考虑到中国制造型中小企业的现状,精细化管理也要适实“粗放”
□本刊记者 赵楠
7月的北京,闷热得让人有些透不过气。北京加增工贸有限公司副总经理陈建萍坐在办公室,点击着鼠标浏览生产车间当日上报的生产数据。她心里非常明白这套详细数据的来之不易。用她自己的话说,加增上马ERP的过程是“艰难跨越两道门槛的过程”。作为一家拥有自有品牌、自主生产食品,拥有400多名员工的企业,加增是北京最大的3家熟食供应商之一,同时在天津、河北等地区也有不错的销售成绩。在业绩逐年攀高的同时,陈建萍也看到,企业的年销售额虽然早已过亿元,但管理层无法对生产部门进行有效管理和监控正成为企业进一步发展的最大隐患。 头痛的生产监控 食品行业,尤其是熟食领域的企业向来以供应链高效著称。尤其在七八月份这样的食品销售旺季,更是考验一个食品企业产能、管理能力的重要时期。“现在这段时间,除了质量之外,我们和其他竞争对手最重要的就是比拼效率。”陈建萍对记者说。的确,现在加增每天需要向近千家零售网点发货,从库房出库的冷藏车经常是司机几班倒轮流出发。 “加增生产部门需要8个流程才能把订单转化为成品发货。一般来说,从供应商把生肉运入我们的的冷冻库到成箱包装入库的周期大约为3天。”陈建萍告诉记者。像很多中型食品生产企业一样,加增的销售部经理每天都要和各大超市、零售网点取得联系,估算一个需求量,如A火腿500箱,B香肠400箱。由他告知生产部门后,由生产计划员根据订单数量估算所需原材料的重量,如生牛肉1吨、生鸡肉2吨。生产计划员的估值除了要对销售计划员估算成品数换算成原肉,还需考虑工厂的产能问题,因为如果当日给车间的生产目标过高,拖到第二天,会对以后的计划造成影响。显而易见,人为的估算是不够准确的。 经过两次人为的估算,最后贴到车间的当日生产计划是以生肉重量呈现的,车间工人随后会按量解冻生肉,进行车间生产第一个环节:入料。然后经过搅拌、滚揉、腌制以及高温(或低温)等8道工序后,最终个体包装、封箱并入库。 由于加增食品的生产原料只有猪、牛、羊等几种,而生产的100多个品种的熟食产品中,大多所需原料相同,只是配比、规格不同。所以,除入料和包装环节外,中间生产环节的工人根本不知道这些生肉制品最终是制成火腿肠500克,还是猪肉1千克。工人只负责自己的工序,把原肉放到一起进行加工,不会按照、也不需要按照最终出产的规格分类加工。到最后的单品包装环节,往往是当天哪个规格、种类的产品要货紧,就把生产完毕的熟食半成品封装成哪种。这种不可控的生产现状让陈建萍苦恼不已,“我之前手中能获得的准确数据只有两个:一个是销售经理下单的数量,另一个是最终入库的数量,中间环节根本无法了解,而这两个数据往往是对不上的。”陈建萍给记者举了个例子:如果8月1日销售经理告诉生产部门,需要生产500箱500克规格火腿肠、600箱片装600克火腿的话,3天后到包装库房查库,基本会出现两种情况:一是生产了300箱500克火腿肠,而由于当日市场需求,剩下的原料全部临时生产成片装火腿出库了;另或者入库总数比计划的少了十几箱,包装工序的负责人则会解释说从上一生产线下来的熟食的半成品不够再包装十几箱。“当初遇到这种情况时,我都不知道该追究谁的责任,这就像有人在中间环节把熟肉半成品偷偷运出工厂,我却不知道怎么丢的!”陈建萍无奈地告诉记者。 这种情况在尚处在发展期的中小企业尤为常见。从十几人甚至几人发展起来的企业,他们在发展中更关注发货和进货环节,因为这两个环节会牵扯到和原材料供应商以及分销商的对账问题。随着企业规模不断扩大,大多数沿用袖珍企业时的生产、管理机制的企业当规模发展到数百人时,原先的管理方法显然无法有效监控生产流程,这就需要通过IT手段来规范企业的运营体制。考虑到中国制造型中小企业的现状,精细化管理也要适实“粗放”
