如今那些对丰田模式有粗略认识的人会认出现在著名的按灯系统(andon)正是源于丰田佐吉“错误预防”(mistake-proof)的织布机。按灯系统是一个工人在生产车间中检查到错误时,停止装配线时使用的。丰田所有的自动化设备都安装有错误甄别系统,目的是自动关闭机器。快速甄别和根除错误与浪费的基本哲学在创始时就已经成为公司的核心支柱。
在父亲的建议下,丰田喜一郎决定将公司从生产织布机转型到生产机动车。丰田佐吉认为公司需要扩展到其他生产领域,所以在1929年丰田喜一郎开始有目的地到美国和英国参观,表面上是为公司的织布机技术协商许可证事项,实际上,他正尽其所能学习汽车和机械设备及工厂方面的一些知识,以指导他在丰田织布机厂设立汽车分厂。在1933年,他真的建立了汽车分厂。到1937年,汽车生产已经是丰田汽车公司(Toyota Motor Corporation,TMC)业务的核心。
丰田喜一郎在20世纪30年代晚期的一份展示丰田经营理念的重要文件中第一次写下了“及时生产”(JIT)的字样,用来描述物质从原料到消费者手中的流动过程。该理论在丰田历史上另一个标志性人物大野耐一的领导下投入了实践。为了应对顾客的需求,大野耐一于1948年创立了“拉动式生产系统”(pull system),并且在1953年第一次应用于工厂,该系统与我们今天所谓的“超级市场”类似。
大野耐一的超级市场概念是在和一个朋友的谈话中受到启发的,而他的朋友当时刚访问了美国并且描述了美国的超级市场。在冰柜被广泛使用之前,存货控制在杂货店业务中是非常重要的。食品变质很快,所以杂货店需要时刻注意存货,仅仅保存能够满足几天需求的现货。在现代术语中,超市需要JIT的存货管理,这也正是它们一直在做的。
丰田公司成立初期存在着一个类似于超市的问题。虽然公司的存货没有坏掉的危险,但是公司没有维持存货的现金。作为一家小公司,公司需要尽可能保存有限的运转资金,如同美国的超级市场一样,像牛奶等食物放在货架上的数量要和顾客购买时取走的数量相当,丰田公司最终形成了内部的“超级市场”来为生产线补充其所需要的零部件。
丰田佐吉所重视的消除错误的理念和丰田喜一郎强调的JIT生产系统及大野耐一在其基础上的创新理念共同结合形成了著名的丰田生产方式(Toyota Production System,TPS)。在TPS演进和提炼的近80年中,它指导着丰田从供应商到汽车生产的经营、运输及经销商的服务。重要的是它专注于对质量和消除浪费的严格追求,而这种追求是通过所有个人和管理者的持续改善实现的。这在今天听起来好像很平常,但不论在当时还是现在,这都是革命性的。在丰田上升为全球引领者之前,一般生产方式主要追求的是规模经济。这种生产方式着重于在生产过程中的每一环节都增加产量来降低成本。这就不可避免地会引起存货的增加,但是却被认为是一件好事。质量问题可以被容忍,因为库存中总有零部件。当时的理念是,降低缺陷的成本远远高于效率最大化以及扔掉有瑕疵的产品的成本。
然而丰田证明这种经营理念是错误的。如果你消除错误和质量问题,你就能以更低的成本经营,同时保持更高的顾客满意度。丰田消除浪费和错误的过程是建立在大野耐一高度的前瞻性之上的。大野耐一认为,如果公司使用丰田佐吉的方式去发现和解决问题以及用丰田喜一郎的方式去及时生产,那么必须在整个公司内建立一种系统的解决方法。他的焦点是以依靠问5次为什么来挖掘问题的根本原因。
