石化行业管理系统的组成包括生产计划与控制(PP-PI模块)、定额与计量管理、物料管理(MM模块)、财务会计与成本核算(FI-CO模块)、工厂维护(PM模块)。
生产计划与控制(PP-PI模块)
在离散式制造行业,生产计划和业务流程完全靠销售订单驱动,系统根据销售订单分解出物料需求计划,进而生成物资采购计划、生产计划等,企业按计划组织生产。
但在石化这种流程制造行业,无论订单多少,生产都必须连续稳定进行,其生产计划的主要任务是如何有效地利用现有装置,以最少的资源付出,最大程度地组织最具效益的产品品种、型号的生产。
按此方式,就需要在ERP系统中预先设定各种产品、型号相对合理的配方(BOM),并具有相对准确的消耗定额、成本指标等,在初步拟定的多个计划方案中,通过系统运算,在众多方案中择优。
另外,在做生产计划时,还要兼顾产品品种切换过程中可能发生的物耗、能耗增加,产量、负荷变动,废次品产生等各种情况。
另外,对于石化行业来讲,配方涉及企业的安全保密问题。但按照系统的要求,需要预先确定完整配方,在生产过程中还要准确下达具体的生产指令,给企业的保密工作带来了比较大的麻烦。
为此,一方面需要企业在配方管理、授权等方面进行严格控制,及时跟踪检查(目前较好的石化行业软件都提供了相应的控制手段);另一方面,建议生产指令采取分段下达、分段操作、多人控制的方式分散风险。
定额与计量管理
石化企业在系统中的生产控制主要取自于配方(BOM),配方即各种原辅材料、公用工程、人工、机器等生产要素的消耗比例和定额。
然而对于石化企业而言,人工工时、机器工时的确定相当困难,特别是机器工时。
定额和消耗在石化行业中往往是通过计量仪表进行实时记录和定期抄表确定的。由于石化企业的物流情况十分复杂,因此计量在生产和成本控制中的地位也显得格外重要,特别是对液态和气态物质,需要进行准确的计量才能确保生产的正常运行和成本的准确计算。
为此,石化企业在实施ERP系统前,首先应对计量系统进行全面的清理和完善,确保企业内外部之间,分厂、车间、装置、甚至产品品种、种类之间的各个界面能够有准确的计量。
其次,计量系统最好能采用实时数据采集和传输技术,通过ERP系统相应的接口实时传递计量信息,减少众多物料数据的人工采集,避免事后统计录入对系统实时性的破坏。
再次,对管道中流动的液态、气态物料,还必须考虑其成分、浓度(密度)以及自然损耗、管道中间存留等特殊情况。
最后,计量单位还应该采用国家标准,并保证统一。
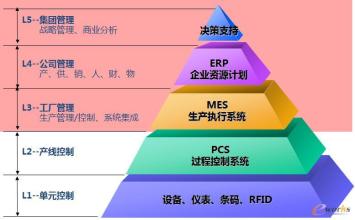