●周朝时,文王问姜尚怎么样才能成为明君呢?姜太公曰:“目贵明,耳贵聪,心贵智。以天下之目视,则无不见也。以天下之耳听,则无不闻也。以天下之心虑,则无不知也。“《太公六韬》。“看板制度”犹如一辆日式车子,里面满载的却是华文化稀世瑰宝●
丰田在1978年前的合理化过程中,职工提出了46万3千件合理化建议,当时4万名左右职工,人均十几件。进入90年代,平均每年收到的数目达到约200万个,平均每年每人提出35.6个。真可谓是"无不见、无不闻、无不知也"!还有什么角落不能合理化?什么环节不能合理化?丰田公司一个最小的螺丝钉的拧法都是最合理化的!职工的这些"建议"内容大到降低成本、保证质量、生产技术、产品开发、经营管理等一系列环节,小到怎样利用旧信封和短铅笔头。
"庖丁解牛"这个故事大家都熟悉吧,论治国梁惠王肯定比庖丁高明,但说到宰牛,庖丁那"恢恢乎其于游刃必有余地矣!”这种境界,梁惠王就望尘莫及!只能惊讶慨叹:“嘻,善哉! 技盖至此乎?”。"如果骨子里只认为领导专家"高明",工人脏兮兮苦力一个懂什么!让员工提"建议"只是作样子当摆设,从未真当会事,落满灰尘的"建议箱"就难怪被麻雀疑为昔日旧巢了。领导专家与工人各有各的"高明"之处,领导专家宏观应该比工人高明,但加工某一个零件,工人就肯定比领导专家高明。据当年负责研制毛泽东水晶棺的曹金瑞工程师回忆,连续奋战10个月,一次次失败,愁死人难死人了!最后突破工艺难题的一种全新工艺,不是什么"专家",居然是605分厂一位经验丰富的老技工徐兆彩设计出来的。
在丰田,那些行之有效的合理化建议都得到了公司的重奖。丰田车工部一个叫铃木胜康的工人,提出了一个消除座位下弹簧发出"格吱"响声的建议。很简单,就是在接头部位涂上石蜡,然后烘干,问题就解决了。这个小点子使用后客户大为满意。铃木胜康因此得到了公司10万日圆奖金,还申请了日本国内和美国专利加以保护。在四川丰田每个车间都有一个区域,专门用黑板甚至用绳子挂起一些纸张,多是流程的每一步质量管理,但更吸引记者眼球的是一张张工人们来自生产中的保质增效又降低成本的建议图。一张图纸上,清晰地画着一个工件,该工件大概是属于易损工件需经常更换。而工人在实践中发现,该工件易损部位只是头部,是可以单独更换工件头部的,完全不用整个工件更换,这样无疑将降低成本。
这里面有个对员工的正确认识和态度问题,企业积累是两部分的一体化:一是以利润和再投资积累起来的物质资本;二是从业员工在工作过程中、由于经验积累使技术水平能力熟练程度提高形成的特殊资本,事实证明,产品质量数量的提升与后者高度相关。丰田非常注重专家、技术人员与工人操作经验的结合。职工由于一天到晚在车间,最熟悉了解解决问题的要害,他们脑子经常闪烁数不清解决问题的想法、灵感、小发明。我年轻时当过兵和工人,那时觉得许多捋捋袖子就成的事,领导们来回开会研究却不得要领。丰田几万职工常年的操作经验积累是最大的合理化源泉,这可是个"合理化富矿"。这里可以省1分,那里可以节约2角,什么地方还可能再提高改善一下………等等。正如丰田员工上下津津乐道的:"我们大企业做的是小企业的抠门事","干毛巾也要拧出一滴水来"。各个环节的无数小的完善、创新,如涓涓溪流之不竭,如江河日月之无穷,是没有时间终始和空间极限的。大野耐一所说"合理化是无止境的"就是指的这个。这是任何高明的技术专家所做不到的!员工如同钟表的每个齿轮,是把整体核心竞争力一点一点提升的最基础环节。
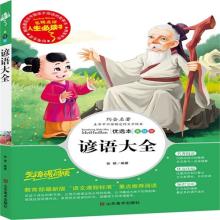
现代大哲毛泽东,更将《六韬》阐释为"人民群众中蕴藏着无限的创造力",他就是仗着这个八年打败小日本,三年解放全中国的。什么"麻雀战"、"地道战"、青纱帐、神出鬼没,搞得日本人和老蒋焦头烂额、草木皆兵!1969年,北京某企业各车间就“普遍建立了技术人员、干部和工人三结合的技术革新小组。” 。然而,由于种种原因,在本土却没有得到认真扎实深入的实行。据报道这个发明很快传到日本,并被广泛认真地制度化到企业管理中, TPS始于1973年,而“三结合”却早出现于1969年。源与流,道与技,难道不值得中国模仿者们深思!