已更,详见第一条分割线后。
首答。首先回答题主的问题,嗯,在短期内是造不出的。
下面说说我作为所谓的汽车内燃机零部件研发工程师的理解。
1. 客观原因:我朝现代工业起步时间较晚
第一次工业革命时我朝还在自居天朝上国,当权者并没有意识到科技将会对人类世界带来的巨大影响,也没有自上而下科教兴国的意识和对应的政策。百年后被怒X,现在想想也不觉得有什么好冤枉的,该。
十九世纪七十年代第二次工业革命伊始,靠着蒸汽时代的技术积累,内燃机被发明(内燃机的发展史可见度娘百科,非常详细),在此后200多年的时间里,虽然内燃机的原理并没有改变,但是随着汽车产业的发展,供应链逐渐完善,各大零部件供应商百花齐放。汽车内燃机作为制造业下的汽车行业下的小小一个动力总成,且不提一个内燃机的know-how由主机厂掌握,单说零部件,新中国成立的时间都没有诸如Bosch, Mahle, Erlingklinger等零部件公司营业的时间长。所以从Know-how的积累层面上,绝对时间已被欧美日甩开一大截。窃以为可以把原因归结为先天的基因缺陷。
2. 主观感受:说说我所接触到的我朝汽车行业现状
题目说的可能太大了。主要想说的是自己参加工作以后的经历。
交代一下笔者和所在公司的背景。笔者毕业后有幸进入德国法兰克福地区的一家汽车零部件公司。公司很年轻,上世纪50年代成立。OEM造车的未来趋势是Downsizing,且为了响应减排法规,公司一直致力于生产发动机进气系统和声学元器件,以及装在增压单元和thermo Management单元上的执行器,取得该领域内不错的成绩。
在位于德国黑森洲MKK的总部经过半年的入职培训同时结束了自己的试用期后,接到了第一个研发任务:在中国将一款欧洲已经量产的执行器做本地化。相对之后接到的问题,该任务实在算不上什么,而在中国Localization过程中遇到的问题往大里说,暴露的或许正是中国制造业的不足。
再简单的介绍一下当时参与设计研发的零部件。因为牵涉到Confidential问题,请知友们原谅笔者用一张示意图进行说明。
蓝色框内为我司产品:Pneumatische Steuerdose bei Wastegate des Abgasturboladers. 中文叫涡轮增压器废气门处的气动执行器。客户为某跨国大型涡轮增压器供应商,我司根据Specification的要求将它设计为负压执行器。工作原理是,当增压压力超过限定值时(不同涡轮增压器的增压压力限定值不同),EPW后的负压泵产生负压,克服弹簧力将膜片向右端移动,从而带动连杆机构,打开废气门,使部分废气不经过涡轮增压器的涡轮端,直接进入三元催化器而后排出,从而达到控制涡轮增压器转速、增压载荷和温度载荷的目的。
作为已经在欧洲量产的零部件,在德国工程师同事的帮助以及与中国本地供应商的沟通下,笔者当时最优先需要解决的,是因为我国冲压工艺不成熟所导致的尺寸与公差放宽问题。
对机械制图有涉略的知友或者仍在相关专业进修的同学们一定对尺寸和公差不陌生。尺寸与公差的放宽最直接的影响是配合不紧密,导致的最糟糕后果是零部件失效。此处放宽并不是传统意义上的放大,而是指供应商没有到达对应尺寸与公差的设备精度,因此在报价之前反向对客户的提出建议,最终仍然需要客户的拍板定夺。无需多说,若并非重要尺寸,那么该尺寸和公差放宽尚可妥协,但是涉及功能尺寸,德国老法师一定是不会同意的。
