1.DCS与PLC 60年代以后, 随着生产过程的大型化和复杂化, 诞生了计算机集中监视和控制的集中控制系统。集中控制方便了监视、操作和管理, 同样也使危险性高度集中, 系统一旦故障, 对装置造成的影响及危险性都是非常大的。随着微处理机的诞生, 为新型控制系统的开发创造了无比优越的条件。1975年11月, 随着计算机(COM PU T ER)、通讯(COM M UN ICAT ION)、控制(CON TRL)和CRT 4C技术的不断发展和完善, 美国霍尼韦尔(HON EYW ELL)首次向全世界推出了分散控制系统TDC-2000被称为当时“最鼓舞人心的事件”。从第1套D CS系统诞生至今,D CS系统已经历了4个发展阶段。 1975~1980年为初创阶段。由于软硬件技术的限制, 此时的D CS系统性能还不十分完善, 硬件结构还不十分成熟。 1981~1987年为第2个阶段。这一时期容错、冗余技术已成熟使用, 系统可靠性很高,性能十分优越, 各种控制功能十分丰富。 1987~1993年为第3阶段, 各厂家的D CS开始向以O S I为基础的M A P协议靠拢, 以求达到不同系统的互联。 1994年至今为第4阶段,D CS系统在硬件上使用了更先进的CPU及冗余技术, 贮存容量及通讯速度大幅度提高, 软件上采用通用操作系统。 早在D CS出现前的1969年D EC公司按照GM(美国通用汽车公司)的10条要求研制出世界上第1台PL C, 首次安装在美国底特律的GM 公司的汽车装配线上一举获得成功, 1969年在D EC之后GOU LDM OD ICON使PL C商品化, PL C是专门设计出来用于同继电器产品竞争的, 并且已逐渐取代了继电器。PL C做为一种工业控制专用计算机已跨过25年的历史, 经历了5个发展阶段: 1969~1972年是PL C的出世阶段, 各家PL C结构差异很大、功能简单、硬件结构以分离元件为主, 体积较大。 1972~1976年为第2阶段, 系统开始标准化、系统化, 整机功能由专用向通用过渡。 1976~1987年为第3阶段, PL C逐步演变成一种专业的工业计算机, 可靠性大大提高, 成本大幅度降低, 面向过程的梯形图语言及其变种语句表语言问世, 为PL C的普及奠定了基础。 1981~1988年为第4阶段, 梯形图语言和语句表语言完全成熟, 基本标准化, SFC语言问世。 IEC 发表PL C标准草案, 各厂家的PL C向规范化系列化发展。 1988年至今为第5阶段, IEC 正式颂布PL C标准。整体式PL C与外界连接的输入、输出部分标准化、模块化, 并与主机分离。 2.过程控制、顺控、安全联锁全部在D CS系统中完成 顺控是工业控制过程中重要的一环, 大量采用离散的开/关信号, 执行较复杂的逻辑控制功能来完成间断的、批量的工业生产过程。 安全联锁一般只须要执行较简单的逻辑功能。 过程控制系统要求用模拟信号, 完成复杂的数字及逻辑运算功能。 过去, 由于技术上的原因, 加上传统观念对人们的影响, 世界上许多国家的设计资料及规范均要求把过程控制与安全联锁分开,这就造成大量的装置过程控制与顺控, 特别是过程控制与安全联锁系统分别采用相互独立的控制系统。随着生产工艺越来越复杂, 随着4C技术突飞猛进地发展,D CS已取代了常规控制仪表完成过程控制, PL C取代了继电器完成顺序控制及安全联锁。D CS与PL C无论从硬件结构, 还是在软件上都很相似, 而现在D CS系统在功能上要比PL C强得多,D CS有很好的操作监视界面, 有丰富的管理软件, 有很强的控制功能, 可利用率已达到99.9999%。用D CS取代PL C, 在1套工业装置中即完成过程控制又要完成顺控, 特别是安全联锁, 这是完全可能的, 并且在工业界中已有考虑应用, 这也是工业自动化发展的一个方向。 从系统结构上看。从系统硬件构成来看,D CS系统是由上位管理计算机, 操作站和控制站等组成, 而有些D CS系统还设立了专门的逻辑控制站,(即PL C) 如TDC-3000的LM。1个控制站(包括独立的逻辑控制站) 就相当于1台PL C, 其硬件结构也与PL C基本相同, 包括I/O模件、通讯模件(站内部)、存贮模件和CPU运算模件。从软件及通讯上来看D CS的基本出发点就是分散控制, 每一个控制站与控制站, 控制站与操作站、上位机之间是相对独立的, 不论哪一个站出现故障都不会对其他站造成影响, 如果选用高分散型的控制站还可进一步把危险分散。