□本刊记者 赵楠
7月的北京,闷热得让人有些透不过气。北京加增工贸有限公司副总经理陈建萍坐在办公室,点击着鼠标浏览生产车间当日上报的生产数据。她心里非常明白这套详细数据的来之不易。用她自己的话说,加增上马ERP的过程是“艰难跨越两道门槛的过程”。作为一家拥有自有品牌、自主生产食品,拥有400多名员工的企业,加增是北京最大的3家熟食供应商之一,同时在天津、河北等地区也有不错的销售成绩。在业绩逐年攀高的同时,陈建萍也看到,企业的年销售额虽然早已过亿元,但管理层无法对生产部门进行有效管理和监控正成为企业进一步发展的最大隐患。 头痛的生产监控 食品行业,尤其是熟食领域的企业向来以供应链高效著称。尤其在七八月份这样的食品销售旺季,更是考验一个食品企业产能、管理能力的重要时期。“现在这段时间,除了质量之外,我们和其他竞争对手最重要的就是比拼效率。”陈建萍对记者说。的确,现在加增每天需要向近千家零售网点发货,从库房出库的冷藏车经常是司机几班倒轮流出发。 “加增生产部门需要8个流程才能把订单转化为成品发货。一般来说,从供应商把生肉运入我们的的冷冻库到成箱包装入库的周期大约为3天。”陈建萍告诉记者。像很多中型食品生产企业一样,加增的销售部经理每天都要和各大超市、零售网点取得联系,估算一个需求量,如A火腿500箱,B香肠400箱。由他告知生产部门后,由生产计划员根据订单数量估算所需原材料的重量,如生牛肉1吨、生鸡肉2吨。生产计划员的估值除了要对销售计划员估算成品数换算成原肉,还需考虑工厂的产能问题,因为如果当日给车间的生产目标过高,拖到第二天,会对以后的计划造成影响。显而易见,人为的估算是不够准确的。 经过两次人为的估算,最后贴到车间的当日生产计划是以生肉重量呈现的,车间工人随后会按量解冻生肉,进行车间生产第一个环节:入料。然后经过搅拌、滚揉、腌制以及高温(或低温)等8道工序后,最终个体包装、封箱并入库。 由于加增食品的生产原料只有猪、牛、羊等几种,而生产的100多个品种的熟食产品中,大多所需原料相同,只是配比、规格不同。所以,除入料和包装环节外,中间生产环节的工人根本不知道这些生肉制品最终是制成火腿肠500克,还是猪肉1千克。工人只负责自己的工序,把原肉放到一起进行加工,不会按照、也不需要按照最终出产的规格分类加工。到最后的单品包装环节,往往是当天哪个规格、种类的产品要货紧,就把生产完毕的熟食半成品封装成哪种。这种不可控的生产现状让陈建萍苦恼不已,“我之前手中能获得的准确数据只有两个:一个是销售经理下单的数量,另一个是最终入库的数量,中间环节根本无法了解,而这两个数据往往是对不上的。”陈建萍给记者举了个例子:如果8月1日销售经理告诉生产部门,需要生产500箱500克规格火腿肠、600箱片装600克火腿的话,3天后到包装库房查库,基本会出现两种情况:一是生产了300箱500克火腿肠,而由于当日市场需求,剩下的原料全部临时生产成片装火腿出库了;另或者入库总数比计划的少了十几箱,包装工序的负责人则会解释说从上一生产线下来的熟食的半成品不够再包装十几箱。“当初遇到这种情况时,我都不知道该追究谁的责任,这就像有人在中间环节把熟肉半成品偷偷运出工厂,我却不知道怎么丢的!”陈建萍无奈地告诉记者。 这种情况在尚处在发展期的中小企业尤为常见。从十几人甚至几人发展起来的企业,他们在发展中更关注发货和进货环节,因为这两个环节会牵扯到和原材料供应商以及分销商的对账问题。随着企业规模不断扩大,大多数沿用袖珍企业时的生产、管理机制的企业当规模发展到数百人时,原先的管理方法显然无法有效监控生产流程,这就需要通过IT手段来规范企业的运营体制。 陈建萍是个易于接受新事物的人,她主动联系了专门做生产制造ERP的天思软件公司来厂做调研。