50年前,当日本大福株式会社(DAIFUKU)向丰田公司提供第一套车身流水线时,还需要向全球物料搬运领域的领先企业美国威勃公司(JervisB.Webb)求助,购买其链式输送机,而50年后,威勃公司却被当年这个小弟收入囊中。 2007年11月15日,大福正式对外宣布全资收购威勃的消息,大福的代表取缔役副社长北条正树将作为新威勃的董事长,并将与威勃原CEO苏珊·威勃共同担任联合CEO。 1937年成立的大福公司一直专注于物流领域,其设备系统在输送、保管、拣选和分拣等方面引领着国际业界的发展。目前,大福在全球有40多家分公司。根据2007年3月国际权威媒体《现代物料搬运》(ModernMaterialHandling)“2006全球20强物料搬运系统供应商”排名,大福公司以19.5亿美金的销售额位列第二,威勃公司以2.2亿美金的销售额位列第15,两者的销售额相加将超过位列第一的Schaefer公司。 “等到2008年新的数据公布,大福将全球排名第一。”坐在位于日本滋贺县新工厂的会议室里,大福株式会社代表取缔役社长竹内克己表情安详,对于成为全球新王者,这位70多岁的日本人虽然语调平淡,但可以感觉出其内心对多年心血的自信。 1970年代以来日本先进制造业席卷世界,但很少有人知道,在丰田、本田、松下、日立等大名背后,大福这家专业的生产线和物流设备提供商起到了重要的“推手”作用。不论是大福的工业流水线还是自动化立体仓库,对于促进日本制造业和流通业的发展,大福的贡献不言而喻。 “大福为日本汽车制造业做出了贡献。”竹内克己认为,“丰田模式”的成功,有大福的功劳,而日本制造业在全球的成功进而也成就了大福。 “丰田模式”的推动者 1937年5月20日,一家名为株式会社坂口机械制作所的小企业在日本大阪成立,150名员工主要制造压延机、钢铁冶炼用的锻压机械和起重设备。1947年,公司更名为大福机工。 对于日本制造业来说,1937年还有另外一件具有重大意义的事情发生。那就是丰田汽车正式成立。丰田喜一郎从1931年开始就在父亲的丰田自动织机工厂一个角落里研制发动机,并买来美国的汽车进行分解学习,历经6年的努力,终于试制出了A1型轿车和G1型卡车,丰田喜一郎在1937年正式打出了丰田汽车的旗号。 1950年代初,日本的汽车工业逐渐形成完整的体系,现在日本主要的汽车厂家都是在这一阶段起步。但最初日本汽车产业的规模弱小,尤其是生产线和生产流程很落后。根据日本汽车产业专家、东京大学经济学教授藤本隆宏的研究,由于生产线落后,当时日本汽车工厂里零部件等在生产线上的流转很不顺畅,极大影响了作业效率。 竹内克己也告诉《商务周刊》,早期包括丰田在内的汽车企业制造生产线都很简单,工人的工作环境恶劣,安全也得不到有效保证,工作效率低下,急需对生产设备和生产线改造。大福从中看到了商业机会,随即涉足汽车自动生产线的制造。 1950年,丰田英二、斋藤尚一等丰田领导人相继前往美国,参观位于底特律郊外的福特Rouge工厂,学习其先进的生产线。在此基础上,丰田制定了1951—1955年的“生产设备现代化五年计划”,重点是更新陈旧设备,引进输送带,通过自动化手段提高生产效率。 竹内克己向《商务周刊》回忆,当时丰田公司找到大福,两家公司开始合作研制更先进的生产线。1957年,大福为丰田开发出第一套车身流水线。 “这套自动系统改善了作业流程,大大提高了工作效率。”竹内说。 1959年,丰田公司第一家也是日本第一家轿车专业工厂——元町工厂在爱知县丰田市建成投产,这是一个从冲压到车体焊接、车体涂装、最终装配实行一条龙生产的工厂,整套汽车制造生产线系统的提供者正是大福。 