因此从系统结构上看D CS的一个现场控制站对整个系统可以说是独立的, 其可靠性完全可以和1台PL C相比, 仅受本站内故障的影响。 可靠性。由于D CS系统采用了容错、纠错, 从电源、I/O到通讯以及存贮运算等一系列的冗余, 甚至四重镜面CPU等多种高可靠性措施, 加上今天的电子元器件, 集成电路可靠性大幅度提高, 整个系统平均无故障时间M T B F高达10万d, 平均修复时间M T T R为10- 2d, 利用率A 高达99.999 9% ,即使假设目标故障率H 为每年0.01% ,对D CS要求的故障率D为100次/a, 系统的利用率为:U=H/D则 U= (0. 01%)/100= 0. 000 01%,可利用率= 1- U= 99. 999 9%。 从D CS与PL C的发展过程来看,D CS,PL C都经历了4~5代, 已完全成熟, 从硬件选型到制造工艺,D CS和PL C厂家都是精益 求 精, 选 用 最 先 进 的CPU (32B IT M C68020~M C68040), 采用最先进的表面贴装技术, 在软件方面采用成熟的可靠的操作系统。总之都利用了当今世界上最先进优秀的手段, PL C没有任何优势可言, 而D CS第2代产品中就采用了分散, 冗余等先进手段。 由D CS完成安全联锁有利于把事故消除在萌芽状态。 把生产的安全可靠性提到重要地位上来, 寻求更完善可靠的安全控制策略, 要求对不正常情况的出现进行自动检测、诊断、控制。随着生产工艺的大型化、复杂化及精密化, 单纯的安全联锁系统不论从及时性、可靠性, 还是从经济性的角度考虑, 都存在很多不足之处, 难以处理复杂的情况。而在D CS内可以采用故障检测和诊断技术, 可以在故障的萌芽阶段就被发现, 这样可以及时处理, 避免事故扩大, 并减少停车损失。国外已有了安全性检测和保护系统的软件商品, 这也只有在D CS系统中才能很好地运行(需要各种信息)。 在安全联锁中D CS不能做为PL C的后备。有观点认为在PL C单独完成安全联锁的情况下,D CS可以做为PL C的后备。 在工业控制过程中, 一般的顺控特别是安全联锁系统, 从检测元件到报警给定器, 无论是驱动继电器, 还是PL C或D CS, 完成逻辑运算, 然后送出执行信号到现场执行机构,这一系列的过程中的元件都是完全独立的。特别是对于安全联锁, 更是这样, 即操作信号(人能干预的信号)与联锁信号是分开的, 从检测目的, 到检测设备都是相互独立的, 即使是在D CS内部完成顺控(安全联锁), 这一部分功能也是相对独立的。D CS或常规控制手段的监视操作功能, 并不能看作是联锁的后备功能, 事实上也根本起不到安全联锁的作用。 当D CS出现大故障或停电, 必将造成对工艺过程不能正常监视、操作, 以至停车, 这 时安全联锁也就不需要起作用了。由于D CS有完善的双重化功能, 如果是一般的控制站 内的故障, 系统仍可正常运行, 可通过不停站, 在控制站正常运行的情况下, 进行故障处理, 则联锁系统照样能正常运行, 起到安全作用。 运行速度问题。随着计算机技术的不断发展,D CS系统控制站尽管容量在不断扩大, 但扫描速度也在不断提高, 有的系统现在扫描速度大于1m s, 并且能区分第1事故点, 大多数D CS虽达不到如此快的扫描速率, 但也有各自具体的处理方法, 比如回路扫描速率由用户自己定义, 对重要的回路扫描周期可以相对提高。 在工业生产上, 绝大多数的工业过程, 其反应、变化过程是比较缓慢的, 根本不需要10-9S级的处理速度, 加之传感元件的反应速度或给定器的工作速度也无法达到10-9S级, 因此D CS控制站的扫描速度完全可以满足一般顺控或安全联锁的需要。 从D CS与PL C的硬件结构或工作方式来看, 是基本相同的, 只是在处理信息的容量上有一定的区别。从这一点上看, PL C的扫描速率比D CS也不可能有非常大的区别。 容量上看。从硬件结构上看, 现在最大的PL C可以达到32 00个I/O点, 而整套的D CS系统的I/O点数完全可以与之抗衡。 从软件功能上看,D CS系统有丰富的功能模块及先进的顺控方法, 大大超过PL C。一般的由D CS控制的工业生产, 其顺控或安全联锁都不十分庞大,D CS完全可以胜任。 从通讯速度上看,D CS的通讯速度, 控制站与控制站之间, 或控制站与操作站之间已达到5M bp s或10M bp s。 