接着是材料问题。1.0338最后都会变成DC04,1.4567最后都会变成SUS 304。不管与原材料存在的差距是否可以得到德国工程师的释放,这些材料已经是国产市场上能够找到的最接近设计当中的材料,因此做出材料代用申请是稀松平常的事情。
根据之后获得的数个Localization的经验,多数情况下再严格的原设计都必须对我朝的工业标准和工程能力进行妥协。比如:欧洲与国产的标准本就不同。DIN EN 1544对1mm钢板厚度偏差标准如下图:
GB/T709-2006标准如下图:
对比如红框内。
说实话笔者在看到DIN对GB的吊打时,除了内心深处如上文提到的“先天的基因缺陷”而产生的悲哀外,更多的是无奈。冲压件供应商告诉笔者,不管在何时,他们的处境都是极其被动的,更别提在接到国外项目国产化的订单时,欧中工程能力的差距会更明显。产业上游有遵循不如欧标的GB/T和多数情况下为了节约成本而走下偏差的宝钢和首钢,下游有必须满足OEM提出的技术要求而设计出图纸,并严格要求冲压件供应商达到尺寸公差精度的Tier1, 如笔者所在的零部件公司。然而因为“两块钢”的轧制设备精度原因,出厂的钢材厚度并不稳定,那么在冲压供应商开完量产硬模的情况下,国产冲压件的尺寸和公差也因此就没办法得到保证。什么?知友你问为什么不用进口的轧制设备?或许因为民族情结和政治因素;什么?知友你又问为什么不去更改GB/T,将上下偏差范围调整得与DIN更接近?因为这样的调整对一个产业来说是牵一发而引全身的大动作,上游动辄几千万乃至价格更高昂的设备会因为标准的改变而报废,下游也会因为这一个所谓小小的改变而为钢板材供应商的设备改进而进行不可避免的成本分摊。而改变谈何容易呢?首先,不可否认的是标准的完善或改变有难度,其次,因为现行的GB/T中规定钢板厚度允许的下偏差,那么原材料供应商绝不会放过这个偷工减料的机会,因为钢板宽度越长,能够节约的钢材质量越大,能够省下的成本也就越多。这是悲哀,也是对某钢和人心的无奈。
然而刚才提到的只是对板材厚度的单个GB/T中暴露出的问题,而中国的工业体系由数万条GB或GB/T所组成。那句话叫什么来着,哦,简直了。
在该执行器项目后续的本地化过程中,也因为如“欧中同牌号材料组成不同”、“钎焊供应商没有控制好钎焊温度和时间导致钎焊区域DC04金相发生改变引起材料强度不足”、“客户突然提出设计变更却不接受OTS样件交期相应调整”种种原因,险些失控,好在在项目团队的协调下将问题逐个击破,在此就不多赘述了。
楼有点歪了,强行撸直。
笔者接触到多数如BorgWarner, Mahle, Hengst, Continental,
ZF等大规模的一级零部件供应商都是独资企业;OEM客户主要为SVW, FAW-VW, SGM, Daimler,BMW, Ford,直至近些年Volvo-Geely才向我司抛出橄榄枝,在介绍了发动机进气降噪减震方面独到的Know-how并从商务和技术角度得到对方认可后才开始了业务往来。
诚然如VW,等德系OEM非常重视供应链的概念,对供应商有比较完整的管理流程,也因为我司德国总部VW总部长达几十年的良好沟通,设计总能满足DV与PV,拿到Baumustergenehmigung (BMG认可), PPAP后SOP的极低投诉率也使得如进气系统从进气格栅一直到节气门之间进气及降噪的同类产品赢得了客户的信任,因此客户并不会频繁地(或并不会)更换供应商。这样的优势也让诸多本地化项目都建立在双方熟悉对方的流程的基础上体现了出来,对应不同OEM的项目经理们可以比较好地把握住各大熟悉的OEM的时间节点,避免不必要的麻烦,少走了许多弯路。
然而国内的OEM呢?