陈建萍决定引入生产ERP的理由很简单:她需要了解入料和包装中间这段空白地段到底是怎么运作的,改善目前混乱的管理状态;另一方面,她希望通过信息化手段来控制企业的成本。 精细化管理的两道门槛 其实在决定上信息化之前,陈建萍已经意识到了生产车间流程不可控的隐患,为此她曾经建立过企业的统计部门,由专人对每道工序进行人工记录、监控,几个月下来,整理出了一份数据。但是出乎陈建萍的意料,连统计部的经理都不知道这份数据到底在记录什么:比如搅拌这道工序,由于要把上一工序多个流水线下来的生肉统一搅拌,然后又按量再与其他肉料组合进行再次搅拌,统计部的记录员分不清哪些是自己跟踪的肉料,哪些应该由其他同事跟踪。食品加工过程中这种“分分合合”的复杂工序使得统计的结果变得没有多少意义。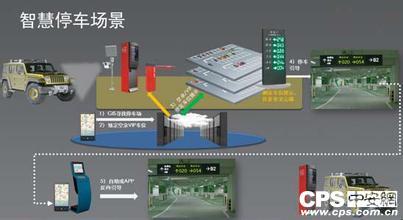
2007年10月,陈建萍把天思的实施工程师请入加增,进行了1个多月的调研。“调研之后,我和厂方代表讨论,决定通过培训,让每道工序负责的工人自行填写数据,然后到统计部汇总,最终把数据录入ERP系统。”天思软件项目经理单晓亮告诉记者。 2007年底ERP系统正式上线。经过3个多月的试运行,在下料环节,通过解冻前后的数据对比,陈建萍可以轻松地了解原料的含水程度,判断出供应商肉料质量高低,为日后筛选供应商提供了有力数据。另一方面,入库之前单品封装的数据也可以清楚地从ERP系统获得,这样加增可以通过ERP清楚地了解到每天车间不同种类、不同规格的产品生产了多少,以便调整第二天的生产计划。理顺每道工序的流程数据,标志着加增跨越了精细化管理的第一道门槛。 只是ERP系统显示的数据,乍一看非常完美,但实际上除去入料和包装环节之外,其他工序统计上来的数据和当初统计部人员统计的数据对比来看,却没有多少差异。这让陈建萍非常失望。问题出在哪呢? 做过多个食品行业生产ERP项目的单晓亮告诉记者:“人员是进一步进行精细化管理的瓶颈。”原来,加增在其近10个生产车间的400多名员工大多文化程度较低,人力资源成本较低的另一面就是很难使这些员工习惯信息化的生产管理制度。一方面面对相对复杂的单据,工人不知道如何正确填写;另一方面,工作量是直接和工资挂钩的,如果如实填写,势必对他们的收入有致命的影响。在这两方面的作用下,统计部人员从员工手中整理出的数据就没有太大的可参考性。 怎么办?单晓亮在和陈建萍讨论后,最终决定从原来对全部工序都进行严格数据监控,变为抓重点工序监控:继续对入料和单品包装实行数据监控,而中间环节,只对高温(或低温)直接制成熟食半成品的环节严格监控。这样一来,管理者不用获得每个工序的数据,只需要获得当天可供包装的熟食半成品总量,再根据计划,控制到底需要包装成哪些规格、品种的产品。 由原来逐步监控转变为有重点的“粗化”监控,在单晓亮看来是个必然。“目前加增的生产管理较以前已经有了很大改善,生产效率以及可控程度已经大大提高。但是要实现每个工序的精细化管理,企业还是需要一段适应的时间。” 很多中小企业主在通过IT手段进行内部管理后,所看到的结果往往和最初的预想有很大差距。而这种差距并不是信息化系统本身的问题,而是出在中小企业本身,这在生产型企业信息化时尤为明显。在推进企业精细化内部管理时,这种来自企业内部人员的阻力并不是一朝一夕能够解决的。所以,给中小企业普及精细化管理的理念后,在实际实施过程中,也要适实“粗放”,并通过时间使整个企业的员工逐渐习惯这种高标准的管理规范。 当企业真正接受并顺利进行精细化管理时,这个企业也就具备了向大型企业发展的内部条件。上马ERP系统这道门槛中小企业跨越较为容易,可真正迈过全流程精细化管理,这第二道门槛还需要广大中小企业苦练内功才行。