虽然最初丰田的流动作业装配模式、传送带生产线、自动线搬运等全部学自福特,但由于日本汽车企业是按多品种小批量方式生产,而福特是少品种大批量的生产模式,所以大福为丰田提供的生产线从一开始就考虑到了生产体系的弹性问题,这也使得丰田超越了福特生产模式,创造出自己独特的“丰田精益生产模式”。 这就要求输送线的设计必须满足所谓柔性生产,即按订单在一条生产线上混合生产不同车型对汽车零部件的输送要求。经过长期跟踪汽车制造商的生产线发展和与客户的紧密合作,1980年代,大福开发出先进的悬挂式搬运系统Ramrun(自动化制造模式),到2000年,大福又研发出更具柔性特点的Friction搬运系统FDS(混合制造模式),不论是搬运、涂装还是装配等环节,都适应汽车制造商对混合生产的更高要求。
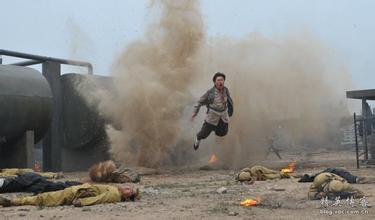
全球范围内,汽车生产自动化(AFA)市场总规模大约为2000亿日元,大福在这一领域占据了20%以上的份额,在日本市场更高达65%,用户囊括了丰田、日产、本田等日本主要汽车公司。随着美国自上个世纪末回头学习“丰田模式”,通用、福特和克莱斯勒三大北美车厂也都成为大福的客户。跟随日本制造业的全球化,大福的AFA业务也得以在全球延伸,在中国和泰国等国家都建有工厂,中国的天津一汽丰田、东风日产、广州本田和上海通用都使用了大福最先进的自动化生产线。 作为大福工业起步的基础,AFA事业部每年为大福带来持续增长的销售。大福提供给本刊的数据显示,2007年其AFA业务的销售额达到520亿日元,预计到2009年将增至600亿日元。 物流不仅仅是搬运 每天,位于日本茨城县土浦市的可口可乐工厂大型自动立体仓库前,随时有十几辆利根物流公司的运输卡车等待把刚从仓库里搬运出来的饮料配送到周边的各大超市和便利店。 负责为这家可口可乐工厂提供物流服务的利根物流株式会社输送部土浦营业所所长根本忠七告诉记者,在工厂内部,所有饮料的搬运、储藏信息控制都由大福提供的一套自动仓库系统完成。这套2007年11月1日刚刚开始运行的系统,实现了完全的自动化和信息化控制。 记者在现场看到,一瓶瓶可口可乐从灌装线上装箱后,被滚筒输送带送到专用托盘上,其间的条码信息扫描和装盘都自动完成,一辆高速搬运台车把码放整齐的一个个货盘送上垂直搬送机,再送到仓库区的输送带,货物又一次被扫描和信息处理,码放倾斜和不规范的货盘被自动送到一个专门的校正区。合格的货盘被输送到货架前,15台高速搬送台车将货盘送上堆垛机,在30米高的货架间,9台自动升降堆垛机穿梭往返,把沉重的货盘安放到信息中心指定的货位上。物流公司的运输车到位后,出货信息通过信息中心发送过来,堆垛机把指定的货盘从货架上卸下,送到出货的输送带上,信息条码再次被扫描,然后装车运到这些饮料该去的地方。一瓶饮料就经过这样的流程送到了消费者那里。 由于高度自动化和智能化,可口可乐工厂偌大的仓储和输送车间里几乎看不到一个工人。而在每一个环节中,由于RFID等信息处理技术的应用,信息中心能清楚知道每一瓶饮料到了哪个环节,具体在哪个货位上,何时出库,被配送到了哪家超市。 竹内克己曾与日本的物流专家笑谈,以后每个饮料瓶上都会注明这瓶饮料是大福搬运的。 玩笑正真实地发生在日新月异的现实中。工业物流已经不再是简单意义上的搬运,在促进效率和节省人工的同时,产品信息不再只有生产的履历,还包含了其间的物流信息,商品更高精度的品质管理正在成为现实。而大福对于变革发生的贡献早就开始了,茨城可口可乐工厂的自动立体仓库系统只是一个最新的案例。 现代意义上的物流概念进入日本是在1950年代中期。