庞然大物吉利集团是个已经是本地主机厂的特例,笔者窃以为,它在收购沃尔沃后,供应商管控流程会有比较大的变动。但是,短期内消化Volvo长达85年的整车know-how积累,共享供应商清单仍然是非常有难度的。我司销售和项目经理也曾经一度因为吉利的采购所秉承的“沃尔沃的质量,吉利的价格”而抱怨“卧槽玩不动啊”。为什么?因为零部件供应商最注重的合作因素,除了技术上的feasibility作为内部工程能力的硬指标以外,还剩下的无非是Profitability和Volume,还有该客户未来的可能增长。管你是OEM还是Tier One, 在确认了技术可行性后,如果贵司的6年中Peak Volume只有例如8000或者刚过万的产量,那大可对客户说,走吧中午我们也不要去好的饭店了,路边沙县小吃搞一点得了。
笔者曾在2015年上海车展上与FAW的动力总成工程师短暂交谈,该工表示:“不是我们做不出好的发动机造不了优秀的整车,而是我们没有资源。”然而笔者想说的是,设想一下,local OEM们,你们最好情况不过是现在的吉利这般,请问你们如何管理和运用这些站在巨人的肩膀上获得的供应商资源?请问你们的Marketing团队如何在早已群雄割据被各大国外OEM跑马圈地几乎瓜分完毕的中国市场,说服国人购买你们生产的装着号称“拥有完全自主知识产权”发动机的车呢?然而笔者仍相信在不久的将来,消化了Volvo的Know-how并优化例如供应商管理和质量管控等内部流程后,Geely定会有给国产发动机扬眉吐气的一天。希望这不只是一个美好的愿景。
写到这里笔者将第二个原因归结为“后天营养不良”。从原材料标准一直到本地OEM试图重新在本土掌握市场主动权,我们还有很长的路要走。
回到前面,车展后我司受邀去FAW,向动力总成部NVH工程师团队展示公司进气系统与降噪的Know-how。当然有很多笔者不能当场回答的问题,如“如何定义自吸容积”、“如何在不同位置设定谐振器的频率”、“如何定义1/4管和阻性谐振腔的降噪dB数”,只能写下当做Open Point,带回总部后再尝试做更多了解。后来这些问题通过一段时间的学习总算是都能勉强回答了,可是在笔者整理了一系列由其他本地主机厂提出的类似问题后,发现它们的答案早几年就已经存在于多数成熟的国外整车厂动力总成的Specification中,供应商只要参照这份SOR设计并制造出满足要求的零部件即可。笔者慢慢感受到了国产OEM的无奈。如上文所提到的,VW,GM,Ford等欧美OEM瓜分中国市场多年,加上得天独厚的长时间Know-how积累、工业标准的绝不含糊、QC体系的完整和企业们对自家产品的绝对严谨态度,使得中国消费者愿意掏钱消费。需求带动生产,车零部件Volume高,供应商必定马首是瞻,欧美OEM们则拥有了更多的供应商资源,可以将更优质的技术反馈到自己的车型上,开启新车型的SOP,迎来新的销售记录;而受影响最大的往往是中国本地OEM们,因为量太少,导致不太有零部件供应商乐意接国产车的茬儿,除非量非常可观,否则结果的多半是是“走吧客户大人今天中午我再请您去吃沙县小吃,什么?哦好的想吃兰州拉面也可以啊,吃完了你赶紧滚球吧我们也很忙的”这样的收场。
可以说几乎所有汽车零部件供应商都受过上汽集团(主要靠SVW和SGM)的恩泽,带来了公司营业额上的显著增长,然而鲜有人听说“天哪我们拿到了北汽XXXX车型上XXXX的定点”的消息后让全公司欢呼雀跃,为什么?因为零部件供应商根本就不在乎本地OEM的这些鸡毛小量,还对比如进气和降噪、强制曲轴箱通风系统、涡轮增压器、温度控制、水循环几乎没有know-how积累,仅想让供应商们交出设计细节和方案,却不要他们做生产,恨不得把你脑子剖开来榨干你的Know-how, 如我司这样的德国供应商们又怎么会傻傻地把知识双手奉上呢?
《新约·马太福音》一则寓言曰: “凡有的,还要加倍给他叫他多余;没有的,连他所有的也要夺过来”。强者越强,弱者越弱,这是马太效应,没有公司能够违背市场规律却健康发展,欧美OEM们不能,而本土OEM更没实力。
Know-how的积累和技术人才的储备并不是今天党妈妈公开并实行一条有利于中国汽车发展的政策,明天就能立刻解决的问题。完整的工业体系和掌握发动机核心技术的工程团队需要至少三代人的努力。而真正有兴趣有使命有愿景地去投入科研开发,放弃其他赚钱机会的人有多少?聊大了又是上层建筑问题。有这样一个类比,若不贴切还请知友们听过算过。有一个穷小子成了凤凰男,却给一家家族企业的第三代继承人打工。由于富三代不学无术,脑子里没有脑浆只有屎,凤凰男非常不服气就跳出老东家自己创业,却输的一无所有。他非常愤懑并怒斥上天的不公,然而试想想,如果人前两代加起来超过100年的拼搏还比不过你丫30年的努力,那才叫不公平呢。
中国整车厂短期内造不出能够与欧美匹敌的发动机,没错,需要对症下药,但可怕的是知道必须对症下药,却不知病在何处,好不容易知道了病源却没有医生愿意治,那么请问这病又从何处开始医呢?