从存贮容量上看,D CS控制站的内存可达16M bp s或更大, 远大于PL C。 便于联网通讯。从全厂管理的角度出发, 从控制的更高一 层次的要求来看, 我们又在搞全厂各装置自动控制系统的联网, 又千方百计地利用各种通讯接口、通讯方式, 把各系统连接起来,以便于全厂信息管理与信息采集。如果1个装置采用1套控制系统来完成, 不就可以大大减少这方面的工作量了吗? 运用D CS实现整个装置的自控也是自动化的发展方向 自动化与工艺知识更密切的结合, 工艺过程与控制设计的一体化已提到议事日程,与其让设计出来的过程难于控制而费力地在控制策略上解决, 不如一开始就考虑两方面的关系。在线统计过程控制(SPC)或连接过程的总体质量控制(SQ C)都必须建立在全装置统一的控制系统之上。 由经营、决策、生产、调度, 操作优化与直接控制等层次组成的综合自动化系统, 也要使用全装置、全厂的过程信息, 这也要求统一的控制系统,
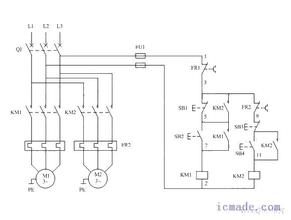
高速通讯与综合信息处理系统。D CS系统使自动化某些方法得以实现,同时规模巨大的综合自动化系统, 又对D CS提出了新的更高的要求, 促使D CS有更大的发展。 作组态维护。现在普遍使用的PL C, 其监视、操作都是通过各种不同接口, 用工控机来完成的。其PL C与工控机之间的通讯速率, 要远远小于D CS的5M bp s, 且操作平台一般都使用通用的操作系统, 其针对工业控制的特殊功能要少得多。而D CS的操作具有很多专用功能,其操作性能远远优于工控机,D CS还具有成熟的、丰富的管理功能, 省却了用户的二次开发的麻烦。 组 态:使用D CS系统控制工业过程, 必须要进行针对性的组态、完成用户软件。如果再加上1套PL C, 无论谁来组态, 用户必须再学习,熟悉一套新的系统。而如果把顺控功能设在D CS内部完成, 则仅仅增加了一定的工作量。而且1个装置、1套系统, 不可能所有的顺控都由PL C来完成, 但全部由D CS来完成是完全可能的, 这样可给使用者带来很大方便。 维护及管理:从运行后维护、管理的角度考虑, 把PL C用D CS来替代,D CS的规模可能会稍大一点, 但可以从原来的两套系统合为1套系统。这样不论从软件维护、修改, 还是系统硬件日常维护, 都可以减少维护人员的数量, 且便于维护, 而备品备件的数量和种类也可以减少很多, 故障的检修处理, 也只针对1套系统。 实际情况。玉柴石化20万吨溶剂油生产装置,。已经投入使用。此装置的导热油系统, 火炬系统, 有模拟输入35点, 开关量输入/输出274点, 使用了2套西门子公司的S7-200 PL C来完成顺序控制过程。通过R S232接口与1台工控机相连进行监视操作, 有独立的控制室。主装置采用的是和利时MACS V4.5分散系统,共有3个操作站U S, 4个控制站A PM, 1个工程师站UW S, 1台N M及1台HM。主装置控制室至导热油炉控制室直线距离不过百米, 完全可以用1台U S和1台A PM或LM来完成导热油炉系统的控制, 而两个控制室可以连成1个系统。这样, 对用户来说, 即便于管理, 也方便了操作(MACS V4.5系统软件的操作性比工控机要好得多), 特别是为生产开车后的日常维护, 备品备件带来很大的方便。 1个装置的几个部分由于工艺联系不太紧密, 或由于装置布置距离相对较远, 或由于不是由1家设计院设计, 无法协调统一等种种原因。搞得1个装置几个控制室, 往往主装置是D CS, 而辅助装置是常规仪表或常规仪表带PL C, 给工艺操作带来不少困难, 大大增加了仪表维护人员的工作量。实际上只要设计管理协调搞得好, 1个装置的自控完全可以用1套D CS系统来完成。这样做还有利于降低成本、提高利用率, 减少今后联网的费用与工作量。 3.结论 由前述的种种依据可以看到, 用D CS的控制站或逻辑控制站来取代PL C(在主装置采用D CS控制的情况下)完成顺序控制或安全联锁是完全可行的, 也是非常合理的。 参考文献 1.廉鸿帅,迟 军.西门子系列PLC原理及应用[M]。北京:人民邮电出版社,2009 2.徐国林,PLC 应用技术[M].北京:机械工业出版社,2007 3. Michael Babb The Disappearing DCS Control Engineering, 1992.05