家族的精神与管理结合,是丰田几十年长盛不衰的根基
文/陈振烨
美国底特律三大汽车巨头称霸的时代彻底结束了。通用汽车、克莱斯勒和福特的高层在讨论首要竞争对手时,他们已经不再提及彼此的名字,而是集体把目标对准了日本丰田。有些人甚至把丰田年报放在公文包里,时刻提醒自己对手是多么强大。 “属于丰田的时代正在到来。”一位知名管理专家向《经理人》感叹道。这家1937年创立的汽车制造企业,终于在70年后坐上全球销量冠军的宝座,并荣登全球最受尊敬企业榜首。其去年总销售额为2528亿美元,净利润165.4亿美元。这相当于底特律三巨头外加德国大众和宝马的利润总和。它2000多亿美元的市值,竟比底特律三巨头总和的7倍还要多。 丰田出色的业绩让许多CEO眼红心跳。这与在生死线上挣扎的通用汽车和福特,还有受困于成本压力及利润下滑的德国大众和宝马形成鲜明反差。当外界为汽车巨头急速衰落而惋惜时,我们却不禁要问:丰田过去70年持续缔造辉煌的秘诀是什么?越来越多企业在研究和仿效丰田模式,它们又能从中得到哪些收获? 丰田家族式基因 丰田的庞大规模富可敌国,它的子公司有520多家,日本本土和海外差不多各占一半,员工超过28万人。但与很多过百年的日本企业一样,丰田在很多方面仍然像个家族企业。这并非因为丰田家族掌控丰田,而是丰田家族对丰田公司文化留下的持久影响。 这种影响使丰田能在漫长的70年中始终延续一致的企业文化和管理理念,最终形成享誉全球的丰田模式和丰田精益制造方式。丰田家族的精神与管理结合,是丰田几十年长盛不衰的根基所在。 说到丰田今天的成就,自然要提到创始人丰田喜一郎。这位极富远见的领导者在1938年刚创建丰田时就提出:“要尽可能地缩减工作流程,以及输送零件、材料流程中的松散时间,实现此计划的基本原则是采取‘准时生产制度’,不要太早或太晚输送货物。” 这一精辟思想正是今天丰田精益制造方式的核心内容:杜绝浪费时间、物料、员工创造力,等等。这可是1938年!即便在今天,很多现代公司仍然无法做到这点。 二战之后,丰田喜一郎的堂弟丰田英二接任公司董事长,他把福特和通用作为研究和学习的对象。亨利·福特1926年提出规模经济的概念,要大规模的自动化作业。但丰田英二却意识到,面对小而复杂的日本市场,规模化对丰田不现实也不适用。 因此,丰田英二设法对学来的经验进行调整,然后提出“一个流”原则,要求丰田做到高品质、低成本、短前置期及灵活有弹性。这是丰田精益制造方式基础内容的前身,也是它坚持到今天的“生产节能和经济型轿车”的经营原则。 在丰田英二之后,我们很难说清楚有多少位丰田家族成员管理过丰田公司,但你能够感受到:不论是丰田英二之后的大野耐一,还是首位非丰田家族总裁奥田硕,以及他之后的张富士夫和渡边捷昭,他们都保持着一致的领导风格—既保守又能不断创新突破,以及持续缔造和完善丰田模式和丰田精益制造方式。 精益制造让丰田崛起 丰田精益制造方式即丰田生产方式,它被誉为世界制造业的标杆,是减少浪费、降低成本、提高品质和利润的流程化生产能力的代名词。天津大学管理学院院长齐二石认为:日本汽车业曾经远远落后于欧美,但经过几十年努力,丰田却能凭借强大的管理竞争力超越欧美汽车巨头,成功的关键就在于精益制造。 1973年爆发第一次石油危机,把汽车业甚至整个西方经济拖进漫长的黑夜,但这却为丰田等日本汽车企业提供了绝佳的机会。丰田赶超欧美汽车巨头,使丰田精益制造方式开始受到世人瞩目,现在越来越多企业在研究和效仿丰田,其中不乏波音这类超级公司。 丰田精益制造的核心原则是“一个流”—无间断生产流程,其目的是为了杜绝浪费。从新车型设计、原型打造,到最后组装加工、成品上市的整个过程都实行无缝式流程。这种“无缝”不仅体现在生产线上,还体现在各个部门之间的沟通中。 举个直观的例子。当顾客下单时,流程终端马上做出反应,同时不多不少地指出顾客订单所需要的所有原材料。接着将这些原材料送往供货工厂,工人立即加工零部件,然后输送至另一个工厂,由工人立即组装,最后完成产品送抵客户手中。 所以,多数汽车厂商推出一款新车需要两年多时间,但丰田却不到一年。丰田在1990年时生产规模只有通用的一半,但投向市场的车型却和通用一样多。一位管理专家认为:“这个生产制度的优点在于,它能针对顾客的特定需求而小量地生产产品,使丰田迅速适应顾客需求的日常变化。” 北美地区丰田汽车制造公司前任总裁箕浦照幸说:在“一个流”制造方法中,若有问题发生,整条生产线都会暂停。这种生产制度看似很糟糕,但当生产停止时,每个人都要被迫去解决问题,促使大家思考解决之道,员工也因而得到成长。 所以在丰田企业文化中,倚重而非减少对员工依靠,着重支持和鼓励他们持续改进工作流程,并且最大限度地尊重他们。这是丰田精益制造方式成功的根本,如果理解不到这点,简单效仿丰田是无法成功的。 丰田对于浪费的理解似乎更加宽泛一些。一种是资源性的浪费;另一种是那些不能为客户创造价值的活动也被视为浪费。在近些年原材料涨价和能源紧张的情况下,丰田依然能够保持高速增长,与其奉行的“杜绝浪费”理念有直接关系。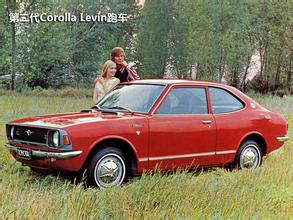
以2000年丰田对“花冠”旗舰小型车的改版为例,这款车累计产量超过2400万辆,与大众“甲壳虫”同为全球最畅销的大众车型。丰田将这款车改版后,使其配置和档次都大大提升,但价格却比同级别车型便宜很多。 之所以能够做到这点,是因为花冠执行了一项“降低成本和减少浪费”的活动。举个例子,原来光转弯时用来支撑身体的辅助拉手就有35种之多,但将这35种统一成3种,就能节省下很多成本。除此之外,丰田在与供应商协作、产品设计开发和满足客户需求上,都与其他公司的做法截然不同。这些独特的管理方式造就了强大而与众不同的丰田汽车王国。