汽车零部件市场已经非常饱和,而国内外主机厂和零部件供应商的关系很微妙,有如鱼和水。要脱离开国外零部件供应商,将零部件也完全自主化本地化,在现阶段是基本不可能的。虽然现在仍在为德国人打工,但笔者作为发动机零部件研发工程师,不管身在何处,都希望能为未来大方溢彩的国产发动机添砖加瓦,献上些许绵薄之力。
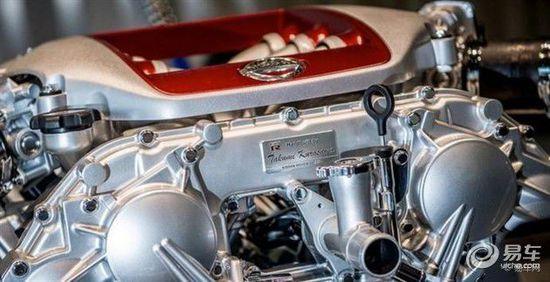
就这样,谢谢知友们的耐心。
-----------------------------------------------分割线----------------------------------------------------
22:30, 24.07.2015 Aktualisierung.
文中笔者在对比欧中标准时犯了很大的错误,非常感谢知友@ 发现并指出,没有让笔者继续误人子弟。
GB/T709-2006标准是热轧钢板标准,而DIN 1544是冷轧钢板标准,笔者因疏忽而选错标准进行对比。上图为GB 708-88 冷轧钢板和钢带的尺寸、外形、重量及允许偏差中对1mm冷轧钢板的描述截图。
GB/T708对热轧钢板的标准确实与冷轧钢板标准不可作对比,请知友们原谅笔者的不严谨,写回答时只为列数据进而强调“国产冷轧钢板走下偏差”的观点,并非有意黑国情,但是贻笑大方非常抱歉。再次感谢知友@。
-------------------------------------------------------------------------------------------------------------
23:53, 24.07.2015 Aktualisierung
刚才知友@提到积累时间短并不是主要问题,笔者寻思着从这个角度看的确有别的切入点。
民族品牌得不到本地消费者的支持是件各种意义上很难过的事情。反观日韩两国的丰田、本田、现代(起亚)等就有大把大把他们本国的国民愿意消费,其中一个原因在于对“匠”的崇拜流淌在他们尤其是日本人的血液中,愿意投入科研和发动机应用开发的人多,之后就积累起经验和Know-how,国民买的放心的同时又逐步产生了很强的民族自尊、自豪感,发动机和整车的品质就上去了。例如近年马自达的SkyActiv Tech真是让人咋舌,压缩比14简直是X了狗。日系自然进气技术发展到这样的程度跟他们本国的国民支持绝对是分不开的。
补充解释一下,笔者并不是在鼓吹要让中国消费者有这样的民族自豪感而去购买国产车,更不是想哗众取宠,毕竟本地OEM的车子没人家的好是事实。但从个人角度出发,在外企学习、被喂饱第一口奶打好基础以后,有机会的话我仍然非常想投入到国产发动机和整车的研发中,然而要呼吁大多数掌握了各自领域Know-how的外企国人工程师们一起这么干,上面不给点甜头的话开这个头是非常困难的。大多数的R&D和Q还有工艺工程师们都习惯了外企里优秀的软硬件环境,细分开来讲比如公司企业文化,完整地开发流程、项目管理流程和防错机制,设备齐全的实验室和经验丰富的老法师同事们,没有勇气也的确没有必要再往外跳,人到中年,就可以用“这样挺好”来归纳自己的状态了。
抱歉,说得有点太多了,这些东西作为所谓“年轻人的理想和抱负”,我只能用来来鞭策自己,并不能拿它们要求别人。不得不说有时候还是感受的得到自身努力的局限性和机遇的偶然性,说穿了自己只是个普通人。
最后,欢迎转载,注明出处即可。不定期更新,感谢所有知友的指正和信息的分享
2/3 首页 上一页 1 2 3 下一页 尾页