1956年,日本流通技术考察团从美国引入物流的概念,整个日本产经界逐步把对物流的认识、研究和应用深入到制造业和流通业。作为实现物流价值的手段,物流处理系统(MHS,MaterialHandlingSystem)被大福开发出来,在对物品进行合理、高效的管理和控制的同时,追求低成本化,为用户提供包括“保管、分拣、搬送、控制、信息”在内的总体解决方案。 为应对社会对商品快捷流通及顺畅地生产、配送的要求,大福构筑了以自动仓库为代表的各种保管系统、分类分拣系统、搬运系统等面向工厂自动化和流通自动化的产品体系。成立了FA&DA(工厂自动化与物流自动化)事业部。 1966年,大福向松下电器交付了第一个立体自动化仓库。到1970年代,自动化立体仓库在日本盛行起来,大福自动化物流设备(上海)有限公司总经理藤木胜敏称:“那时候在日本拥有一个自动化立体仓库是一件很了不起的事情”。 自动化立体仓库货架长度大、排列数多、巷道窄、密度高。巷道机上装有各种定位的检测器和安全装置,保证堆垛机高速、精确、安全地在货架中存取货。与普通仓库相比,自动化立体库具有无可比拟的优越性。以库存11000托盘、月吞吐量10000托盘的冷库为例,自动化立体仓库占地面积只是普遍仓库的13%、工作人员为21.9%、吞吐成本为55.7%、总投资为63.3%。 1999年,大福为佐川急便研发出了先进的物流分拣系统,作为转折点,大福向DA(流通自动化)领域挺进,推动了日本物流配送中心的快速发展。 2007年9月,大福与日本38家出版商合作的“东贩桶川(SCM)中心”在琦玉县桶川市启用。SCM中心流通系统部长森冈宪司称,该中心是目前世界上最大的图书物流配送中心,采用了大福最先进的专用高速分拣装置以及料箱自动仓库等物料搬运系统。 5层搂的新中心可以存放80万种超过1800万册的图书,大福的设备和信息控制系统每天24小时地不停运转:高速分拣设备自动分拣图书,通过输送带输送到指定位置,输送装置具有自动称重和自动验货功能,每天,多达200万册退订图书和出库图书被自动处理,这些图书来自不同的出版社和分销书店,不同开本、不同重量,200万册图书如果用10吨的卡车装,需要100辆。 森冈宪司告诉本刊,与以往的人工作业相比,大福的自动设备系统几乎节省了一半的人力,更关键的是验货差错率降低到十万分之三以下。 与大多数竞争对手不同的是,大福公司成套系统中的关键设备都是自行开发、制造,包括货架、输送机、数字显示式拣选设备、自动导引车、自动堆垛机、AGC控制系统、WMS信息系统等,几百种高品质产品几乎涵盖了建设物流系统所需要的全部硬件和软件,大福公司通过强大的技术集成能力将其集合为适合不同用户的成套系统。 这其中,FA&DA业务已经成为大福最重要的和最擅长的领域。在日本,大福向零售、图书配送、电子、医药、汽车制造、机械、农业、冷冻仓储等多个行业的用户提供了超过15500套物流系统和整体解决方案。FA&DA领域的销售,持续多年稳居大福总销售额的第一位,2007年,FA&DA领域的销售额达到了810亿日元。 新技术和产品正在大福被加速开发,位于滋贺县的大福新工厂里,40米高的堆垛机已经矗立在工厂大楼里,这个超过十几层搂高的大家伙是目前世界上最高的自动堆垛机,如此高度,对材料、稳定性和精准度有更高的要求。全球行走速度最快的堆垛机(500米/分钟)也在大福被研发出来,在快速运行过程中可以戛然而止,停在信息指定的货位。 竹内克己期待,这些当今世界上最先进的物料搬运设备,在不久的将来能为大福带来更大的利润空间。 在“失去的10年”崛起 在占地超过125万平方米的大福滋贺半导体与液晶生产自动化(eFA)工厂里,工人们进入车间前,都要穿上专业的防尘服,经过空气除尘室,才能开始一天紧张的工作。 