺序有没有来来回回交叉的路线。在难以判断或产生异常的时候,作业人员之间是否有随意商量解决办法的情况。在生产线作业中有没有取放并不需要的物品的动作,取放的浪费。让生产线作业人员补充零件时,是否也有明确的规则。在重复作业中有没有每次都需要用手拿着或者用手按着让机器加工的地方。有没有因为加工零件的放置方法与位置不好、给作业增加很多困难、作业时间波动也很大的情况。工装工具、测量工具是否专业化。是否设备被设置得能在加工结束时自动停止、自动弹出。在人与设备进行加工的工序中是否形成了“节节方式”即人的工作只是放加工物品,不用取出。“同期作业方式”即并行作业是否得到有效应用。如同时加工、同时检查。作业时的脚下空间清理得情况怎样,是否方便行走,是否安全。手工作业中,利用夹具固定后加工或者用工具进行加工的时候,有没有每次作业都是又取又放工具的情况。 七、如何消除不合格品 不合格品对策是否彻底,不合格是否很少。后工序是顾客,不合格不能后传。当不合格品发生时,是否以现场、现地、现物的原则,迅速采取措施。是否不仅仅是处置,而是通过反复问为什么找出真正原因,从原因对应而防止再度发生。生产线是否设置为只要一出现不合格品就自动停止的模式(自働化)。有没有形成用防错装置使不合格不能传递的机制。通过反馈修正不合格的组织机制是否融入了工序中。对慢性不合格品,是否经常应用工序能力调查的SPC/SPC等手法彻底采取对策。不合格品的修正、再检、甄别等作业是否是在出现不合格的地方进行的。对不合格采取的对策是否都有记录。是不是在线检查,是不是按生产顺序进行检查(顺次检查)。后工序发现不合格品的信息是否及时反馈到产生不合格品的工序。有没有设置有涂成红色的不合格品箱。有没有采取各种措施来提高作业人员的质量意识。有没有不合格品对策体制,是否在发挥作用。针对外购厂商、调配单位的不合格品对策是否健全。对作业人员的质量教育是否充分。对标准遵守情况的检查是否扎实。除特定品外,有没有在工序外设置检查场地批量进行检查(特定品指的是客户提出需要另外特殊检查的保安类的零件等)。标准作业中是否融入了检查的要点和顺序。标准作业中是否融入了有关质量的要点。不合格品的数据是否有切实的统计汇集。有没有将其用为采取对策的依据,有没有在现场展示以帮助提高质量意识,生产计划是不是预留了不合格品数量的。