提高加工效率和加工精度,是机床加工技术始终追求的目标。数控机床的发展和普及,不仅大大减小了加工的辅助和准备时间,而且为提高加工精度和实施高速加工创造了条件。高速切削机理的不断变化和现代刀具新材料的飞速发展,又为高速切削加工提供了理论和保证,从而使得在数控机床基础上的高速高精度加工成为现代机械制造技术的重要发展趋势之一。创新加工技术为机械加工带来了革命性的变化.也促进机床技术得到了飞速的发展。
对列双主轴布置
双主轴布置从产生至今已经过三代重大的变化,第一代是在转塔刀架的动力刀座上,安装上小卡盘成为第二主轴。从第一主轴上抓取夹紧工件后靠第二转塔刀架进行背面二次加工。很明显,它只适用于小型工件且进行二次加工时,第一主轴只好闲置不用。第二代为尾座主轴,即将可伸缩的尾架套筒改为第二主轴。先伸向第一主轴抓住夹紧工件后退回原处,再进行背面二次加工。这样的第二主轴在尺寸大小方面,明显小于第一主轴。现在已发展到第三代,即在同一轴线上相对布置大小完全一样的第二主轴—简称对列双主轴。相应地配备了第二转塔刀架。主要主轴的主轴箱一般是固定的,但也有少数可在床身导轨上移动。这样实质上等于将两台车削中心相对合并成为一台机床了。配备辅助主轴的优点是能在一台机床上进行全部加工,而且从两端加工的尺寸精度和同轴度比移至另一台机床上去进行另一端加工时要高。日本中村留精密公司的丁W系列对列双主轴车削中心.它的左主轴箱是固定的,而右主轴箱可以沿床身移动,不用机器人也可实现第一、第二主轴间工件的传送。有的厂家的产品是左右两主轴同步回转。第一与第二主轴的功能一般不完全一样,如有的产品第二主轴的C轴功能只限于分度。日本MAZAK的MULTIPLEX双主轴车削中心具有6轴控制,两个X轴控制两个转塔刀架的滑板移动,两个Z轴控制两个主轴箱滑座移动,两个C轴控制两个主轴分度。由于两个主轴均有C轴控制,在右主轴上铣削的表面可与左主轴上已加工的铣削表面采用同一参考位置。当工件装在左主轴上加工完毕后,左右两主轴同时向前进,在机床中部相遇。将工件转移到右主轴中,右主轴退回原处,进行背面加工。当工件在右主轴中加工时,左主轴上装上新的工件.同时加工,如此进行连续加工。
高速移动和高加/减速的机械进给系统
当前,高速高精度切削机床的进给系统是“回转伺服电机+精密滚珠丝杠”和直线伺服电机直接驱动两种方式并存,而以前者为主。这时所用的回转伺服电机,是大扭矩,低惯量,转速稍有提高的交流伺服电机。精密滚珠丝杠的导程则比原来加大了近一倍. 同时采用多头螺纹结构以增加螺母的有效圈数。加速度可达1g,最大进给速度40m/min。这种传统进给方式尚有潜力可挖,进给速度和加速度还有可能进一步提高。90年代在高速高精度机床上出现的直接驱动方式,则是取消了联轴节、滚珠丝杠螺母副等中间环节,由直线伺服电机按照伺服控制信号直接驱动执行部件移动的进给方式。由于它不存在中间环节所产生的滞后现象和其它的非线性误差,因而执行部件能对进给指令立刻作出响应,从而实现很高的加速度和进给速度。目前,采用直线电机的机床,在轮廓加工精度为3um -5um的条件下,加速度达1-1.5g,最大进给速度80m/min,
直线电机本身所能产生的加速度可达10g.但由于受到执行部件质量的影响而使加速度大大降低。所以,要千方百计减轻执行部件的质量。另一方面,目前直线伺服电机的进给力还不够大,尚有待于进一步提高。同步式和感应式两种直线伺服电机可以满足高速高精度机床的较大推力要求。
虽然目前直线伺服电机驱动的机床还不多,但越来越被生产机床的厂家采用,说明它代表了一种技术发展方向。
直线滚动导轨
在机床导轨设计过程中,如需要高精度高刚性时,设计师通常采用V形或平面滑动导轨,但这些导轨的缺点是摩擦力大,为此:常采用较大的电机和复杂的伺服控制系统。同时,由于这些导轨中动,静摩擦系数相差很大:在运动开始时驱动力要突然增大,在运动开始后驱动力要突然下降。车削中心高速化的过程中,滑动导轨由于摩擦系数相对较大,低速运动时容易产生爬行现象,而逐渐被滚动导轨所代替,其中直线滚动导轨得到了广泛的应用,即便是载荷比较高的设备也广泛应用直线滚柱导轨来提高机床的响应。应用于机床的直线滚动导轨具备以下特点:
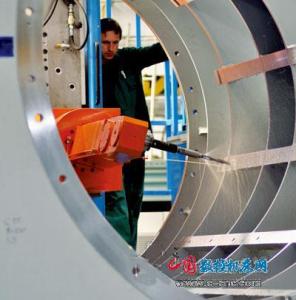
▲高刚性,且在各个方向上刚性相同
▲摩擦系数较小,一般为0.001-0.005,具有适度的磨擦
▲具有高精度,高运动直线性能
▲寿命长.可靠性高,有良好的耐冲击性能 由佳密特高速加工中心http://www.giamite.com.cn整理发表,转载请注明