eFA事业部所属的I工厂和J工厂都是无尘车间,为全球半导体用户和液晶制造商的生产线研发无尘物料搬运、输送和存储设备。大福提供给《商务周刊》的数据显示,eFA业务已经成为其FA&DA之后的第二大销售来源,2007年,eFA业务的销售额可以达到740亿日元。 而更为关键的是,从大福成立eFA事业部,不但把业务拓展到更广阔的空间,而且无意间避免了历史上日元升值和国内泡沫经济破灭给日本制造业带来的沉重打击。 1985年,美国联合欧洲向日本施压,签订了逼迫日元升值的《广场协定》。两年时间里,美元对日元的汇率降低了51%。日元的升值缓解了美国对日的贸易逆差,但却导致日本企业出口利润大幅度下滑,给日本包括汽车产业在内的制造业造成很大打击,日本经济进入“失去的10年”。 但在这场经济打击下,与日本制造业关系密切的大福总体经营和运转却没有受到多大影响。大福常务取缔役、海外统辖井上正义解释,其中的原因除了大福良好的营销策略、多年来对行业的专注和优质的售后服务外,另一个根本性的因是大福没有止步于已经取得的业绩,而是紧跟新兴的制造产业,开发新技术和产品,开拓新业务领域。在“失去的10年”之前,大福的AFA、FA&DA和eFA三大事业部都已经建立,三大业务互相支撑,互相补充和平衡,使得大福稳定地度过了“失去的10年”。 1980年代,PC工业在日本起步,日立、东芝、NEC、三菱、富士通等一致加大在半导体产业的投资和研发,迅速形成了强大的半导体产业,而随着中国台湾、韩国半导体工业的突飞猛进,东亚地区已成为世界半导体工业的基地。 半导体制造对于无尘的要求非常高,早在1979年,大福就开始研发半导体生产无尘车间使用的搬运、保管系统。1984年,大福完成了防尘立体自动仓库(cleanstocker)和防尘轨道输送车(cleanway)的开发,并迅速推向市场。1999年,大福开发出了300mm级晶圆无尘搬运设备,以及防尘无人搬运车(cleanAGV)和防尘悬挂单轨式搬运车(cleanspacecarrier)。目前,全球最大的几家半导体制造商都是大福忠实的客户。 在大福滋贺新工厂的I工厂里,eFA事业部技术人员告诉记者,大福研发生产的半导体生产线无尘搬运系统,洁净度已经达到了每立方米空间里只有10个0.3微米以下的灰尘。 1990年代,液晶显示技术获得突破,到1990年代末,日立、东芝、夏普、三星和LG等液晶生产商主导了这一产业。随着技术的发展,液晶玻璃基板的尺寸越来越大,而厚度越来越薄,如何在生产线上安全搬运这些特殊的产品对搬运设备的精确度和稳定性有很高的要求。 在跟踪这一市场需求的基础上,大福不断推出适应液晶生产大型化要求的物料搬运解决方案,2001年,大福研发出了第五世代(1500mm×1800mm)玻璃基板卸载机,并迅速占领了50%的市场。2004年,第七代(1870mm×2200mm×0.7mm)“悬浮式液晶玻璃基板搬运输送”设备在三星的生产线上应用。为保证搬运的安全,大福采用了新的气体悬浮技术,气流从玻璃基板下部喷出,将每片易碎的玻璃片悬浮起8mm高度进行输送。 在大福滋贺新基地J工厂的无尘车间里,目前世界上最尖端的第八代超大型液晶屏玻璃基板无尘搬运系统正在研制之中,第八代液晶玻璃基板的尺寸已经达到了2460mm×2160mm。经过20多年的技术研发和对客户的跟踪,目前,大福eFA业务在全球的市场占有率超过了40%。 “大福成功的一个主要因素,就在于大福始终站在最前线同客户并肩前进。”竹内克己说,“制造业的水平到达哪里,大福的搬运技术也就能到达哪里。”