大野耐一解决问题的过程受到爱德华8226;戴明的影响,戴明是第二次世界大战后受美国政府的派遣来援助日本战后重建的。戴明的思想是现代质量运动的基石。他教日本的经营者学习质量的重要性和实现的方法。戴明思想的核心是对消费者定义的根本拓展。历史上,消费者被认为是产品的最终使用者,但戴明认为消费者其实也参与到生产过程的下一个环节。因此,在一个生产性的环境中服务于消费者意味着为生产线提供下一步需要什么,即产量和质量,以及什么时候需要。当服务顾客遭遇困难的时候,戴明提倡用一种高度系统化的方法来解决,即著名的计划(plan)──执行(do)──检查(check)──行动(act),也被称为PDCA循环。(戴明的PDCA循环法摘自威廉姆8226;休哈特。)
PDCA循环是相当直观的。在你试图解决问题时,你要确保有一个计划,这个计划是基于对问题根本原因(而不是问题的表象)的透彻研究而制定的。一旦你拥有了处理问题根本原因的计划,就可以在一个测试的环境中去执行解决方案,检查解决方案是否奏效,然后根据你在测试环境中所得到的信息处理,要么改进计划,要么转向另一个需要改进的领域。因此,PDCA永远不会结束,最后一步总是下一步的开端。
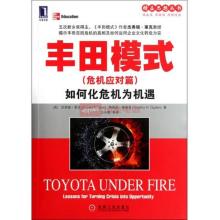
丰田解决问题的过程以实际问题解决法最为出名,当它发展到现代时被称为丰田问题解决法(Toyota Business Practices,TBP)。TBP是丰田从工作中消除错误和浪费到为公司制定全球战略时的问题解决方法。
总而言之,TBP始于对实际问题的描述,包括理想状态和现实状况之间的差距,然后这种差距被分解为可以执行的一些重要问题。这些具体的子问题依靠问为什么来分析找到根本原因,而不是表面原因。在丰田内部,这被称为“5个为什么”──要发现问题的根本原因,你不得不至少问5次为什么。对策之后被确认、尝试、监督和进一步的调整,直到差距被消除以及下一次的挑战被识别出来。
TBP的8个步骤:
计划
1.确定相关的问题。
2.把问题分解成可行的几个部分。
3.确定根本原因。
4.制定出几个解决方案。
5.基于所知评价和筛选出最好的解决方案。
执行
6.执行解决方案(如果可能则进行试验)。
检查
7.检查解决方案的实施效果。
行动
8.在得到信息的基础上调节、校准和扩展。
虽然TPS几乎是一个生产和重复的过程,但是它采用了TPS的理念,并把它广泛应用于整个企业,包括生产、设计、销售,甚至战略决策的制定。丰田认为这种解决问题的方法对企业的领导层来说是非常重要的,无论他处于什么职位和部门,每个领导者都应该是TBP的控制者。控制这个过程允许哪怕是一个有财务和人力资源背景的领导者,都能对车间生产作出有意义的贡献,同时也把他所在部门的工作看做一系列可以被不断改善的过程。
大野耐一的另一个重要贡献就是对标准化工作的发展。这个概念指的是生产线上的每项工作都需要被严格定义并且每个从事这项工作的工人都要按照相同的方式执行。如果工作不被标准化,在生产线上解决问题以及不断提高和改善绩效就是不可能的──实际上,如果相同的工作以不同的方法来做的话,导致缺陷或者表现不佳的因素就不能被识别和改正。很多西方人起初认为标准化工作是灾难性的,把它想象成为对待人像对待齿轮和机器人一样的模式。相反,标准化工作允许生产线上的工人思考他们正在做的工作、为什么工作以及怎样改进工作的问题。这样来想:没有人会把西恩8226;潘和梅丽尔8226;斯特里普这样著名的演员认为是齿轮与机器人,但是只有记住台词,他们才能把自己的创造力和洞察力融入角色中。标准化工作就像是演员的剧本,它是生产工人把自己的技能运用到不断改进过程中的基础。没有标准化工作,TPS和TBP是不可能实现的。